Researchers Create Microstereolithography for 4D Printing, Potential for Impacts in Medical, Solar & More
Technology can be confusing when it begins moving at such an accelerated rate, perfectly exemplified by the 3D industry, and encompassing all that goes with it, from 3D scanning to 3D printing and then peripheral industries that are often connected too such as augmented and virtual realities. We’ve barely digested all the stunning innovations making impacts in so many different sectors, from 3D printed medical models that allow for more complex surgeries, to 3D printed parts for a suspension system that make racing bikes go faster, all the way to incredible toys for your kids using augmented reality systems.
Yet, while work is definitely just beginning in the 3D realm, scientists have already begun exploring a range of uses for 4D technology that should prove offer impacts in just as many applications, from the medical field to electronics and far beyond. It might seem like a lot all at once, but the two technologies definitely work together, with the 4D emphasis adding a more intuitive, smart angle to fabrication.
As we’ve seen in other studies using the application of heat, it would appear that 3D printed objects can be treated or manipulated to cause shapes to morph according to their environment, as well as remembering their previous state and going back to it in the appropriate conditions. Now, teams from both MIT and the Singapore University of Technology and Design (SUTD) are employing light in their endeavors to create smart structures. They’ve had good success too, if the amount of torturing they’ve put these materials through is any indication. According to the engineers, they’ve twisted, bent, and stretched everything from small coils to flowers fabricated out of numerous materials, and even a replica they made of the Eiffel tower. As is the case with structures being pushed into the 4D realm, all of the above materials reverted.
The researchers say this is due to a ‘sweet spot’ that is reached in temperature, alerting the shape to go back to its previous structure. And as is usually the case in these other-worldly 3D and 4D technologies, this is really just a rudimentary beginning. While currently they can indeed 3D print items that are as minute as the width of one of the hairs on your head, numerous applications will most likely benefit from this technology soon.
Nicholas X. Fang, associate professor of Mechanical Engineering at MIT, sees incredible potential for these morphing shapes, and especially as they are activated by heat, with promise in areas such as the manipulation of of solar panels. Fang thinks they could perhaps create ‘soft, responsive hinges’ for turning panels toward the sun automatically.
“Very often, excessive heat will build up on the back side of the solar cell, so you could use [shape-memory materials] as an actuation mechanism to tune the inclination angle of the solar cell,” Fang says. “So we think there will probably be more applications that we can demonstrate.”
Fang also mentions that this could have a huge impact in the medical field and for fighting illness, allowing drugs already taken internally to open on their own and disperse medication when an infection begins.
“We ultimately want to use body temperature as a trigger,” Fang says. “If we can design these polymers properly, we may be able to form a drug delivery device that will only release medicine at the sign of a fever.”
Their research is outlined in ‘Multimaterial 4D Printing with Tailorable Shape Memory Polymers,’ recently published in Scientific Reports, and authored by Qi Ge, Amir Hosein Sakhaei, Howon Lee, Conner K. Dunn, Nicholas X. Fang, and Martin L. Dunn.
“Two key attributes of [shape memory polymers] SMPs are their ability to fix a temporary programmed shape (fixity) and to subsequently recover the original shape upon activation by a stimulus (recovery),” state the researchers in their paper.
While this is of course all centered around 3D printing and its corresponding hardware and software, 4D printing comes into play with those structures that are able to evolve with their environment.
“Our method not only enables 4-D printing at the micron-scale, but also suggests recipes to print shape-memory polymers that can be stretched 10 times larger than those printed by commercial 3-D printers,” says “Kevin” Ge, assistant professor at SUTD. “This will advance 4D printing into a wide variety of practical applications, including biomedical devices, deployable aerospace structures, and shape-changing photovoltaic solar cells.”
Their method in using light to print is called microstereolithography.
“Ultraviolet (UV) light produced from a light emitting diode (LED) array is spatially modulated with the patterns of the corresponding 2D images, and illuminated onto the surface of photo-curable polymer solution. Once the material in the exposed area is solidified to form a layer, the substrate on which the fabricated structure rests is lowered by a translational stage, followed by projection of the next image to polymerize a new layer on top of the preceding one. This process proceeds iteratively until the entire structure is fabricated,” state the researchers in their paper.
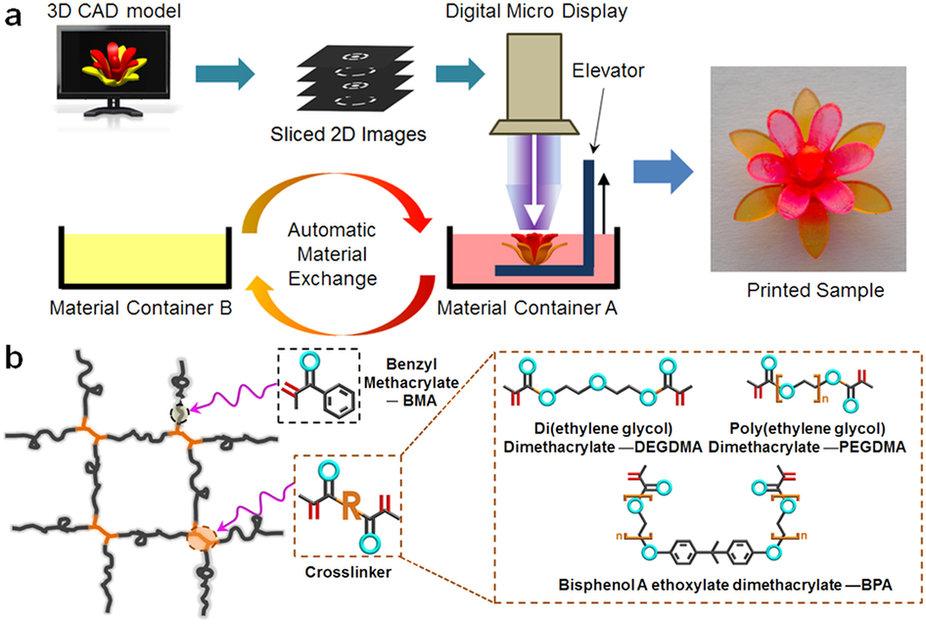
From the research paper: (a) A workflow illustrates the process of fabricating a multimaterial structure based on PμSL (b) Photo-curable shape memory polymer network is constructed by mono-functional monomer, Benzyl methacrylate (BMA) as linear chain builder (LCB), and multi-functional oligomers, Poly (ethylene glycol) dimethacrylate (PEGDMA), Bisphenol A ethoxylate dimethacrylate (BPA), and Di(ethylene glycol) dimethacrylate (DEGDMA) as crosslinkers.
Here, as Fang and the research team are using projected light tin layers, they liken it to the way dentists work.
“It’s almost like how dentists form replicas of teeth and fill cavities, except that we’re doing it with high-resolution lenses that come from the semiconductor industry, which give us intricate parts, with dimensions comparable to the diameter of a human hair,” said Fang.
The material that they are using, composed of a long-chain polymer and one that looks like a ‘stiff scaffold,’ can be stretched to as much as three times of its original length or shape, according to Fang. They are also seeing them revert back to shape in just a matter of seconds.
Their own printers operate with a much smaller pixel, allowing for a super fast response, which Fang thinks may eventually be refined to milliseconds.
In what is really a perfect example for showing how this applications works, the researchers fabricated a gripper with a handle for opening and losing it. They discovered that when they increased the temperature, the gripper began to close.“This is a very advanced 3D printing method compared to traditional nozzle or ink-jet based printers,” says Shaochen Chen, professor of nano-engineering at the University of California at San Diego, who was not involved in the research. “The method’s main advantages are faster printing and better structural integrity.”
“The grippers are a nice example of how manipulation can be done with soft materials,” Fang says. “We showed that it is possible to pick up a small bolt, and also even fish eggs and soft tofu. That type of soft grip is probably very unique and beneficial.”
The hope as this research progresses is that they will have success with even lower temperatures as they hope to translate their work to that of applications for health, with a need to be able to get closer to the regular human body temperature—especially with the idea of drug delivery upon signs of infection.
This research was supported in part by the SUTD Digital Manufacturing and Design Center (DManD) and the SUTD-MIT joint postdoctoral program. Discuss further in the Microstereolithography & 4D Printing forum over at 3DPB.com.
[Source: MIT News]Subscribe to Our Email Newsletter
Stay up-to-date on all the latest news from the 3D printing industry and receive information and offers from third party vendors.
Print Services
Upload your 3D Models and get them printed quickly and efficiently.
You May Also Like
The Dental Additive Manufacturing Market Could Nearly Double by 2033, According to AM Research
According to an AM Research report from 2024, the medical device industry, specifically in dentistry, prosthetics, and audiology, is expected to see significant growth as these segments continue to benefit from...
Heating Up: 3D Systems’ Scott Green Discusses 3D Printing’s Potential in the Data Center Industry
The relentless rise of NVIDIA, the steadily increasing pledges of major private and public investments in national infrastructure projects around the world, and the general cultural obsession with AI have...
AM Research Webinar Explores Continuum’s Sustainable Metal Additive Manufacturing Powders
Metal additive manufacturing (AM) powder supplier Continuum Powders is working to develop solutions that empower industries to reduce waste and optimize their resources. An independent life cycle assessment (LCA) of...
3D Printed Footwear Startup Koobz Lands $7.2M in Seed Round
California-based Koobz is focused on reshoring the U.S. footwear supply chain with advanced manufacturing processes, including 3D printing. The startup just announced that it has added $6 million to its...