In the first surgery of its kind in the United States, a novel 3D printed PEEK spinal implant has been successfully inserted into a patient. Made by medical tech firm Curiteva using Evonik’s proprietary implant-grade filament based on PEEK (polyetheretherketone), called VESTAKEEP i4 3DF PEEK, the 3D printed, fully interconnected porous structure is the world’s first of its kind for commercial use and will be launched in the U.S. later this year.
News of the successful outcome arrived only weeks after the U.S. Food and Drug Administration (FDA) cleared Curiteva’s novel 3D printed spinal implant for use. According to the FDA 510(k) summary document, the porous PEEK cervical interbody fusion system called Inspire is indicated for intervertebral body fusion of the spine in adult patients. It is “intended for use for anterior cervical interbody fusion in patients with cervical disc degeneration and/or cervical spinal instability.” In addition, during the non-clinical tests, the 3D printed fusion system demonstrated strength and performance substantially equivalent to existing medical devices.
Overall, the combination of Curiteva’s technology and Evonik’s cutting-edge material offer the possibility of enhancing integration and healing for spinal surgery. The Inspire platform used for the first-of-its-kind U.S. surgery was manufactured with Evonik’s VESTAKEEP high-performance polymer on a proprietary, patented 3D printer designed, programmed, and built by Curiteva.
Described by the company as the first 3D fused filament fabrication (FFF) printer to consistently create novel PEEK implant structures, Curiteva’s platform has continuous and contiguous filament deposition and fabrication layers that incorporate engineered (TPMS) diamond structures. The result is an implant structure that provides superior biomechanics and enhanced biological osseointegration (a direct structural and functional connection between the living bone and the surface of the implant).
Commenting on the latest 3D printed spinal development, Alexander Vaccaro, president and orthopedic spine surgeon at Philadelphia’s Rothman Orthopedic Institute, said: “I believe structure drives biology and the lattice PEEK architecture enabled by Curiteva’s 3D printing process represents an exciting advancement in spine, orthopedics, and neurosurgical procedures which involve any type of biologic implant.”
Others, like Kevin Foley, Chairman of Semmes-Murphey Neurologic and Spine Institute, and Randy Dryer a spine surgeon with the Central Texas Spine Institute, highlighted the importance of this interbody implant’s fully interconnected porosity.
Dryer commented: “Interconnected porosity, pore size distribution, and nano-surface architecture are typically hallmarks of the most effective synthetic allografts. I believe this novel implant enhanced with HA Fuse nano-surface topography incorporates those features and presents an optimal environment for osteoprogenitor cells to move throughout the implant, enhancing bone healing (fusion) and reducing the risk of subsidence. I’m excited to offer this to my patients.”
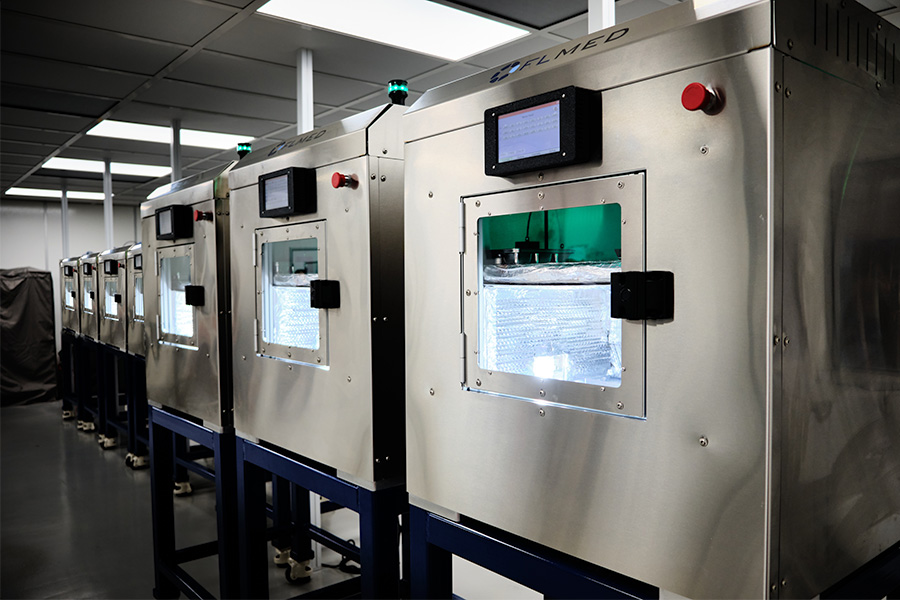
The Inspire HA FUSE interbody platform is manufactured with a proprietary, patented 3D printer. Image courtesy of Curiteva.
With the potential to fit the specific anatomy of a patient’s spine, 3D printed spinal implants have been used in a growing number of surgeries in recent years. These bespoke implants are helping reduce the risk of complications while improving the effectiveness of the surgery.
Furthermore, according to a report by the American Society of Mechanical Engineers (ASME), over 100,000 spinal implants are produced using 3D printing technology each year, and this number is expected to continue to grow.
In 2019, Australian neurosurgeon Ralph Mobbs became the first surgeon in the world to use a 3D printed spinal implant. After removing a tumor in the neck of a patient with chordoma, a rare form of spinal cancer, he inserted a perfectly fitted implant to successfully restore stability to the patient’s spine. The spinal implant cage was 3D printed by researchers at the Royal Melbourne Institute of Technology (RMIT) and the medical device company Anatomics using titanium.
Although the choice of material is a complex decision typically made on a case-by-case basis by the treating physician, what makes Curiteva and Evonik’s device so special is Evonik’s high-performance polymer, which is specially designed for 3D printing and is made with proprietary technology. It’s biocompatible, meaning it is safe for use in the human body and is commonly used in medical implants and devices. VESTAKEEP comes in filament form and meets the stringent requirements of ASTM F2026, which is the standard for PEEK polymers approved for use in surgical implant applications.
As the world’s first 3D-printable filament to meet this requirement for medical use, it is an ideal choice for medical implants and devices. In the past, Evonik collaborated with many companies to create implants.
With Oxford Performance Materials (OPM), Evonik produced spinal implants designed to mimic the natural structure of bone and allow for bone growth through the implant. Evonik has also collaborated with Acuitive Technologies to develop a new generation of orthopedic implants using its VESTAKEEP biomaterial, designed to improve the longevity and performance of joint replacements and other orthopedic devices. The company has also partnered with EOS to develop a new 3D printing technology for the production of customized medical implants. These collaborations showcase the versatility and potential of VESTAKEEP filament and the brand’s commitment to innovation and partnership in the development of new materials and technologies.
Subscribe to Our Email Newsletter
Stay up-to-date on all the latest news from the 3D printing industry and receive information and offers from third party vendors.
You May Also Like
NSF Awards Kentucky $1M for Advanced Manufacturing
The National Science Foundation has awarded a $1 million grant to the University of Louisville for the Advancing Manufacturing and Building Construction Technologies (NSF AMT) project. This initiative is part...
3D Printing News Briefs, May 11, 2024: 3D Printed Stent, Tower, Sculptures, & More
We’re starting off with medical research in today’s 3D Printing News Briefs, as researchers in Korea used CT images and 3D printing to fabricate an educational simulator for a mastoidectomy....
3D Printing Unpeeled: Wind Turbines, Probiotics and Lenses
TPI Composites, ORNL and Ingersoll Rand are working to make wind turbine tooling segments that can be 18.3 meters long. These elements also include resistive wires that help keep the...
Tethon 3D Releases Cost-effective Bioprinter
Tethon 3D, known for its ceramic-loaded DLP materials, custom resins, and DLP 3D printers, has recently released a bioprinter. Vat polymerization printers like DLP systems have been widely used by...