We’re starting off today’s 3D Printing News Briefs with a little business, including a new 3D printer launch, a feasibility study, an automotive partnership, and more. Then we move on to medical news with a hospital 3D printing lab in India. A mobile workshop in Hamburg offers advanced digital manufacturing technologies, and a mobile 3D printer can autonomously add features to a room. We finish up with a biosolution by UMAMI BIOWORKS that can detect pathogens in seafood.
Lynxter Launches S300 X – FIL11 | FIL11 IDEX 3D Printer
Lynxter recently launched the S300X – FIL11 | FIL11 3D printer for elastomer materials, which builds on the commercial success of its silicone S300X – LIQ21 | LIQ11. In line with the company’s philosophy, the IDEX printer is open for both software and materials, and it can process PP, PEKK, PA-CF, and several others, which makes it a great system for industries that require robust, high-quality components. The new S300X – FIL11 | FIL11 offers a 300 x 250 x 280mm build volume; maximum print speed of X-Y = 1000 mm/s, and Z = 50 mm/s; independent single and dual extrusion; a heated chamber of up to 80°C; closed and filtered environment (HEPA14 and activated carbon); and independent single and dual extrusion. With features like mirror mode, dual-material 3D printing, duplication, support options, step-by-step guided interface, and and an automatic calibration system, users should find it easy to improve their design and production capabilities.
“We have received numerous requests to extend the value proposition of the S300X – LIQ21 | LIQ11 to other materials. Recent developments in consumer machines have set new expectations in terms of productivity. It was therefore essential for us to offer an industrial solution for high-performance materials that meet these expectations,” said Thomas Batigne, the CEO of Lynxter. “The proven robustness and performance of the S300X platform coupled with its service and software ecosystem have allowed us to create a common platform. The S300X – FIL11 | FIL11 is a machine in tune with the times, enriched by the experience of its companion machine, highly responsive, and soon to be seen in all production workshops.”
Customer Orders Feasibility Study to Validate Freemelt’s E-PBF Technology
Deep-tech, green-tech company Freemelt, headquartered in Mölndal, Sweden with sales offices in the Netherlands and the U.S., has received an order from an industrial customer in North America. The customer, which specializes in advanced additive manufacturing (AM) technologies, uses its expertise in AM and metallurgy to deliver solutions to industries like energy, aerospace, and automotive. The unnamed company is at the top of the field in transforming AM into an efficient manufacturing method for high-temperature metals through continuing R&D efforts. As such, it has ordered a feasibility study in order to validate Freemelt’s E-PBF (Electron Beam Powder Bed Fusion) technology for creating novel alloys that target high-temperature applications.
“Thanks to our intensified commercialization efforts in North America we are experiencing an increased interest in our technology from industrial companies transitioning to additive manufacturing. I am thankful that another industrial company has chosen to validate Freemelt’s E-PBF (Electron Beam Powder Bed Fusion) technology for the manufacturing of high-temperature metals, further expanding our footprint across North America,” said Freemelt CEO Daniel Gidlund.
“Feasibility studies are the first critical step in realizing serial production through AM. Feasibility studies bridge the gap between concept and production, proving that additive manufacturing is a viable, cost-effective, and scalable solution for serial production. It provides the data-driven foundation needed to move forward, minimizing risks and ensuring readiness for industrial serial production. Feasibility studies are crucial for Freemelt’s commercialization, as they are related to industrial applications that are well-suited for the E-PBF technology and will over time result in new orders for the industrial machine, eMELT.”
LEGACY MOTOR CLUB Names BigRep America Official 3D Printing Partner
LEGACY MOTOR CLUB, a professional auto racing club that competes full-time in the NASCAR Cup Series, has taken a major step in transforming its production capabilities by announcing that large-format 3D printing leader BigRep America, Inc. has become its official 3D printing partner. During this multi-year strategic partnership, the two will work to expand the CLUB’s use of large-scale AM, starting with deploying two BigRep STUDIO G2 3D printers. These massive systems, with their 1000 x 500 x 500 mm build area, will allow the CLUB to create precise quality control templates for car builds, drive high-volume production of smaller automotive parts, support wind tunnel testing components, and facilitate mold-making for composite parts. By using BigRep’s large-format 3D printing, LEGACY MOTOR CLUB will be able to streamline its operational workflows, innovate faster, and gain a competitive advantage.
“In an ever-evolving performance-driven industry, our ability to effectively go from concept to reality as quickly as possible is what will set us apart from our competition. We are excited to partner with BigRep and leverage their technology to take our operations to the next level. Their 3D printers and wide array of material capabilities will help us meet the highest standards of part size, reliability, and performance,” said Steven Sander, Director, Aerodynamics Engineering for LEGACY MOTOR CLUB.
Kiben3D Uses Farsoon Printers with Automatic Grafting for Mold-Making
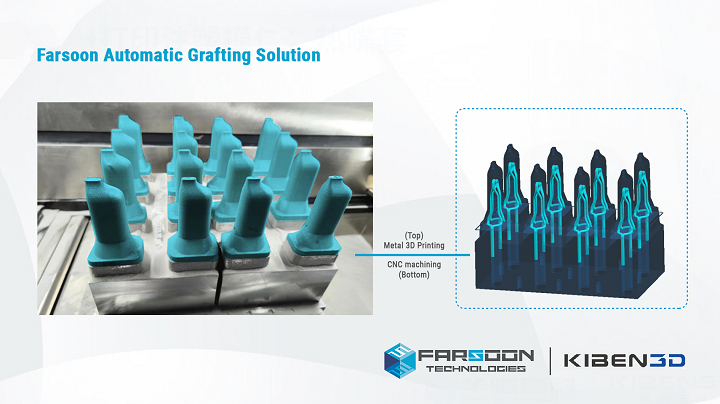
Figure 5: Automatic grafting solutions integrating CNC and metal 3D printing. Image courtesy: Kiben3D
Chinese company Kiben3D Technology, a leader in advanced mold manufacturing, operates a fleet of Farsoon FS200M metal 3D printers for this purpose. Kiben3D has helped over 600 leading manufacturers around the world reduce costs and improve efficiency with 3D printing, and led the drafting of important industry standards in its home country, including Conformal Cooling Water Channel Design and Maraging Steel Process Specifications for AM. Zhang Lei, General Manager of Kiben3D, says that metal AM can improve the cooling efficiency of most injection and die-casting molds, offers superior dimensional accuracy, and can address common quality issues like flow lines, weld marks, gate burns, and trapped air. Metal 3D printed molds are rough and require extra finishing work, so Kiben3D includes a 0.8mm allowance during printing to prepare for post-processing. After post-processing, Farsoon’s as-printed metal 3D molds can achieve nearly 100% part density, and a polishing grade of A2 or higher, meeting the needs of most molds.
Farsoon began working with industry partners in 2019 to explore the integration of CNC machining and metal 3D printing, and to improve the precision and speed of transitioning between the two, it introduced an advanced automatic grafting solution. First, the 3D printing laser coordinate system is set up for grafting, and the CNC base outlines for metal 3D printing are defined. Then, the build package is imported, and the grafting parts have to be aligned with the previously marked baselines. Finally, a laser scan of the baselines is performed to make sure the grafting surface and the sintering level are aligned. Farsoon says its automatic grafting enables positioning accuracy up to 0.05 mm, which allows for seamless structural integration without leaks or cracks. Currently, over 70% of Kiben3D’s tooling products use this automatic grafting, ensuring high-quality mold production with faster lead times and lower costs.
Sparsh Hospitals Launches India’s First Onsite 3D Printing Lab
Moving on, Sparsh Hospitals has adopted many advanced robotics systems, and is now taking the next step by launching the first advanced onsite 3D Printing Lab in India at its Infantry Road facility. Featuring cutting-edge 3D technology, the lab will offer comprehensive solutions in orthopedic and personalized medical care, from scanning and printing patient-specific medical models for surgical planning all the way to post-processing. This will help improve surgical precision, reduce patient recovery times, and decrease long-term healthcare costs. At a press conference for the 3D printing lab, Sparsh Hospitals showcased several advanced technologies, including custom prosthetics designing, its existing robotics systems, and a Virtual Reality (VR) system. The lab is also actively exploring future innovations, including creating artificial organs. All of this shows the organization’s dedication to making healthcare more efficient.
“After the adoption of robotic systems, today we are taking a big leap forward with our advanced 3D printing lab and this move underpins our focus on technology, expertise, and experience. Tech-enabled 3D printing lab will be a game-changer for personalized patient care in India. It will allow us to design custom-made prosthetics, implants, and deliver surgical models that precisely match each patient’s unique anatomy. With the adoption of both 3D printing and robotic technologies, we will be setting new standards for surgical precision and patient outcomes,” said Dr. Sharan Shivaraj Patil, Chairman and Chief Orthopedic Surgeon, Sparsh Hospitals.
Süderelbe’s Open Lab Mobile Offers Hamburg Access to Digital Technology
Süderelbe AG recently opened the Open Lab Mobile truck, a mobile workshop in Hamburg that gives companies in the city and region access to digital production technologies, including a laser cutter, CNC milling machine, and a 3D printer. The truck is part of the worldwide Fab City initiative, which is working to build a global network of cities focused on sustainable living practices. Fab City Hamburg specifically targets companies, startups, SMEs, and educational institutions in the Hamburg Metropolitan Region, and Open Lab Mobile, funded by Next Generation EU, is a part of it, as well as the Bundeswehr Centre for Digitalisation and Technology Research. The truck, 13 meters in length, is currently in use at Scholz Mechanik, where gripper components for robots are manufactured. Open Lab Mobile offers hands-on workshops, and Melanie Leonhard, the Senator for Economics, said during her visit last month that it “has tangible benefits for companies.”
Jürgen Glaser, project manager, said, “We want to teach skills in the mobile production workshop, so that SMEs can identify potential for innovation and realise it themselves with new, digital production technologies.”
Mobile 3D Printer Autonomously Adds Features to Room
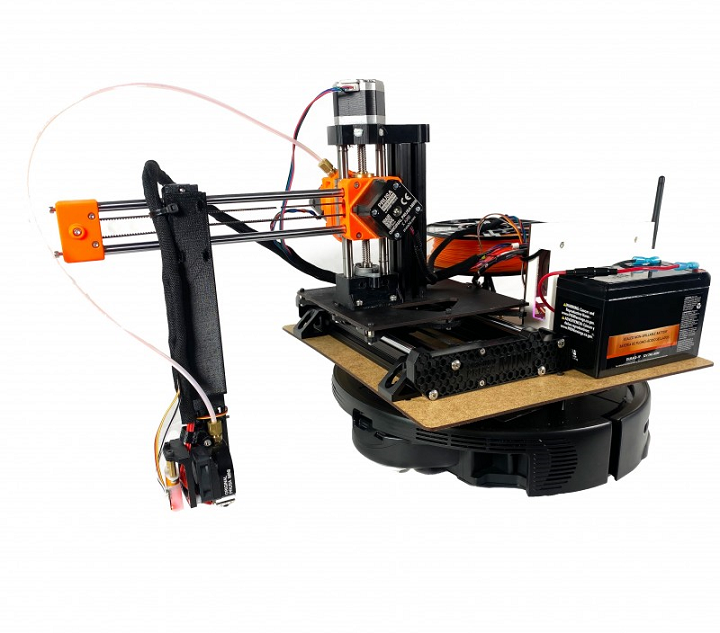
MobiPrint is a mobile 3D printer that can automatically measure a room and print objects onto the floor. Image credit: Zamora et al. / UIST ’24
A trio of researchers from the University of Washington and Purdue University have developed MobiPrint, a robotic, mobile 3D printing system that can automatically measure a room and then print objects onto its floor. As they explain in their paper, the prototype system autonomously roams an indoor space and maps it using LiDAR, and a design tool converts the map into an interactive canvas. Then, the user chooses a model, like a cat food bowl or even a ramp to cover uneven flooring, and works to scale and position the object within the design interface. Then MobiPrint, which was built on a modified consumer vacuum robot, rolls over to the correct location and prints the object right on the floor out of PLA. The system can add artistic design details to a room, or even accessibility features, like tactile markers for low-vision people. The team is now working to have MobiPrint remove objects that it has 3D printed, and maybe even recycle the plastic. They also want to explore robots that can print on other surfaces, in other environments, with more materials.
“Digital fabrication, like 3D printing, is pretty mature at this point. Now we’re asking: How can we push it further and further into the world, and lower the barriers for people to use it? How can we change the built environment and tailor spaces for peoples’ specific needs — for accessibility, for taste?” explained Daniel Campos Zamora, a doctoral student in UW’s Paul G. Allen School of Computer Science & Engineering.
The team presented their research, which was funded by the National Science Foundation (NSF), at the recent ACM Symposium on User Interface Software and Technology in Pittsburgh.
UMAMI Bioworks Biosolution Detects Pathogens in Seafood
Finally, Singapore-based UMAMI Bioworks announced an important development in the alternative seafood industry with the launch of Arbiter, a powerful seafood safety and quality assurance biosolution that can supposedly detect up to 800 unique pathogens in seafood. This milestone builds upon the company’s recent move into the UK market and partnerships in Korea, marking an expansion of its biotech offerings beyond cultivated seafood and pet food to help solve critical challenges across broader markets. Arbiter, a nucleic acid-based testing platform, offers high speed, sensitivity, and quantification, able to deliver actionable pathogen detection results in less than six hours. This innovation also majorly reduces labor intensity and cost, as it takes less than 15 minutes of preparation time for up to 50 test samples at less than $1 per target. UMAMI’s new biosolution is well-suited for applications in aquaculture, food safety and assurance, and environmental monitoring.
“The introduction of Arbiter not only embodies our commitment to pushing scientific boundaries but also to creating real-world impact by tackling significant challenges across multiple industries. It exemplifies our core mission—to harness the power of cellular biology and our ocean heritage to solve some of the world’s most pressing challenges and create a healthier future for humanity,” said UMAMI Bioworks CEO Mihir Pershad.
Subscribe to Our Email Newsletter
Stay up-to-date on all the latest news from the 3D printing industry and receive information and offers from third party vendors.
Print Services
Upload your 3D Models and get them printed quickly and efficiently.
You May Also Like
The Market and Industry Potential of Multi-Material 3D and 4D Printing in Additive Electronics
Additive manufacturing leverages computer-based software to create components for products by depositing either dielectric or conductive materials, layer by layer, into different geometric shapes. Since its birth in the 1980s,...
3DPOD 262: Bio-inspired Design for AM with Dhruv Bhate, Arizona State University
Dhruv Bhate is an associate professor at Arizona State University. There, he looks at structures, materials, and design. Previously, he worked at PADT as well as in the semiconductor and...
3DPOD 261: Tooling and Cooling for AM with Jason Murphy, NXC MFG
Jason Murphy´s NXC MFG (Next Chapter Manufacturing) is not a generalist service; instead, the company specializes in making tooling. Using LPBF and binder jet, the company produces some of the...
3DPOD 260: John Hart on VulcanForms, MIT, Desktop Metal and More
John Hart is a Professor at MIT; he´s also the director of the Laboratory for Manufacturing and Productivity as well as the director of the Center for Advanced Production Technologies....