In the most recent decade of the 3D printing industry’s history, the bioprinting sector has gone through a somewhat repulsive transition from human organs and tissue to animal meat. At the same time, in addition to printed flesh, there have also been many companies exploring and even commercializing printed plant-based alternative meat.
Yet, aside from this, there haven’t been many other examples of 3D printing with plants, even though there certainly seems like there should be demand for it. For instance, it’s interesting that, although 3D printed wood derived from recycled lumber waste has gained steam, bioprinted wood — as far as I can tell — has been comparatively unexplored, with some exceptions related to cellulose.
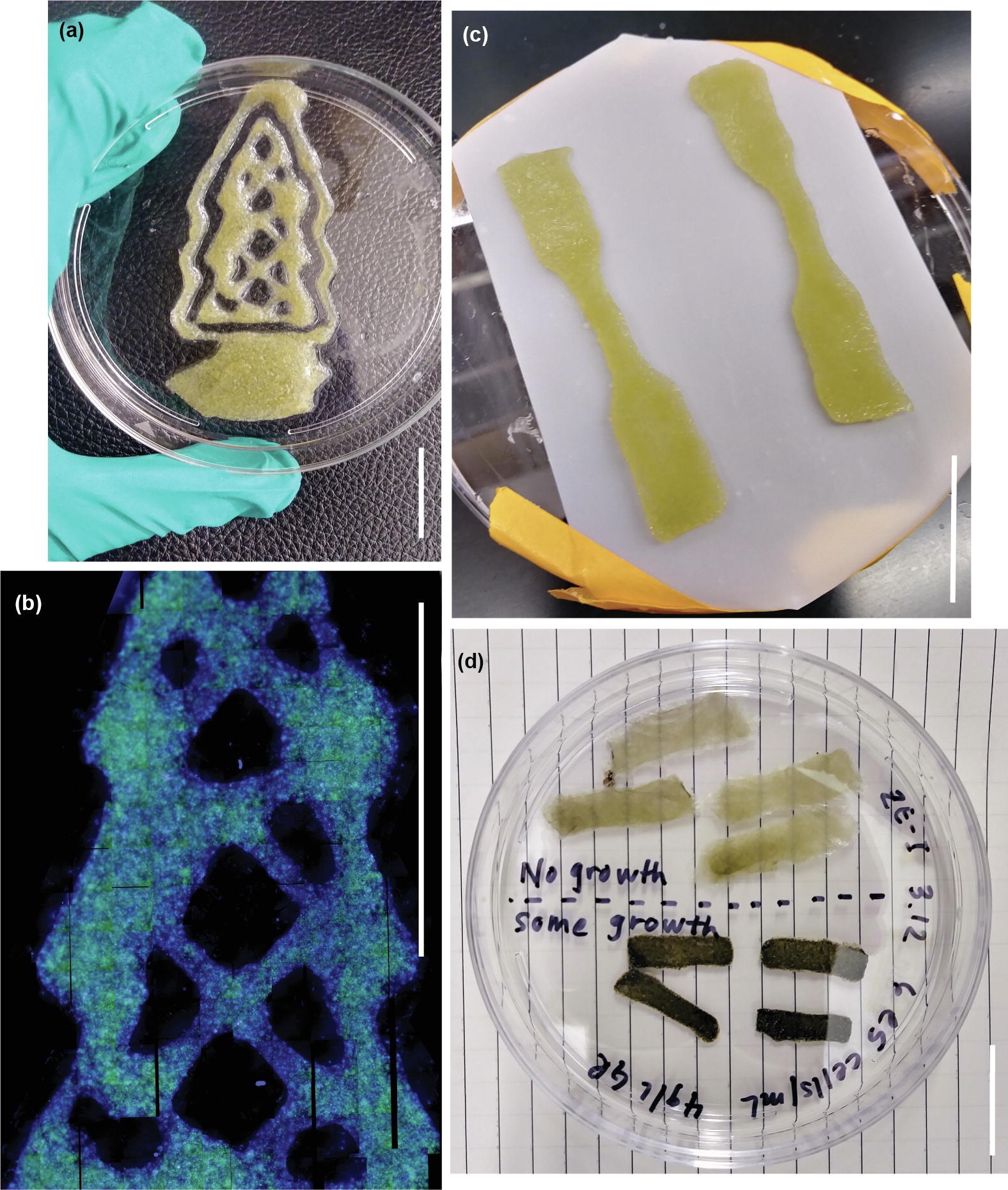
This is what makes a recently completed study by a team at MIT so intriguing. Published in the journal Materials Today, the study concerns “…novel, 3D-printed, tunable, lab-grown plant materials generated from Zinnia elegans cell cultures”. While the common zinnia is, of course, a flower and not a tree, it is the researchers’ stated interest to use the data as a springboard into the study of wood-forming plants. Moreover, the study’s lead author, Ashley Beckwith, a recent Charles Stark Draper Laboratory Scholar and PhD graduate at MIT, is also the CEO of a bioprinted wood startup, FORAY bioscience, which she founded in 2021.
In the paper published in Materials Today, Beckwith et al. conclude, “In a woody species, one could similarly employ a nutrient-rich, structured gel culture environment to facilitate cell growth and proliferation and…to encourage morphological development and differentiation into vascular cell types. The resulting materials would exhibit wood-like attributes and could likewise be grown in a tree-free manner in defined shapes and with tunable properties.”
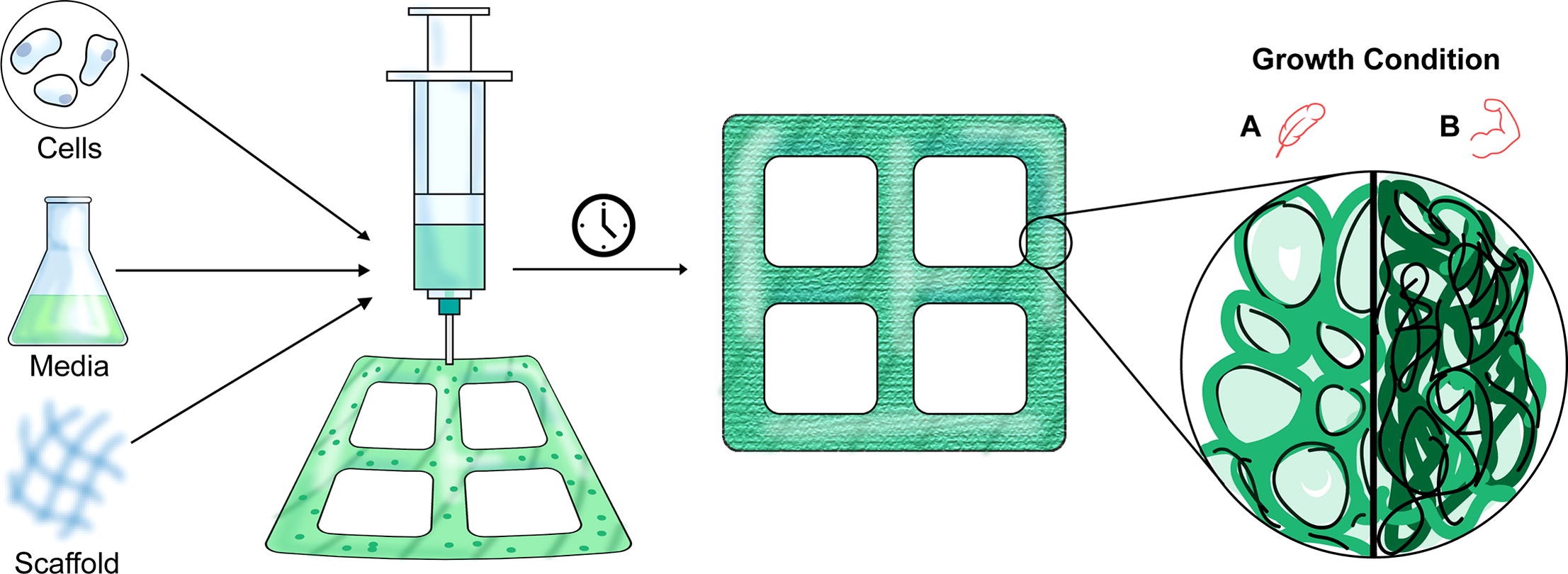
For the present project, cells were extracted from zinnia leaves, then soaked in a liquid solution for two days. Next, the cells were concentrated into a gel solution composed of various combinations of nutrients and hormones, depending on how the team wanted to “tune” the cells’ properties during growth. The concentrations of plant cells and grow gel were then extruded into petri dishes by a 3D Cultures’ Tissue Scribe bioprinter, after which they were, finally, left in a dark, temperature-controlled (at about 72 degrees Fahrenheit) lab for three months. At intermittent times during those three months, the researchers also added more solution to the petri dishes, as well as releasing gases from them for brief intervals as needed.
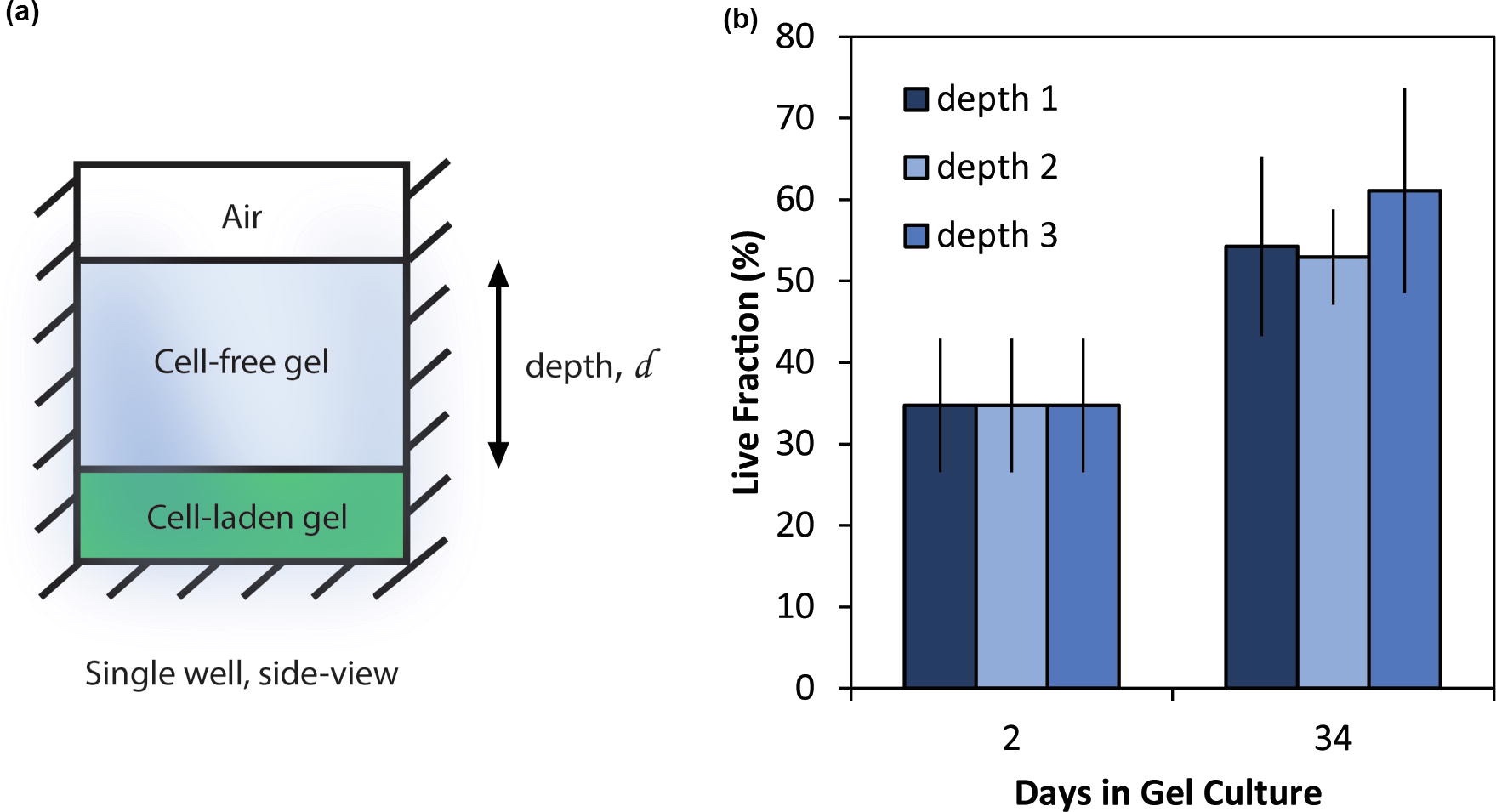
Since the study utilized bioprinting, “…required nutrients and hormones are incorporated within the scaffold itself, [and so] this fully contained setup requires little intervention after deposition.” Moreover, use of a bioprinter made it possible to control the shape of the gel solutions in the petri dishes, which adds to the potential usefulness of deploying the method for lab-based wood production. And, perhaps most impressively of all, the process can produce a mature plant “two orders of magnitude”, or a hundred times faster, than normal growing methods.
Beyond the advantages of conservation and speed, I think there’s much to be said in favor of the concept of “growing” plants in the dark. In terms of alternatives to conventional industrial agriculture moves towards indoor farming, are often seen as more sustainable, but this isn’t necessarily the case. Indoor farming uses enormous amounts of electricity: indoor growing if commercial cannabis, for instance, is already estimated to be responsible for 1% of U.S. electricity use. Adding additional crops to that list doesn’t seem feasible unless a significant dent can be made in the carbon footprint of indoor grow systems. Bioprinting of plants, therefore, could be another interesting technique to have in the toolkit as humans start to address the need to slow the further growth of industrial farming.
Images courtesy of Beckwith et al.
Subscribe to Our Email Newsletter
Stay up-to-date on all the latest news from the 3D printing industry and receive information and offers from third party vendors.
Print Services
Upload your 3D Models and get them printed quickly and efficiently.
You May Also Like
Could 3D Printing for Biocomputing Make Wetware Aware?
As an AI arms race consumes ever more electricity, and every ChatGPT search query costs $0.36, the search for new ways of computing has intensified. One answer could be in better...
Bambu Lab Launches Software to Manage 3D Printer Fleets—No Cloud Needed
Bambu Lab has introduced a new software tool, Bambu Farm Manager, designed to help users manage large fleets of 3D printers over a local network, without relying on the cloud....
Consolidation in AM: How 2025 Is Shaping the Industry’s New Normal
The first half of 2025 has been marked by a clear shift in the additive manufacturing (AM) industry. Companies are no longer just focused on developing new tech by themselves....
3D Printing News Briefs, July 2, 2025: Copper Alloys, Defense Manufacturing, & More
We’re starting off with metals in today’s 3D Printing News Briefs, as Farsoon has unveiled a large-scale AM solution for copper alloys, and Meltio used its wire-laser metal solution to...