Europe’s leading additive manufacturing trade show, Formenxt 2024, comes to a close today. There have been many product, material, software, and other business announcements during the event, and we’ll summarize some more for you here!
Malping Using AIM3D’s Pellet 3D Printer
Depending on your application, and batch size, pellet 3D printers have excellent price advantages in terms of material input, as well as improved process capability, making them very cost-cost effective. AIM3D, which was relaunched earlier this year, has focused on pellet 3D printers since 2017, and German 3D printing service provider Malping is now using the technology. Malping supports its customers all the way from initial product idea to design, simulation and validation, and manufacturing, and now uses AIM3D’s ExAM 510, which premiered at Formnext 2021, to help fill its customers’ orders. The system operates at a maximum build rate of 150 cm³/h, with a goal of eventually reaching build rates of 300 to 600 cm³/h; this could enable annual processing volumes of 1,000 to 4,000 kg. One application Malping used the ExAM 510 pellet 3D printer for recently was to manufacture a suction ring for the food industry. This technology was useful in this case due to rapid availability
“The advantages of an additive solution are obvious in this application: rapid availability of the component starting from component number 1, no tools, possible rapid modification of the component for specific applications on different filling systems. The system operator benefits from a high system availability,” said Dr.-Ing. Bastian Gaedike, the CEO of Malping.
You can learn more about this partnership at AIM3D’s Formnext Booth E81, Hall 12.1.
Ceramic 3D Printed Filter Membranes by Evove & Lithoz
At its Formnext booth, Lithoz will be showcasing ceramic 3D printed filter membranes, produced using its lithography-based ceramic manufacturing (LCM) technology by advanced filtration company Evove. The Separonics ceramic filter membranes were designed to reduce energy usage by 80%, recycle 80% more water, and increase output by five times. This is the largest application ever built by the company’s LCM technology—the complete filter module is a full meter long, made up of 20 stacked filter membrane segments, each of which are 5 cm high and have a 10 cm diameter. Using Lithoz’s new CeraFab S320 3D printer, which the company debuted at Formnex, Evove was able to achieve a high level of manufacturing control, with complex geometries and uniform pore size. Plus, because of how durable ceramics are, Evove’s filters are more resistant to aggressive chemicals, physical wear, and high temperatures, which means the alumina membranes require less maintenance and last longer.
“Water touches 60% of global GDP, and the ability to recycle even the most challenging of feeds is a lynchpin of the circular economy and decarbonization. Ceramic materials offer great advantages but, until now, have suffered from the high cost of manufacture and susceptibility to random filtration performances,” said Evove CCO Andrew Walker. “With Lithoz 3D printing technology, it’s proven that we can precision engineer and manufacture cost-effectively at scale.”
You can see Evove’s 3D printed filtration solution at the Lithoz Booth C49, Hall 11.1 at Formnext.
Incus Introduces Newly Redesigned LMM 3D Printer
Austrian 3D printer manufacturer Incus, which specializes in Lithography-based Metal Manufacturing (LMM), introduced its newly redesigned Evo35 printer at Formnext this week. This latest iteration of the printer, which was formerly known as the Hammer Lab35, has several major upgrades, including an improved climate control system for the build chamber, which ensures that it’s operational in any production environment. Other improvements include an industrial software interface for streamlined communication with ERP systems, and a full overhaul of the printer’s architecture, including the latest generation of projector units, a CNC-grade machine frame, and mechanics. These projector units improve the benefits of LMM, like excellent surface finish and fine resolution, and also help to enable larger building fields. Delivering higher production capabilities, precision, and efficiency for complex metal structures, the new Evo35 is well-suited for professional environments that require robust machinery, and its versatility also makes it ideal for research and development purposes as well.
“We are proud to introduce the Hammer Evo35, a reflection of our ongoing dedication to advancing metal additive manufacturing. This redesign combines all the benefits of our core LMM technology with new features that increase efficiency, reduce costs, and improve safety, while maintaining the superior quality our customers expect,” said Dr. Gerald Mitteramskogler, CEO of Incus.
Visit Incus at Formnext Booth E59, Hall 11.1.
Q.BIG 3D’s Variable Nozzle for Large-Volume VFGF Printing
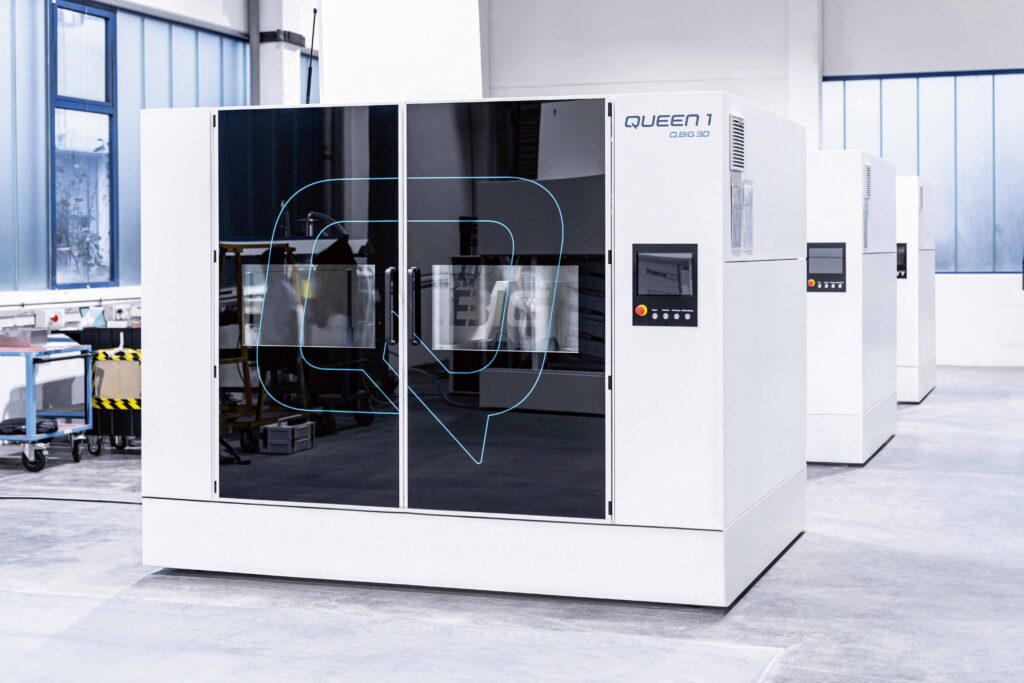
QUEEN1 system from Q.BIG 3D for XXL applications in 3D extrusion printing. Image: Q.BIG 3D GmbH, Backnang (Germany)
Q.BIG 3D and its Variable Fused Granulate Fabrication (VFGF) extrusion process can help make the process of printing large-volume components more economically viable. This is partially due to using less expensive, commercially available plastic granulate, and shorter amortization periods in comparison to tool-based processes, but the real kicker is the QUEEN1 3D printer’s variable nozzle, which significantly increases production because it can vary between two build modes during the process. Turbo mode is for fast printing and high material throughputs, perhaps for part of a design featuring infill areas inside the geometric form, while detail build mode is better for high precision and low material throughputs. By using these two modes during a build, the variable nozzle applies material layer by layer, just like your typical 3D printer, so economic fabrication of large-volume, high-resolution components without using molds is possible. Some example applications Q.BIG 3D has shared include a functional model for caravan construction, a helicopter simulation cockpit, and a pipe elbow for a hydroelectric power plant.
“We are producing the future. 3D material extrusion using the VFGF process is pushing the boundaries of what is possible and is making a whole new level of cost-effectiveness and amortization possible,” said Dennis Herrmann, Managing Director of Q.BIG 3D. “I see enormous potential for product development in large-format 3D printing. This also applies to lightweight construction, bionics and saving resources. Above all, however, the VFGF process is an accelerator for the Industry 4.0 approach.”
You can visit the Q.BIG 3D Booth E19, Hall 11.1, at Formnext to learn more.
Roboze Unveils Proprietary SlizeR Software
Finally, Roboze unveiled its proprietary SlizeR software at Formnext this week. This slicing software, an intrinsic part of the company’s strategy to optimize customer production, was designed to maximize its AM potential by optimizing performance, part quality, and efficiency. With the launch of SlizeR, Roboze is also introducing a new motto: Your Production Power. The company says that when SlizeR is adopted by businesses that also use its 3D printers, those businesses will simplify their project management, reduce setup time, and achieve more production flexibility, all of which leads to professional results and increased competitiveness. So companies looking to improve production processes and respond to customer needs more quickly and accurately should be excited for this software.
This slicing software has functionalities that can improve part quality, automate operations, and decrease conversion times. Some of SlizeR’s key features are:
- A faster transition from 3D design to R-code (G-code), as SlizeR reduces print job preparation times
- Increased system repeatability, because automatic settings and optimized print parameter management means more consistency
- Data-driven optimized print parameters, with automatic adjustment for more accessible 3D printing
- Improved part performance, as internal defects are reduced thanks to optimized print trajectories
- Advanced material control, with tools that enable more accurate material management and forecasts
- Intuitive, user-friendly graphical interface, which simplifies the print process for less experienced users
- Continuous evolution alongside Roboze printers, as it was designed to constantly adapt to new materials and machine functionalities
You can learn more about SlizeR by visiting Roboze’s Booth D12, Hall 11.1, at Formnext.
Subscribe to Our Email Newsletter
Stay up-to-date on all the latest news from the 3D printing industry and receive information and offers from third party vendors.
Print Services
Upload your 3D Models and get them printed quickly and efficiently.
You May Also Like
The Dental Additive Manufacturing Market Could Nearly Double by 2033, According to AM Research
According to an AM Research report from 2024, the medical device industry, specifically in dentistry, prosthetics, and audiology, is expected to see significant growth as these segments continue to benefit from...
Heating Up: 3D Systems’ Scott Green Discusses 3D Printing’s Potential in the Data Center Industry
The relentless rise of NVIDIA, the steadily increasing pledges of major private and public investments in national infrastructure projects around the world, and the general cultural obsession with AI have...
AM Research Webinar Explores Continuum’s Sustainable Metal Additive Manufacturing Powders
Metal additive manufacturing (AM) powder supplier Continuum Powders is working to develop solutions that empower industries to reduce waste and optimize their resources. An independent life cycle assessment (LCA) of...
3D Printed Footwear Startup Koobz Lands $7.2M in Seed Round
California-based Koobz is focused on reshoring the U.S. footwear supply chain with advanced manufacturing processes, including 3D printing. The startup just announced that it has added $6 million to its...