In 2015, Daimler Buses initiated a critical transition from using additive manufacturing (AM) primarily for prototyping to full-scale series production. This shift has not only transformed how parts are manufactured but resulted in a new digital business model for the auto giant. To learn more, we spoke to Ralf Anderhofstadt, Head of the Center of Competence Additive Manufacturing at Daimler Truck | Daimler Buses, who detailed the company’s journey in adopting AM, the factors driving the creation of the consulting division AMS – Additive Manufacturing Solutions, and its future plans for 3D printing within the automotive industry.
Transitioning from Prototyping to Series Production
Daimler Truck & Buses foray into AM began with testing and validating the potential of 3D printing for producing series parts. The transition from prototyping to series production required rigorous technical and qualitative approval processes, special material developments, and numerous certifications.
“We started in 2015 within Daimler Buses to test and validate the leap from AM for prototype production to series production. In addition to technical and qualitative approval processes, special material developments, and numerous certifications, we qualified and implemented a large number of spare parts and series production parts on AM in the following years,” Anderhofstadt explained.

Ralf Anderhofstadt, Head of the Center of Competence Additive Manufacturing at Daimler Truck | Daimler Buses.
The extensive groundwork laid during this period paid off, enabling Daimler Buses to realize that AM was more than just another production technology. It offered a new digital business model that went beyond manufacturing, opening up opportunities for collaboration across industries. This realization led to the formation of AMS – Additive Manufacturing Solutions, a consulting unit established to explore the exciting field of industrial 3D printing in collaboration with other companies from various industries.
The Birth of AMS – Additive Manufacturing Solutions Daimler Truck
As AM technology gained traction within Daimler Truck & Buses, numerous companies from different industries approached the truck & buses manufacturer with questions about becoming involved in 3D printing at an industrial level. Recognizing the potential to share its expertise, Daimler Buses formed the consulting unit to help other businesses leverage AM technology.
Anderhofstadt highlighted the comprehensive services offered by AMS: “As part of AMS – Additive Manufacturing Solutions, we map the entire digital value chain in line with our internal procedure at Daimler Truck. This includes various workshop and consulting packages from Quick Start to Part Screening, as well as digitalization and brand protection, right through to well-founded quality management packages and certified approval processes.”
AMS – Additive Manufacturing Solutions positions itself as an all-in-one provider. In addition to those areas already highlighted by Anderhofstadt, a significant offering is an all-inclusive Software as a Service (SaaS) package, which helps clients navigate the complexities of adopting 3D printing technology.
Additionally, AMS has expanded its services to include data preparation and digital warehousing. This service portfolio allows customers to benefit from AM’s flexibility, particularly in situations where parts are difficult to source or suppliers are unavailable.
Leveraging AM Amidst Supply Chain Disruptions
The COVID-19 pandemic profoundly impacted global supply chains, causing delays and shortages across various industries. For Daimler Trucks & Buses, AM proved to be a valuable tool in navigating these challenges. “During the pandemic and to this day, there are still numerous missing parts and supply chain delays in various industries. Since then, industrial 3D printing has been able to showcase its strengths in a more well-founded manner,” Anderhofstadt noted. In addition to the partnership with certified AM service providers, this led to the construction of a mobile “mini factory” for the decentralized production of 3D-printed spare parts.
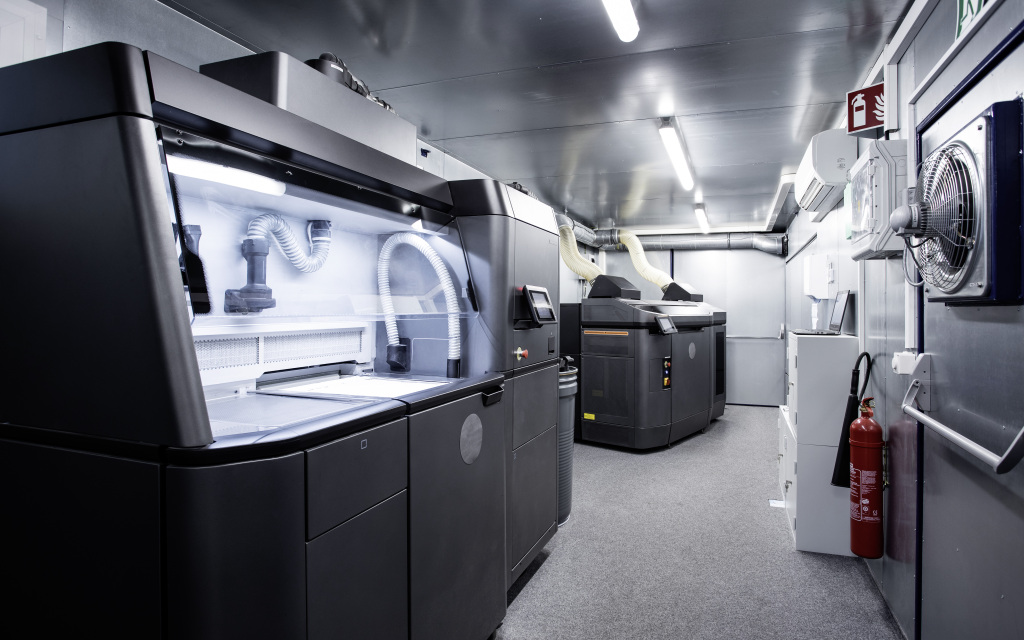
The mobile printing centre in the form of a container includes all of the stations relevant to the production of spare parts using a 3D printer on an area of only 36 m2.
Daimler Truck & Buses has already 3D printed over 100,000 spare bus parts digitized over 2,500 more. With its Digital Parts Warehouse, the company enables the management and retrieval of 3D models, ensuring that critical parts can be produced as needed, significantly reducing storage costs and transport distances. This capability has enabled them to mitigate some of the supply chain disruptions by quickly producing parts on-demand, reducing dependency on traditional supply chains.
Meeting Industry Standards and Regulations
One of the key challenges in adopting AM for series production is ensuring that parts meet the stringent quality and reproducibility standards required by the automotive industry. “Series production by AM is only possible if these aspects are 100% ensured,” Anderhofstadt emphasized. Daimler Buses has invested significant time and energy into developing well-founded approval processes and certifications to ensure that their 3D printed parts meet all requirements.
To this end, AMS offers comprehensive additive preparation services. These include data generation, which involves creating 3D models through scanning and reconstruction, and product protection through exclusive branding and texturing options. These services ensure that AM components not only meet quality standards but also align with brand-specific requirements.
The Future of Additive Manufacturing at Daimler Truck
Looking ahead, Daimler Trucks & Buses plans to expand the use of AM across more materials and components in series applications. “We are convinced that the number of materials and components for series applications within Daimler Truck & Buses will continue to increase significantly in the coming years,” Anderhofstadt stated. This expansion is fueled by specific material developments and further approvals of different 3D printing processes for series production applications.

Daimler Buses and its service brand Omniplus have created a mobile printing centre for the decentralised production of 3D printed spare parts in order to be able to provide bus customers with spare parts more quickly.
Another crucial aspect of AM’s future lies in its integration with digitalization efforts, such as digital twins, virtual warehouses, and digital rights management. Daimler Truck’s Digital Parts Warehouse, for example, offers a sustainable and future-oriented management and backup of 3D models, enabling companies to optimize logistics and procurement. This digital transformation not only supports faster and more flexible responses to demand but also significantly contributes to sustainability efforts by reducing storage costs and transport distances.
Daimler Trucks & Buses’ journey from using AM for prototyping to launching its own AMS service highlights the transformative potential of additive manufacturing in the automotive industry. By embracing AM, Daimler Truck has not only enhanced its manufacturing capabilities but also opened up new digital business models and opportunities for collaboration across industries. As the technology continues to evolve, Daimler Truck is poised to remain at the forefront of the AM revolution, driving innovation and sustainability in the automotive sector.
Subscribe to Our Email Newsletter
Stay up-to-date on all the latest news from the 3D printing industry and receive information and offers from third party vendors.
Print Services
Upload your 3D Models and get them printed quickly and efficiently.
You May Also Like
Heating Up: 3D Systems’ Scott Green Discusses 3D Printing’s Potential in the Data Center Industry
The relentless rise of NVIDIA, the steadily increasing pledges of major private and public investments in national infrastructure projects around the world, and the general cultural obsession with AI have...
Formlabs Teams Up with DMG MORI in Japan
In late June, Nick Graham, Chief Revenue Officer at Formlabs, announced on LinkedIn that the company had partnered with DMG MORI, one of the world’s leading machine tool companies, to...
EOS in India: AM’s Rising Star
EOS is doubling down on India. With a growing base of aerospace startups, new government policies, and a massive engineering workforce, India is quickly becoming one of the most important...
3D Printing News Briefs, June 25, 2025: R&D Materials, 3D Printed Veneers, & More
In today’s 3D Printing News Briefs, 3DXTECH has launched a program that gives customers early access to experimental materials, and the first Lithoz CeraFab Multi 2M30 in the Czech Republic...