One sector that’s been increasing its use of additive manufacturing (AM) is the maritime industry, with examples like submarine and subsea parts, and even underwater 3D printing. International ocean engineering and technology company DEEP recently launched the DEEP Manufacturing Limited (DML) business to fabricate and deploy large-scale, customized metal components for its underwater pressure vessels using wire arc AM (WAAM). DEEP uses WAAM for these components, which are used to build its subsea human habitats, but the business could potentially offer its services to other commercial customers—like those in aviation, energy, and offshore industries—who require large metal parts at speed. As such, the new company has also secured DNV Approval in Principle (AiP) for its use of WAAM to produce steel pressure vessels for human occupancy.
“It is a great pleasure to award DML this AiP and is another step forward in utilizing additive manufacturing at the cutting edge of the maritime industry,” said Dr Eva Junghans, Senior Principal Engineer, and Practice Lead for Materials & Welding, Additive Manufacturing at DNV Maritime. “This AiP shows that DML has demonstrated the feasibility of AM in the manufacture of large-scale components that can fulfil maritime quality standards – further expanding the potential uses of AM for our industry.”
The UK-based business was launched after DEEP went through a period of intense R&D. At its Advanced Manufacturing Centre of Excellence in Avonmouth, DML is operating one of the largest concentrations of WAAM systems in the world. There are 20 robotic WAAM printers at the COE, and each one can manufacture large-scale metallic parts with complex geometries. WAAM uses an electric arc to melt wire feedstock, which achieves a higher level of material quality, and also offers greater speed of production in comparison to traditional technologies like forging. The company can also synchronize the operation of a configuration of multi-arm systems, which supports the printing of parts up to 3.2 meters in height and 6.1 meters in diameter.
Its use of WAAM technology allows DML to drive scale, speed, and quality to improve commercial resilience and support supply chain growth.
“We’re excited about the opportunities ahead for DEEP Manufacturing. This spin out will enable us to drive the acceleration of our advanced manufacturing capabilities, bringing innovation and growth through automation and robotics,” said DEEP’s COO Louise Slade. “We believe this will create significant value and growth for the business and our employees here in the Southwest, and significantly contribute to driving Industry 4.0 growth globally.”
The manufacturer plans to double its workforce this year to meet increased demand for its manufacturing capabilities, and has added new roles at the Avonmouth COE across sales, production, several engineering disciplines, manufacturing, safety, and quality. As recently appointed CEO Peter Richards states, DML is “in a prime position to revolutionize the production of large-scale metal components across various industries.”
“We’ve developed a unique capability, backed by world-class technical expertise, that is contributing to the advancement of UK manufacturing.”
DML is currently in the final stages of the audit process to obtain DNV approval to produce pressure vessels for human occupancy with its WAAM systems, which proves how committed it is to safety, standards, and quality.
“We are the only company in Europe with this AiP, and we are already in the process of working towards final DNV approval for the production of steel pressure vessels. Our combined subsea engineering resources, knowledge and experience across DEEP means we can deliver manufacturing projects at an unprecedented scale, faster and at lower life of project costs compared to traditional manufacturing processes,” Richards said.
“Using DEEP Manufacturing’s additive manufacturing process allows companies to stay ahead of the game in their subsea projects. Additive manufacturing is the fast, safe solution to manufacturing large-scale, complex metal parts.”
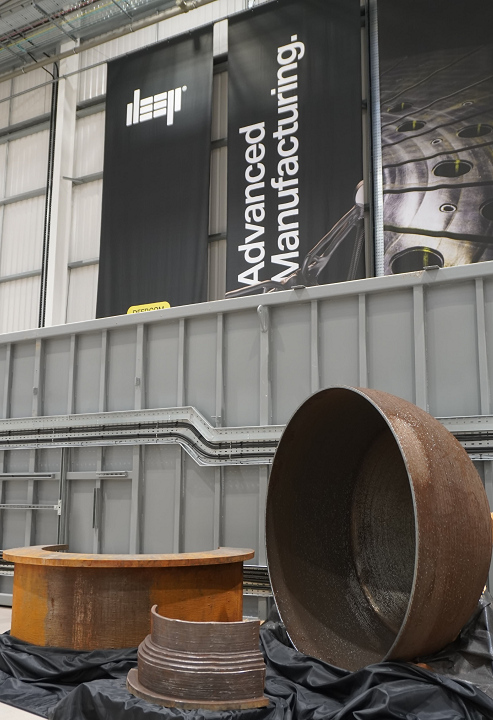
A selection of parts manufactured by DEEP Manufacturing Ltd using the Wire Arc Additive Manufacturing (WAAM) process.
An Approval in Principle (AiP) is an independent assessment of a concept within an agreed framework. It confirms that the suggested design is feasible, and that no major obstacles exist to prevent the concept from coming to fruition.
“If subsea companies are still relying on traditional forge and casting methods, they risk falling behind,” Richards continued. “There is a need for a mindset shift toward innovation and proactive measures to enhance industry-wide resilience. As we move forward, we want to support our customers to embrace innovation and build more adaptable, resilient operations. This is a tipping point for our industry, and it is time to fully leverage the benefits that additive manufacturing offers.”
The world’s leading classification society, DNV is an independent expert in quality assurance and risk management, and helps to advance safety and performance, as well as set industry benchmarks. DNV is very familiar with AM technology, and is also a recognized advisor for the maritime industry, investing in R&D to work with industry to find solutions that address operational, regulatory, and strategic challenges.

Thorsten Lohmann, Head of the Materials & Welding Section at DNV Maritime and Dr Eva Junghans, Senior Principal Engineer, and Practice Lead for Materials & Welding, Additive Manufacturing at DNV Maritime, present Louise Slade, COO DEEP Manufacturing Ltd and Harry Thompson, Technical Director, DEEP Manufacturing Ltd with the Approval in Principle certificate.
“At DNV we have been working with manufacturers on safely realising the unique capabilities of additive manufacturing for many years with our class framework, rules and guidelines,” said Thorsten Lohmann, Head of the Materials & Welding Section at DNV Maritime. “Going forward we will continue to help our customers show that AM produced parts can be accepted under the class regime, driving progress and acceptance of this exciting technology.”
Source/Images: DEEP Manufacturing Limited
Subscribe to Our Email Newsletter
Stay up-to-date on all the latest news from the 3D printing industry and receive information and offers from third party vendors.
Print Services
Upload your 3D Models and get them printed quickly and efficiently.
You May Also Like
Making Space: Stratasys Global Director of Aerospace & Defense Conrad Smith Discusses the Space Supply Chain Council
Of all the many verticals that have been significant additive manufacturing (AM) adopters, few have been more deeply influenced by the incorporation of AM into their workflows than the space...
EOS in India: AM’s Rising Star
EOS is doubling down on India. With a growing base of aerospace startups, new government policies, and a massive engineering workforce, India is quickly becoming one of the most important...
PostProcess CEO on Why the “Dirty Little Secret” of 3D Printing Can’t Be Ignored Anymore
If you’ve ever peeked behind the scenes of a 3D printing lab, you might have caught a glimpse of the post-processing room; maybe it’s messy, maybe hidden behind a mysterious...
Stratasys & Automation Intelligence Open North American Tooling Center in Flint
Stratasys has opened the North American Stratasys Tooling Center (NASTC) in Flint, Michigan, together with automation integrator and software firm Automation Intelligence. Stratasys wants the new center to help reduce...