For a long time, I’ve bemoaned the lack of systems integrators in 3D printing. We have resellers who will sell you a box and help you troubleshoot its contents. But, we don’t really have firms that will integrate printers, scanners, and robot arms and make the perfect 3D printing manufacturing solution for you. If you want to automate everything from software to parts getting put in boxes, then right now, you’ll mostly have to do this yourself. It is unreasonable for us to expect people to do this, and it slows down the adoption of AM, keeping us a promising cottage industry with so much potential but no immediate future.
That’s why I’m so enthusiastic about Max Resolution 3D. This German firm is an automated production provider making parts in Berlin. You can meet with them, and they’ll discuss your part needs. They will test and see if the material and part are viable. Then they will do a production run in house for up to 50,000 parts. The team wishes to “make the series production via 3D printing accessible for everyone, especially the Small & Medium Enterprises.” Eliminating “over-production or unnecessary plastic waste through production on demand, no supply chain failures through local production in Berlin, and no high investment costs in injection molding tools.” To do this, the team has coupled Nexa3D printers with a robot arm in a production cell to automate the process.
The Max Resolution team didn’t have to develop this production cell themselves; instead, it was made by another German startup, Production to Go. This company makes the cells which it claims can make example parts such as a COVID Swab “500 parts in 148 minutes, theoretical number of items per year: 800,000, print jobs per year: 1,600.” Production to Go also makes cells for the Stratasys RPS, a printer I adore, and sells the Smart3D, which is purported to be a large FDM production system with a heated chamber.
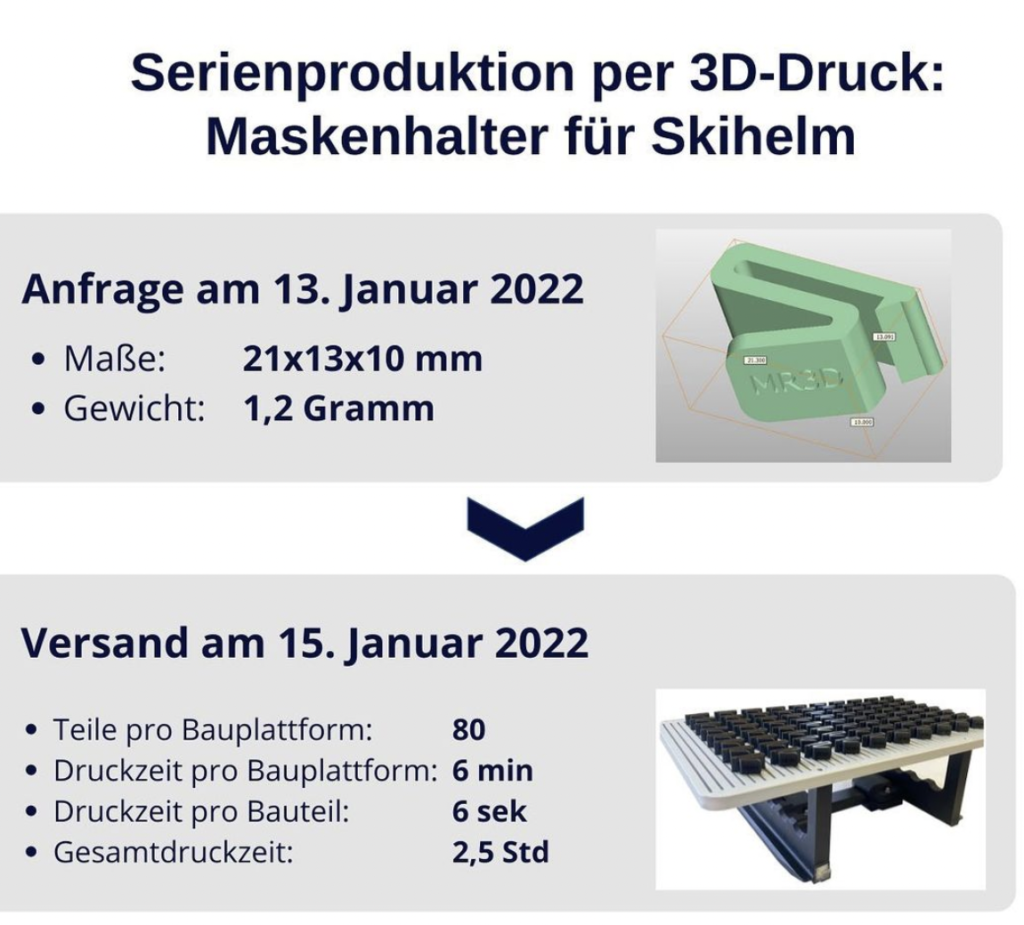
Max Resolution gives as an example a clip that they got a request for and two days later came up with a calculation for. Image courtesy of Max Resolution.
In this case, these startups are aiding each other by making 3D printing more accessible. This builds value for the OEMs by making their products more suitable for low-cost manufacturing and more likely to be bought quickly as a part of an implementable manufacturing solution. At the same time, extra innovation, work, and capital are being put into making their systems suited for manufacturing, and they don’t have to do anything just focus on making a better 3D printer. These firms are really a force multiplier for each other and our industry. They can lower barriers to entry and hasten sales and implementation cycles.
By focusing, they could make industry-specific or even part-specific solutions that could further quicken adoption and make parts less expensive. Overall what they are doing is taking a powerful box and turning it into a manufacturing solution. And yes, we know that everyone already offers solutions in the press release. But, in reality, 3D printing for manufacturing today is a guy opening a box and then filing down or cutting away things by hand before moving them to another box or two. This is silly and will never work in terms of cost, reliability and repeatability. If we want to make true manufacturing solutions and really manufacture at scale, then we will need services and systems integrators like these companies.
Through networks of these firms reselling, creating, and deploying manufacturing solutions, we can penetrate the globe. Of course, Nexa3D or Stratasys don’t need to be everywhere or don’t need to make the perfect solution for manufacturing for every use case, but other players in the market can do this. This kind of behaviour and market evolution with resellers taking on more of an integration role and offering more than boxes is a sign of maturity. I really believe that such behaviour can lower part costs and help deploy 3D printing in more places more rapidly. What other examples have you seen of a network of integration and automation companies emerging? What other helpful signs do you see in our industry of our maturity?
Subscribe to Our Email Newsletter
Stay up-to-date on all the latest news from the 3D printing industry and receive information and offers from third party vendors.
Print Services
Upload your 3D Models and get them printed quickly and efficiently.
You May Also Like
Heating Up: 3D Systems’ Scott Green Discusses 3D Printing’s Potential in the Data Center Industry
The relentless rise of NVIDIA, the steadily increasing pledges of major private and public investments in national infrastructure projects around the world, and the general cultural obsession with AI have...
Formlabs Teams Up with DMG MORI in Japan
In late June, Nick Graham, Chief Revenue Officer at Formlabs, announced on LinkedIn that the company had partnered with DMG MORI, one of the world’s leading machine tool companies, to...
EOS in India: AM’s Rising Star
EOS is doubling down on India. With a growing base of aerospace startups, new government policies, and a massive engineering workforce, India is quickly becoming one of the most important...
3D Printing News Briefs, June 25, 2025: R&D Materials, 3D Printed Veneers, & More
In today’s 3D Printing News Briefs, 3DXTECH has launched a program that gives customers early access to experimental materials, and the first Lithoz CeraFab Multi 2M30 in the Czech Republic...