I never thought I’d be so excited about an event focused on additive manufacturing (AM) standards, but here we are! When I learned that the recent biannual ASTM F42/ISO TC 261 meeting would be held at The Ohio State University (OSU) in Columbus, Ohio—a mere 63 miles from my home in Dayton—I made plans to attend, but didn’t really know what to expect. First and foremost, this was one of the most well-organized industry events I’ve ever attended, and for me, it started with a tour of Quintus Technologies and ended with a visit to OSU’s Center for Design and Manufacturing Excellence (CDME). But I’ll share more about those later.
ASTM & ISO
Formed in 2009, ASTM International’s F42 committee works to develop standards for additive manufacturing. F42’s work is coordinated with other ASTM committees, as well as other national and international standards organizations that have related or mutual interests. That’s why, in 2011, ASTM signed an agreement with the International Standards Organization (ISO) to “increase their cooperation in the development of International Standards for additive manufacturing.” Thus, ISO/TC 261 was created to “develop and support Standards to promote the industrialization of this new technology,” i.e. additive manufacturing.
In 2016, ASTM and ISO unveiled a framework for creating global AM standards, which identifies standards-related gaps in the industry, prevents overlap in AM standards development, prioritizes AM standards areas, guides the work of creating standards, and more.
Last week’s ASTM F42/ISO TC 261 meetings, which took place in conjunction with ASTM AMCOE’s 11th Snapshot Workshop, were split into several categories, including Executive Meetings that were closed to general attendance and meetings strictly for ISO TC 261. While I didn’t make it to these, I did sit in on a convening for ASTM F42, one for an ISO/ASTM Joint Group (JG), and another for an ISO/ASTM Working Group (WG).
These meetings were different than anything I’ve ever attended, which makes sense. No one was saying, “Hey, my new machine/material/process is the brightest and shiniest of all; come buy it!” Or in my case, “Come write about it!” This was the detailed, nitty-gritty, down-in-the-dirt work that’s necessary to make sure everything in the AM industry advances through an alignment around standards. It was going through comments and suggested edits one by one, and agreeing to or rejecting modifications—everything from changing a verb to “specify” to ensuring all parts of the documents stayed true to scope. For instance, one comment suggested getting rid of the term “state of the art,” but as no rationale was given for the proposed change, it was rejected.
ISO/ASTM JG 80: Quality for AM Construction
F42 has 22 subcommittees, ranging from Test Methods, Materials and Processes, Maritime, and Data to Metals, Polymers, Ceramics, Terminology, Electronics, and Environment, Health, and Safety. As Pat Picariello, ASTM’s Director of Developmental Operations, explained to me in an email, ASTM’s “three Applications sub-sections…busiest at present” are Construction, F42.07.07, with 150 members; Aviation, F42.07.01, with 215 members; and F42.07.03 on Medical/Biological, 219 members. Though I didn’t attend the ASTM F42.07.07 meeting, I did make the tail end of the ISO/ASTM JG 80 meeting about Quality for AM Construction.
“It’s very helpful for us to be able to have some in-person meetings to discuss some of this stuff. Several of us have been working for the last several years on these standards. For us to be able to meet in-person and have more informal discussions that aren’t limited to one hour is going to help a lot, because I think a lot of the changes that need to be made to this overarching document—and these other documents—are going to require a lot of debate and discussion,” I was told by Megan Kreiger, Portfolio Manager of Additive Construction (AC) and the Department of Defense’s subject matter expert of AC at the U.S. Army Corps of Engineers, Engineer Research and Development Center (ERDC).
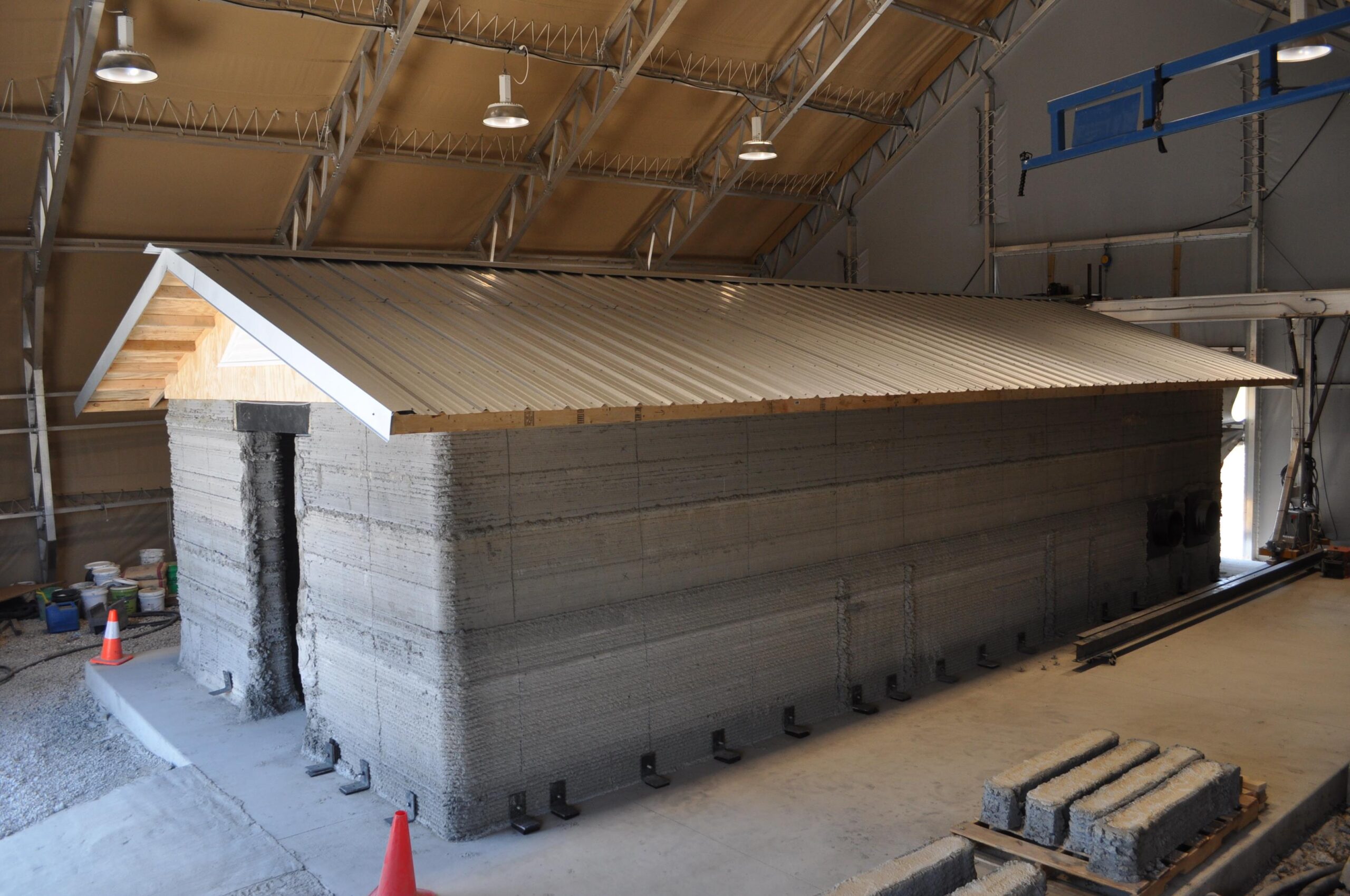
A barracks hut 3D printed by Kreiger and ERDC-CERL circa 2017. The printer cut building materials shipped by half and construction manpower requirements by 62 percent when compared to expedient plywood construction in overseas military construction. Image courtesy of ERDC-CERL.
I also spoke with Stephan Mansour, a consultant at Wohlers Associates who specializes in AC. He’s also the co-convener of JG 80 and the chair of ASTM F42.07.07, both of which focus on construction AM.
“What we’re trying to do is set a standard for additive construction to make sure that whatever is printed is safe and stands the test of time,” Mansour said about the ASTM and ISO work items. “The reason we are concerned about safety is to deliver structures that people can live in and ensure that they will last, but also to allow the general adopters of 3D printing to issue warranties and mitigate their risk. As a general contractor, you build something, you are responsible for it. So, you have to make sure that it stands the test of time and you have to have standards and codes that sort of meet that requirement.”
He explained that Standard 52939:2023 is one of the first published under ASTM and ISO together, and that it essentially bridges the gap between traditional construction and AC. Because there aren’t any existing standards that define how to certify 3D printed construction elements, they’re turning to the standards everyone’s already used to in construction, and showing how these can be used to certify 3D printed structures as well.
“So, that is bridging that gap and making people understand that this technology is just another tool on your construction site, just like an excavator or a crane or anything that you see on a typical construction site. It is not this revolutionary type of tool that’s going to make magic,” he said. “3D printing is there to address a pain point and a need. We have issues with safety, labor, materials, efficiency, productivity. It’s just another tool to address, if not all, then most of these issues.”
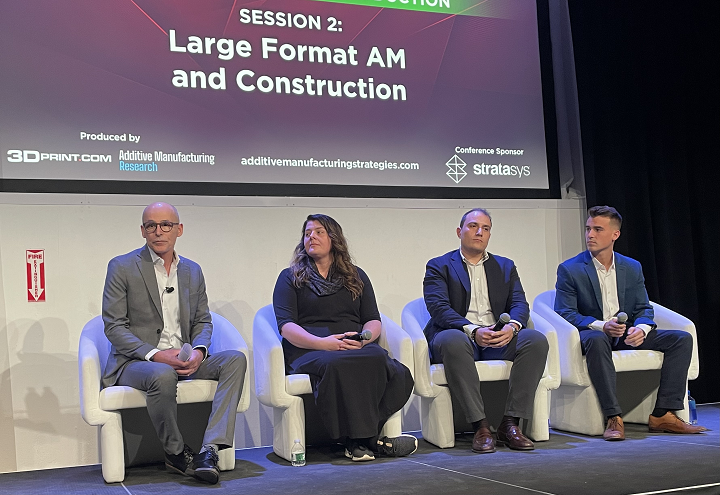
Stephan Mansour (L) moderating a panel on “Additive Manufacturing in Construction” at Additive Manufacturing Strategies 2024. Image: Sarah Saunders for 3DPrint.com
Mansour explained that the work done at the meeting was focused on updating 52939:2023 by making it more user-friendly, less confusing, and easier to implement.
“We can’t just issue it and be done. It’s an evolving industry, so it has to evolve,” he said. “So we’re trying to modify, modify, modify to where we get the perfect version, so we only have to revise it every three years.”
ASTM F42.07.03: Medical Applications
While I only caught the last half of the ISO/ASTM JG on Quality for AM Construction meeting, I was in attendance for the entirety of the ASTM meeting on F42.07.03, all about 3D printed medical applications. Matthew Di Prima, Materials Scientist at the U.S. Food and Drug Administration (FDA), provided the attendees with a quick overview of a recent Build Verification workshop, and then the meeting moved on to a brief presentation about AMiquam‘s W1-2CH and its use in the ISO 15548-1:2013 standard on non-destructive testing (NDT). AMiquam, which relies on compliant sensors for inline, layer-by-layer inspection of 3D printed parts, had coupled eddy currents and lattices to extract information about 3D printed parts, which contributes significantly to quality control and NDT.
Another point of discussion during the meeting was finding a faster, less expensive build coupon for verification of 3D printed spinal fusion cages. Tensile bars were the norm 10-15 years ago, but machining one of these is, as I heard someone say, “a horrible representative coupon for a spinal cage.”
There was plenty of debate during the meeting over the scope of WK82776, “New Test Method for Additive Manufacturing for Medical – Powder Bed Fusion – Assessment of Residual Powder,” a standard that has been in the works for over two years. The goal is to develop a uniform method for collecting and recording residual powder from medical device 3D printing. Apparently, some aerospace industry attendees in a previous meeting were very excited about the use of ultrasonic technology for this, so there will be a validation of this approach. As for measuring the residual powder, there are a few methods for this, including SEM and gravimetric analysis.
Another topic of discussion was a newer standard: WK90089, “New Test Method for Additive manufacturing of medical devices – Test Method – Relative Density of Porous Structures via Gravimetric Analysis.” This was proclaimed as a valuable test method, and the standard will designate a specific geometry for test specimens, applied to 3D printed lattices and intentionally porous materials. It was asked if a draft of the standard could be ready in six months, and if the laughter was any indicator, the answer is likely no. This brings me to the final meeting I attended.
ISO/ASTM WG2 – F42.05: Material & Processes
The F42.05 subcommittee for ISO/ASTM on Material & Processes has over 20 matching standards, including the following:
-
F3049-14(2021): Standard Guide for Characterizing Properties of Metal Powders Used for Additive Manufacturing Processes
-
F3091/F3091M-14(2021): Standard Specification for Powder Bed Fusion of Plastic Materials
-
F3301-18a: Standard for Additive Manufacturing – Post Processing Methods – Standard Specification for Thermal Post-Processing Metal Parts Made Via Powder Bed Fusion
-
ISO/ASTM52930-21: Additive manufacturing — Qualification principles — Installation, operation and performance (IQ/OQ/PQ) of PBF-LB equipment
-
ISO/ASTM52945-23: Additive manufacturing for automotive — Qualification principles — Generic machine evaluation and specification of key performance indicators for PBF-LB/M processes
There are many others I didn’t list, so obviously, that’s a lot of work for this group to take on.
During one conversation, an attendee from the Federal Aviation Administration (FAA) said that they weren’t interested in making standards for the sake of having them, i.e. for no reason. He urged the need for faster decision-making when it comes to AM industry standards, explaining that he needs to move quickly when companies come and say they need something. He said that if AM would be a good solution, but the necessary standard won’t be complete for a few years, he’s going to go with the standards, and probably technology, that the customer is using.
I can see both sides here. On the one hand, because additive is a newer technology than something like casting or injection molding, we need our butts to be covered and these standards to be rock-solid. On the other hand, the longer it takes us to finalize them, the less patient industries like aviation are apt to be, and the more likely they are to choose the familiar. As the saying goes, if it ain’t broke, don’t fix it, right? However, just because something isn’t broken doesn’t mean we can’t make it better, which is where AM so often comes into play.
I’ll bring this first piece to a close by noting that someone in the ISO/ASTM F42.05 meeting, after the FAA attendee made his point, quoted President Dwight D. Eisenhower, stating that “plans are worthless, but planning is everything.” What do you think about this?
Subscribe to Our Email Newsletter
Stay up-to-date on all the latest news from the 3D printing industry and receive information and offers from third party vendors.
Print Services
Upload your 3D Models and get them printed quickly and efficiently.
You May Also Like
The Market and Industry Potential of Multi-Material 3D and 4D Printing in Additive Electronics
Additive manufacturing leverages computer-based software to create components for products by depositing either dielectric or conductive materials, layer by layer, into different geometric shapes. Since its birth in the 1980s,...
3DPOD 262: Bio-inspired Design for AM with Dhruv Bhate, Arizona State University
Dhruv Bhate is an associate professor at Arizona State University. There, he looks at structures, materials, and design. Previously, he worked at PADT as well as in the semiconductor and...
3DPOD 261: Tooling and Cooling for AM with Jason Murphy, NXC MFG
Jason Murphy´s NXC MFG (Next Chapter Manufacturing) is not a generalist service; instead, the company specializes in making tooling. Using LPBF and binder jet, the company produces some of the...
3DPOD 260: John Hart on VulcanForms, MIT, Desktop Metal and More
John Hart is a Professor at MIT; he´s also the director of the Laboratory for Manufacturing and Productivity as well as the director of the Center for Advanced Production Technologies....