This year’s digital edition of Formnext managed to gather the additive manufacturing (AM) community in an unprecedented event. Due to the ongoing coronavirus pandemic, the leading exhibition transformed into a virtual event for 2020. As usual, it was hard to keep up with the wide-ranging content program, multi-session digital platform, and hundreds of exhibitors. Over 45,000 spectators worldwide gathered from November 10 through 12, 2020, to follow current and future trends, developments, and applications. The three-day trade show quickly became a premier forum for AM in aerospace, with key industry stakeholders discussing technological innovations, cost-effective production strategies, and part scalability.
During the 2020 pandemic crisis, aerospace rapidly turned into one of the most impacted business sectors, with commercial airline fleets and air traffic down everywhere due to massive lockdown measures. Despite a challenging near-term aerospace market, the industry remains resilient about the future, relying on AM to accelerate aircraft design and manufacture.

2020 Formnext Connect event went virtual due to the coronavirus pandemic. Image courtesy of Formnext
Vice President of Formnext at Mesago Messe Frankfurt GmbH, Sascha Wenzler, said to 3DPrint.com: “AM holds huge potential for a number of industries. Often, production cost is the only factor taken into account when looking at AM applications. In the aerospace industry, however, other factors such as weight reduction and increasing fuel efficiency outweigh initial manufacturing costs. As the number of applications in this sector increase, the aerospace industry itself becomes a role model for other sectors and a trailblazer for the adoption of AM overall.”
Wenzler’s remarks about the industry coincide with many of the highlights from the event, which included a panel of experts discussing the current and future influence of AM in space and aircraft industries, real production processes of high-end parts, introduction to some of the latest machines available for aircraft part production, and industry insights from event exhibitors.
Aerospace manufacturers were among the first industries to embrace AM technology. However, strict safety regulations and long certification processes, coupled with a drop in aircraft demand seem to have slowed down the technology’s advantages. In order to fully incorporate digital manufacturing in aerospace, a panel of experts from the rocket and aircraft industry suggested ambitious objectives, including continued investment in R&D, more sustainable-driven productions, target spare part production for commercial aircraft, building up supply chains, and focusing on getting processes qualified.
AM Roadmap Leader at Airbus Hauke Schultz said during the “AM: A Boost for Aerospace” panel that the company expects AM to play a major role in the development of the recently revealed plans for zero-emission aircraft. The hydrogen-fueled planes could take to the skies by 2035 as part of Airbus’ move towards more sustainable goals.
For the ZEROe planes, Schultz suggested the company will think of AM “first time right,” focusing on increasing part performance and savings, but also really looking at functional parts where AM raises a unique solution. Parts like manifolds, heat exchangers, and complex system components, which cannot be manufactured with conventional subtractive technologies, and offer a huge potential for scaling. In the near term, however, the expert said Airbus has identified spares as a key sector for AM, with the company currently supplying four-digit numbers of additively manufactured spare components to its customers.
Talking about the current aerospace scene, Jens Telgkamp, Professor of AM at Hamburg University of Applied Sciences in Germany, said: “I see that most companies during the last five years took a decision while going in the same direction, focusing a lot on serial parts. They focused on parts with a high-value creation, parts in the safety-critical regime, with advantages and disadvantages (…) Safety is not for debate in aerospace. All of our companies need to comply with the regulations. To achieve this for a relatively young technology like additive manufacturing, you need to take many post-treatment steps to the internal quality of the part. You can do safety-critical parts with AM today, but you are paying for this with a long process chain that you need to undergo to qualify or certify parts. The way to get out of this, is to continue doing research.”
On the space side, Relativity Space Senior Engineer Eliana Fu said 3D printing is the enabling technology that will help humanity build an interplanetary future. The expert discussed the company’s fully 3D printed Terran-1 rocket, and how Relativity has been taking lessons from AM in commercial aviation but taking it to the next level for space flight. The key, she said, is “thinking outside the box,” without the constraints of just one 3D printing technique. Crucial to Relativity’s success is its proprietary AM technology called Stargate. It allows the business to produce large structures in-house, giving the engineers full control of part manufacturing, including size, structure, and overhang, without depending on supply chains, said Fu, ensuring faster access to space for its customers.
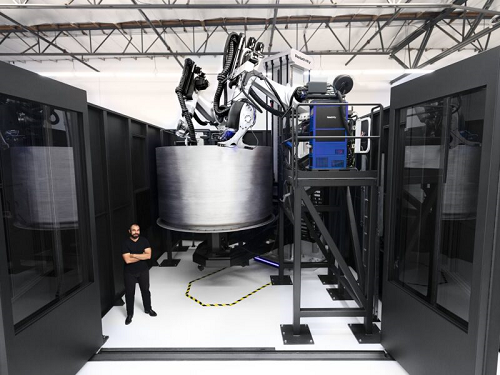
Relativity Space co-founder Jordan Noone next to the Stargate 3D printer. Image courtesy of Twitter/Jordan Noone
“Right now, we have signed a couple of customers, mostly commercial satellite customers like Telesat and new space, but we also signed Lockheed Martin. Those are completely unmanned flights. There is plenty of room in space exploration for crewed flights, space tourism, and there is also room in space for uncrewed flights. As we go into further space exploration in the near solar system, 3D printing is going to become a key enabling technology,” explained Fu.
During the event, attendees could watch lectures and presentations targeting aerospace manufacturing. For example, Taniobis, a developer and producer of high-quality metal powders, teamed up with Alloyed to discuss how they are jointly developing and optimizing alloy compositions through engine and architect software platforms, to provide customers the best material for their aerospace application area.
German industrial machine manufacturing company TRUMPF Lasers was one of the event exhibitors with 12 sessions overall, one of them focusing on 3D printing of high-quality parts for aerospace with its laser powder bed fusion technology. While Alexis Capoen, from Janus Engineering, and Thomas Heß, VP of AM at MT Aerospace, focused on rocket thrust nozzle part production and how Siemens’ software tools are enabling design optimization, manufacturing preparation, and the simulation of machine movements in the digital twin of manufacturing.
Additionally, a session by advanced manufacturing startup Volunteer Aerospace revealed the behind-the-scenes of working with GE Additive’s recently launched X Line 2000R. Co-founder and VP of Volunteer Aerospace Jonaaron Jones described how the new machine expands the company’s additive capabilities and enables them to drive “true customer outcomes” and reduce costs for single, large parts all the way to serial production.
“With these new advanced multi-laser, large volume machines, we can really compete, especially on lower rate productions—anywhere from 10 parts to 100 parts. It’s a very interesting time for additive, and these big machines really make that type of competition possible (…) Dual lasers enabled an increase in parts produced per build, with minimal increase in build time, increased reliability with automatic powder refill, minimal laser off-time between builds due to efficient powder handling,” said Jones. “We can take a part cost that originally was around $3,000 and drop it down to $1,000 per part, and are now onto serial production for two different customers.”
Apart from the sessions and panels of technology experts and exhibitors, there was product and material news, aerospace applications were discussed in post-session Q&As, and much more—proving that, even in challenging times, Formnext remains a digital hub for the AM world. Following the conclusion of this year’s live Formnext Connect program, the platform continues to be accessible until December 31, 2020 and will still offer opportunities to engage with exhibitors and other attendees via text-chat as well as a wealth of on-demand content.
Subscribe to Our Email Newsletter
Stay up-to-date on all the latest news from the 3D printing industry and receive information and offers from third party vendors.
Print Services
Upload your 3D Models and get them printed quickly and efficiently.
You May Also Like
The Market and Industry Potential of Multi-Material 3D and 4D Printing in Additive Electronics
Additive manufacturing leverages computer-based software to create components for products by depositing either dielectric or conductive materials, layer by layer, into different geometric shapes. Since its birth in the 1980s,...
3DPOD 262: Bio-inspired Design for AM with Dhruv Bhate, Arizona State University
Dhruv Bhate is an associate professor at Arizona State University. There, he looks at structures, materials, and design. Previously, he worked at PADT as well as in the semiconductor and...
3DPOD 261: Tooling and Cooling for AM with Jason Murphy, NXC MFG
Jason Murphy´s NXC MFG (Next Chapter Manufacturing) is not a generalist service; instead, the company specializes in making tooling. Using LPBF and binder jet, the company produces some of the...
3DPOD 260: John Hart on VulcanForms, MIT, Desktop Metal and More
John Hart is a Professor at MIT; he´s also the director of the Laboratory for Manufacturing and Productivity as well as the director of the Center for Advanced Production Technologies....