Aerospace and defense company Leonardo was chosen to provide AgustaWestland AW101 helicopters to the Royal Navy, but a major improvement was needed to keep them airworthy. The company needed a fast solution, and requested help from SFM Technology and its AeroAdditive section, which decided that large-format 3D printing was the way to go.
Helicopters are used in many fields, such as transportation, tourism, law enforcement, and military, and 3D printing has been used to fabricate their parts and components. Often, these unique aircraft will have to land on ships at sea in all kinds of weather, either remaining on the flight deck, or being stowed away in the hanger. To fold in their blades, helicopters use automatic folding software; this folding helps to ensure maximum stabilization, which is vitally important when it comes to smooth embarkation. Necessary to the whole process is a main rotor blade restraint cradle.
“When a helicopter is on board a ship, it has the facility to fold its helicopter blades back. Once the helicopter blades are folded back at sea, it’s still windy, and the blades can flap,” explained Gary Wilson, Head of Sales at SFM Technology’s AeroAdditive. “So, these blades need to be restrained so this flapping doesn’t occur.”
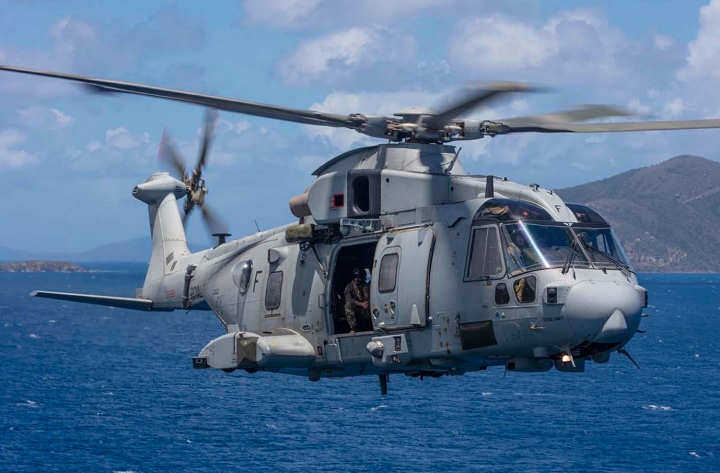
In fulfilling the request for the medium-lift AgustaWestland AW101 helicopters, Leonardo determined that the currently used main rotor blade restraint cradles weren’t working as well as they should be, and contacted SFM Technology for help finding a solution to the urgent problem. A privately owned British company, SFM Technology has plenty of expertise creating and providing engineering solutions for demanding environments, such as aviation, and called on BigRep to develop the first 3D printed main rotor blade restraint cradle, which measures 900 x 230 x 160 mm.
“This is quite a long process, so we had a look at many aspects of 3D printing. We must look at cost, efficiency, and of course, the size, which pushed us to BigRep,” Wilson said. “Eventually, we looked at the BigRep PRO as we had to look at a production 3D printer, which I believe the BigRep PRO can provide. The machine is used as a production machine, so every rotor blade restraint cradle will be going to the end customer.”
It was vitally important to find the right material, as lightweight but strong parts are necessary when it comes to aerospace applications. SFM selected the carbon fiber reinforced Hi-Temp CF material—with its high-strength properties, the material gives the blade restraint cradle powerful resistance to external pressure, in addition to the normal wear and tear.
“We carried out many tests to establish which was the most suitable material within the budget given. Having looked at the data sheets, we felt that Hi Temp had a slight advantage over the other BigRep materials,” Wilson said.
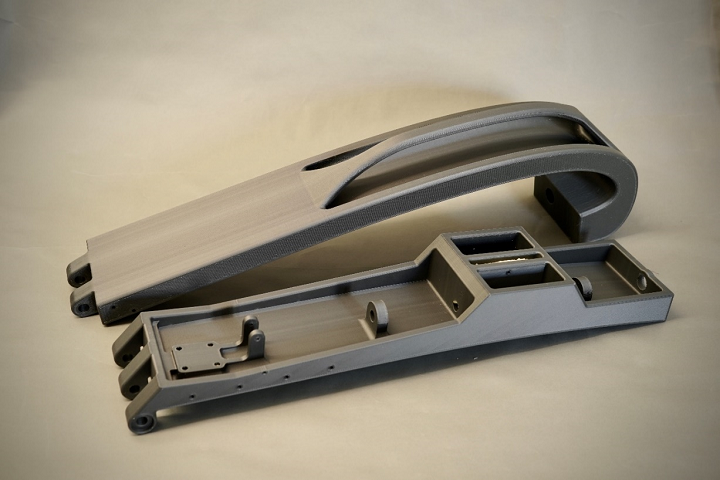
Once the support material is removed from the part, sandpaper is used to smooth the surface of the parts, and then bushes are inserted in the hinges, as well as helicoil inserts when needed. Metal parts and foam are added to the inside of the cradle once it’s painted, to offer protection to the main rotor blade when the restraint cradle is lifted. The benefits of 3D printing for this project have been numerous, especially in terms of saving time.
“To date, we have printed 30 cradles, consisting of 60 halves, since January. If we were to do that in a traditional way, we would have done about a quarter of that,” Wilson stated. “So, you can see that 3D printing is far quicker, as we don’t have any adjustments to make, or if we do, they’re very minor and can be quickly overcome. And the material is just as strong.”
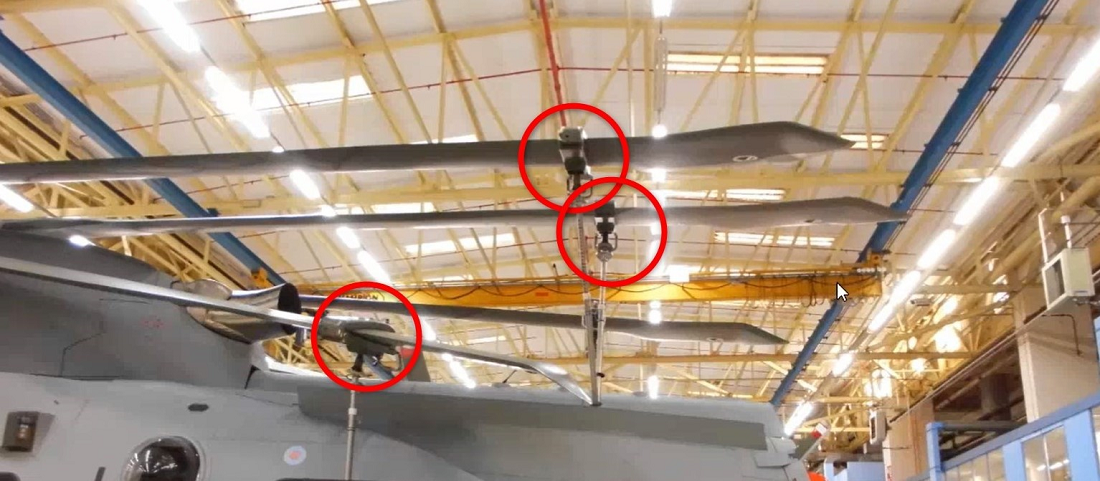
The 3D printed main rotor blade restraint cradles are already being used, and SFM Technology is now investigating the use of the BigRep PRO for batch production. Wilson says “it’s only a matter of time before additive manufacturing becomes the norm” in the aerospace industry, and from the looks of recent news, the same will likely go for military applications all across the board.
“In the aerospace industry, there are many designers still slightly nervous about 3D printing. By using these cradles, we can demonstrate that 3D printing can be used in the aerospace industry quite comfortably from a strength, repeatability, and quality side,” Wilson concluded. “I know for a fact, that as the industry gets more technically forward on 3D printing, certainly there will be more and more paths because of the accessibility to them.”
Source: BigRep
Subscribe to Our Email Newsletter
Stay up-to-date on all the latest news from the 3D printing industry and receive information and offers from third party vendors.
You May Also Like
3D Printing Unpeeled: Biofuel Waste to Filament & Sustainable Photopolymers
I can’t ever remember a day with so many potentially high impact news stories have come out. In one story, we all know that there are problems with the safety...
Finnair Hires AM Craft to 3D Print Plastic Parts for Aircraft Interiors
Riga-based AM Craft, a supplier specialized in 3D printing aviation components and certified under EASA Part 21G, announced a significant achievement today. The company will assist in upgrading Finnair’s A320...
3DPOD Episode 198: High Speed Sintering with Neil Hopkinson, VP of AM at Stratasys
Neil Hopkinson, a pioneering 3D printing researcher, played a pivotal role in developing a body of research that is widely utilized today. He also invented High Speed Sintering (HSS), also...
3D Printing Webinar and Event Roundup: May 12, 2024
Webinars and events are picking up in the AM industry this week! ASTM International continues its Professional Certificate Course and Stratasys continues its advanced in-person trainings, while 3D Systems is...