‘This additional step may reduce the length of storage almost one thousandfold’ – Andrew Breshears, Argonne nuclear chemist
3D printing and additive manufacturing processes are progressing at lightning speed, but it’s nuclear materials scientists at the U.S. Department of Energy’s (DOE) Argonne National Laboratory are worried about. Emphasizing how important 3D printing is to the nuclear industry, scientists continue to delve further into the realm of new materials—along with using them to promote the recycling of very sensitive materials.
Previously, Argonne scientists have been able to recycle up to a staggering 95 percent of used fuel from a nuclear reactor; however, the five percent of fuel that is left still amounts to a lot of material to be stored. That is all changing now, however, as Argonne scientists are 3D printing parts for recycling even more, cutting into that five percent.
With their findings outlined in ‘Closing the Nuclear Fuel Cycle with a Simplified Minor Actinide Lanthanide Separation Process (ALSEP) and Additive Manufacturing,’ the scientists explain how ‘expanded low-carbon baseload power production through the use of nuclear fission can be enabled by recycling long-lived actinide isotopes within the nuclear fuel cycle.’ Further, they can recycle an additional two percent of the nuclear material, making an exponential difference still.
“Rather than store five percent for hundreds of thousands of years, the remaining three percent needs to be stored at a maximum of about one thousand years,” said Andrew Breshears, an Argonne nuclear chemist and co-author. “In other words, this additional step may reduce the length of storage almost one thousandfold. And breaking down that nuclear material in a fourth-generation fast reactor would generate additional electricity.”
The scientists were able to reach their goal by separating americium and curium from rare earth metals known as lanthanides. With AM processes, they were able to overcome ongoing challenges in converting their work from test tubes to the larger scale. In redesigning the processes that separate the chemicals, the researchers were able to 3D print ‘contactors’ and link them.
“This bridges the gap between separating the elements at the laboratory scale and at the industrial scale,” said Breshears.
In all, the scientists had to use a 36-step separation blueprint, separating 99.9 percent of the actinides from the lanthanides.

From: Closing the Nuclear Fuel Cycle with a Simplified Minor Actinide Lanthanide Separation Process (ALSEP) and Additive Manufacturing
“Their oxidation states are the same, making them very difficult to separate,” said Breshears.
The team also discovered that in using 3D printing, the contactors served as safeguards, with the tubes connecting the contactors preventing diversion of plutonium or radioactive materials. They also realized how helpful it was to have the flexibility offered by the 3D printed materials.
“If a part did fail, it would be easy to reprint and replace it. We could easily add or remove steps,” Argonne nuclear chemist and co-author Peter Kozak said.
“Maybe we will find a new way to cut down on the size of the process,” said Breshears. “The greater we can separate the actinides, the more we can reduce the impact they have on the public and environment.”
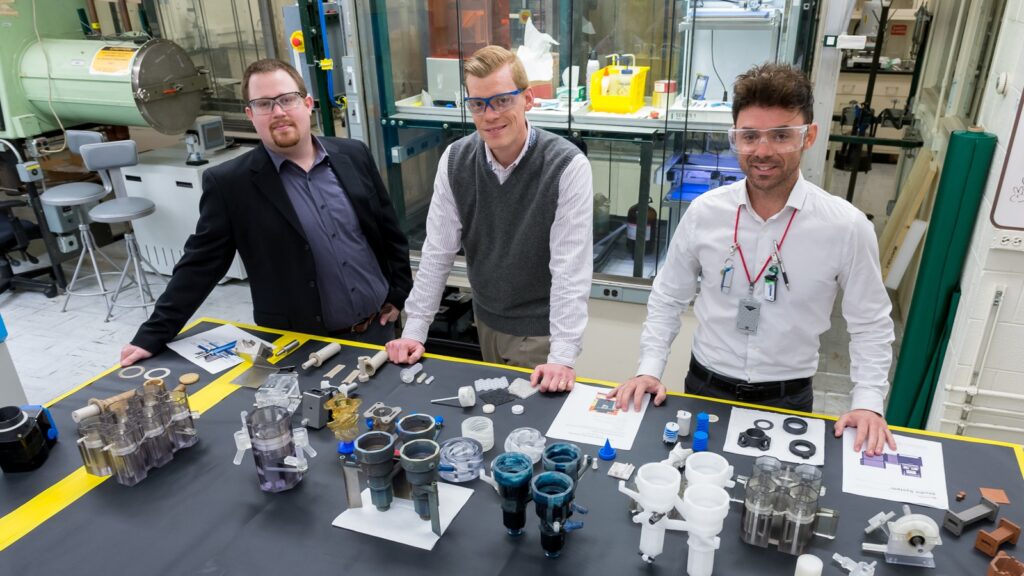
32783D, CFCT chemists group: Andrew Breshears, Peter Kozak, Alex Brown
Other Argonne co-authors include M. Alex Brown and Cari Launiere. The research was supported by the DOE Office of Nuclear Energy.
3D printing continues to produce one innovation after another, virtually every day. That means a lot of material is being used and made into products that produce waste and often become waste, whether because they were part of a failed print or an obsolete design, or for other reasons.
No one wants a greater accumulation of trash on the planet, so many companies endeavor to recycle, from turning used powder to filament, using composites, and also studying the comparisons between virgin and recycled materials.
What do you think of this news? Let us know your thoughts! Join the discussion of this and other 3D printing topics at 3DPrintBoard.com.
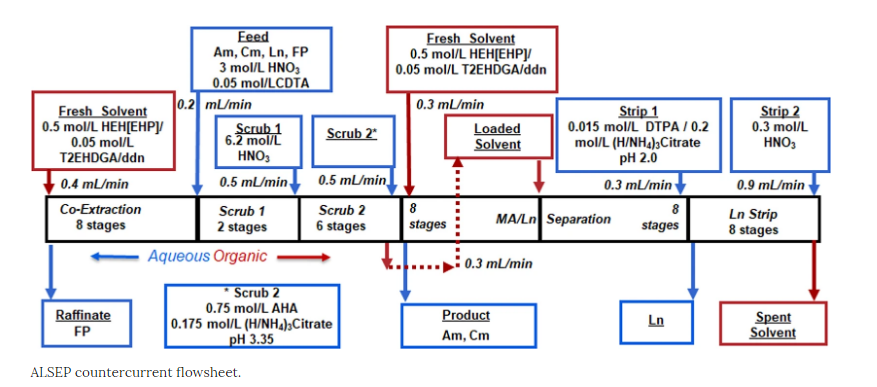
From: Closing the Nuclear Fuel Cycle with a Simplified Minor Actinide Lanthanide Separation Process (ALSEP) and Additive Manufacturing
Subscribe to Our Email Newsletter
Stay up-to-date on all the latest news from the 3D printing industry and receive information and offers from third party vendors.
Print Services
Upload your 3D Models and get them printed quickly and efficiently.
You May Also Like
3D Printing News Briefs, July 2, 2025: Copper Alloys, Defense Manufacturing, & More
We’re starting off with metals in today’s 3D Printing News Briefs, as Farsoon has unveiled a large-scale AM solution for copper alloys, and Meltio used its wire-laser metal solution to...
3DPOD 260: John Hart on VulcanForms, MIT, Desktop Metal and More
John Hart is a Professor at MIT; he´s also the director of the Laboratory for Manufacturing and Productivity as well as the director of the Center for Advanced Production Technologies....
3D Printing News Briefs, June 28, 2025: Defense Accelerator, Surgical Models, & More
In this weekend’s 3D Printing News Briefs, 3YOURMIND was selected to join an EU Defense Accelerator, and PTC has announced model-based definition (MBD) capabilities within Onshape. Finally, a study out...
EOS in India: AM’s Rising Star
EOS is doubling down on India. With a growing base of aerospace startups, new government policies, and a massive engineering workforce, India is quickly becoming one of the most important...