

3D Printing Off-Earth Ecosystem
Undoubtedly the most exciting frontier for human exploration, outer space is a gateway to probing promising worlds, looking for biosignatures in the atmospheres of exoplanets, or pushing the boundaries of our scientific and engineering limits. Nonetheless, steering the course of human space exploration beyond the far side of the moon could take decades. It has been 49 years since the last Apollo 17 crewed mission landed in the lunar Taurus-Littrow highlands, and it could be at least five more years before we see humans navigating the moon's lower-gravity atmosphere.
If our species will ever settle on the Red Planet or voyage into the distant regions of the outer cosmos, the space industry needs to thrive. For decades, a handful of space agencies lay the groundwork for the upcoming era of off-Earth commercialization. Still, it was not until the twenty-first century that companies began privately developing and operating launch vehicles and spacecraft. Once a fierce cold war duopoly, the space race is now dominated by private businesses.
At 3DPrint.com, we found 50 space companies using 3D printing to help create an off-Earth ecosystem, displayed in the infographic.
Earth
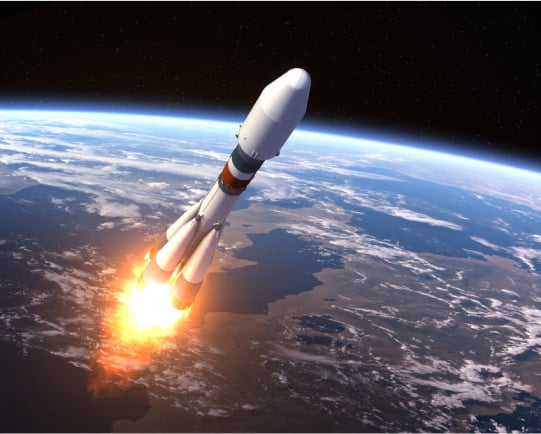
ABL Space Systems
Determined to prove that reaching space can be simple, efficient, and routine, the Los Angeles-based rocket startup ABL Space Systems set out to design and manufacture its rocket engines in-house. ABL used AM techniques to create parts of the E2 engines that will power Stage 1 and 2 of its RS1 launch vehicle, including the thrust chamber. This targeted use of AM allowed the creation of complex internal fluid passageways to be incorporated into the engine.
AgniKul Cosmos
Spacetech startup AgniKul Cosmos builds made-in-India 3D printed rocket engines. Produced as a single component in one run, the higher stage semi-cryogenic liquid propulsion engine called Agnilet was constructed to support orbital-class launch vehicle Agnibaan, expected to carry micro- and nano-satellites to LEO on-demand in 2022. With 3D printing technology, AgniKul can make single-part engines in less than 72 hours, ready to be fitted in a space vehicle after standard post-processing.
Astra Space
Founded with a vision to make rocket launches to LEO frequent, routine and automated, Astra Space is building small rockets designed for mass production and reliable performance to meet the rising demand for small satellite launches. Even though Co-Founders Chris Kemp and Adam London suggest they don’t rely on “costly 3D printing or labor-intensive composites” to make the rockets, for their Rocket 3.0, they used AM to complete the impellers for its pumps and rocket engine chambers.
Axiom Space
Axiom Space, the leading developer of the world's first privately-owned commercial space station, plans to 3D print parts in orbit. Through a promising partnership with Made In Space, Axiom plans to incorporate its proven 3D printing capabilities on the ISS. The companies have been working out the logistical elements of in-space manufacturing, outfitting the in-space factory with equipment, utilities, power, and thermal management to answer customers' growing demand.
Dawn Aerospace
Based in New Zealand and the Netherlands, Dawn Aerospace builds same-day reusable launch vehicles and non-toxic satellite propulsion systems for sustainable space transportation. As of 2020, the company has begun 3D printing combustion chambers for high-performance and high combustion pressure rocket engines destined to take its Mk-II Aurora sub-scale suborbital vehicle to space. Using composite materials for 3D printing the engines, they expect to provide the thermal conductivity needed to protect against space travel elements, which traditionally printed materials, such as titanium and stainless steel, lack.
Gilmour Space Technologies
Australia’s Gilmour Space Technologies will produce high-performance rocket and space components using AM. The startup received $3.7 million in investment funding in 2017 to develop its launch vehicles that use 3D printed rocket fuel. Focusing on the suborbital and LEO markets for satellite launches, Gilmour aims to provide an affordable launch service and improve accessibility to space. A pioneer in the Australian space industry, Gilmour will be using Titomic Kinetic Fusion (TKF) metal 3D printing to explore the production of rocket and space components.
KULR Technology Group
Leading developer of space-qualified electronics cooling systems and proven solutions for preventing dangerous battery fires and explosions, KULR develops unique 3D printed battery systems for space. The company’s space-proven solutions for electronics and lithium-ion batteries had demonstrated their efficiency when NASA used them to transport and store batteries aboard the ISS in 2019 and as part of the Mars Rover that landed on Mars in February 2021.
Launcher Space
Brooklyn-based Launcher Space has been developing what it says is the world’s largest 3D printed liquid rocket engine combustion chamber in a single piece. The E-2 engine, made in Germany by AMCM using its specialized M4K printer, has been tested many times at Launcher’s test facility in New York. Focusing on the smaller private satellite launch market, Launcher’s small rockets will begin flight tests in 2023.
Orbex
Vertical launch vehicle Orbex Prime will use a large 3D printed rocket engine uniquely manufactured in a single piece without joints, seams, or welds. The complex part, developed by UK-based startup Orbex, is expected to withstand extreme temperature and pressure fluctuations while traveling to orbit. Conceived and developed as an environmentally sustainable launch system, Orbex Prime will use renewable biofuels to deliver an industry-leading ultra-low carbon dioxide footprint.
Parabilis Space Technologies
One of the first companies to complete the first round of hot-fire testing of a 3D printed Reaction Control System (RCS) thruster, Parabilis Space Technologies, uses advanced manufacturing for launch vehicles and spacecraft parts. This was a massive step toward demonstrating that a 3D printed Liquid Oxygen (LOX)-methane thruster can be used in space. When commercialized, it will dramatically change the relationship between cost and performance. Parabilis is also developing novel AM methods to enable the use of multiple dissimilar materials in 3D printed parts for space thrusters and spacecraft structures and more technologies toward lunar exploration spacecraft.
Relativity Space
Space manufacturer Relativity Space of Long Beach, California, is working on 3D printing an entire rocket. For the task, it has developed its own massive in-house 3D printer called Stargate, which utilizes 18-foot-tall robotic arms equipped with lasers that can melt the metal wire. Those robotic arms can stream about eight inches’ worth of metal onto a large turntable in just a few seconds. Directed by custom software, the robotic arms can produce the rocket’s entire body in one piece, and the printer allows Relativity to reduce the part count of a typical rocket from 100,000 to 1,000.
Rocket Crafters
As part of the incredibly diverse and thriving aerospace industry around Florida’s Cape Canaveral Spaceport, Rocket Crafters focuses on producing rocket engines and pioneering its 3D printed rocket fuel. The startup is building and testing a large-scale hybrid rocket engine using Direct-Digital Advanced Rocket Technology (D-DART) and producing a unique fuel made primarily out of plastic. Using a patent-pending, horizontal 3D printing method that reduces production time for orbital-class fuel grains to a matter of hours in a single section, Rocket Crafters moves away from combustible and toxic propellants.
Rocket Lab
Like other space companies, aerospace manufacturer and small satellite launch service provider Rocket Lab is on a mission to “remove the barriers to commercial space by providing frequent launch opportunities to LEO.” The company has created the low-cost launch system Electron, whose Rutherford engine can be 3D printed in 24 hours. The engine’s main prop valves, injectors, pumps, and engine chambers are all created with electron beam melting.
Skyroot Aerospace
In 2020, Indian space tech startup Skyroot Aerospace unveiled its fully 3D printed cryogenic engine to fuel the upper stage of its Dhawan-1 rocket. The engine is considered India’s first privately developed indigenous fully cryogenic rocket engine that runs on propellants, like Liquid Natural gas (LNG) and LOX. Skyroot is one of India’s first private sector companies to participate in space activities with the government’s authorization and supervision.
Skyrora
Founded in 2019 to accommodate the UK's renewed entry into the global space industry, Skyrora has created a 3D printed 30kN liquid bi-propellant engine for its full-size suborbital launch vehicle, the Skylark L. This ground-breaking engine technology was precision welded at Skyrora’s production facility in Scotland using powder bed fusion, allowing engineers to integrate the cooling channels into one printed chamber piece.
United Launch Alliance
Formed as a joint venture between Boeing and Lockheed Martin, United Launch Alliance (ULA) manufactures and operates several rocket vehicles capable of launching spacecraft into orbits around Earth and other bodies in the solar system. For its Atlas V rocket, ULA turned to Stratasys for serial production of 3D printed thermoplastic components. Using Stratasys’ Fortus 900mc Production 3D Printer, ULA created everything from tooling and support equipment to production parts.
Ursa Major Technologies
A Colorado company, Ursa Major Technologies, develops innovative propulsion solutions for the emerging micro- and nano-satellite launch market. To optimize the unique part creation of its engines for launch and hypersonic applications, Ursa Major leverages 3D printing techniques to modernize the development of staged combustion engines. The company successfully designed and built two liquid oxygen and kerosene combustion engine models and is currently working on a third one.
Virgin Orbit
Space travel and commercialization have been a lifelong dream for one of the world’s most recognizable entrepreneurs, Richard Branson. Enthralled with space ventures, Branson created Virgin Orbit, a spin-off out of his space tourism company Virgin Galactic. The company, which focuses on small satellite launch services, acquired one of the first hybrid additive-subtractive manufacturing machines globally through a partnership with DMG Mori and used it to 3D print rocket engine parts for space launch. The LASERTEC 4300 3D hybrid is turning out large parts in its Long Beach, California, facility, allowing new material combinations, like Copper and Inconel, and a vast working room for workpieces of up to 3,306 pounds.
Low Earth Orbit (LEO)
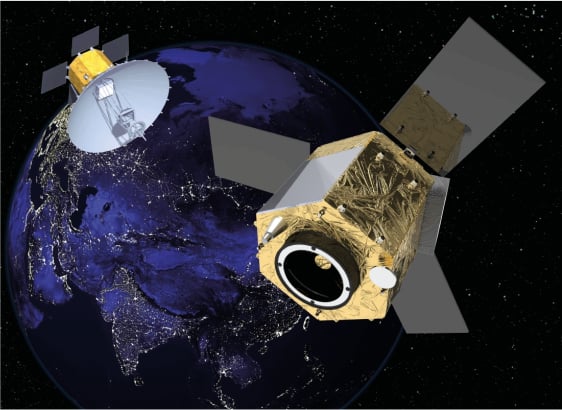
Airbus
Airbus has 3D printed a total of 500 radio frequency (RF) components, made of multi-waveguide blocks and switch assembly networks, for two Eurostar Neo spacecraft that will join the in-orbit fleet of Eutelsat, a primary provider of satellite communications services. RF components are at the heart of every telecommunications satellite, and now these parts are being produced by Airbus in large volumes.
Anywaves
A French Space Agency (CNES) spin-off, Anywaves develops miniature and high-performance antennas for the satellite constellations market. Applications such as telecommunications, navigation, Earth observation, atmospheric input, and many others require antennas for both receiving and sending signals. Anywaves’ novel 3D printed ceramic antennas have garnered many awards and will be ideal for the flourishing industry of nanosatellites. Soon the company will begin series production of the antenna via 3DCERAM.
Dhruva Space
Another of India’s first space startups, Dhruva Space, seeks to build low-cost satellites to collect real-time data. The company uses a lot of 3D printing, replacing space-grade components with commercial-grade components that cost one-tenth after extensive testing, and reusing and re-engineering parts wherever possible. Dhruva uses 3D printing technology, advanced CNC machines, and open-source architectures to integrate the satellites.
Mini-Cubes
Small space manufacturer Mini-Cubes is focusing on PocketQube Earth Observation satellites and using CRP’s carbon-reinforced nylon laser sintering material to 3D print them. At one eighth the volume of a CubeSat, PocketQubes are miniaturized satellites for space research typically built with commercial off-the-shelf electronic components. Hoping that their innovative product helps anyone reach space today, Mini-Cubes turned to CRP to 3D print the entire satellite frame.
Optisys
Focused on providing 3D printed antenna products for high-performance space applications, Optisys believes metal 3D printing promises to reduce the size and weight of critical satellite components significantly. The company uses metal AM to create critical parts for satellites and expects to bring increased capabilities to the burgeoning satellite industry that are otherwise impossible with traditional fabrication methods.
Stratodyne
Newcomer Stratodyne wants to 3D print stratospheric satellites and CubeSats. Founded by a 21-year old college student, the startup is focused on applying advances in 3D printing technology to lower costs for space and high altitude research. Its 3D printed modular and remotely controlled airship could serve as a satellite, testbed, and even a launch platform for small rockets into space. Stratodyne plans to go commercial by mid-2021.
Swissto12
A spin-off of the Swiss Federal Institute of Technology in Lausanne, Switzerland, (EPFL), Swissto12 is heavily invested in leveraging 3D printing technology to deliver complex satellite parts. From 3D printed waveguide solutions for communication satellite payloads to 3D printed all-metal patch antennas for a fleet of satellites, Swissto12 is looking to push the boundaries of 3D printing technology for the satellite industry.
Thales Alenia Space
Like many satellite manufacturers, Thales Alenia Space is installing more AM parts in satellites destined for low and medium Earth orbit. In 2017, 45 communications satellites built by the French-Italian space manufacturer were successfully orbited, all of them fitted with 3D printed parts. Now, Thales Alenia Space is taking 3D printing into series production to make components for telecom satellites built on the company’s new all-electric Spacebus Neo platform, a metal powder-bed fusion technique.
International Space Station

3D Bioprinting Solutions
Moscow-based bioprinting company 3D Bioprinting Solutions has engaged in a series of unique experiments in orbit thanks to a space bioprinter. Organ.Aut, the world’s first space bioprinter, was launched to the ISS in 2018. Since then, the device has been used to bioprint several tissues, including 3D bioprinting bone tissue in space for the first time using growing fragments of bone structures and carrying out a high molecular weight protein crystallization experiment in zero gravity.
Boeing
The U.S. aerospace giant is working on the CST-100 Starliner space crew capsules. These passenger taxis will initially take NASA astronauts to and from the ISS and are expected to take civilians later on. To supply over 600 3D printed components for the three Starliner capsules, Boeing turned to Oxford Performance Materials (OPM), saving close to 60% compared with traditional manufacturing.
Intuitive Machines
With a vision to enable sustained robotic and human exploration to the Moon, Mars, and beyond, Intuitive Machines provides innovative solutions for the commercial space ecosystem. The company relies on AM for many of its space parts, which go to different space projects, including constructing the first commercial space station on the ISS and the Nova-C Lunar Lander.
OHB Systems
German space and technology group OHB will develop a 3D printer prototype for the ISS for large part production using high-strength and functional thermoplastics. The undertaking is part of the IMPERIAL project, aiming to design, develop, and test a 3D printer model that alleviates build volume constraints while meeting the ISS fabrication requirements. The 3D printed parts produced using this system will demonstrate extraterrestrial manufacturing potential, enabling new maintenance and life support strategies for human space flight.
Made In Space
One of the most prominent players in the space ecosystem, Made In Space, has been experimenting with AM in microgravity since the early 2010s. The startup created the first Zero-G 3D printer that left for the ISS in the fall of 2014, followed by an updated version, the Additive Manufacturing Facility (AMF), in 2016. But the list doesn’t end there; the company has even manufactured the Plastic Recycler, capable of processing waste plastic into feedstock to use in the AMF.
nScrypt and Techshot
nScrypt and Techshot have created the innovative BioFabrication Facility (BFF), designed to print organ-like tissues in microgravity aboard the ISS. Launched in July 2019, the BFF has already successfully printed tissue-like constructs with a large volume of human heart cells aboard the ISS Lab as well as human menisci. One of the keys to 3D bioprinting in microgravity is that the bioink only contains cells but no scaffolding materials or thickening agents — typically required when bioprinting on Earth to resist the destructive pull of gravity.
SpaceX
With 3D printing, SpaceX can create its incredibly powerful SuperDraco thrusters, a critical component of the Crew Dragon’s launch abort system (LAS). The SuperDraco is an advanced version of the Draco engines used by SpaceX’s Cargo Dragon spacecraft to maneuver in orbit and during re-entry. The first demo mission of the Crew Dragon spacecraft with 3D printed SuperDraco engines took off in March 2019. The Crew Dragon’s highly anticipated final test mission was successfully launched and returned in the summer of 2020 with two astronauts on board.
Tethers Unlimited
Pioneering space company Tethers Unlimited focused on reprocessing space trash or debris to make resources and feedstock for in-space manufacturing. Its unlimited recycler and 3D printer onboard the ISS, the Refabricator, has demonstrated a unique process for repeatable, closed-loop recycling plastic materials for AM in the ISS microgravity environment a minimum of seven times. The integrated recycling/3D printing capability provides significant cost savings by reducing the launch mass and volume required for printer feedstock while decreasing Earth reliance.
Archinaut
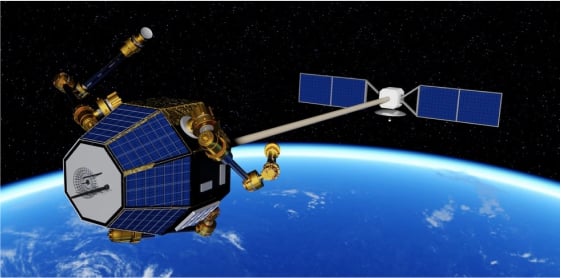
Made In Space
To further self-sustainability in space through the construction of satellites and even entire spacecraft, Made in Space is developing Archinaut, a 3D printer capable of working in the vacuum of space. Equipped with a robotic arm, Archinaut is scheduled to be installed on an external space station pod and capable of in-orbit AM, the fabrication, assembly of communications satellite reflectors, or the repair of in-orbit structures and machinery. The robotic manufacturing and assembly platform will orbit LEO to provide the most innovative means to date of large-scale manufacturing in space.
Northrop Grumman
To build Archinaut, Made In Space (now part of Redwire) has asked Northrop Grumman to provide software, systems engineering, control electronics, and space station interface support for the Archinaut project. As well as demonstrate Archinaut’s capabilities on a flight mission. The objective of Archinaut’s flight demonstration mission is to construct two 10 meter solar arrays, in orbit, to power a small satellite. The Archinaut system will be integrated into an ESPA class satellite bus (an adapter for launching secondary payloads on orbital launch vehicles) and launched into space. Once in orbit, Archinaut will employ its extended structure AM capabilities and advanced robotics to manufacture and assemble the satellite’s power generation system.
Oceaneering Space Systems
Strategically located near Johnson Space Center in Houston, Texas, Oceaneering Space Systems (OSS) has provided NASA with space flight hardware systems and equipment for more than 35 years. For Archinaut, OSS will focus on creating the robotic arm to be integrated with Made In Space’s novel 3D printing system.
Redwire
Formed in June 2020, new space venture Redwire has already incorporated several space companies into its acquisitions list. Self-defined as a new leader in mission-critical space solutions and high-reliability components for next-generation space systems and infrastructure, Redwire is now uniquely positioned to deliver end-to-end solutions to meet the needs of customers and advance the future of space exploration. Currently leading the work behind Archinaut, Redwire could become a household name as the space commercialization era proliferates.
Artemis
The European Space Agency (ESA) and NASA continue working together on a modern-day version of the Apollo program. Better known as Artemis, the program that takes its name from the Greek goddess of the hunt and twin sister to Apollo, is expected to return the next man and first woman to the Moon by 2024 (a timeline that has now been pushed back). One of its essential components is NASA’s Orion spacecraft, which will carry crew to and from lunar orbit. At the heart of Artemis is the European Service Module (ESM), which is critical to provide electricity, water, and air to the crew capsule and maintain temperature for life support.
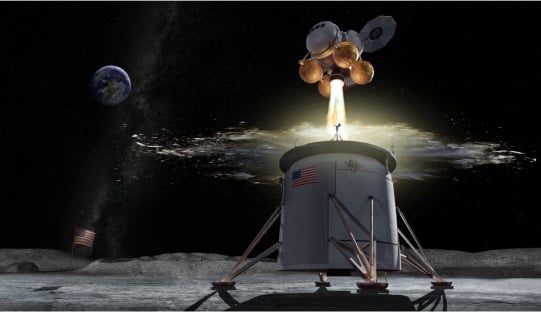
Aerojet Rocketdyne
Rocket engine manufacturer Aerojet Rocketdyne will provide rocket engines with 3D printed parts for NASA's Artemis program. As part of a years-long working relationship with NASA, Aerojet Rocketdyne of Sacramento, California, will be building a total of 24 RS-25 rocket engines to support as many as six Space Launch System (SLS) flights. Six new expendable RS-25 engines are already being assembled using 3D printing, and the additional 18 engines will continue to leverage supply chain optimization and incorporate AM techniques.
Airbus
Aerospace giant Airbus has already built two service modules for Orion with hardware from companies throughout Europe, and now it has signed a new contract with ESA for a third ESM module. The ESM is Orion spacecraft’s powerhouse. It is responsible for pushing the capsule through space by providing propulsion energy, consumable storage to sustain the crew onboard, and navigation control for the Moon and back. At the Airbus facility in Bremen, where the ESM will be developed, company engineers have been using 3D printing materials and processes for many years.
Boeing
Boeing will be producing 10 SLS core stages and up to eight Exploration Upper Stages (EUS) to support the third through the twelfth Artemis missions. SLS is NASA's deep space exploration rocket that will launch astronauts in the Orion crew vehicle, plus cargo, from the Earth to the moon and eventually to Mars. Boeing technicians used 3D printing to create precise molds for foams used to protect small hardware or cramped areas like the internal ducts of the engine section of the SLS, which would have otherwise required technicians to either manually spray the foam on or apply a foam casting.
Lockheed Martin
Lockheed Martin works with Stratasys and Phoenix Analysis & Design Technologies (PADT) on 3D-printed parts for NASA’s Orion deep-space spacecraft. In 2019, Lockheed announced completing the Orion crew and service module being developed for the uncrewed Artemis I mission, which has 100 3D printed parts. The spacecraft for the Artemis II mission has Lockheed developing close to 200 3D printed parts.
Masten Space Systems
A leader in rocket-powered terrestrial flight, Masten Space Systems has been working to prepare for lunar missions since 2004. The company is launching a mission to the moon in 2022 as part of the NASA Commercial Lunar Payload Services (CLPS) Project. In carrying out their mission to make rockets as operative as airplanes, 3D printing plays a critical role. For the Artemis Program, Masten turned to Elementum 3D to 3D print an electric fuel pump made out of aluminum alloy.
Northrop Grumman
All the sectors within Northrop Grumman do 3D printing and composite parts. Now, Northrop Grumman Space has initial design review (PDR) for the Habitation and Logistics Outpost (HALO), which is part of NASA’s Artemis program and will support the Lunar Gateway by working as a crew habitat and docking hub for vehicles. Northrop is experimenting with 3D fiber printing as a technology with many potentials to build in orbit because it doesn't require any tooling other than a digital computer model.
Moon

Big and ICON
As the hype around additive construction continues to grow on Earth, NASA has tapped companies for a project to deliver the technology to the Moon. The highly-publicized project Olympus aims to develop a method for robotic building on the moon. The idea is to create 3D printed lunar housing infrastructure using materials found on the surface. For now, Big and ICON will explore additive construction of a simulant of moon soil. ICON has already explored various building forms ideal for containing atmospheric pressure and optimized for protection from cosmic and solar radiation. Moreover, the habitat will be designed with the inherent redundancy required for extraterrestrial buildings while also using groundbreaking robotic construction that uses only in-situ resources, leaving zero-waste.
Blue Origin
Rocket company Blue Origin has created a three-stage lander that could take the astronauts’ crew to the Moon’s south pole in four years. A 3D printed high-performance BE-7 engine will power the company’s lunar lander system. Competing with Elon Musk’s SpaceX and Leidos-owned aerospace company Dynetics for the final NASA contract to make the next human lunar landing system, Blue Origin has already begun testing the fourth thrust chamber test series of its high-efficiency engine, demonstrating capabilities to land on the Moon.
Dynetics
Applied sciences company Dynetics is also developing a lunar landing system for Artemis and testing and evaluating AM materials and parts. Dynetics expects to ensure affordability for its robust, commercially supported lander capability that is easily adaptable for civil and commercial exploration by using modern technology to enable near-term reusability and sustainability.
SpaceX
The third contender for the lunar lander is SpaceX. The company is not shying away from its competitors, Blue Origin and Dynetics, to build the definitive version of the lunar lander that astronauts will use to go from Orion in lunar orbit down to the surface of the Moon and back. The three landers are very different. SpaceX offers a lunar lander based on Starship, the reusable launch vehicle developing and testing at a Texas coast site near Brownsville. The Starship spacecraft is powered by the Raptor engine, which includes quite a few 3D printed parts, SpaceX’s Starship lunar lander prototype is sure to contain 3D printed parts.
RUAG Space
In 2019, RUAG Space prepared to send the first 3D printed part to the moon. The Swiss company had developed an aluminum engine mount fitted on the Beresheet lunar lander’s main engine, designed by non-profit organization SpaceIL from Israel. The 3D part was expected to support landing and lift off of the spacecraft on the moon. Even though Beresheet 1 did not complete the landing as planned, Israel will aim for the moon again in 2024 with the Beresheet 2 mission.
Mars
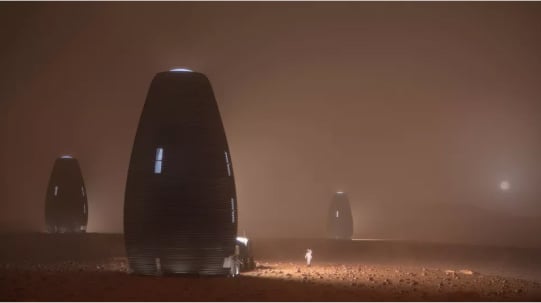
AI Space Factory
The architectural and technology design firm AI SpaceFactory, winner of NASA’s 2019 3D Printed Habitat Challenge for the successful construction of Mars habitat MARSHA, will develop a new material that mimics lunar regolith or dirt. The company will use the material to 3D print a test structure in a vacuum chamber that simulates the Moon’s environmental conditions. The research could inform a 3D printing system capable of constructing large surface structures from in-situ materials on other worlds.
Jacobs
Multinational company Jacobs is focusing on new and innovative ways to create building materials from Martian and lunar regolith through autonomous additive construction systems. AM has the unique capability to reduce the amount of time and materials needed to build the structures that future missions to other planets will demand. The Jacobs Space Exploration Group is testing the material simulants that mirror the regolith found on the Moon and Mars, which could become the basis for building roads, homes, and other Red Planet structures. Due to the scarcity of water on the Moon and Mars, the company is pursuing a waterless binder for an in-space manufacturing process called additive construction.
SpaceX
On December 9, 2020, Starship serial number 8 completed a high-altitude flight test, the first to prove that landing where prepared surfaces or runways do not exist, including Mars, could be possible. The company says its Starship spacecraft is the world’s most powerful launch vehicle ever created. Powered by Raptor engines that have 3D printed parts, including the turbopump and many of the critical components of the injectors, Starship is expected to enter the Red Planet’s atmosphere in three decades. At this time, we expect 3D printing in space will be much more advanced.
The Space Zone on 3DPrint.com
Discover the latest Space Zone articles from the 3DPrint.com team.
3D Printing News Briefs, July 12, 2025: Nerve Repair, Glass Nanostructures, adidas, & More
In this weekend’s 3D Printing News Briefs, we’re starting with medical news from 3D Systems, and then moving on to research about glass nanostructures and synthetic lichen. Then, 3D printing…
Daring AM: Space 3D Printing Heats Up Across the Globe
We keep coming back to China’s foray into space 3D printing—and there’s a good reason for that. The country’s space program continues to turn great ideas into working technology, proving…
South Korea 3D Prints a Titanium Space Tank and Freezes It to Prove It Works
Building hardware for space is not easy. It needs to be light, strong, and capable of surviving extreme environments, like the bitter cold and vacuum of space. Now, a South…
Research
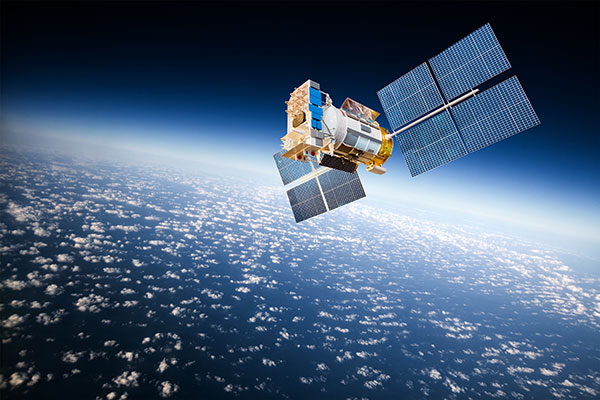
3D Printing in Commercial Space: The AM Ecosystem in the Private Space Industry
$2,497.50 – $3,497.50
Select options
Additive Manufacturing Industry Verticals (Automotive, Aerospace, Consumer, Dental, Energy, Industrials, Medical, Oil and Gas, Service Bureaus)
$1,000.00 – $3,750.00
Select options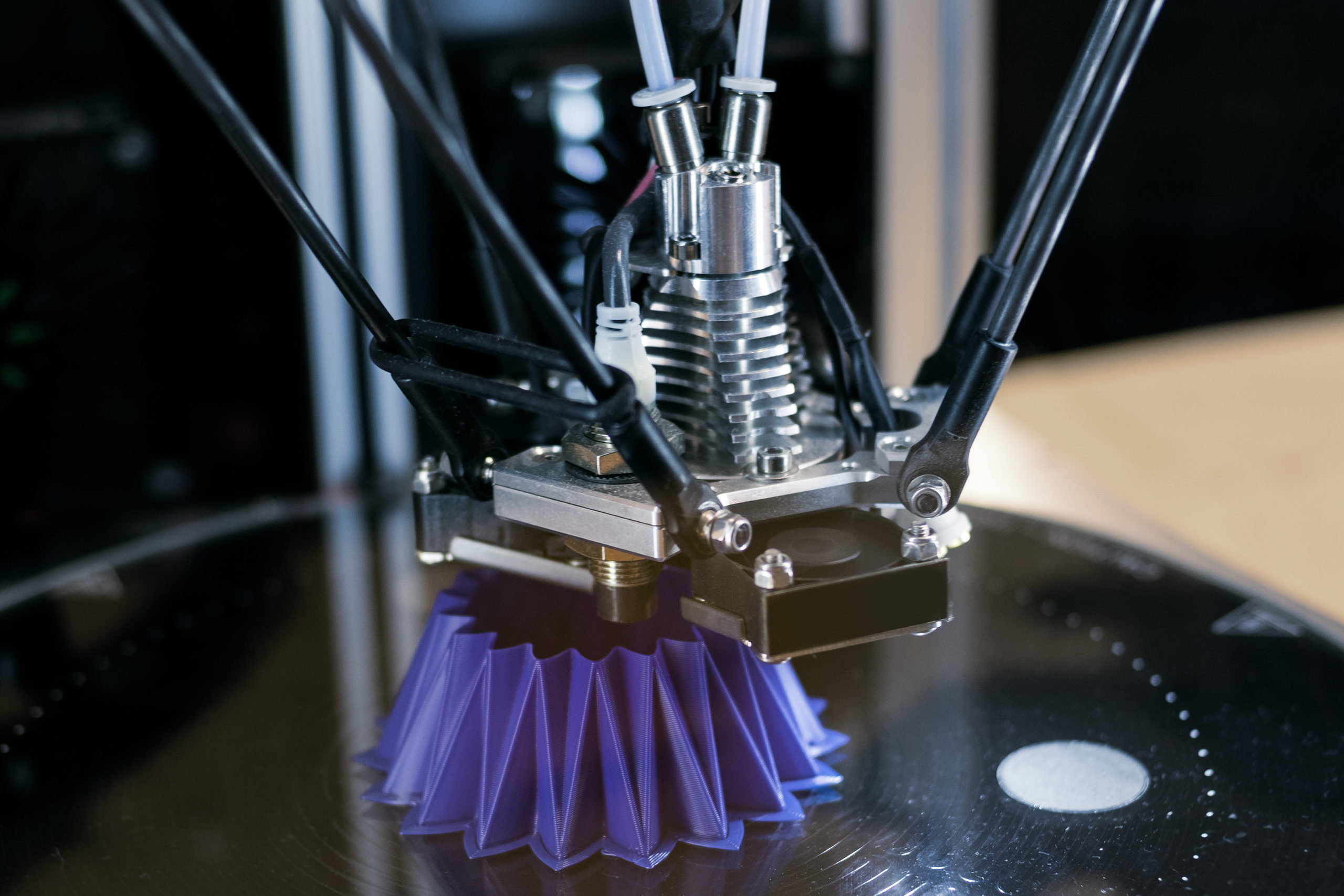
Polymer Additive Manufacturing Markets and Applications: 2020-2029
$2,750.00 – $3,750.00
Select options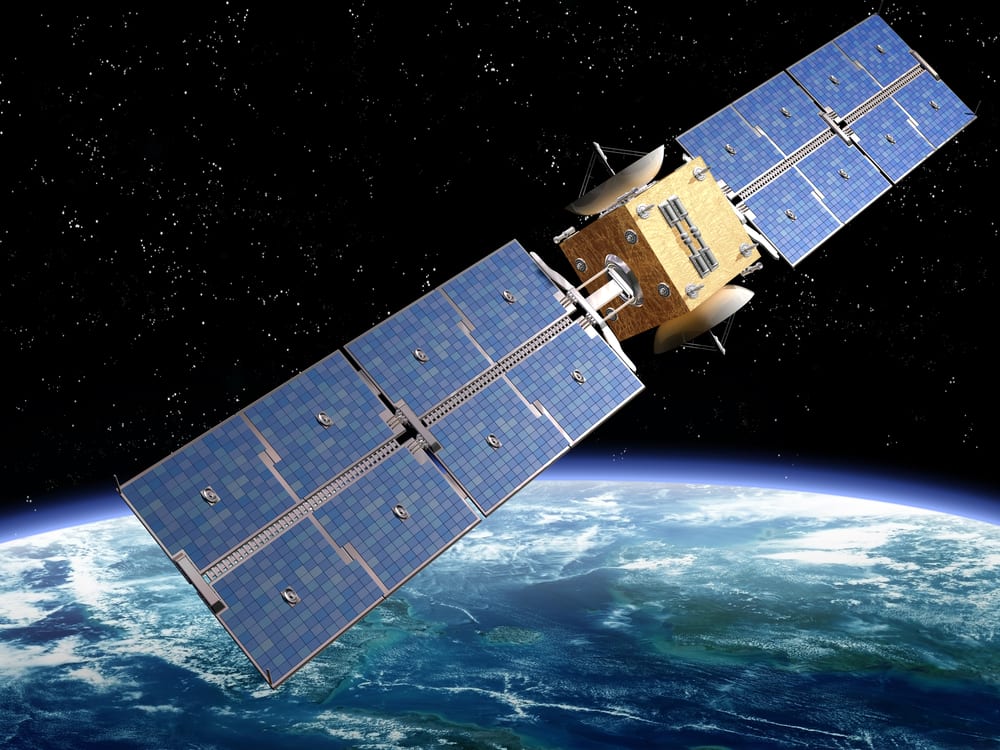
Additive Manufacturing For Space Industry Applications – From Earth To Orbit And Beyond: An Opportunity Analysis And Ten-year Forecast
$1,248.50 – $1,748.50
Select options