ASTRO America, the American Lightweight Materials Manufacturing Innovation Institute (ALMII), and the United States Army Combat Capabilities Development Command Ground Vehicle Systems Center (DEVCOM GVSC) have partnered to develop a large metal printer for the U.S. Army’s Rock Island Arsenal. The printer will be made up of MELD’s Friction Stir Additive Manufacturing technique atop an enormous motion stage from Ingersoll Machine Tools.
The aim of this project is to industrialize the large scale manufacturing of military vehicles. Initially the focus will be on underbody hulls, traditionally hard to manufacture. Welds are key points of weakness in the hulls of tanks and armored vehicles. Specifically in Iraq and Afghanistan, US.. ground vehicles were particularly vulnerable to improvised explosive devices (IEDs) that flipped vehicles or penetrated them. It took far too long for the U.S. to up armor Humvees to resist IEDs. It took much longer to develop mine-resistant ambush protected vehicles that were much more resistant to IEDs through V-shaped hulls.
In wars against irregulars, the U.S. military is too slow to upgrade and improve its kit. If the insurgent can adopt new tactics and develop new IEDs quickly, then the U.S. needs to be able to adapt its vehicles quickly. The military is not set up to do this currently, with procurement being sluggish and cutting edge manufacturing technology not deployed in the most effective way possible.
Ingersoll, you may recall, has previously worked with ORNL to make a large-scale polymer 3D printer. This now serves as the basis for the new metal 3D printing system, which relies on Siemens industrial automation components. The MELD head applies heat of 60 to 90 percent of the metal feedstock to lay down tracks of 1 mm thick and 38 mm wide. In this project, an initial machine will make 1 x 1 x 1 m metal parts.
This is similar to Sciaky‘s electron beam process, wire arc additive manufacturing, and other directed energy deposition (DED) technologies. However, later on, the team will develop a machine with a build volume of 10 x 6.5 x 4 meters. This has perhaps been done on large truss structures for specialized military vehicles, but that is not a capability that has not yet been publicly disclosed.
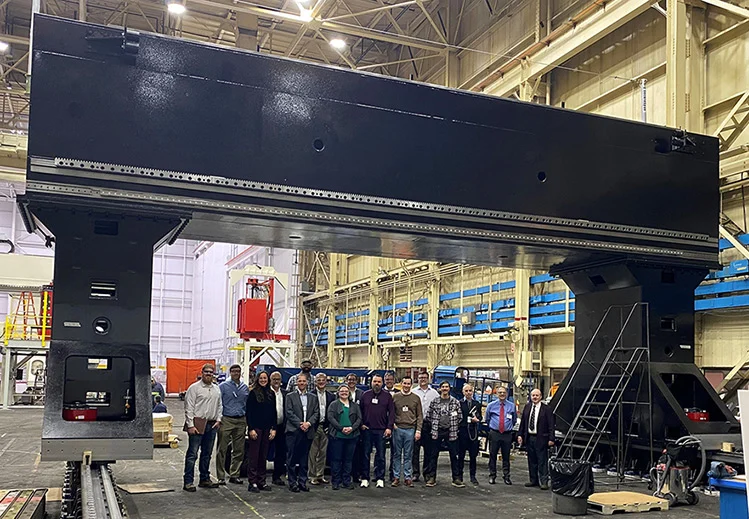
Jointless Hull project team standing under the the full-scale tool being manufactured. Image courtesy of SME.
The printer combines MELD with subtractive machining to finish the part, making it possible to scale up a relatively safe and cheap technology for large components. By relying on MELD, the team avoids having to try to build a football-pitch-sized heated chamber with powder and argon gas, which would be very dangerous if not cost-prohibitive. It also means that the process would work in the open air, without the need to come up with a complex method for heating a part or its surroundings, as some other DED solution would likely require.
Additionally, the team can use cheap feedstock. MELD is also said to achieve good part properties, via good grain structure, part strength and more. Therefore, fully dense parts that suffer less from cracking, porosity, and thermal stress are a possibility with this process.
This project is a huge win for ASTRO America, a brain trust of advanced 3D printing folks that is also involved in the AM Forward program announced by the Biden administration. The team includes LJ Holmes, who was previously at the U.S. Air Force Research Laboratory; Michael Maher who lead a number of key 3D printing projects at the Defense Advanced Research Projects Agency; former Defense Intelligence Agency officer Jason Gorey; and Pentagon manufacturing leading light Neal Orringer. ASTRO board member Jim Williams led Paramount Industries, a very early adopter of 3D printing for defense. The project is also a huge win for MELD, largely overlooked so far by many, but whose efforts in the defense establishment have been consistently nurtured by ASTRO.
This project is a concrete step towards making the U.S. more versatile against threats in the future. By focusing on 3D printing underbody hulls, this collective is pioneering valuable work for the U.S. military.
Subscribe to Our Email Newsletter
Stay up-to-date on all the latest news from the 3D printing industry and receive information and offers from third party vendors.
Print Services
Upload your 3D Models and get them printed quickly and efficiently.
You May Also Like
3D Printing News Briefs, July 2, 2025: Copper Alloys, Defense Manufacturing, & More
We’re starting off with metals in today’s 3D Printing News Briefs, as Farsoon has unveiled a large-scale AM solution for copper alloys, and Meltio used its wire-laser metal solution to...
3DPOD 260: John Hart on VulcanForms, MIT, Desktop Metal and More
John Hart is a Professor at MIT; he´s also the director of the Laboratory for Manufacturing and Productivity as well as the director of the Center for Advanced Production Technologies....
3D Printing News Briefs, June 28, 2025: Defense Accelerator, Surgical Models, & More
In this weekend’s 3D Printing News Briefs, 3YOURMIND was selected to join an EU Defense Accelerator, and PTC has announced model-based definition (MBD) capabilities within Onshape. Finally, a study out...
EOS in India: AM’s Rising Star
EOS is doubling down on India. With a growing base of aerospace startups, new government policies, and a massive engineering workforce, India is quickly becoming one of the most important...