Australian cold spray additive manufacturing (AM) OEM Titomic has landed some key deals over the last couple of years, including one with Aussie energy giant Woodside to deploy a Titomic D523 system on an offshore gas platform, as well as a sale of ten D523 systems to the Dutch Army as part of the North Atlantic Treaty Organization (NATO) effort to support Ukraine.
Now, in quick succession, Titomic has announced two more deals that should prove pivotal in accelerating the adoption of the company’s metal 3D printing technology. First, Titomic has partnered with Metal Powder Works (MPW), a metal powders supplier based in the Pittsburgh area, to optimize MPW’s DirectPowder process for use with Titomic’s Kinetic Fusion technology.
Via the partnership, MPW and Titomic will work together to test and evaluate the performance of MPW’s powders in Titomic machines, enabling a quicker, cheaper route to materials qualification for Titomic customers. And, assuming that the early phases of the joint work are successful, the agreement should lead to a future commercial supply deal between MPW and Titomic.
Further, Titomic also announced that it is collaborating with US defense prime Northrop Grumman to produce pressure vessels for the aerospace sector. The partners are aiming to enhance the quality of the end-use parts compared to what’s possible with conventional manufacturing methods while also reducing lead time.
Like other Australian AM OEMs like AML3D and SPEE3D, Titomic has made the US defense market a cornerstone of its growth strategy. In the last year, alongside a ~$20 million capital raise to support those expansion ambitions, Titomic has also named US defense sector veterans, Dr. Patricia Dare and Sarah Neeley, to executive roles in its US operations.
In a press release about the materials optimization partnership between Metal Powder Works and Titomic, CEO and co-founder of Metal Powder Works, John Barnes, said, “We’re excited to expand our relationship with Titomic to achieve better results for them and their customers with powder consistency. We have seen in other trials that cold spray users achieve high deposition rates with the DirectPowder process aluminum and titanium powders.”
Likewise, in a press release about Titomic’s deal with Northrop Grumman to develop and manufacture pressure vessels, Neil Matthews, Senior Technical Fellow at Titomic and a Member of the Order of Australia (AM), said, “This collaboration with Northrop Grumman showcases the potential of cold spray technology to overcome traditional manufacturing limitations. By enabling the production of high-strength components with reduced material waste and reduced lead times, we are setting a new benchmark for aerospace and defense manufacturing. This project exemplifies the innovation that drives Titomic’s engineering efforts.”
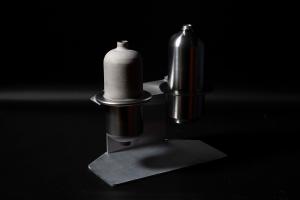
Pressure vessel prototypes made with Titomic’s cold spray metal 3D printing method. Image courtesy of Titomic.
Although still not technically considered a form of AM by ASTM standards, cold spray is the AM technology that I think may have the most growth potential over the next few years. In addition to being relatively cheap and easy-to-deploy, cold spray really excels at maintenance, repair, and overhaul (MRO). This objective has been increasingly prioritized by the big global manufacturing players that hold the most power when it comes to driving adoption.
These two moves by Titomic reinforce the bull case for cold spray, as the company is simultaneously cultivating the means (its partnership with MPW) and the opportunity (its deal with Northrop Grumman) to grow the user-base for this unique manufacturing process. The moves also illustrate the least outlandish aspects of the Trump administration’s goals when it comes to reshaping global trade: the emerging dynamic between the US defense industrial base and small and medium enterprises in Australia provides at least a shred of proof that the blueprint for future supply chains can be valuably informed by past mistakes.
One development that could truly solidify that concept would be if manufacturing stakeholders in key US allies like Australia — and indeed, manufacturing stakeholders in the US itself — could organize themselves behind rallying cries like SPEE3D CTO Steven Camilleri’s Make Things Here initiative. In order for a re-imagining of supply chains to become something more than a theory, voices from within the manufacturing sector need to get comfortable with the idea of unifying to advocate for themselves.
Subscribe to Our Email Newsletter
Stay up-to-date on all the latest news from the 3D printing industry and receive information and offers from third party vendors.
Print Services
Upload your 3D Models and get them printed quickly and efficiently.
You May Also Like
The Market and Industry Potential of Multi-Material 3D and 4D Printing in Additive Electronics
Additive manufacturing leverages computer-based software to create components for products by depositing either dielectric or conductive materials, layer by layer, into different geometric shapes. Since its birth in the 1980s,...
3DPOD 262: Bio-inspired Design for AM with Dhruv Bhate, Arizona State University
Dhruv Bhate is an associate professor at Arizona State University. There, he looks at structures, materials, and design. Previously, he worked at PADT as well as in the semiconductor and...
3DPOD 261: Tooling and Cooling for AM with Jason Murphy, NXC MFG
Jason Murphy´s NXC MFG (Next Chapter Manufacturing) is not a generalist service; instead, the company specializes in making tooling. Using LPBF and binder jet, the company produces some of the...
3DPOD 260: John Hart on VulcanForms, MIT, Desktop Metal and More
John Hart is a Professor at MIT; he´s also the director of the Laboratory for Manufacturing and Productivity as well as the director of the Center for Advanced Production Technologies....