The nuclear power industry is often overlooked. If we talk about nuclear power it’s usually a discussion about whether it is the solution to our climate change woes or an inherently dangerous technology. Nuclear power is always associated with risk due to Fukushima and other nuclear accidents. The industry results in some of the most technologically advanced, complex and expensive construction projects that humankind undertakes. Right now there are 53 nuclear power plants under construction. Each one costs around $5 to $9 billion to build. In some cases cost overruns have doubled cost estimates. Now with rising interest rates, these expensive plants will be a bit less likely, and the cost to build plants per kilowatt far outstrips that of other sources of energy. Nuclear is a very efficient power-generating technology overall however, and gives countries energy independence that doesn’t depend on the weather. There are around 440 operational nuclear reactors in existence right now and the maintenance on them is also a substantial business. Companies such as TerraPower have also reinvigorated the market by offering newer nuclear technologies. Meanwhile, industry giant Toshiba has been in a state of financial discombobulation due to its purchase of the Westinghouse nuclear business.
The future of nuclear is far from assured. But, it is still going to be a considered technology and if it could be safe, would solve all of our energy problems. We’re already seeing a lot of things happening with 3D printing in the nuclear industry.
The University of Pittsburgh looked at making AM more efficient specifically for the nuclear energy industry. GE and Hitachi cooperated on a similar project to reduce the costs of AM. At Purdue, researchers are trying to 3D print microreactors. Also, Desktop Metal´s printers are being used to print silicon carbide parts for the Ultra Safe Nuclear Corporation (USNC).

From left to right, the original, obsolete impeller; the 3D printed prototype; and, the resulting 3D printed replacement part (Image: Siemens)
Siemens has installed at least one 3D printed part on a working nuclear power plant. First announced in 2017 for Slovenia´s Krško Nuclear Power Plant (NEK), these parts are helping to reduce maintenance costs. The first Siemens part was a 108 mm diameter metal impeller for a fire protection pump. The impeller´s manufacturer was out of business, making this an excellent case for the part to be 3D printed.
Westinghouse in turn has also 3D printed components for reactors. The firm demonstrated part integration as well as consolidation, and we know that reducing assembly steps through 3D printing can significantly reduce costs when quality is expensive and paramount.
Idaho National Lab has also looked at 3D printing safety testing and qualification equipment to make it faster and less expensive to create new parts for the nuclear industry.
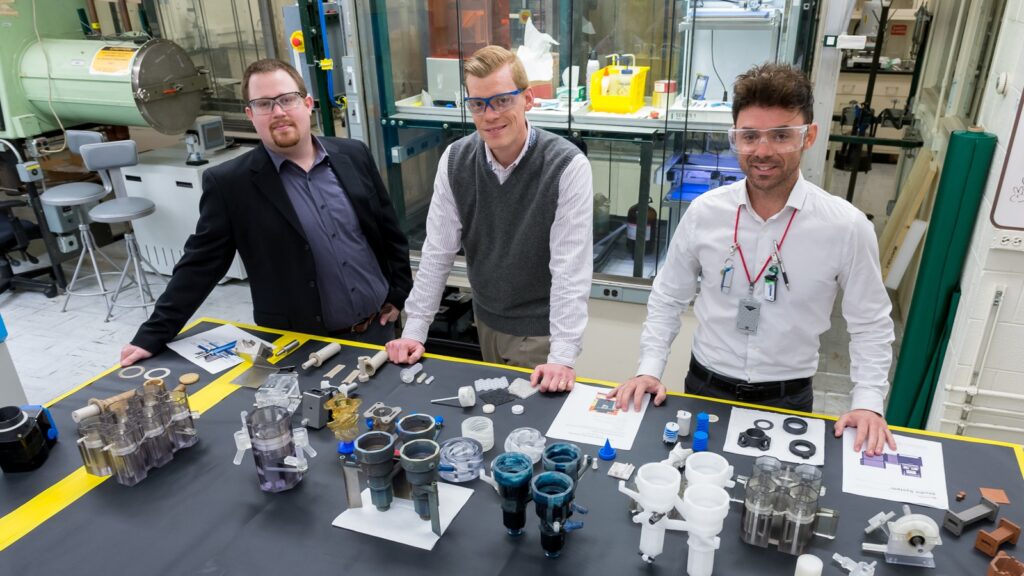
32783D, CFCT chemists group: Andrew Breshears, Peter Kozak, Alex Brown
Argonne National Lab scientists used 3D printing to make nuclear fuel recycling more efficient. The scientists believe that they could recycle up to 97% of used fuel produced by nuclear reactors through their continuous ALSEP process. They used a lot of 3D printed parts in their designs, with some even being made on Formlabs desktop 3D printers. 3D printing makes for more efficient fluid movement, and also allowed for more components to be integrated.
In another project, Argonne researchers were looking to recycle molybdenum more efficiently as well.
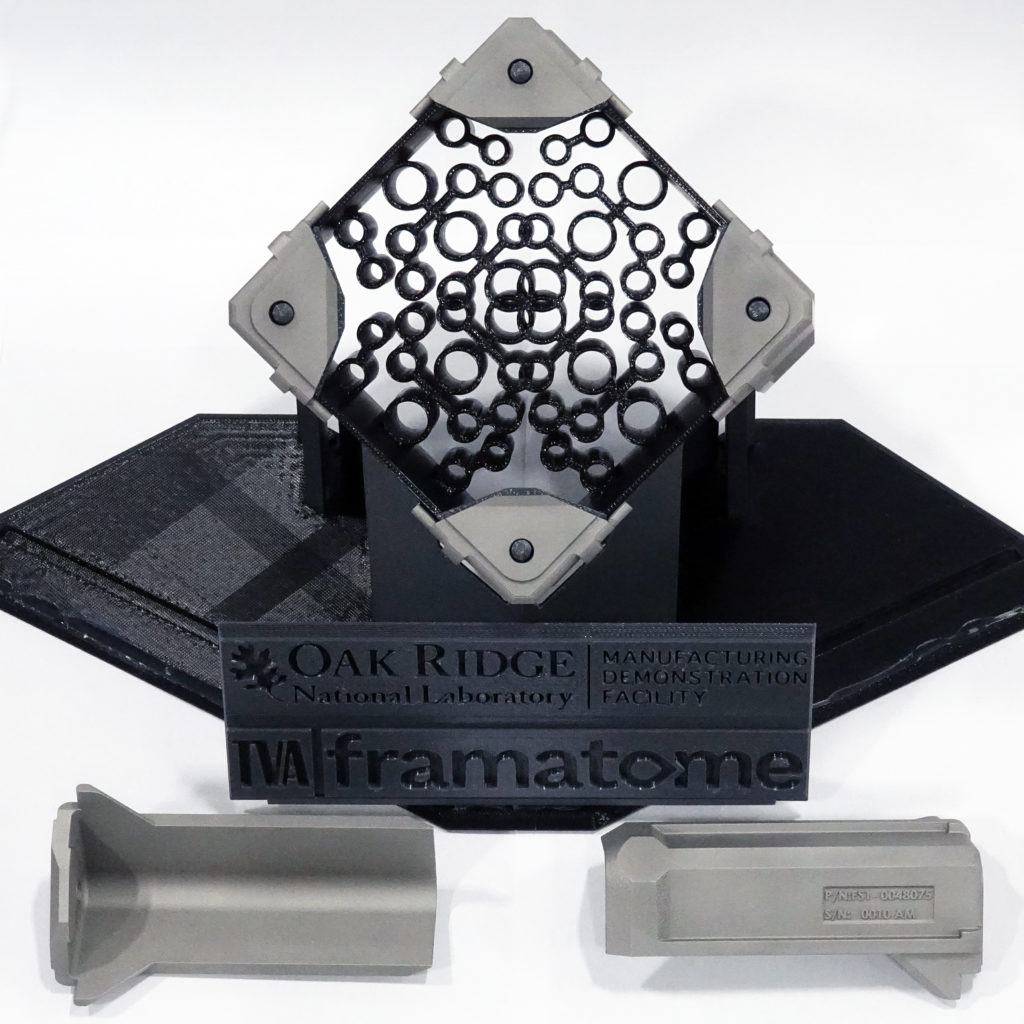
These fuel assembly brackets, manufactured by ORNL in partnership with Framatome and Tennessee Valley Authority, are the first 3D printed safety-related components to be inserted into a nuclear power plant. Image courtesy of Fred List/ORNL, U.S. Dept. of Energy
ORNL has made parts that have been used on a TVA nuclear reactor. These parts, made in cooperation with Framatome, are safety critical faster components. The “components secure the fuel channel to the boiling water reactor fuel assembly, with the fuel channel wrapping around the assembly and directing coolant through the fuel rods.” Every print layer was logged to ensure quality.
ORNL has also licensed a refractory metals Electron Bean Melting technology, as well as a binder jet with chemical vapor infiltration 3D printing method, for use in the 3D printing of reactor components. In addition, ORNL also used DED to make nuclear reactor cores.
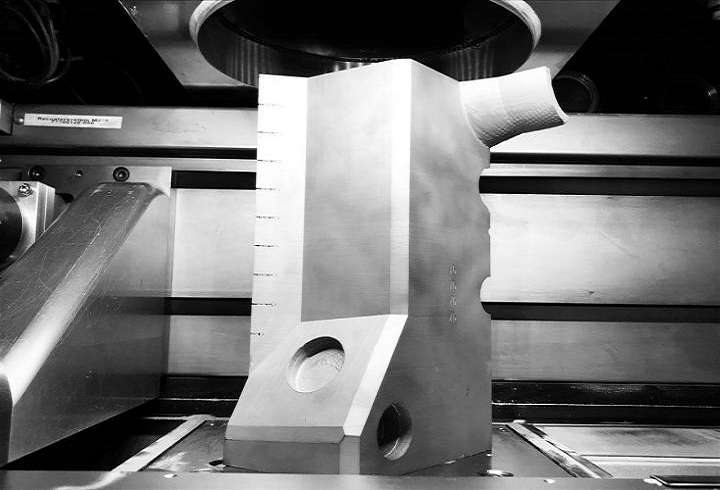
3D printed part for nuclear fusion test reactor. [Image: Dr. Leifeng Liu, University of Birmingham]
Another Chinese group is looking to optimise the core tritium production unit of nuclear fusion reactors with ceramic slurry components, such as those that can be made with Admatec or Lithoz.
In the development of a new generation of fusion reactors, and in the ongoing Tokamak projects worldwide, 3D printing could play an increasing role as well. In safety critical use cases, we know that part consolidation provides us with a lot of advantages. There is less assembly cost. Also, fewer assembly steps mean that there is lower risk. If we eliminate steps, we also eliminate human error, which could cause things like fasteners, welds, brazing and glue to react adversely or fail as well. In essence we are concentrating our manufacturing risk on the 3D printing step. We’re having less human interaction with parts and less parts being stored and carried around a lot as well.
We can optimise fluid transfer through making internal channels that are more highly optimised. We can direct fluid better but also slow it down, speed it up or heat and cool it more efficiently. We know that we can reduce mass through 3D printing as well. This is especially important, since every cubic centimetre of space that we save in a nuclear reactor means that we have to use less steel and concrete to encase it. Small savings could therefore have huge implications for construction projects. In developing new parts and making them, we could also potentially save money as well. Slightly more optimal surface textures or part properties could also have dramatic effects over the lifetime of a plant and its efficiency. There is significant volume in obsolete parts as well in all of the 440 plants currently in existence. There are also a lot of impellers and turbines in nuclear and other power plants, and we are particularly good at making those components. Nuclear energy also uses a lot of hard materials that are difficult to make with curing processes, and plenty of exotic materials that are difficult to make in general. Given the reach and criticality of the components in the nuclear industry, this is one sector that is currently being overlooked and should deserve more of your attention.
Subscribe to Our Email Newsletter
Stay up-to-date on all the latest news from the 3D printing industry and receive information and offers from third party vendors.
You May Also Like
Supply Chain Management and the Role of 3D Printing Digital Inventories
As the additive manufacturing (AM) industry grows beyond its humble roots as a rapid prototyping technology, it has been adopted by some of the world’s leading companies to produce not...
3D Printing Webinar and Event Roundup: April 28, 2024
In this week’s 3D Printing Webinar and Event Roundup, the Ceramics Expo is taking place in Michigan, Stratasys continues its advanced training courses, and SPE is holding a Polymer Characterization...
$25M to Back Sintavia’s Largest Expansion of Metal 3D Printing Capacity Since 2019
Sintavia, the digital manufacturing company specializing in mission-critical parts for strategic sectors, announced a $25 million investment to increase its production capacity, the largest expansion to its operations since 2019....
Velo3D Initiates Public Offering in a Bid to Strengthen Financial Foundations and Drive Future Growth
Velo3D (NYSE: VLD) has been among a number of publicly traded 3D printing firms that have attempted to weather the current macroeconomic climate. After posting a challenging financial report for 2023,...