Researchers Yongsan An and Woon-Ryeol Yu explore improved 3D printing through the study of alternative materials. In the recently published ‘Three-dimensional printing of continuous carbon fiber-reinforced shape memory polymer composites,’ the authors discuss challenges with mechanical properties that plague many industrial users.
In this study, they experiment with continuous carbon fiber reinforced shape memory polymer composites (SMPC), in FDM 3D printing—using both thermoplastics and thermosets.
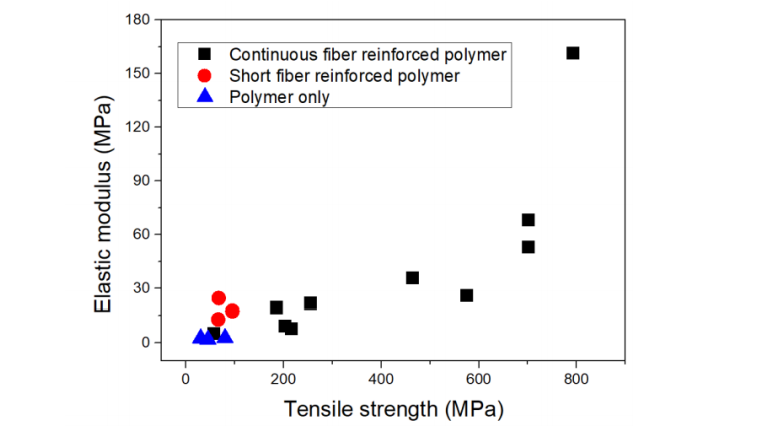
Mechanical properties of continuous fiber-reinforced polymer composites, short fiber reinforced polymer composites, and polymer matrix fabricated by FDM.
Parameters were tested, and samples were printed, as the researchers learned more about the benefits and limits of smart materials like SMPs—able to change with their environment and then morph back to their normal shape. This type of material borders on the 4D and allows users much greater flexibility in use—across a wide variety of applications. With the addition of carbon composites, the research team hoped to improve fabrication processes.
The team created a customized FDM 3D printer for the study, to fabricate continuous fiber-reinforced SMPC parts. For materials, two different types were chosen for evaluation: PLA and a polyurethane-type of SMP filaments (as the thermoplastic matrices) and an SMP epoxy as the thermoset matrix. The team then added the continuous carbon fibers for reinforcement to the filament.
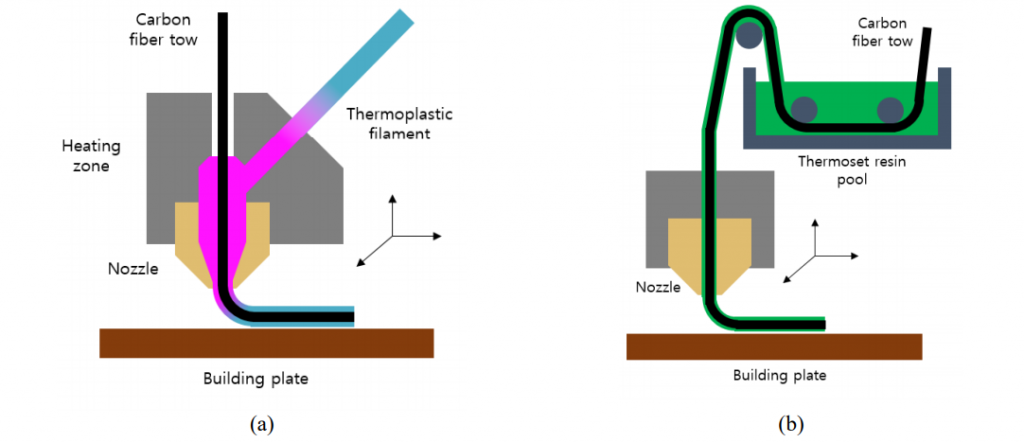
Schematic diagram of the 3D printing system of continuous carbon fiber-reinforced polymer composites for (a) thermoplastics and (b) thermosets.
They experimented with differences in temperature and print speed in printing out samples to be tested. Mechanical and shape memory properties were then assessed by the team.
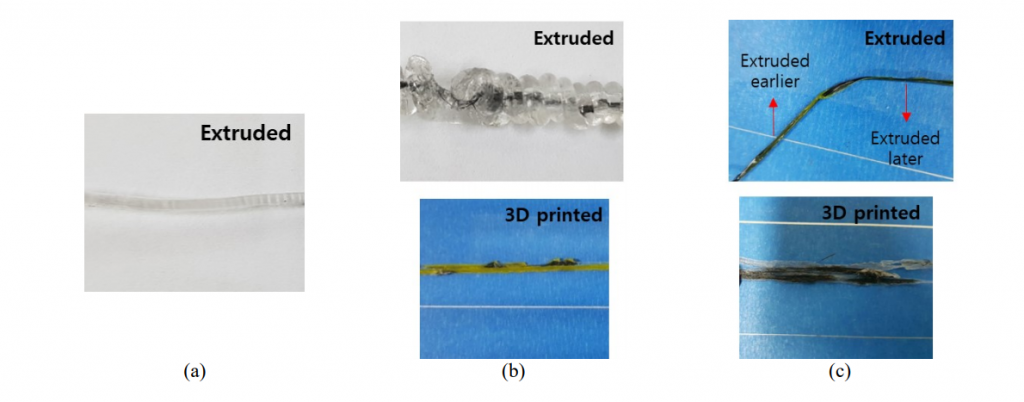
3D printing of CF and PLA composites. (a) only PLA, (b) 1.5 mm-diameter nozzle, and (c) 2 mm- diameter nozzle.
“The storage modulus (G’), loss modulus (G’’), and the viscosity of the PLA were decreased around its melting point. The storage modulus was decreased at a larger rate than the loss modulus, resulting in more liquid-like properties of PLA. Therefore, the PLA could be easily extruded from the nozzle of which temperature was 180℃,” the researchers wrote.
“The PLA filament without CF was smoothly extruded from a nozzle whether its diameter was larger than the fusion area or not. However, for a nozzle with 1.5 mm diameter, the PLA matrix was extruded like wrapping the CF helically. It was due to a fact that the PLA was extruded more than the CF because the CF was not stretched during extrusion. In addition, harsh temperature and different extrusion speed caused CF to fail during 3D printing. On the other hand, for a nozzle with 2 mm diameter, the PLA and CF were extruded straightly because their extrusion speeds were synchronized.”
There were numerous challenges—such as the CF not coated completely with PLA. The researchers created an improved printhead for better optimization in terms of supplying speed of PLA and CF and the structure and fusion time of the materials. They also added calendar rolls and a proper tension device.
“The printed SMPC showed good mechanical properties compared to those of conventionally 3D printed polymer in the fiber direction,” stated the researchers.
Strength and stability in mechanical properties are a constant challenge in 3D printing—but there are constant improvements as researchers are determined to perfect the materials and processes of progressive fabrication techniques from testing carbon lattices, to titanium, to examining issues in biocompatibility.
What do you think of this news? Let us know your thoughts! Join the discussion of this and other 3D printing topics at 3DPrintBoard.com.
[Source / Images: Three-dimensional printing of continuous carbon fiber-reinforced shape memory polymer composites]Subscribe to Our Email Newsletter
Stay up-to-date on all the latest news from the 3D printing industry and receive information and offers from third party vendors.
You May Also Like
NSF Awards Kentucky $1M for Advanced Manufacturing
The National Science Foundation has awarded a $1 million grant to the University of Louisville for the Advancing Manufacturing and Building Construction Technologies (NSF AMT) project. This initiative is part...
3D Printing News Briefs, May 11, 2024: 3D Printed Stent, Tower, Sculptures, & More
We’re starting off with medical research in today’s 3D Printing News Briefs, as researchers in Korea used CT images and 3D printing to fabricate an educational simulator for a mastoidectomy....
3D Printing Unpeeled: Wind Turbines, Probiotics and Lenses
TPI Composites, ORNL and Ingersoll Rand are working to make wind turbine tooling segments that can be 18.3 meters long. These elements also include resistive wires that help keep the...
Tethon 3D Releases Cost-effective Bioprinter
Tethon 3D, known for its ceramic-loaded DLP materials, custom resins, and DLP 3D printers, has recently released a bioprinter. Vat polymerization printers like DLP systems have been widely used by...