Whenever design artist Nicole Hone brings one of her ideas to life, she creates a world of wonder. Her mesmerizing 4D printed structures are genuinely one of a kind, evoking the pureness of nature and widening the spectrum of what is possible in multi-material printing. In 2019, 3DPrint.com discussed Hone’s achievements in the field, particularly in creating tangible animation through her research project dubbed Hydrophytes. Fast forward to now, and Hone is no longer a graduate student at Victoria University of Wellington in New Zealand but is now a graphic designer for scientific green beauty brand Antipodes and a 3D printing research assistant at her alma mater, working with her mentor and renowned industrial designer Ross Stevens.
In Hone’s latest collaboration with Stevens, they designed and printed objects that could be used to interact with natural elements like water, air, and ice in a playful and emotionally captivating way. The results are visually stunning prints that graciously interact with other elements without the need for heavy manipulation.
Part of MADE (Multi-property Additive-manufacturing Design Experiments) – a research stream at the School of Design Innovation at Victoria University that focuses on multi-material printing – the project is described as Liquid Printing research. It uses Stratasys’ groundbreaking beta software and materials for the J7 and J8 series of PolyJet 3D printers. Integral to the pioneering brand’s portfolio, the J7 and J8 are designed for high-capacity, high-speed, multi-material prints for various design and engineering applications.
For over a decade, MADE research and Stratasys have been working together to expand 3D printing technology by developing new applications and materials for printers. This collaboration recently culminated in MADE becoming part of an exclusive group of researchers with access to the company’s J7 and J8 printers. Then in 2021, Stratasys introduced the PolyJet Research Software package, which offered the opportunity to print with liquid support materials to create soft parts, hydraulics, or fluidic models.

With access to these enriching systems, Stevens and Hone set out to design the new objects for their 2022 project. First, the duo posted three videos of the printed structures in action. The first, Liquid Four Elements, shows an algae-like 4D creation that interacts with four elements (air, smoke, ice, and water). At the same time, Liquid Leaves shows how the 4D printed leaves move when a liquid element is inserted through a tiny tube. Finally, Polyphytes is a beautiful design that secretes various elements with a coordinated grace that is unique to this project.
“The primary intention was to show how these analog physical objects can create a powerful visual display without the need of lengthy digital manipulation, in fact their analog ‘randomness’ exceeding the digital creation potential in intricate detail,” states Made on the Liquid Printing project site.
Since the process is still in beta, the team will not discuss how these structures are being created. Still, they will explain that the new software, printers, and liquid support material enable printing more minor, more reliable, and intricate internal tubes directly into the object. The Liquid Print feature of PolyJet technology allows the creation of these airtight cavities filled with liquid inside an object. Previously these cavities would have been filled with support material and difficult to clean. The final structure design allows for “multidimensional interactions with actors or viewers.”
Hone wrote about her project in Designboom magazine in July 2022, focusing primarily on the development process behind Polyphytes. In the published piece, the designer explains that the basis of this work draws on the connection between 3D printed channels and vascular systems in natural plants. In addition, her research project film (shown below) explores various physical effects created as different substances flow through the Polyphytes: water, air, smoke, icing sugar, bubble mixture, and soap.
“The Polyphytes are procedurally modeled in design software Houdini with a series of internal channels, some as small as 1mm in diameter, then printed on the Stratasys J850 in full-colour rigid photopolymer resin with variable levels of opacity. The enclosed voids are initially filled with PolyJet cleanser liquid which is then drained out in post-production. This allows the channels to become instantly free flowing,” explains Hone in her Designboom article.
The designers stated that although the research is focused on the filmmaking application of the new materials, its potential can be easily expanded to medical and other creative uses. Victoria University and Ross Stevens have a history of research work with the film industry. Stevens even leads a program at the School of Design where he explores 3D and 4D printing for film and coined the term Computer Generated Object (CGO), which follows the use of computer graphics to create images in a broad range of segments, including films and computer animation.
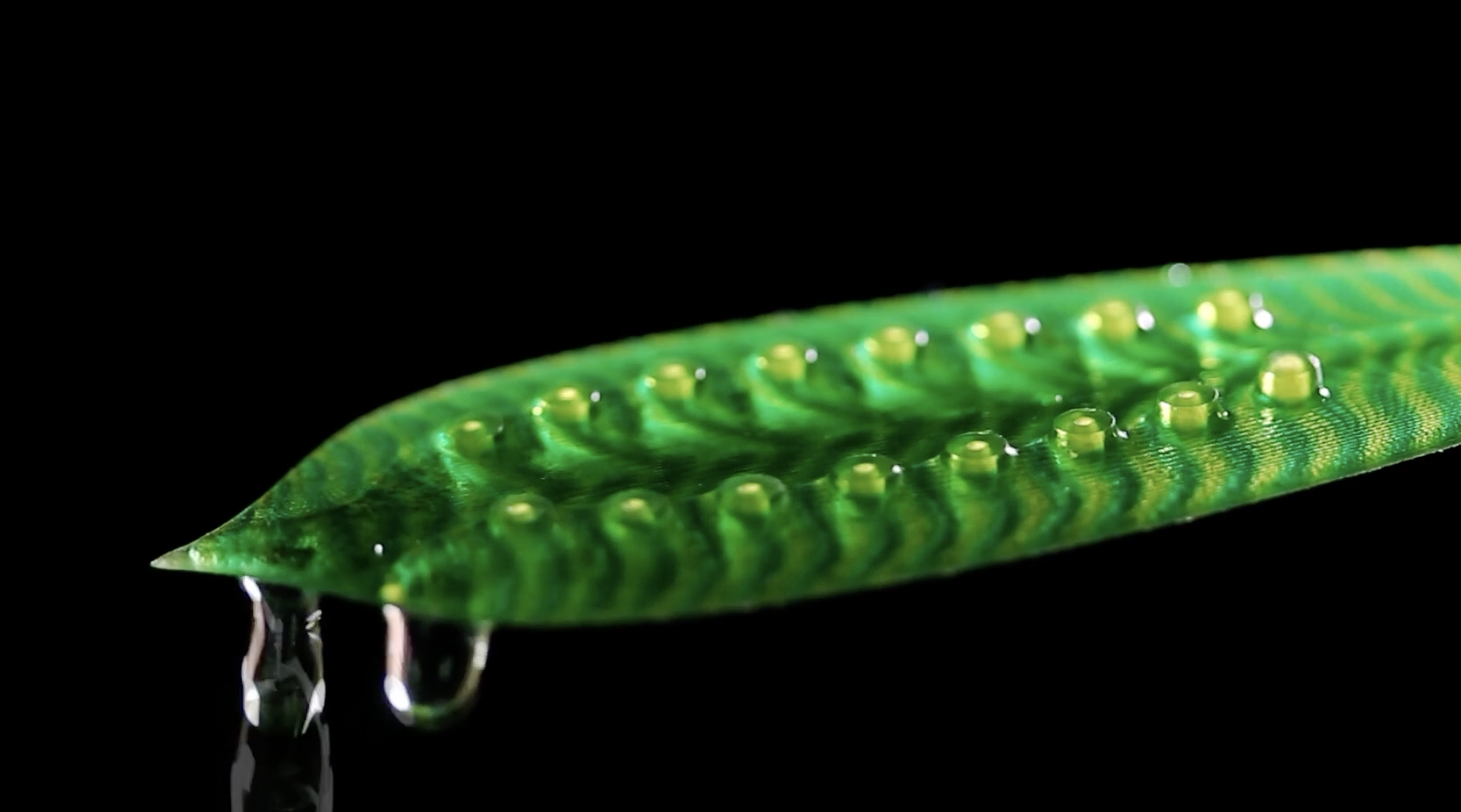
While CGI was a novelty in 2015 when Stevens came up with the Lissom project (which saw 3D printed objects interact with humans in real life and display characteristics of living organisms), the 3D printing enthusiast is onto new developments. One of them is Object Reality (OR), a new term he developed for digital objects taken from the virtual plane and given a life in the physical world, expanding the range of worlds for digital creations.
Stevens, Hone, and other graduate students from the School of Design have been heavily involved with projects at New Zealand’s special effects and prop company Weta Workshop. A lot of the work done at Victoria University has provided a superb basis for projects at the award-winning company. Students have even found jobs, helping create special effects for many beloved shows and movies.
Subscribe to Our Email Newsletter
Stay up-to-date on all the latest news from the 3D printing industry and receive information and offers from third party vendors.
Print Services
Upload your 3D Models and get them printed quickly and efficiently.
You May Also Like
Reinventing Reindustrialization: Why NAVWAR Project Manager Spencer Koroly Invented a Made-in-America 3D Printer
It has become virtually impossible to regularly follow additive manufacturing (AM) industry news and not stumble across the term “defense industrial base” (DIB), a concept encompassing all the many diverse...
Inside The Barnes Global Advisors’ Vision for a Stronger AM Ecosystem
As additive manufacturing (AM) continues to revolutionize the industrial landscape, Pittsburgh-based consultancy The Barnes Global Advisors (TBGA) is helping shape what that future looks like. As the largest independent AM...
Ruggedized: How USMC Innovation Officer Matt Pine Navigates 3D Printing in the Military
Disclaimer: Matt Pine’s views are not the views of the Department of Defense nor the U.S. Marine Corps Throughout this decade thus far, the military’s adoption of additive manufacturing (AM)...
U.S. Congress Calls Out 3D Printing in Proposal for Commercial Reserve Manufacturing Network
Last week, the U.S. House of Representatives’ Appropriations Committee moved the FY 2026 defense bill forward to the House floor. Included in the legislation is a $131 million proposal for...