mimiX Biotherapeutics Unveils First Acoustic Bioprinter: Creating Life With Sound, the Next Generation of Biofabrication
During most of 2020, the entire world has been submerged in a health crisis due to the ongoing COVID-19 pandemic. This unprecedented situation could be a turning point in history, especially to ideally reimagine the future of hospital health. Patient needs are becoming more complex and, as the pressure on healthcare providers continues to escalate, it is clear that regenerative medicine and cell therapies promise to transform healthcare, pharma, and biotech industries by improving patient outcomes and enabling long-term economic savings. Nonetheless, how we plan to get there is still not entirely clear.
While conventional 3D printing technologies are actually applied for biological or biomedical applications, true 3D bioprinting involving direct printing of cells and other biological substances for tissue reconstruction is still in its infancy. Experts are divided as to how far we are from lab-grown organs, and moving the technology from bench to bedside could take years. To bridge this gap, the founders of Swiss biotech startup mimiX Biotherapeutics (mimiX) announced the launch of an entirely new technology that could produce multi-cellular functional tissue constructs, quickly and affordably, through sound waves.
mimiX’s first acoustic bioprinter, called cymatiX, stands to transform biofabrication, say the company co-founders. They believe it will enable the field of biofabrication to overcome some major limitations of conventional bioprinting methods and direct us toward the creation of physiologically relevant in vitro models and engineered tissue constructs. The gentle, fast, and user-friendly laboratory instrument relies on the company’s patented Sound Induced Morphogenesis (SIM) bioprocessing technology.

The mimiX team with the first prototype of the 3D SIM patterning instrument (From left to right: Roman Amrein, Nicola Di Marzio, Marc Thurner, and Tiziano Serra). Image courtesy of AO Foundation
The 3D-SIM technology behind mimiX biotherapeutics is nearly a decade old. It was developed by Dr. Tiziano Serra, a Research Scientist at the AO Research Institute in Davos, Switzerland, and co-founder of mimiX, with the objective of creating well-defined biological patterns that self-assemble into functional tissues using sound waves. In the past, Serra has poetically defined this process as “orchestrating biology,” and today SIM technology offers a unique and highly efficient strategy to fabricate dense and organized cell patterns and addresses necessities in the broad field of life sciences, finding applications in tissue engineering, regenerative medicine, and pharmaceutical research for drug discovery.
Earlier last fall, the startup published in vitro scientific results on the orchestration of vascular networks and entered an in vivo translation program driven by focused pre-clinical studies on soft tissue regeneration. Just one year after its foundation, mimiX is also disclosing a new corporate identity and its first bioprinter. mimiX CEO and Co-founder Marc Thurner revealed exclusively to 3DPrint.com that cymatiX will be available to the scientific community in 2021.
“It will change biofabrication technology forever,” Thurner explained. “At mimiX, we work for a world where regenerative medicine is accessible to everyone, and our new emerging technology will be a paradigm shift, a completely new approach to biofabrication, leveraging researchers’ creativity to pattern biologicals (cells, spheroids, organoids, micrografts). The bioprinting industry was the hype of the last decade, but now, it could switch towards a new tech curve: our sound-based next-generation biotech. The new instrument will be accessible to institutes, academia, and researchers everywhere that wish to enter a new era of biofabrication hype.”
As the device is still a prototype, mimiX is currently in the process of industrializing cymatiX, which will be commercialized next year. Anyone can pre-order the device and look forward to receiving it after May 2021. However, the company plans to offer cymatiX for purchase to 10 select partners in January 2021. This VIP group of researchers and scientists will be selected from a pool of interested candidates that can apply today through mimiX’s website here.

mimiX biotherapeutics’ novel biofabrication technology exploits SIM technology to create well-defined biological architectures. Image courtesy of mimiX Biotherapeutics
Built to create biological architectures, the proprietary technology behind cymatiX will allow for clinical translation and to push the frontiers of bioprinting both in fundamental and applied research. The new SIM process represents a versatile and time-efficient strategy to create organized cell assemblies at defined spatial resolution and physiologically relevant cell density.
So, how does it work? First, biological particles, like cells, spheroids, and organoids, are dispersed in a hydrogel precursor and loaded into the SIM carrier. Then, a sound-generated vertical vibration is applied, and a pattern is created within seconds. Crosslinking of the patterned particulates within the hydrogel is carried out by using different stimuli, such as light, enzymatic, or thermal crosslinking, depending on the material. More importantly, multiple, differently patterned layers can be built sequentially.
“cymatiX can create patterns, and condense matter to trigger its biological functionality,” described mimiX co-founder Tiziano Serra. “Instead of having dispersed cells with low density, researchers will be able to condense cells in a very fast and gentle process through the liquid movement of all the cells via a low-frequency vertical vibration applied at the bottom of the chamber. This dynamic cell condensation is one of the critical points for the regeneration of functional tissue. Moreover, we were able to predict through a simulation which kind of pattern we want to generate for a specific application, from an implantable tissue to drug screening or disease model testing.”
According to the founders, this fast technique produces multicellular architectures within seconds from a large bank of sound profiles. It is cell-friendly, contactless, and mild. Controlled remotely by acoustic waves, the SIM device allows patterning of biological material into 3D constructs that develop into in vitro engineered tissues, for example, microvascular networks.
To prove the technology, Serra worked with colleagues from the Swiss National Science Foundation (SNSF) and the AO Research Institute, to prove that SIM technology can generate multiscale organized vascular networks. In a paper published in the IOPscience journal Biofabrication, the researchers developed an in vitro experimental model as a proof-of-concept to assess the feasibility of SIM for creating vascular structures.
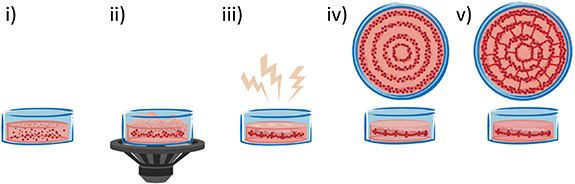
Schematic representation of vascular network formation with SIM process. Image courtesy of Tiziano Serra/IOP Science
In the study, the researchers prove that even with a low initial density of cells, they are able to self-assembly into functional multiscale vascular networks. Furthermore, the authors conclude that this is a highly versatile method with many degrees of freedom (material, cells, patterning parameters), that can be applied to several biomedical fields, such as the development of advanced spatially-orchestrated, patient-specific micro physiological 3D models for drug screening and its implementation in bioprinting to provide automated tissue fabrication towards clinical translation.
“It’s all about cell condensation and patterning, these are the two secrets of life, and that is what we offer with our process, the capacity to condense and pattern. We are certain that cymatiX will offer much better performance than any other bioassembly process in the market today,” suggested Thurner, who until recently was CEO of another startup that he founded, Swiss-based biotech firm regenHU. “This new device is part of our vision to completely redesign regenerative medicine by increasing the patient’s accessibility to the point of care approach.”
Subscribe to Our Email Newsletter
Stay up-to-date on all the latest news from the 3D printing industry and receive information and offers from third party vendors.
Print Services
Upload your 3D Models and get them printed quickly and efficiently.
You May Also Like
The Market and Industry Potential of Multi-Material 3D and 4D Printing in Additive Electronics
Additive manufacturing leverages computer-based software to create components for products by depositing either dielectric or conductive materials, layer by layer, into different geometric shapes. Since its birth in the 1980s,...
3DPOD 262: Bio-inspired Design for AM with Dhruv Bhate, Arizona State University
Dhruv Bhate is an associate professor at Arizona State University. There, he looks at structures, materials, and design. Previously, he worked at PADT as well as in the semiconductor and...
3DPOD 261: Tooling and Cooling for AM with Jason Murphy, NXC MFG
Jason Murphy´s NXC MFG (Next Chapter Manufacturing) is not a generalist service; instead, the company specializes in making tooling. Using LPBF and binder jet, the company produces some of the...
3DPOD 260: John Hart on VulcanForms, MIT, Desktop Metal and More
John Hart is a Professor at MIT; he´s also the director of the Laboratory for Manufacturing and Productivity as well as the director of the Center for Advanced Production Technologies....