Australian OEM SPEE3D, which specializes in cold spray metal additive manufacturing (AM) solutions that work under extreme conditions, is one of the more interesting companies in the AM industry right now, due to its fast, relatively low-cost, portable technology. As predicted by Macro Analyst Matt Kremenetsky in December of 2022, the company’s metal 3D printing is poised for a breakout this year, and after speaking with Paul Maloney, SPEE3D’s Chief Sales Officer, at RAPID + TCT recently, it seems like this is still the case.
Defense 3D Printing
“We are doing a ton on the defense side,” Maloney said, which seems to have been true for quite some time. “It’s kind of a fortuitous thing, I think COVID really pushed us towards defense, because Australia was locked down. We spent a lot of time in the bush with the Australian defense force, so it kind of drove us to a defense angle.”
Having a deployed machine that can print anywhere, using multiple materials, definitely made defense an obvious application.
“I was at Stratasys and Desktop Metal, and at both of those, we were pushed to have deployable machines. But neither company was really willing to do the ruggedization of the machines. So, when I heard about [SPEE3D], I was like, ‘Oh my god, this is a home run for defense.'”
Maloney noted the recent press with the UK army and the US military, and said that SPEE3D has some “significant contracts” with the DoD that can’t yet be discussed.
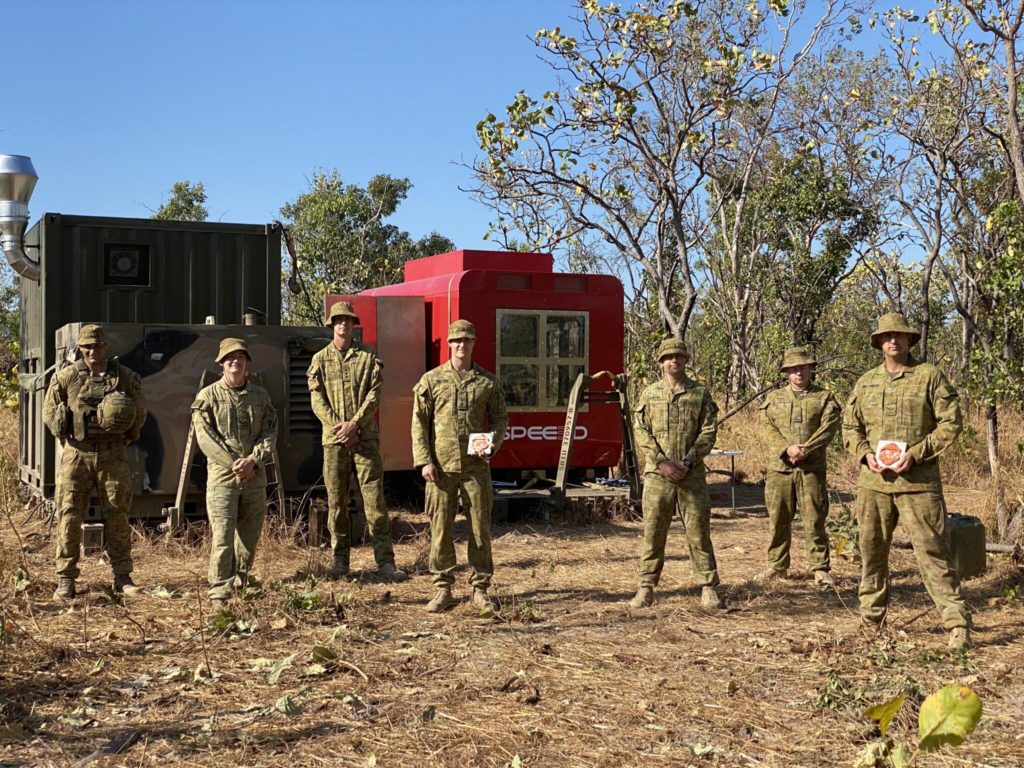
“So, from a defense side, why is this so compelling? It’s kind of both ends of the spectrum,” Maloney continued. “One end of the spectrum is printing at the point of need.”
If a piece of equipment goes down out in the field, the military typically has three options: destroy it, protect it, or bring in heavy equipment to tow it out of the field and bring it back to be repaired. With all three of those options, the risk to soldiers’ lives is potentially high. Maloney explained that the ultimate goal here, and one that SPEE3D’s technology enables, is to print something quickly that will work in the short-term until the equipment can be safely brought back to base.
“It may not be the ultimate part that stays on there, but it keeps the equipment in the fight,” he said.
Commercial 3D Printing
The other end of the spectrum that SPEE3D is working on involves commercial accounts, in which “the way certain parts were procured in the past are no longer open to them,” for geopolitical reasons or a lack of expertise in the manufacturing process. The company has been approached by potential customers who have extremely complicated materials that they don’t think can be produced any other way except machining or cold spray.
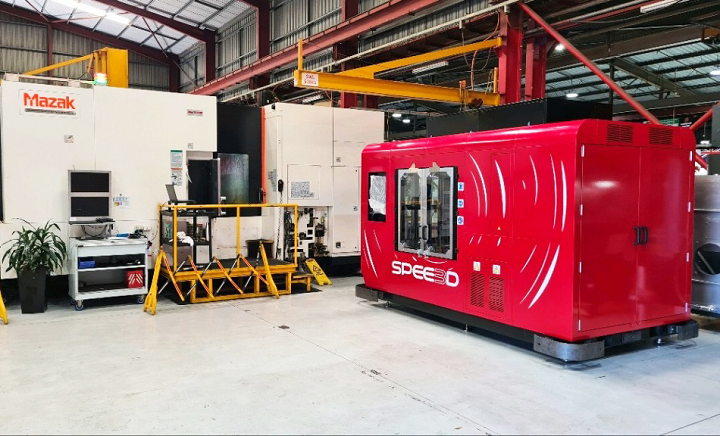
“We’re starting to target some commercial applications as well, for materials that are hard to manufacture traditionally, or there’s a long lead time,” Maloney explained. “So expeditionary machines on the commercial side…if you look at natural resources, oil and gas, mining, these types of organizations have very similar challenges to defense. You’ve got equipment out in the middle of nowhere, and something breaks. It’s not necessarily a life or death scenario, but it’s costing hundreds of thousands to millions of dollars every hour that you’re stopped.”
SPEE3D has sold and shipped “a lot of equipment” over the past eight months, “so we’re really up on the map quite a bit.” At its RAPID booth, the company was printing live on its smaller LightSPEE3D printer, producing a variety of copper parts like a rocket nozzle liner, a replacement flywheel part for a mechanical system used in several industries, a cooling block, and a V8 inlet manifold runner, which was made for an s5000 open-wheeler built by Garry Rogers Motorsport and demonstrated at last year’s Melbourne Grand Prix. Other parts made of aluminum, aluminum bronze, and copper were also on display.
University Partnerships
A few of SPEE3D’s partners were also at the booth to represent their companies and technologies, including high-pressure specialty gas compressor manufacturer Alkin; Diversitech, which provides customizable air pollution control solutions that comply with local regulations; and Comet, a public-private partnership between New Jersey Institute of Technology, New Jersey Innovation Institute, and US Army DEVCOM AC to advance education, innovation, and workforce development in advanced manufacturing. Speaking of this, Maloney also told me that SPEE3D has some great partnerships with universities at the moment.
“We approach education a little different than other companies I’ve worked for, where you just sell a machine and throw it over the fence and let them do what they want with it. We’re very targeted with how we approach universities, and that’s driven by Byron [Kennedy] and Steven [Camilleri], our two co-founders, because they have university and research backgrounds. They know specific universities that have a certain expertise, like metallurgy, manufacturing, AM, or cold spray,” he explained. “So we targeted specific universities, and UCI is a great example.”
For reference, in mid-April, SPEE3D announced a partnership with the University of California Irvine (UCI), which used grant support from the Air Force Office of Scientific Research (AFOSR) to acquire a WarpSPEE3D printer. As Maloney explained, universities, like UCI, acquire SPEE3D’s equipment, and then the company partners with said university for research, and funds further development of its technology. In addition to this development, the other major benefit is workforce development. I was told that partnerships with several other universities, in both the U.S. and Europe, will be announced later this year.
Metal AM Whitepaper
We wrapped up our conversation by talking about a whitepaper in Metal AM’s spring issue that was written by CTO Camilleri, along with SPEE3D’s Andrew Duguid, Sam Katz, and Chris Massar, and several other authors. The article, “What is Good Metal AM? Exploring the Industry’s Value Metrics for Production,” was being distributed at the SPEE3D booth, and around the rest of the show floor. The authors analyze the value of metal AM by establishing use cases for more traditional mass production and supply chain, as opposed to the ones that are suited for additive. Then, they proposed a framework of important criteria that can help industrial organizations determine which processes would be appropriate for their particular application.
“What I really like about the article is…we all know that there are challenges across the world right now from a manufacturing standpoint, right? We’re hearing about sovereign capability, we’re hearing about national defense. Basically what it boils down to is most of the world has lost the ability to manufacture and scale in their own country, so it’s all been export,” Maloney said. “There are solutions for that. It’s not just specifically cold spray, but if you look at additive, there are a bunch of different technologies, specifically on the metal side, that can start to solve these problems very quickly. So it’s a great article to start to kind of pinpoint what the key benefits of each of the additive technologies are, and how they can start to solve some of these problems.”
He explained that cold spray in particular can “add a lot of resiliency” to the supply chain, and so companies can start to bring that capability in-house and circumvent long lead times for things like casting. Maloney has been involved with additive since 2013, and said there’s still not a solid knowledge foundation in the industry of large metal 3D printing, from DED and cold spray to WAAM and friction stir. The “broader world” still doesn’t fully understand the capabilities of large-format metal 3D printers.

“There’s a bunch of different technologies that do different things, and they can solve a lot of the problems we’re dealing with on a global scale right now, but very specifically in countries that are going to scale up manufacturing,” he concluded. “But it’s going to take investment. It’s going to take investment from a standpoint of working together with the OEMs, with government, with universities, with the commercial world, and starting to put standards in place so we can accelerate what we’re doing. There’s lots of solutions to the problems out there that we have right now, but we just need to put more attention on it.”
Maloney explained that the point of the whitepaper is essentially to say that additive is real. I’d say that SPEE3D’s technology is a pretty good example of this as well.
Subscribe to Our Email Newsletter
Stay up-to-date on all the latest news from the 3D printing industry and receive information and offers from third party vendors.
Print Services
Upload your 3D Models and get them printed quickly and efficiently.
You May Also Like
Metal Powder Supplier Elementum 3D Added to $46B Air Force Contract
Elementum 3D, a Colorado-based developer and supplier of metal powders used in additive manufacturing (AM), announced that the company has been added to the vendors list in the fourth on-ramp...
Ursa Major Lands $28.6M AFRL Deal for 3D Printed Draper Engine Flight Demo
The US Air Force Research Laboratory’s (AFRL’s) Rocket Propulsion Division at Edwards Air Force Base has awarded a $28.6 million contract to Ursa Major for follow-on work related to the...
3D Printing Financials: Rocket Lab’s Record-Breaking Year and Over 20 Launches Coming in 2025
Rocket Lab (Nasdaq: RKLB) closed 2024 with its best year yet. The company launched more rockets, signed more contracts, and expanded deeper into spacecraft and satellite production than ever before....
US Air Force Taps Beehive to Study 3D Printed Jet Engines
Propulsion 3D printing firm Beehive Industries secured a contract from the U.S. Air Force Life Cycle Management Center through SOSSEC. SOSSEC is a company that manages Other Transactions Authority (OTA)...