French firm Spare Parts 3D has announced the launch of Théia, a software that transforms 2D technical drawings into 3D models quickly and efficiently. Designed to streamline the process of digitizing spare parts, Théia will help companies create and manage their digital inventories. Stemming from a three-year R&D effort with The Laboratoire Universitaire de Recherche Automatisée (LURPA) and supported by the Defense Innovation Agency—part of the French Ministry of the Armed Forces—this new technology integrates with 3D printing technologies, facilitating on-demand, local production of spare parts and contributing to more sustainable manufacturing practices.
Spare Parts 3D is currently rolling out Théia in its beta phase, inviting companies to participate in a program that tests and enhances the software’s capabilities. The goal is to challenge Théia’s accuracy in transforming 2D technical drawings into 3D models across file formats, design standards, and industries. Théia breaks a 30-year-old industry barrier by automating this conversion process, reducing the time and cost involved, now taking just minutes. Participants in the beta program will contribute their technical drawings and, in return, receive 3D models of the drawings they provided. While the program primarily focuses on mechanical and spare parts drawings, it excludes electrical, architectural, and hydraulic drawings. Companies interested in exploring the capabilities of Théia and aiding in its development can register online to join this innovative beta testing initiative.
https://youtube.com/shorts/uWe3iyaT96c?si=l3AmyxnUv4__j1cX
CEO and Founder Paul Guillaumot said Théia is a disruptive innovation that represents a major technological leap forward. It makes it possible to digitalize supply chains on a massive scale for sectors such as energy, defense, petrochemicals, railways, shipping, and mining, where the need for spare parts is considerable.
“Theia will deliver considerable savings by reducing physical inventories of spare parts. According to a 2018 study by Theano Advisors, the global inventory value of printable parts was $174 billion (€160 billion). Considering an average inventory cost of 20%, Theia will save companies $34 billion (€31 billion) a year through digitalization,” explains the executive.
According to Guillaumot, the initial results of the beta testing will lead to the first publication in mid-2024. The next step is to generalize 3D reconstruction from drawings and parts of any complexity and obtain parametric files, allowing Spare Parts 3D to automatically modify them according to the chosen manufacturing processes.
Théia, integrated with Spare Parts 3D’s proprietary DigiPART software, makes it easy to determine which spare parts can be 3D printed in terms of technical feasibility and cost. This software creates digital twins and identifies the best local 3D printing services. This setup allows companies to produce parts exactly where needed, reducing wait times and shipping costs. More than a tool, Spare Parts 3D wants Théia to become a game-changer for maintaining and repairing equipment, ensuring that parts are readily available for sectors to keep their machinery in great shape.
“Théia addresses two major challenges: on the one hand, reading, understanding, and interpreting the information present in the drawing, and on the other, obtaining a 3D shape from its representation on 2D plans while respecting the geometric and dimensional specifications of the original object. The development of Théia is the result of a harmonious marriage between new developments in AI (deep learning, segmentation, automatic labeling, etc.), mastery of classic computer vision technologies (optical symbol recognition, feature matching), and semantic analysis of technical drawings. This combination makes it possible to identify the various semantic layers of the 2D drawing and thus to interpret the technical drawing in an optimal way for its 3D reconstruction,” highlights Professor Nabil Anwer, Deputy Director of LURPA and expert in shape engineering and 3D reconstruction.
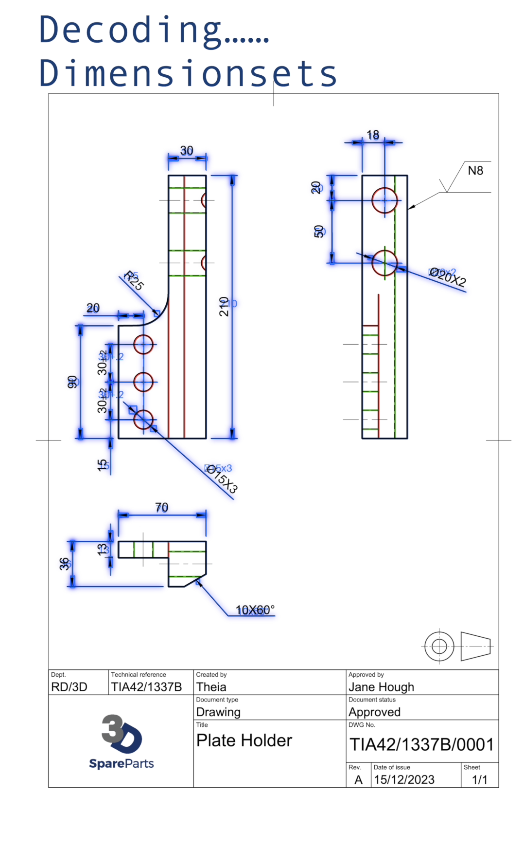
Spare Parts 3D Théia software transforms 2D technical drawings into 3D models. Image courtesy of Spare Parts 3D.
Theia was designed as “a competitive boost for manufacturers.” By enabling manufacturers to adopt additive manufacturing on a large scale, Theia makes it possible to produce on demand with a technology that consumes less material than subtractive or traditional manufacturing. By bringing production closer to the point of use, Spare Parts 3D hopes to help reduce transport-related carbon dioxide emissions, which aligns with the United Nations (UN) Sustainable Development Goals. In turn, this technology could help industries depend less on uncertain foreign suppliers and cut down on unforeseen expenses, benefiting both local economies and the environment.
While Théia is being heralded by Spare Parts 3D as a “world first,” it’s important to recognize that companies like Castor and 3YourMind have also made significant strides in developing technology for converting 2D drawings to 3D models. Castor not only allows the conversion from 2D to 3D but also, in 2023, introduced a feature that automatically visualizes 3D parts from 2D drawings, allowing for a one-click simulation that offers comprehensive printability analysis, cost estimations, sustainability benefits, lead time reductions, and supply chain enhancements.
Previous to Castor, in 2022, 3YourMind had already partnered with Werk24 to automate the processing of 2D technical drawings for additive manufacturing, allowing faster local production of legacy and obsolete spare parts. Other platforms like Onshape, PTC Creo, and Autodesk Fusion 360 also offer tools to convert 2D designs to 3D models, catering to various industry needs.
Théia is the latest tool to help companies turn their 2D drawings into 3D models, making it easier to get the parts they need quickly. It’s part of a trend where more businesses are using smart tech to make things more efficiently and with less waste, seeking a greener way to produce spare parts locally.
Subscribe to Our Email Newsletter
Stay up-to-date on all the latest news from the 3D printing industry and receive information and offers from third party vendors.
You May Also Like
Slice Engineering and Egyptian NGO Give Amputees Free 3D Printed Prosthetics
Florida-based Slice Engineering believes that additive manufacturing can reshape industries and make a lasting impact on humanity, and so works hard to empower innovators and professionals. The company does this...
3DPOD Episode 197: Ceramics 3D Printing with Johannes Homa, Lithoz CEO
Lithoz is a pioneer in the 3D printing of technical ceramics, initially using a ceramic-loaded stereolithography process and later adopting multiple technologies. Johannes Homa, a researcher turned entrepreneur, discusses his...
AddUp Announces Deputy CEO & Innovations in Medical & Injection Molding AM
Global metal 3D printer OEM AddUp, a joint venture between French tire giant Michelin and Paris-based industrial engineering corporation Fives, appointed Julien Marcilly as its new CEO at the end...
Lithoz Expands Ceramic 3D Printing to Japan via New Network
Lithoz is securing the future of its ceramic 3D printing technology in Japan with the formation of a new coalition with leaders from the country’s ceramics and manufacturing industries. Together...