“AM doesn’t require expensive custom tooling prior to manufacturing a needed part. Since niche applications are low-volume applications, they are particularly well-suited for AM. The cost of the tools used in traditional manufacturing is only amortized over a relatively small production volume, and thus the cost per part is very high. In AM, the cost per part is moderate regardless of the production volume.”

“Absolutely. AM is already used extensively in mass manufacturing. For instance, custom dental aligners are produced in volumes of tens of millions per year via AM. This, by any measure, is mass manufacturing. Over 100,000 jet engine fuel nozzles have been produced by AM, which is mass manufacturing for aerospace. As manufacturers explore other applications where the digital workflow and the complexity of parts made by AM create unique market advantages, I believe AM will continue to be adopted for more mass manufacturing applications.”
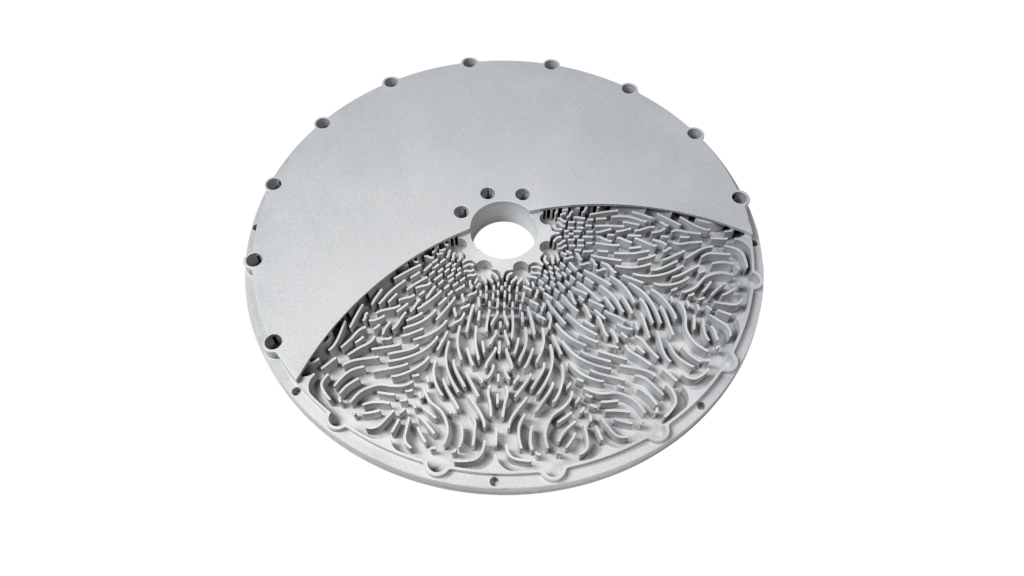
Better thermal management of wafer tables can simultaneously improve semiconductor equipment accuracy by 1–2 nm, as well as speed and throughput. (Image courtesy of 3D Systems.)
I like that bullish and positive approach from Dr. Stucker. However, the really important aspect is where he noted that “the digital workflow and the complexity of parts made by AM create unique market advantages.” This is something that I think so many people get wrong.
To shift to 3D printing, it’s almost as though something has to be unique and create a real advantage to be worth the bother. Often, we just see businesses lightweight a part that then costs six times more and takes a week to make. In such cases, people are looking at implementing 3D printing without there ever really being a chance that this part is significant or will alter their fortunes. I think of this in terms of stacking, whereby, if we look at a really successful case such as orthopedic implants, we can see as many as 18 distinct advantages that 3D printed metal orthopedics have over conventional ones.
“We believe that manufacturing at scale with AM is already beginning to happen. At Stratasys, with a single printer we can produce over 200,000 parts on the machine in a year. Our team at Origin, for example, produced more than 500,000 nasal swabs during the first peak of the pandemic in 2020. We are seeing more and more examples of customers manufacturing at scale with AM. Analysts are predicting that AM at scale will accelerate in the next five years and we are certainly counting on it,” Carey said.
“Yes, almost all manufacturers who have adopted AM are using it alongside their traditional manufacturing processes. We don’t see it as an ‘either-or’ but as an “and”. There are, of course, a few exceptions and we could see dental labs moving to 100% AM. Also, in healthcare applications, we could see a different percentage split between traditional and additive manufacturing, mostly due to the personalized nature of healthcare. The other exception here are AM service bureaus, but that said, some of them have a mix of traditional manufacturing and AM.”
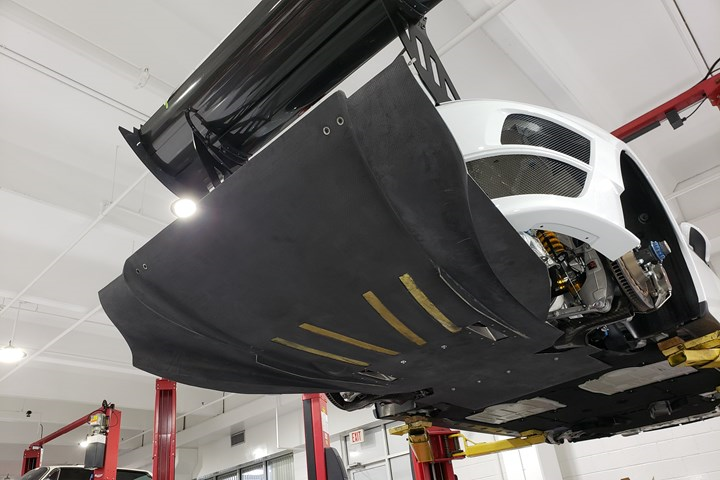
Stratasys 3D printed 16 total components for Champion Motorsports’ recently modified Porsche race car. The largest component (pictured) was a 7 x 5-foot rear diffuser test prototype, for which Stratasys printed a sandwich core from ULTEM 1010 plastic (shown in gold) that was then wrapped in carbon fiber prepreg. Photo courtesy of Stratasys.
I think it’s important that he does look at the exceptionalism here and would totally agree that, for some dental parts at least, 3D printing could be the only technology in use. By looking at one single use case and market, we sometimes get a very different view about market adoption than we would by missing this granularity. It’s also an interesting observation to note that healthcare is a different bird. A lot of people look at these markets more or less the same but, indeed, in the types of requirements and players in this market do suggest that market penetration is going to be radically different compared to other verticals.

Final, 3D printed ECS duct adapter designed to cool aircraft while on the ground. 3D printed in Stratasys Nylon 12 on the Fortus 450mc
“Additive manufacturing is everywhere – it is hard to name an industry where we won’t be used. For us, we believe that there are billion-dollar opportunities in applications such as fashion, dentistry, orthodontics, medical devices, aerospace, automotive, consumer goods, electronics – the list goes on. And in addition to the industries above, because of our mix of technologies and available materials, we also find ourselves with the ability to be used in applications like entertainment, sporting goods, and packaging – just to name a few. Because we have a variety of different AM technologies, we are able to support a wide variety of applications,” Pat said.
“AM will penetrate further into more and more industries as AM machines become faster, cheaper, more reliable, and work with more materials. I have yet to find an industry where AM does not have potential as a current or future manufacturing method.”
Subscribe to Our Email Newsletter
Stay up-to-date on all the latest news from the 3D printing industry and receive information and offers from third party vendors.
Print Services
Upload your 3D Models and get them printed quickly and efficiently.
You May Also Like
Johns Hopkins University Researchers Develop HyFAM Technology
Two scientists from Johns Hopkins University, Nathan C. Brown and Jochen Mueller, have developed a hybrid manufacturing technology they call HyFam, or Hybrid Formative Additive Manufacturing. Their work on this technology...
3D Printing G-Code Gets an Upgrade: T-Code
Good old G-Code still manages many 3D printers, great and small. Just like the STL, it’s a standard that enables collaboration while also holding the additive manufacturing (AM) industry back....
AM Rewind: The Biggest News and Trends of 2024
After a sluggish 2023, driven by persistent inflation and geopolitical tensions, 2024 has seen some recovery. Economic growth climbed from about 2.8 percent in 2023 to a modest 3.2 percent...
Metal Wire 3D Printer OEM ValCUN Announces Plans for 2025 Expansion
ValCUN, a Belgian original equipment manufacturer (OEM) of wire-based metal additive manufacturing (AM) hardware, has announced that the company has entered the next phase of its growth trajectory, making key...