ABB Turbocharging is looking to convert its metal spare parts inventory with digital and 3D printed counterparts. To do so, it has turned to Dutch 3D printer manufacturer Additive Industries, purchasing its MetalFAB 1 3D printer platform.
ABB is relying on the laser powder bed fusion (LPBF) metal 3D printer to manufacture spare parts for its 500 kW to 80+ MW turbochargers for diesel and gas engines on-demand. The companies are optimizing the MetalFAB1 to replace the legacy casting process on which ABB currently uses. With over 200,000 turbochargers within its installed base of marine engine and emergency power generation business, casting has proven too inefficient for the job.
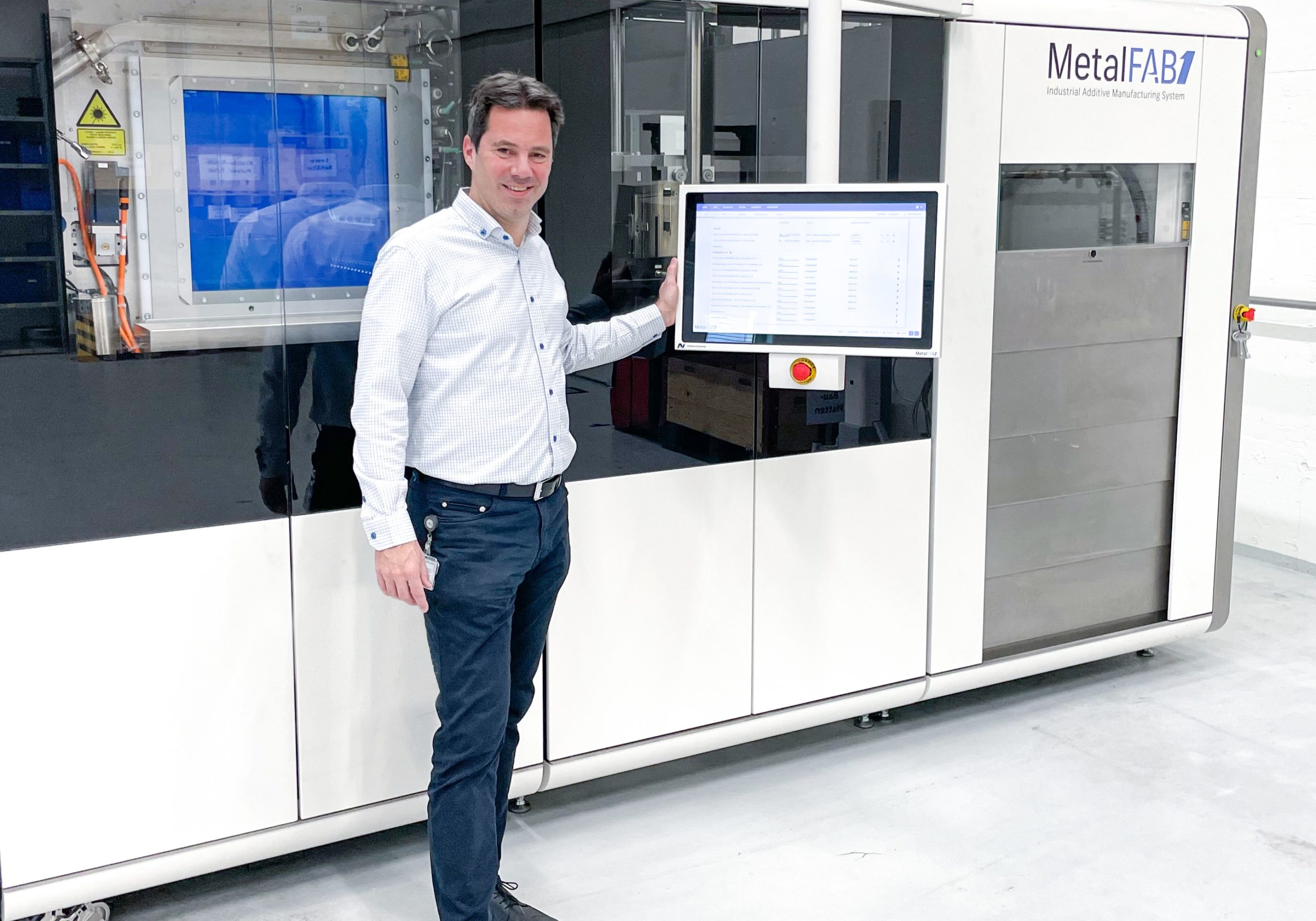
Egon Seegers, General Manager Service Parts of ABB Switzerland Ltd, Turbocharging next to the MetalFAB1 system. Image courtesy of Additive Industries.
The company notes that casting lead times can take up to nine weeks, which in turn requires housing spare parts in inventory. With the LPBF machine, turnaround times can be cut down to a single week, thus freeing up inventory space.
“With ABB we have added another market leader to our very focused list of customers. They are committed to drive progress in the domain of digital spare part manufacturing, very relevant in a time where shortening the lead times and limiting logistical movements around the world is key,” said Ian Howe, CEO of Additive Industries.
“ABB services over 200.000 turbochargers around the globe on ships, in power stations, generatorsets, diesel locomotives and large, off-highway vehicles. The potential for on-demand 3D printing of spare parts is immense,” said Mark Massey, Additive Industries’ CCO.
With 2021 revenues of about $28.9 billion, ABB (NYSE: ABB) is a Swiss multinational manufacturing corporation involved in robotics, power, heavy electrical equipment, and automation. Until 2020, when it sold its Power Grids division, it was Switzerland’s largest industrial employer.
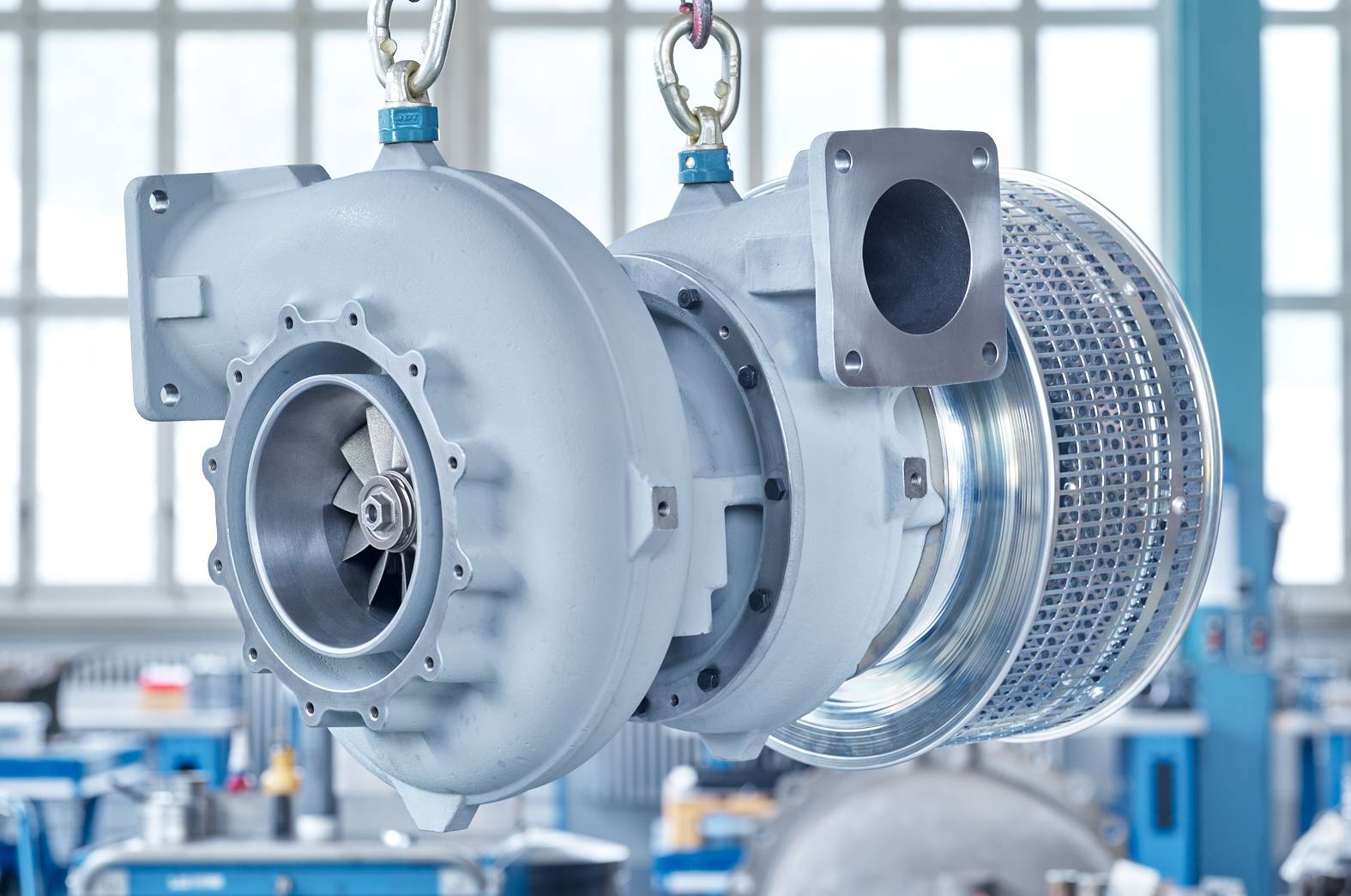
ABB Turbocharging equipment. Image courtesy of ABB.
The company has also expressed regular interest in additive manufacturing (AM). Its robotic arms have been widely used in material extrusion systems, which ABB regularly supports. This includes machines for 3D printing graphene, compostable toilets, carbon fiber, and metal bridges. The popularity of its equipment in 3D printing has been so great that ABB even introduced a 3D printing component to its RobotStudio software.
What we have yet to see is the company embark on 3D printing for the production of its own parts. The spare parts space is where many have long anticipated 3D printing to begin penetrating industrial manufacturing. As a technology capable of producing complex, one-off components on-demand, it is ideal for replacing physical stock. In turn, it could potentially replace actual warehouses with digital ones. Now that the technology is maturing the point where it can repeatability and reliable produce quality items to specification, we may begin seeing this model become more of a reality.
Turbochargers in particular are ideal for AM. As 3DPrint.com Senior Editor Sarah Saunders put it, “Combustion engines uses turbochargers to boost their performance. But, for multiple reasons, there isn’t a conventional process chain for economically manufacturing the component.” For this reason, we’ve seen numerous examples of 3D printed turbochargers from the likes of FIT AG and GE. We may even see Cummins introduce additive to its turbocharger line.
According to the “Market Opportunities for Additive Manufacturing in the General Industry and Tooling Sector 2020-2029” report from SmarTech Analysis, additive for the industrial sector is expected to be a $5.48-billion market by 2029. 3D printed spare parts are expected to play a crucial role in this development.
This could be a significant move for a large manufacturer that sees wider adoption of 3D printing across its business lines. However, ABB is also considering the sale of the turbocharging division, rebranding it “Accelleron” with a possible goal of spinning the unit out or offloading it to someone else altogether. Regardless, it’s an important step toward the widespread industry adoption of AM, as well as virtual inventory and distributed manufacturing.
Feature image courtesy of ABB.
Subscribe to Our Email Newsletter
Stay up-to-date on all the latest news from the 3D printing industry and receive information and offers from third party vendors.
You May Also Like
NSF Awards Kentucky $1M for Advanced Manufacturing
The National Science Foundation has awarded a $1 million grant to the University of Louisville for the Advancing Manufacturing and Building Construction Technologies (NSF AMT) project. This initiative is part...
3D Printing News Briefs, May 11, 2024: 3D Printed Stent, Tower, Sculptures, & More
We’re starting off with medical research in today’s 3D Printing News Briefs, as researchers in Korea used CT images and 3D printing to fabricate an educational simulator for a mastoidectomy....
3D Printing Unpeeled: Wind Turbines, Probiotics and Lenses
TPI Composites, ORNL and Ingersoll Rand are working to make wind turbine tooling segments that can be 18.3 meters long. These elements also include resistive wires that help keep the...
Tethon 3D Releases Cost-effective Bioprinter
Tethon 3D, known for its ceramic-loaded DLP materials, custom resins, and DLP 3D printers, has recently released a bioprinter. Vat polymerization printers like DLP systems have been widely used by...