The US Air Force is currently one of the largest funding bodies in 3D printing. The amount of work that the Air Force is doing in 3D printing is simply incredible. The 3D printing industry is being fundamentally being shaped by the US Air Force´s needs. In this article we will look at what the Air Force is doing with and in 3D printing and why it is doing it. The areas the Air Force seems interested in can be divided into a few key areas: better 3D printing and processing, electronics 3D printing, and maintenance, repair, and overhaul (MRO).
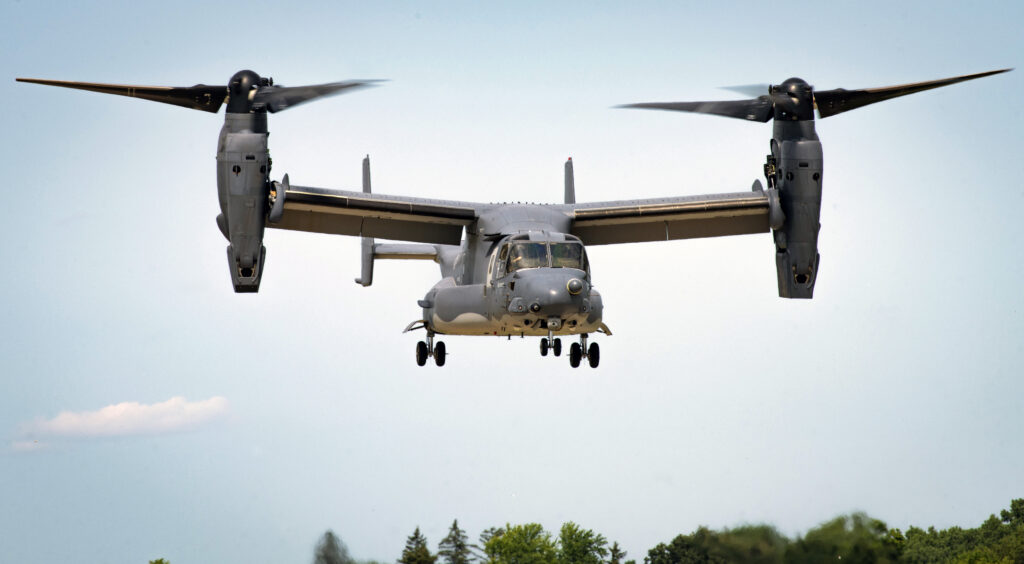
A CV-22 Osprey assigned to Air Force Special Operations Command. Image courtesy of U.S. Air Force/Senior Airman Miranda Mahoney.
Better 3D Printing & Processing
The AFRL and the Air Force seem committed to optimizing 3D printing, funding extensive research to industrialize AM and reduce costs. As the following examples show, their efforts focus on improving processes to scale aerospace parts production.
- Additive Manufacturing Modeling Challenge: In November 2019, the AFRL organized this challenge to evaluate the community’s ability to predict the performance of LPBF parts. The challenge, which saw fierce competition, was won by Dassault Systemes Government Solutions Corp. and several leading universities.
- Additional Challenges: The AFRL conducted multiple challenges, including a scanning challenge and others focused on various aspects of 3D printing.
- Partnerships: IperionX and QuesTek both won AFRL challenges and a collaboration with NASA demonstrated innovative solutions in high-temperature composites.
- Technology Adaptation: The AFRL provided funding to CTC to adapt SLM Solutions machines for their specific needs.
- Advanced Research: Utilizing X-rays to examine part properties, investigating better melt pool dynamics, and collaborating with institutions like the Barnes Group to advance 3D printing technology. Advanced process control for polymer and metals powder bed has also gotten a number of contracts.
- Significant Investments: Investments include $1.25 million for in situ modeling, $8.7 million to Relativity Space, and participation in a $12 million America Makes project.
3D Printed Electronics
Through 3D printing, these devices could be conformal and easier to integrate into existing cavities or craft. 3D printed electronics may seem like a small part of the potential for 3D printing, but aircraft have hundreds of kilometers of wiring on board. Wire harnesses make up a significant weight element on board aircraft and UAS.
For drones, the absence of a pilot inside means there’s no need for an engineer to crawl around inside for maintenance. You can simply take the drone apart and service it that way, or entire assemblies can be immediately replaced. With digital wiring and a significant reduction in wire harnesses, planes can save weight and radically change their form factors.
- Stretching surfaces: In 2017, the AFRL worked with American Semiconductor to make flexible microcontrollers. In the same arena, they created a 3D printed, more efficient airfoil with stretchable skin that can be moved without deforming the surface. In another stretchy project, they worked with Harvard’s Wyss Institute to develop a flexible 3D printing technology using conductive inks with silver-fused TPU. In that project, they 3D printed LED lights and placed microcontrollers in printed structures. In another, far larger project, $154 million was spent on flexible 3D printed electronics. These are baby steps into a more soft robotics and flexible world for the Air Force. The more conformal they can make devices, the more design freedom they have. It is also tempting to consider replacing actuators and other motors inside aircraft with flexible materials.
- Power: Power is another element that needs optimization. Airbus and others are looking at electric aircraft, so it makes sense to learn to 3D print cheaper solar cells.
MRO
MRO is a big focus for the military generally. For the Air Force, maintenance and replacement of parts is a significant cost and labor concern. Parts must be made ahead of time and stored around the world, tying up billions of dollars in capital for decades. Moreover, that one critical part may not be available where a specific plane needs it. Digital inventories and MRO through 3D printing could save a lot of money and enable the Air Force to sustain itself more efficiently and quickly.
- Out of Production: The AFRL held a 25-company, $8 million MRO project for out-of-production and difficult-to-get parts for old aircraft, working with America Makes, the University of Dayton Research Institute, and YSU.
- Material Extrusion: The 910th Maintenance Group received $72k to purchase an AON3D high-temperature material extrusion system, while another project provided $4 million to Juggerbot to combine medium-format material extrusion with Direct Write. Material extrusion offers low-cost components that can be made very locally. The Air Force is clearly interested in the technology but needs higher-performance polymers that can withstand heat and are smooth. These projects demonstrate their efforts to engineer solutions to these issues.
- Engines: The Air Force is not just interested in simple components; they also tested motor components and looked at 3D printed MRO aircraft engine components. In another project they 3D printed a critical component, a sump cover.
- DED: While most work is in Powder Bed and Material Extrusion, there is increasing interest in DED. They have qualified DED components for 3D printing, indicating more work being done in this area.

Staff Sgt. Anthony Brown uses software to digitally design a night guard on a digital teeth model. (Airman 1st Class Makensie Cooper/Air Force)
Other
In the other category, we can find a body of composites research and extensive work on high-temperature polymers. Additionally, new applications and construction 3D printing are included here. This category is surely much larger. They’re probably not going to publish a new call for a material for a Horn antenna or 3D printed CIWS guidance components any time soon. However, given this diverse collection, we can see that the Air Force is exploring facilities, 3D printed protection for aircraft, and highly optimized communications hardware.
- Space Aged: The Air Force funded an orbital antenna project to enhance communications cost-efficiently by allowing more efficient antennas to be made less expensively.
- Building materials: Branch Technology is making a 3D printed insulation kit that will be retrofitted to existing buildings for $1.13 million.
- Composites: The Air Force has done extensive work on composites, including projects on 3D printed composites and wing composites through 3D printing.
- Tooling: Many aerostructures and other aircraft parts are made indirectly with tooling that is milled or 3D printed, explaining the interest in large-scale tooling.
- Software and Digital: They also aim to protect the 3D printing information space, which explains their work with Seoul’s Sungkyunkwan University on cybersecurity and 3D printing.
- New Materials: While superalloys and advanced polymers such as PAEK materials were developed in the 1970s, little breakthrough material development has occurred since then. The Air Force is working on ODS materials, intermetallics, and other newer materials, including exotic projects such as 3D printing beryllium.
Now it’s important to note that the above list is not exhaustive; these are just our articles on the AFRL augmented by a Google search. There is much more going on and much more that they don’t disclose. From sensors to door hinges and missiles, the AFRL is broadly investing in 3D printing. They are active in all processes, from material extrusion to powder bed fusion and composites. They’re looking at MRO, procurement, improvements to new equipment, and more.
From existing aircraft to improvised solutions and future hypersonics, they are using 3D printing for many vehicles as well. And this is only the AFRL portion we are examining. Different commands and parts of the Air Force are doing much more.
If we look at the breadth and depth of their activities, it becomes very clear that the Air Force is absolutely critical for 3D printing now. The Air Force is currently the biggest funding partner for 3D printing, involved in everything from blue-sky research to very mature applications. More importantly, the Air Force is not just looking into 3D printing, exploring it, or trying to develop it; they are aiming to own it. The Air Force clearly wants to outmatch any potential opponent in the world in technological 3D printing prowess, whether in software, materials, machines, or overall capability.
Subscribe to Our Email Newsletter
Stay up-to-date on all the latest news from the 3D printing industry and receive information and offers from third party vendors.
Print Services
Upload your 3D Models and get them printed quickly and efficiently.
You May Also Like
Consolidation in AM: How 2025 Is Shaping the Industry’s New Normal
The first half of 2025 has been marked by a clear shift in the additive manufacturing (AM) industry. Companies are no longer just focused on developing new tech by themselves....
Etsy Design Rule Change Reduces Selection of 3D Printed Goods
Online marketplace Etsy has implemented a rule change requiring all 3D printed goods on the site to be original designs. The update to the site’s Creativity Standards states, ¨Items produced using...
U.S. Congress Calls Out 3D Printing in Proposal for Commercial Reserve Manufacturing Network
Last week, the U.S. House of Representatives’ Appropriations Committee moved the FY 2026 defense bill forward to the House floor. Included in the legislation is a $131 million proposal for...
Transforming From Tourist to Native: Duro CEO Michael Corr Explains Why the Company Rebuilt its PLM Software on AI
In these early innings of the AI boom, many market analysts have expressed concern that AI spend has gotten too far ahead of the technology’s proven ability to deliver significant...