In February of 2020, the Australian Army announced a $1.5 million investment in Darwin- and Melbourne-based additive manufacturing company SPEE3D. The company worked with previous partners Charles Darwin University (CDU) and the Advanced Manufacturing Alliance (AMA) on developing a 12-month trial program, which was designed to test how feasible it was for Australian soldiers to deploy large-format metal 3D printers—specifically the WarpSPEE3D—in the field and on base.

Australian Army Lance Corporal Sean Barton (R) and Craftsman Naythan Ryan (L) from the 1st Combat Service Support Battalion, prepare the Tactical WarpSPEE3D printer for operation during Exercise Buffalo Run at Mount Bundey Training Area, NT.
Since that time, soldiers from the Australian Army’s 1st Brigade have been learning how to use the technology, first at CDU, and then in a successful rapid deployment of the massive metal WarpSPEE3D printer earlier this summer during a brief field exercise 120 km southeast of Darwin. Now, SPEE3D just announced that the Australian Army has completed a second successful field deployment of its metal AM technology.
“This two-week exercise builds on the success of the first three-day trial in June and was the program’s first big test and further demonstrates the potential for this cutting-edge metal 3D printing technology to be deployed to the field by Defence Forces,” Aerin Langworthy, SPEE3D’s Marketing Manager, told 3DPrint.com in an email.

Australian Army Lance Corporal Sean Barton prepares the WarpSPEE3D printer for part assembly during Exercise Buffalo Run.
The goal of the Australian Army’s investment in SPEE3D’s patented supersonic 3D deposition (SP3D) process, based on cold spray technology, was to, as Langworthy wrote, “significantly increase the availability of unique metal parts to the Army compared to what the regular supply chain can provide.” With two successful field deployment exercises completed in a matter of months, I’d say things are going pretty well.

Australian Army Lance Corporal Sean Barton removes a newly 3D metal printed part from the WarpSPEE3D printer.
Soldiers with the Australian Army’s 1st Combat Service Support Battalion (CSSB)’s larger Brigade Support Group brought the WarpSPEE3D system, which can 3D print parts up to 1 x 0.7 m with its 265 mm high nozzle, to the Mount Bundey Training Area in the Northern Territory (NT) for Exercise Buffalo Run. There, in the humidity and high temperatures, the soldiers worked with the WarpSPEE3D in a two-week-long field exercise to make sure the system has what it takes to 3D print parts in extreme situations.
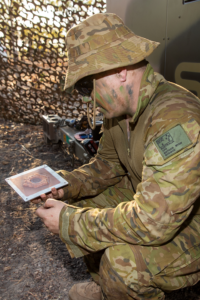
Australian Army Craftsman Naythan Ryan inspects a newly 3D printed part from the WarpSPEE3D printer.
Since its first deployment to Darwin in June, the large-format metal WarpSPEE3D 3D printer has received multiple modifications and upgrades, and this time around, the soldiers moved the system to multiple field locations, sometimes during 37°C days with 80% humidity. Once it was set up each time, they 3D printed and machined metal spare parts for military use.
“This second field deployment proves our technology is a genuine solution for expeditionary metal 3D printing,” SPEE3D’s CEO Byron Kennedy said in a press release. “This two-week trial demonstrates the WarpSPEE3D is a robust workhorse that is capable of printing real parts and solving real problems in the field. It also proves that soldiers can take control of the whole workflow of creating the spare parts they need, from design to printing and post-processing, right here where they need them.”

Australian Army Craftsman Naythan Ryan learns software design techniques from Matthew Harbidge, a 3D printing engineer from SPEE3D.
The WarpSPEE3D printer can fabricate large parts—up to 40 kg in weight—at a rapid rate of 100 grams a minute. Rather than using costly gasses and high-powered lasers, SPEE3D’s metal AM process makes use of kinetic energy and metal cold spray technology to ensure more affordable metal 3D printing, which we now know can be achieved out in the field. This unique method allows users to quickly 3D print industrial-quality parts out of metals, such as aluminum and copper, in only minutes, as opposed to days and even weeks.
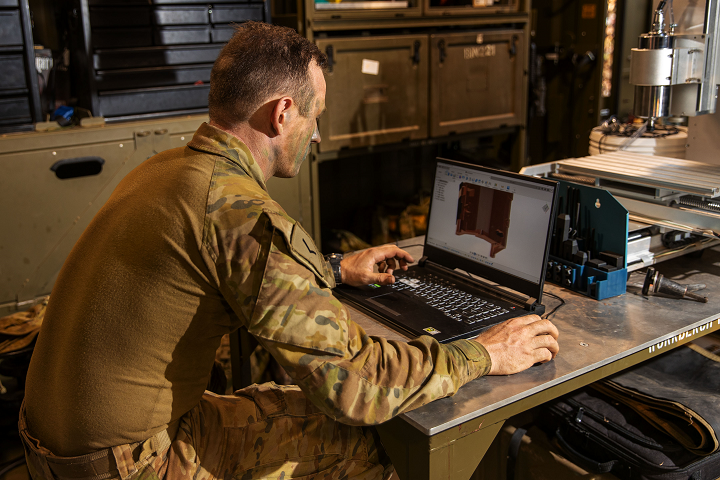
Australian Army Lance Corporal Sean Barton uses engineering software to design spare parts to be 3D printed inside a mobile workshop.
The Australian Army’s trial program with SPEE3D, CDU, and the AMA and is working to make sure that more unique parts are available to its soldiers than they could readily access using the normal supply chain. Using the company’s additive manufacturing technology enables them to do so in a more cost-effective, scalable way.

Australian Army Lance Corporal Sean Barton (L) and Craftsman Naythan Ryan stand with Louis Cianciullo from SPEE3D in front of a mobile 3D printing field workshop.
(Source: SPEE3D / Images: CPL Rodrigo Villablanca)
Subscribe to Our Email Newsletter
Stay up-to-date on all the latest news from the 3D printing industry and receive information and offers from third party vendors.
Print Services
Upload your 3D Models and get them printed quickly and efficiently.
You May Also Like
Havaianas Collaborates with Zellerfeld to Launch 3D Printed Flip-Flops
The shoe of the summer is undoubtedly the flip-flop. Easy on, easy off, your feet won’t get sweaty because there’s not much material, and they’re available in a veritable rainbow...
UCLA Researchers Develop 3D Printed Pen that May Help Detect Parkinson’s Disease
Diagnosing Parkinson’s disease is difficult. Often, early symptoms of the progressive neurological condition may be overlooked, or mistaken for signs of aging. Early diagnosis can help save lives and improve...
Printing Money Episode 30: Q1 2025 Public 3D Printing Earnings Review with Troy Jensen, Cantor Fitzgerald
Printing Money is back with Episode 30, and it’s that quarterly time, so we are happy and thankful to welcome back Troy Jensen (Managing Director, Cantor Fitzgerald) to review the...
Heating Up: 3D Systems’ Scott Green Discusses 3D Printing’s Potential in the Data Center Industry
The relentless rise of NVIDIA, the steadily increasing pledges of major private and public investments in national infrastructure projects around the world, and the general cultural obsession with AI have...