Norsk Titanium (NTI.OL) has long been blazing a path in the challenging field of producing flight-critical hardware using directed energy deposition (DED). Achieving a significant milestone, the Norwegian firm successfully manufactured parts for Boeing in 2017. This paved the way for a public listing in 2021, and more recently, Norsk has produced flight-approved components for Airbus. While many in the industry favor powder bed fusion for crafting aeronautical parts, only a few, like Norsk Titanium, are utilizing DED.
DED technologies, although not optimal for creating highly intricate components, are effective for producing larger parts at a considerably reduced cost. However, Norsk Titanium’s pioneering journey has recently encountered hurdles. The company is actively seeking new capital, suggesting challenges in maintaining its innovative momentum in this specialized sector.
Therefore, that the company has announced its role in supplying flight-critical structural components to General Atomics Aeronautical Systems (GA-ASI) must be a welcome shot in the arm. GA-ASI is known for manufacturing prominent Unmanned Aircraft Systems (UAS) platforms, such as the Predator and Reaper. Working with GA-ASI’s Additive Design & Manufacturing Center of Excellence, Norsk is currently involved in the evaluation and testing of these components. This collaboration builds upon a foundation laid in 2022 when GA-ASI conducted a series of tests on parts provided by Norsk.
“General Atomics has been dedicated to maturing directed energy additive and implementing it in their production programs. After an extensive collaborative qualification effort over the past few years with Norsk Titanium, GA-ASI plans to apply the qualified process to structural components within their next generation platforms currently under development, and is planning on their first flight of a critical, structurally loaded component, within the 2024-2025 timeframe,” stated Norsk Titanium Vice President of Commercial Nicholas Mayer.
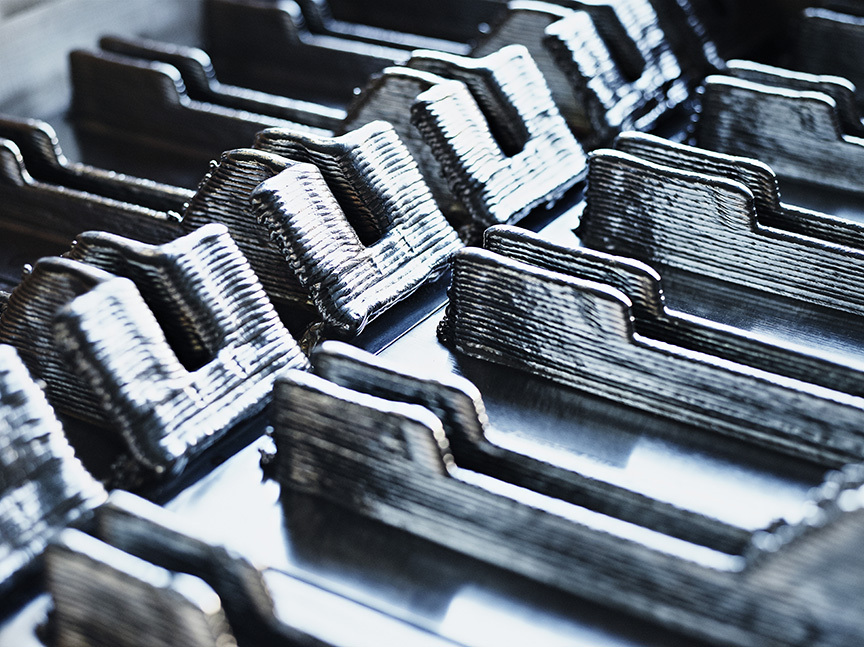
Blanks 3D printed using Norsk Titanium’s Rapid Plasma Deposition process. Image courtesy of Norsk Titanium.
The drone market is indeed experiencing significant growth, with GA-ASI positioned as a clear leader in the space. Historically, drone usage in conflicts was primarily focused on surveillance and targeted operations aimed at eliminating terrorists, often with the unfortunate collateral damage of civilian casualties. However, the scope of drone warfare has evolved considerably. The demand for more specialized drones is on the rise, driven by the need for diverse payload configurations and capabilities to meet the increasingly complex requirements of modern warfare. The pivotal role of drones in recent conflicts has underscored their versatility and indispensability in modern warfare. Drones have been instrumental in intelligence gathering, artillery targeting, direct strikes, and electronic jamming, showcasing their critical role in contemporary military operations.
The United States is a clear leader in the development and deployment of advanced drones, using them extensively in various operations. However, it’s important to recognize Israel’s pioneering role in drone technology. Israel was an early innovator in the field and remains a significant exporter of these vehicles. Israeli advancements include the development of cost-effective drones and loitering munitions.
In the context of the conflict in Ukraine, the spotlight has not been solely on high-end U.S. drones. Inexpensive Chinese consumer drones, particularly from manufacturers like DJI, have played a crucial role. These more accessible products have been instrumental in the conflict, despite the U.S. having almost no market share in this specific segment.
One of the most in-demand drones currently is the Bayraktar UAV, produced by Turkey. While a GA Grey Eagle starts at around $21 million, the Bayraktar TB2 is available for approximately $5 million. This UAV has proven to be potentially decisive in conflicts such as the Nagorno-Karabakh war and has significantly impacted Ukraine’s ability to resist the Russian invasion.
This scenario illustrates that U.S. drone supremacy is under threat in which allies are offering cost-effective alternatives that are changing the dynamics of drone warfare. Furthermore, the man-packable drone market is dominated by a Chinese firm.
What is unfolding appears to be a classic case of the Innovator’s Dilemma, where products that are “good enough” and less expensive might overtake more technologically advanced counterparts. U.S. supremacy in large, globally-operating UAVs seems secure for the moment. However, the advent of cost-effective, locally piloted drones capable of achieving desired outcomes at a lower cost suggests they will become increasingly predominant.
GA-ASI has achieved notable success in crafting ideal drones for affluent nations with global commitments, such as the U.S. However, the focus is shifting towards drones that excel in tactical operations. To maintain its competitive edge, GA-ASI must strive for cost efficiency and adaptability.
With 3D printing, GA-ASI can produce drones more economically. By integrating components, minimizing part count, crafting more optimized components, and generally reducing mass, the company can enhance UAV drone performance and payload capacity. Additionally, 3D printing enables GA-ASI to rapidly produce custom models for new clients. Further, automating a segment of its production process could expedite drone delivery and alleviate production backlogs.
3D printing has been a closely held secret in drone manufacturing since the 1990s, with a significant portion of the U.S.’s 3D printing capacity devoted to drone production. GA-ASI and other firms are now challenged to utilize this knowledge and future investments to secure a leading position in the drone industry. Failing to do so could prove costly for the U.S. and its allies, both in terms of economic impact and strategic positioning.
Subscribe to Our Email Newsletter
Stay up-to-date on all the latest news from the 3D printing industry and receive information and offers from third party vendors.
Print Services
Upload your 3D Models and get them printed quickly and efficiently.
You May Also Like
Heating Up: 3D Systems’ Scott Green Discusses 3D Printing’s Potential in the Data Center Industry
The relentless rise of NVIDIA, the steadily increasing pledges of major private and public investments in national infrastructure projects around the world, and the general cultural obsession with AI have...
Formlabs Teams Up with DMG MORI in Japan
In late June, Nick Graham, Chief Revenue Officer at Formlabs, announced on LinkedIn that the company had partnered with DMG MORI, one of the world’s leading machine tool companies, to...
EOS in India: AM’s Rising Star
EOS is doubling down on India. With a growing base of aerospace startups, new government policies, and a massive engineering workforce, India is quickly becoming one of the most important...
3D Printing News Briefs, June 25, 2025: R&D Materials, 3D Printed Veneers, & More
In today’s 3D Printing News Briefs, 3DXTECH has launched a program that gives customers early access to experimental materials, and the first Lithoz CeraFab Multi 2M30 in the Czech Republic...