On July 4, aerospace giant Airbus opened a new R&D facility in Filton, England: the Wing Technology Development Centre. In the latest sign that the UK government is serious about making up lost ground in terms of the nation’s advanced manufacturing capabilities, UK Minister for Industry and Economic Security, Nusrat Ghani, was on location to join in inaugurating the WTDC.
In its reporting of the event, Reuters framed the WTDC’s opening in the context of what the news agency referred to as Airbus’s “technology race with Boeing.” The article placed a particular emphasis on the significance of the new facility to Airbus’s long-term efforts to eventually replace the single-aisle A320 family of aircraft — the company’s biggest seller.
The “technology race” between the world’s two largest aircraft manufacturers essentially comes down to moving towards producing wings with composites instead of aluminum, on the A320/321 and the Boeing aircraft that most directly competes with those models, the 737. Although wings on larger jets, like the Boeing 787, already contain significant percentages of composites like carbon fiber, the higher cost and lengthy post-processing involved in use of such materials has thus far prevented their incorporation into single-aisle models, which are produced at much higher rates and have much tighter margins.
Notably, in this vein, reporters Joanna Plucinska and Tim Hepher wrote that the use of composites in wings for single-aisle planes could “require a manufacturing revolution to keep up with production targets.” According to Airbus, the new design must not only achieve lighter and longer wings, but also has to be able to be manufactured at lower costs and faster rates than are currently possible with composites. Similarly to the Boeing 777X, Airbus is also intent on incorporating folding wing-tips into the new design, in order to allow for the greater length without necessitating a global overhaul of airport layouts.
Given such ambitious goals, it is not surprising that, in the case of the A320, hypothetical replacements aren’t expected to be flight-ready until 2035. Nevertheless, the lead time involved in the aerospace sector means that any new production methods for a model that needs to be in the air by 2035 would have to be settled upon by 2027-2028. Thus, while the Airbus R&D program is referred to with the shorthand “Wing of Tomorrow” (WoT), this and the parallel Boeing project, “Transonic Truss-Braced Wings”, are already urgent concerns for both companies.
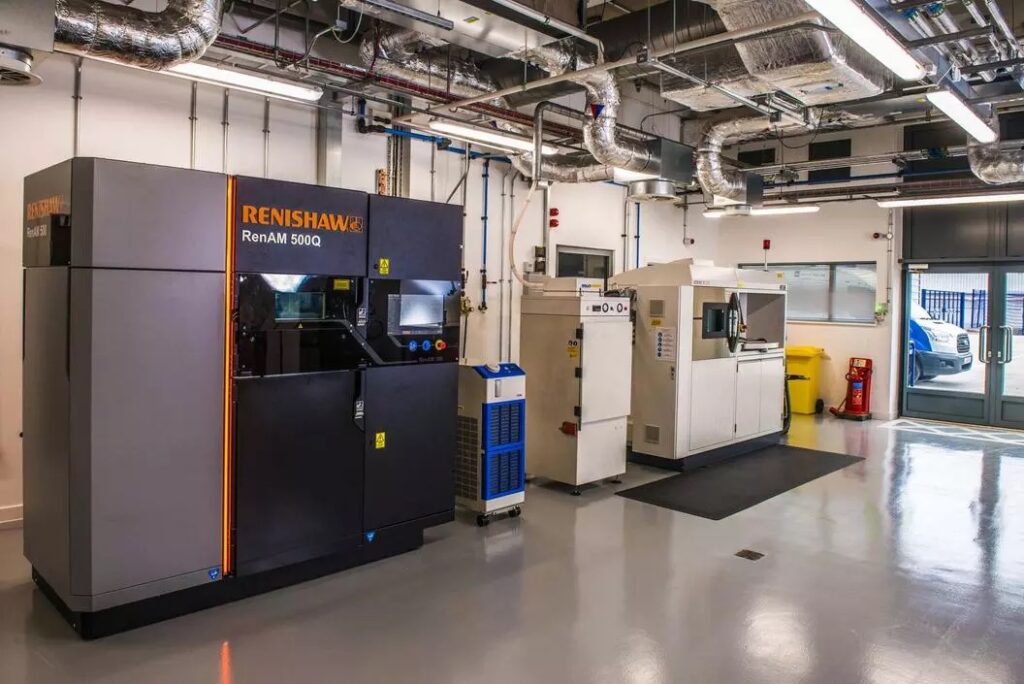
As Sue Partridge, head of the WoT initiative at Airbus, told Reuters, “It’s our program to prepare technologies for the next generation of Airbus aircraft, whatever that is. …We need to develop composite technologies to get weight out of the wing, but they need to be at the right cost and the right production-rate capability.” In an Airbus press release about the WTDC, Partridge explained, “It’s about preparing our people, technology, industrial system, supply chain and digital and physical capabilities for next generation aircraft. We’re leveraging industry partners and the very best digital tools and automation to identify potential technology bottlenecks that may slow us down in the future. The foundations we lay now will help us build better and faster when the time comes.”
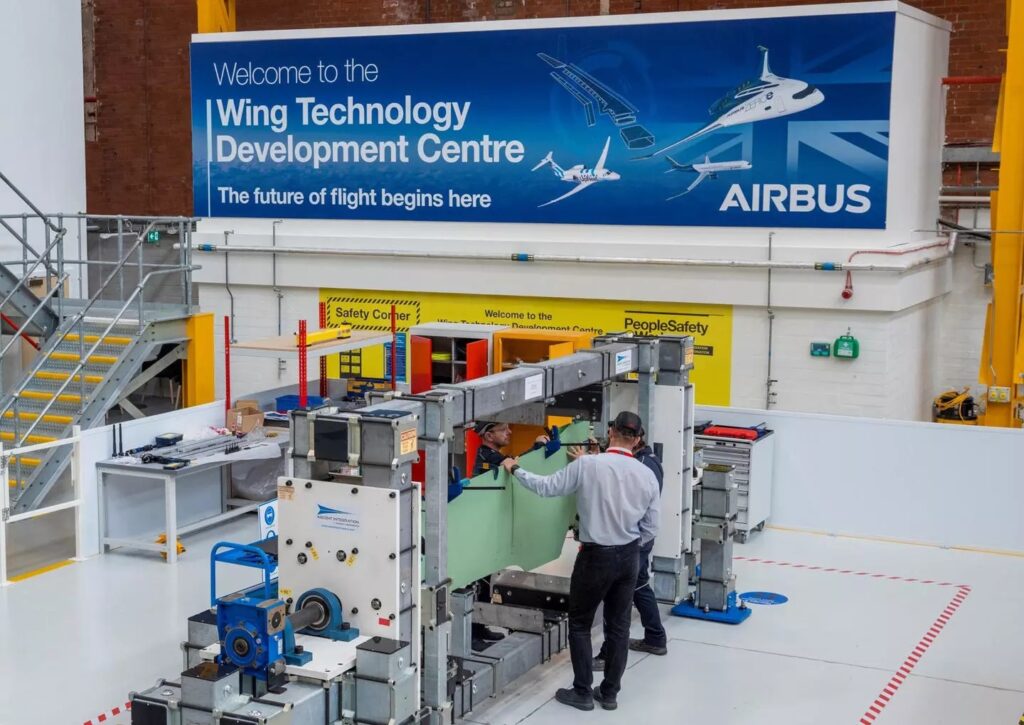
And, although this is all ostensibly about future aircraft models, when Reuters asked Partridge if the “new technology” might also end up being useful for work on current Airbus models, she said, “Yes, theoretically.” Of course, no word on what the “new technology” is, specifically, but anyone who has followed the additive manufacturing (AM) even somewhat closely in the past few years knows that Airbus and Boeing have been two of the most influential forces in accelerating the progress of all the technologies comprising the AM sector.
This is especially true regarding the three main, interrelated concerns at hand in the WoT program as well as in Boeing’s competing efforts: lightweighting, fuel efficiency, and unique geometries. In other words, I think the subtext of this development is more or less, “Ok, AM works — now, can we get it to work at scale within five years?”
Interestingly, even if the answer ends up being “no” for this particular purpose, that alone will not be enough to determine if the overall effort was a success or a failure. In fact, considering that the world needs more things like windmills and satellites than it needs more airplanes at this point, it is perhaps more likely that the purpose of talking about next-generation aircraft is to support next-generation R&D efforts, as opposed to the other way around. Airbus might never figure out how to use AM profitably at scale for the largest airplane parts, but that is far from the same thing as saying that Airbus will never figure out how AM-driven serial production for large-scale parts can be done profitably.
Images courtesy of Airbus
Subscribe to Our Email Newsletter
Stay up-to-date on all the latest news from the 3D printing industry and receive information and offers from third party vendors.
Print Services
Upload your 3D Models and get them printed quickly and efficiently.
You May Also Like
Josh Makeshift and the New Gold Standard 3D Printing Content Creation
In the beginning, 2007 or so, 3D printing videos were almost wholly absent from the web. Then, here and there, makers started to upload pictures of their rickety RepRaps and...
Formlabs Teams Up with DMG MORI in Japan
In late June, Nick Graham, Chief Revenue Officer at Formlabs, announced on LinkedIn that the company had partnered with DMG MORI, one of the world’s leading machine tool companies, to...
AM Research Webinar Explores Continuum’s Sustainable Metal Additive Manufacturing Powders
Metal additive manufacturing (AM) powder supplier Continuum Powders is working to develop solutions that empower industries to reduce waste and optimize their resources. An independent life cycle assessment (LCA) of...
Seakeeper Ride Releases Pocket Fit Kits
Seakeeper Ride makes a Vessel Attitude Control System (VACS), which greatly reduces the pitch and roll of pleasure craft. The Fort Myers-based company hopes to make boating more comfortable by...