4D Printing & Origami Allow LLNL Researchers to Explore Complex Structures for Important Future Applications
Most of us find 3D printing to be incredibly fascinating. From the hardware, software, and materials that allow us to create objects at the desktop to more complex operations in larger industrial settings, this is a technology that few of us have gotten used to yet or even had time to start taking for granted. That’s largely because as soon as we think we have seen it all, a new innovation comes along to blow our minds—as well as open them further. Some of the brightest researchers and engineers in the world have taken to using 3D printing, setting the wheels in motion to change how many processes will work in the future, along with the creation and manufacturing of numerous products that may not have been possible previously.
Scientists at the Lawrence Livermore National Laboratory (LLNL) in California have been behind many projects lately in the field of 3D printing, and they have allowed the world a glimpse into some of what they are researching, from the actual examination of 3D printing itself regarding subjects like porosity and metal 3D printing to creating new supercharging electronics, converting methane to methanol, or exploring the world of nanotechnology. And just when you think you are beginning to grasp how some of this works, LLNL gears up and accelerates straight into the next dimension with 4D printing.
This progression into 4D represents an evolution that most likely is just beginning. The best way to describe it is 3D printing that has come to life. Representing innovation that allows for products to be intuitive and morph with their changing environments, 4D printing is an expanding realm already, with engineers and designers around the world introducing us to innovation in the medical and automotive industries, clothing and consumer products, and much in the way of materials, even programming carbon fibers and wood.
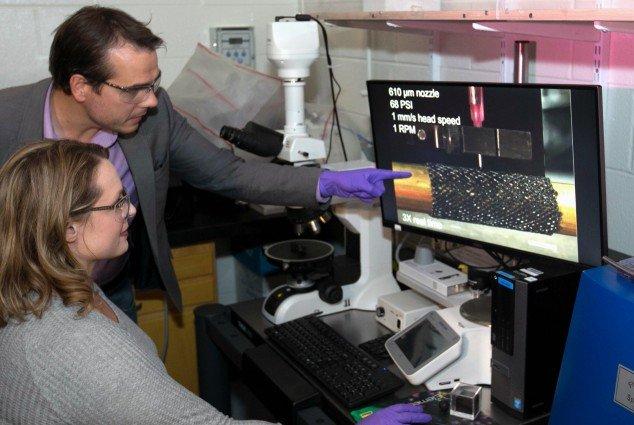
Researchers Jennifer Rodriguez and Jim Lewicki examine a stent that can expand when exposed to heat. [Photo: Julie Russell/LLNL]
The main focus is on SMPs and how they are able to revert to their former shape.
“Shape memory polymers (SMPs) are a category of smart materials that have the capability to recover their permanent shapes from one or multiple temporarily deformed states when exposed to an external stimulus, such as temperature, moisture, light, electromagnetic field, or ∆pH,” state the researchers in their paper. “Specifically, thermally actuated SMPs have found wide applications in biomedical devices, microelectromechanical systems (MEMS), textiles, and self-deployable aerospace structures.”
Their experimentation with temperature has been central as they discovered with constant stress but decreased temperature shapes remained in their current state, but as the temperature was increased they were able to transition. While working to exploit the benefits of SMPs the researchers also wanted to find a way to overcome their limits in terms of component size, in comparison to other ‘smart’ materials.
Their overall goal was to create complex shape memory structures in 3D printing with the use of varied temperatures and ‘bio-originated composites based on novel cure chemistry.’ Having looked back at other methods used to work with SMPs, such as the use of inkjet-based 3D printers, SLS 3D printers, and even the process of direct ink writing, the researchers were inspired in their work.
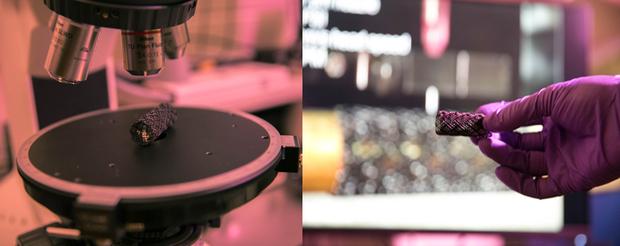
The LLNL researchers were able to create 3D and 4D complex structures with direct ink writing, including a stent which was able to expand due to increased temperature. [Photo: Julie Russell/LLNL]
“Our approach employs the precise deposition of composite filaments utilizing a pre-defined tool path to create complex structures,” stated the scientists in their paper.
Challenges they knew they would have to deal with were in the development of the proper printing inks for their requirements in this particular project, as well as finding a way to meet the appropriate ‘mechanical, electrical and shape-memory properties.’
As research progressed they were able to make both the desired ink (in a combination of soybean oil, carbon fibers, and other co-polymers) and the desired structures, manipulated and directed by temperature either in the form of ambient heat or electricity. And here lies the potential for a future in making very complex parts for numerous applications.
“It’s like baking a cake,” said lead author Jennifer Rodriguez, a postdoc in LLNL’s Materials Engineering Division. “You take the part out of the oven before it’s done and set the permanent structure of the part by folding or twisting after an initial gelling of the polymer.”
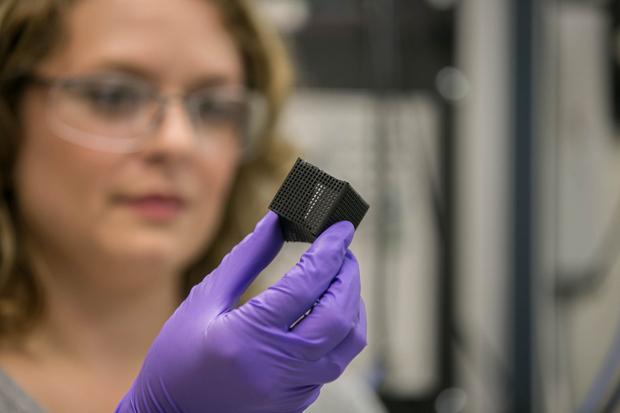
Jennifer Rodriguez examines a 4D printed box from their research project. [Photo: Julie Russell/LLNL]
“We have these materials with 3D structures but they have extra smart properties; they can retain a memory of the previous structure,” said Lab staff scientist James Lewicki. “It opens up a whole new property set. If you can print with these polymer composites you can build things and electrically activate them to unfold. Instead of a dumb lump, you are left with this sentient, responsive material.”
This research was part of a Laboratory Directed Research & Development involving the development of carbon fiber composites with 3D printing. Discuss further in the LLNL 4D Printing forum at 3DPB.com.
[Sources: Scientific Reports; ScienceDaily; LLNL; Computer World]Subscribe to Our Email Newsletter
Stay up-to-date on all the latest news from the 3D printing industry and receive information and offers from third party vendors.
Print Services
Upload your 3D Models and get them printed quickly and efficiently.
You May Also Like
Heating Up: 3D Systems’ Scott Green Discusses 3D Printing’s Potential in the Data Center Industry
The relentless rise of NVIDIA, the steadily increasing pledges of major private and public investments in national infrastructure projects around the world, and the general cultural obsession with AI have...
3DPOD 260: John Hart on VulcanForms, MIT, Desktop Metal and More
John Hart is a Professor at MIT; he´s also the director of the Laboratory for Manufacturing and Productivity as well as the director of the Center for Advanced Production Technologies....
Etsy Design Rule Change Reduces Selection of 3D Printed Goods
Online marketplace Etsy has implemented a rule change requiring all 3D printed goods on the site to be original designs. The update to the site’s Creativity Standards states, ¨Items produced using...
E-Beam OEM Wayland Additive Partners with USC Racing to 3D Print Titanium Exhaust Collector
Every year, standards organization SAE International holds a competition called Formula SAE, in which students from both undergraduate and graduate programs design, build, and race small formula-style race cars. For...