Researchers Complete Comprehensive Evaluation of Manufacturing Methods, Including 3D Printing, for Impellers
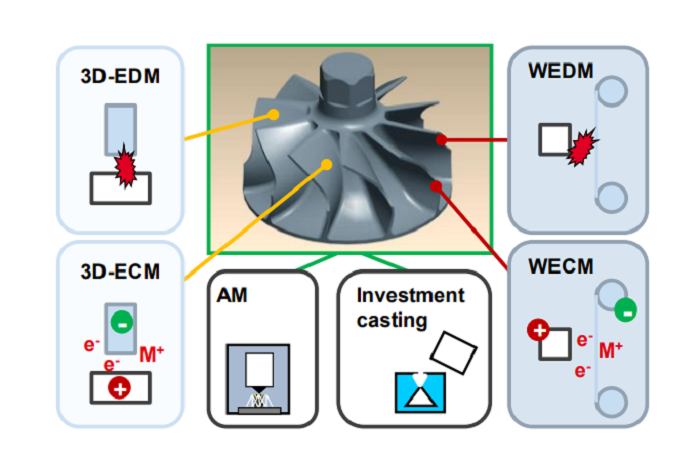
EDM and ECM finishing of near-net-shape turbo charger wheels produced by additive manufacturing and investment casting.
Combustion engines uses turbochargers to boost their performance. But, for multiple reasons, there isn’t a conventional process chain for economically manufacturing the component. A team of researchers from RWTH Aachen University and Robert Bosch GmbH recognized the need for a comprehensive evaluation of alternative manufacturing methods for impellers – 3D printing isn’t the only way – and set out to deliver. They published their results in a paper, titled “Technological and Economical Assessment of Alternative Process Chains for Turbocharger Impeller Manufacture.”
The abstract reads, “In this paper, different manufacturing chains consisting of pre-finishing and finishing of near-net-shape parts are compared to each other for a given example geometry. Electrochemical as well as Electrical Discharge Machining technologies are taken into account as alternatives for conventional milling and grinding processes for the finishing of cast blanks or samples produced by additive manufacturing. Based on a technological analysis a cost comparison is executed, which allows an economical assessment of the different process chains regarding given boundary conditions and varying production quantities.”
In addition to electrochemical (ECM) and electrical discharge machining (EDM) technologies, the team also looked at wire-based technology variants (WEDM/WECM) for outer straight geometries, and 3D-(Sinking)-based technologies for inner flow ones. They completed a cost comparison of the methods, based on technological analysis, which, as the researchers wrote, “allows an economical assessment of the different process chains regarding boundary conditions and production quantities.”
Turbocharger wheels – blank manufacturing by investment casting (near-net-shape and finish contour) or additive manufacturing and conventional finishing by milling and grinding
“In a first step a technological process analysis took place for both alternative primary shaping processes of turbocharger wheel blanks and for finish machining of near-net-shape geometries by conventional as well as unconventional advanced machining processes,” the researchers wrote. “Target values were a geometrical precision better than 0.05 mm and a minimum surface roughness of Rz = 4 µm.”
Fine investment casting can be used to manufacture a blank with defined material allowance, as well as electron beam melting (EBM) 3D printing, though the latter with require post processing because of insufficient geometrical precision and a rough surface. It’s possible to finish with 5-axis milling, but due to extensive tool wear, it will require a lot of effort. The team determined that abrasive flow machining and vibratory grinding would not work.
“All technological necessary efforts have been evaluated and aggregated in a production cost ratio relative to the standard investment casting process as basis,” the team wrote in the paper. “This includes tool costs (purchase costs and life time), raw material costs (melt / powder material), energy (average energy consumption) and working costs (salary and multiple machine work) as well as machine costs (investment, net book value, space, maintenance, machining time per part) for main and secondary process like hot isostatic pressing (HIP) – imperative for the EBM parts – and washing. Additional industrial boundary conditions were a yearly lot size of 150,000 parts and working time of 4,800 h. The earnings per worker amounts to 43.75 €/h, the energy price and monthly space costs are 0.128 €/kWh and 12 €/m² respectively. The imputed interest rate is 10 %.”
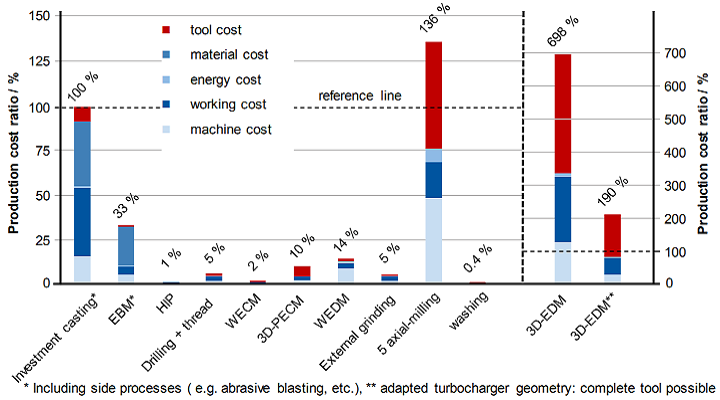
Production costs of different primary shaping and finish machining as well as handling processes relative to the investment casting process.
Alternative EDM- and ECM-based processes were also included in the diagram.
The researchers explained that the microstructures from 3D printing and casting processes had a major influence on the final surface roughness. In addition, the ECM-processed material was analyzed, and basic EDM research showed that for the TiAl material, the correct electrical polarity had to be clarified. By applying a new flushing concept based on WECM, the team was able to achieve higher ECM cutting rates in a “competitive order of magnitude of 20 mm²/min also for macroscopic workpiece heights.”
It was determined that, under the boundary conditions laid down, 3D-EDM is not a competitive or efficient single process, but 3D-ECM is, when compared to 5-axis milling. Additionally, WEDM and WECM showed low costs.
“It can be concluded that the process chains involving 3DEDM are not suitable as their cost ratios are higher than 300 % of the reference but the ECM variants reveal significant advantages due to much lower cost ratios. In addition for the basis costs, the AM produced raw blanks reveal lower cost ratios compared to the investment casted ones – even for the given series production,” the researchers wrote.
These results are due to the specific material properties of the TiAl material. Because of low costs for the outer geometry finishing, the contour casted samples also had higher cost ratios.
“As a conclusion – for the given boundary conditions – the process chain including 3DECM and WECM of AM produced blank wheels achieved the lowest costs and was therefore the most efficient one,” the researchers wrote. “Further work should include detailed studies on surface integrity for the different machining processes and appropriate positioning.”
Co-authors of the paper are A. Klink, M. Hlavac, T. Herrig, and M. Holsten.
Subscribe to Our Email Newsletter
Stay up-to-date on all the latest news from the 3D printing industry and receive information and offers from third party vendors.
Print Services
Upload your 3D Models and get them printed quickly and efficiently.
You May Also Like
Heating Up: 3D Systems’ Scott Green Discusses 3D Printing’s Potential in the Data Center Industry
The relentless rise of NVIDIA, the steadily increasing pledges of major private and public investments in national infrastructure projects around the world, and the general cultural obsession with AI have...
Formlabs Teams Up with DMG MORI in Japan
In late June, Nick Graham, Chief Revenue Officer at Formlabs, announced on LinkedIn that the company had partnered with DMG MORI, one of the world’s leading machine tool companies, to...
EOS in India: AM’s Rising Star
EOS is doubling down on India. With a growing base of aerospace startups, new government policies, and a massive engineering workforce, India is quickly becoming one of the most important...
3D Printing News Briefs, June 25, 2025: R&D Materials, 3D Printed Veneers, & More
In today’s 3D Printing News Briefs, 3DXTECH has launched a program that gives customers early access to experimental materials, and the first Lithoz CeraFab Multi 2M30 in the Czech Republic...