International researchers continue to explore patient-specific treatment, detailing the findings of their study in the recently published ‘Personalized 3D Printed Medicines: Optimizing Material Properties for Successful Passive Diffusion Loading of Filaments for Fused Deposition Modeling of Solid Dosage Forms.’
While FDM 3D printing is one of the most popular methods for digital fabrication around the world—mainly due to the continued growth in accessibility and affordability for users—in many cases it may still not be readily available to hospital personnel, despite the opportunity for offering patients extremely progressive, customized health care in the form of 3D printed models, devices, implants, surgical planning tools and a variety of different forms of medications and drug delivery systems.
In this study, the researchers chose FDM 3D printing for fabrication of personalized oral dosages, creating a ‘facile pre-screening tool’ for choosing suitable parameters. While such technology may offer great potential, the authors remind us that there is still much need for continued development in the often expounded upon areas of accessibility and affordability.
“Because of the limited loading that can be typically achieved (in most cases <1–2% drug), passive diffusion is currently applicable only to extremely potent drugs,” state the authors. “However, we believe the loading process can be significantly improved by optimally combining a biocompatible and extrudable polymeric material with a suitable non-toxic solvent, enabling the fabrication of a range of dosage forms and widening the range of applicable drugs.”
Nifedipine (NFD) was highlighted as an antihypertensive model drug often prescribed, and with a variety of release profiles. The research team explored how it can be loaded into 3DP filaments successfully, based on biocompatible polymers like polyvinyl alcohol PVA, PVA derivatives, and poly-lactic acid PLA. Optimum filaments, PVA and HS, were saturated in ethanol for eight hours, away from the light—and then oven dried at 40 °C for 12 hours.
For 3D printing, the authors relied on a Flashforge Creator Pro with dual extrusion heads; however, for tablets being created with only one filament, combined pills were fabricated using two heads.
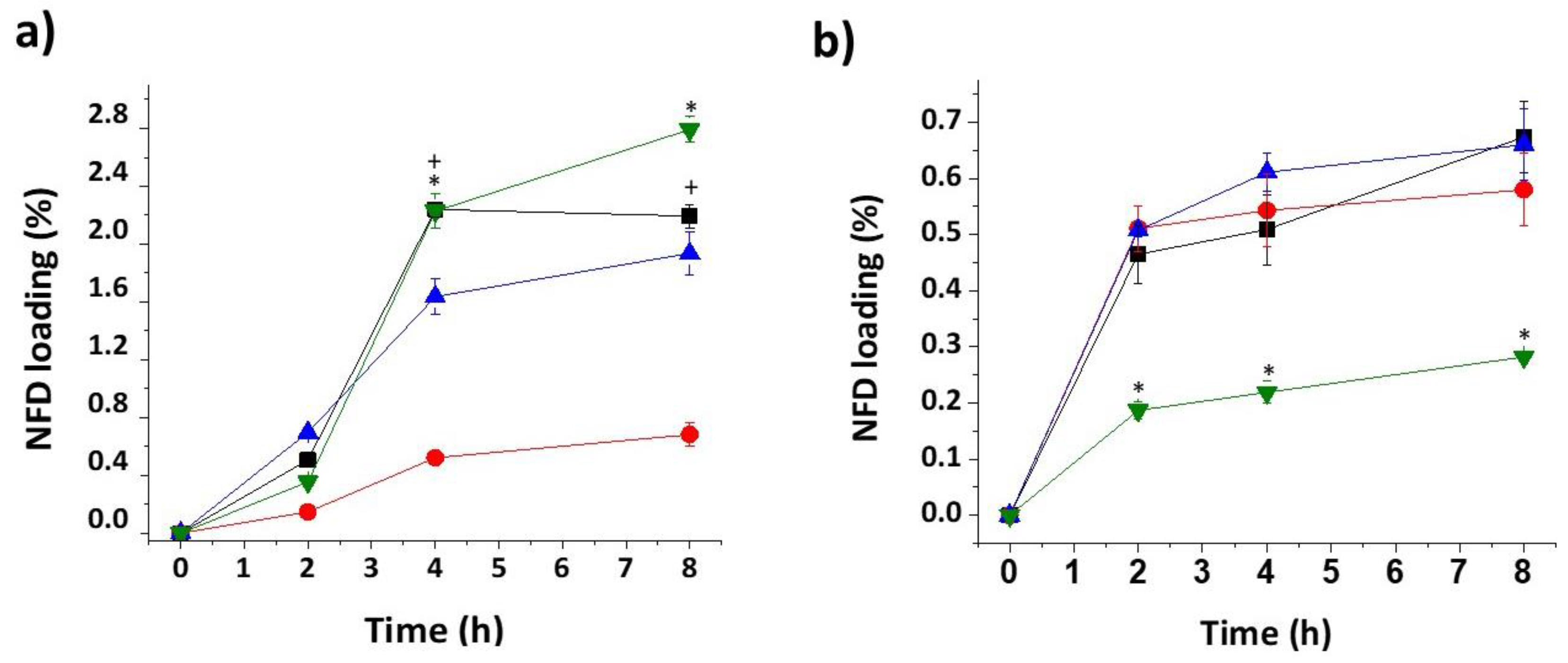
Nifedipine (NFD) loading diffusion kinetics. (a) Ethanol, (b) Ethyl acetate. Key: Hydrosupport (HS) (green), PVA (black), poly-lactic acid (PLA) (red), and thermoplastic polyurethane (TPU) (blue).
Filaments were not affected by eight hours of immersion in ethanol, and no serious cracks were found while NFD was present:
“However, the formation of micro and nanopores in the filaments over time, which would enhance the passive diffusion of the drug, cannot be excluded,” stated the researchers. “Deposits of small crystals were visible on the surface of the filaments, especially when ethyl acetate was used as solvent, which can be attributed to NFD that has not fully diffused into the filament and hence, upon drying, crystallizes on the surface.”

Diffusion kinetics of NDF from different solutions into different filaments. Key: Jss, steady state flux calculated from the slope of cumulative amount of drug diffused into the filament versus time (mg/cm2/h); ER, Enhancement ratio, calculated as the ratio of steady state flux in each filament in ethanol compared to ethyl acetate; P, permeability coefficient (cm/h); – Not applicable.* p < 0.05 ethanol versus ethyl acetate.
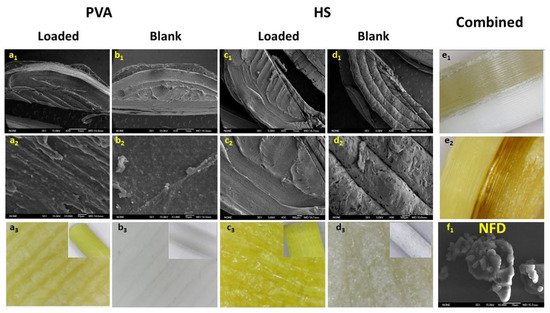
SEM micrographs and digital microscope images of a cut section of the 3DP tablets using PVA and HS NDF-loaded and blank filaments. Key: (a1–a3)- PVA NFD-loaded tablets; (b1–b3)- PVA Blank tablets; (c1–c3)- HS NFD-loaded tablets; (d1–d3)- HS Blank tablets; (e1–e2)- Combined 3DP tablets and f1-NFD raw material.
The researchers focused on understanding the main parameters necessary, along with an estimation of drug loading.
“Our PCA analysis (PC1-PC2 and PC1-PC3) showed a strong inverse correlation between the Jss, permeability, and diffusion with HSP distance (Ra) between solvent and filament and the toughness and bending modulus of the filament.
“Hence, the greater the Ra between the filament and the solvent, the lower the diffusivity of the solvent into the filament and hence, the lower the NFD permeability. Additionally, the lower the stiffness and the lower the energy to bend the filament (bending modulus), the greater the diffusion. No correlation was observed for the filament roughness.”
In establishing proof of concept, the authors compared stability of the drug to NFD raw material. They found that activation energy for NFD raw material was higher, meaning that high temperatures increased sensitivity. Moisture affected the 3DP NFD tablet too, adding to the amorphous state in comparison to the highly-crystalline NFD material.
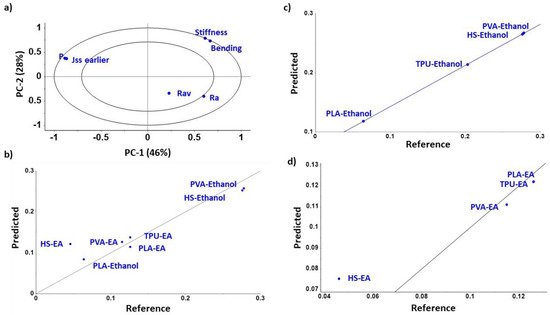
Multivariate statistical analysis. Principal component analysis PC1-PC2 (a) and support vector machine regression models of steady state flux into filaments (Jss), including both types of solvents (b), just ethanol (c), or ethyl acetate (d).
“The surface roughness and stiffness of filaments also appear to play key roles in enhancing the passive diffusion of drug into the polymer,” concluded the researchers. “HS NFD-loaded tablets have been shown to possess most promising characteristics, with a sustained release over 24 hours, long-term stability, and high chemical stability, similar to Adalat Oros tablets.
“Our study shows that passive diffusion coupled with FDM demonstrate good potential to be implemented in clinical settings to manufacture personalized medicines.”
What do you think of this news? Let us know your thoughts! Join the discussion of this and other 3D printing topics at 3DPrintBoard.com.
[Source / Images: ‘Personalized 3D Printed Medicines: Optimizing Material Properties for Successful Passive Diffusion Loading of Filaments for Fused Deposition Modeling of Solid Dosage Forms’]Subscribe to Our Email Newsletter
Stay up-to-date on all the latest news from the 3D printing industry and receive information and offers from third party vendors.
Print Services
Upload your 3D Models and get them printed quickly and efficiently.
You May Also Like
The Dental Additive Manufacturing Market Could Nearly Double by 2033, According to AM Research
According to an AM Research report from 2024, the medical device industry, specifically in dentistry, prosthetics, and audiology, is expected to see significant growth as these segments continue to benefit from...
Heating Up: 3D Systems’ Scott Green Discusses 3D Printing’s Potential in the Data Center Industry
The relentless rise of NVIDIA, the steadily increasing pledges of major private and public investments in national infrastructure projects around the world, and the general cultural obsession with AI have...
AM Research Webinar Explores Continuum’s Sustainable Metal Additive Manufacturing Powders
Metal additive manufacturing (AM) powder supplier Continuum Powders is working to develop solutions that empower industries to reduce waste and optimize their resources. An independent life cycle assessment (LCA) of...
3D Printed Footwear Startup Koobz Lands $7.2M in Seed Round
California-based Koobz is focused on reshoring the U.S. footwear supply chain with advanced manufacturing processes, including 3D printing. The startup just announced that it has added $6 million to its...