Stratasys (NASDAQ: SSYS) is already in the business of supplying the largest number of 3D printed polymer aerospace parts. Now, the company has qualified yet another polymer for 3D printing for aerospace applications. In conjunction with Lockheed Martin (NYSE: LMT) and Metropolitan State University of Denver, the company has released the baseline material qualification data for its Antero 840CN03 filament, used to 3D print parts for the Orion spacecraft.
“We want to demonstrate a new model for how industry, manufacturers and academia can collaborate to gather and release material qualification data that helps accelerate the adoption of additive manufacturing across the aerospace industry,” said Foster Ferguson, Director of Aerospace for Stratasys.
Antero 840CN03 is a PEKK-derived composite thermoplastic with electrostatic discharge (ESD) qualities necessary for use in space applications. The material meets ESD and NASA outgassing requirements and exceeds flame, smoke, and toxicity (FST) characteristics required for aviation. Baseline data was collected by 3D printing over 280 test coupons made from Antero 850CN03 on Stratasys Fortus F900 3D printers at Lockheed Martin facilities in Littleton, Colo., and Stratasys Direct Manufacturing in Belton, Texas. These tests demonstrated tensile strength properties and confirmed the performance of the polymer shown in academic studies. Additional testing will examine other properties to further inform the work of design engineers for other uses.
“We are continually looking for ways to drive innovation for flight-qualified materials and additive manufacturing is key to that endeavor,” said Cris Robertson, Associate Manager of Advanced Manufacturing at Lockheed Martin Space. “Through our collaboration with Stratasys and MSU Denver, we have collected the data necessary to qualify Antero 840CN03 for flight parts and we are now able to expand our use of the material beyond our initial applications on the Orion vehicle.”
“These types of research and development collaborations with leading companies like Stratasys and Lockheed Martin enable our students to be well prepared to help their future aerospace employers with adopting the latest technology in the industry,” said Mark Yoss, Director of the Advanced Manufacturing Sciences Institute at MSU Denver. “By publishing this material qualification data, we can help move the aerospace industry forward by establishing more standards in additive manufacturing.”
In 2018, Stratasys and Lockheed Martin published allowable data for SABIC ULTEM 9085 resin 3D printed using a Fortus 900mc 3D printer. This was only one development in the companies’ partnership, which also included 3D printing over 200 parts for the Orion spacecraft. Stratasys has also qualified another PEKK material, Antero 800NA, for use by Boeing. The public release of the material qualification data is meant to expand the adoption of the material in aerospace applications.
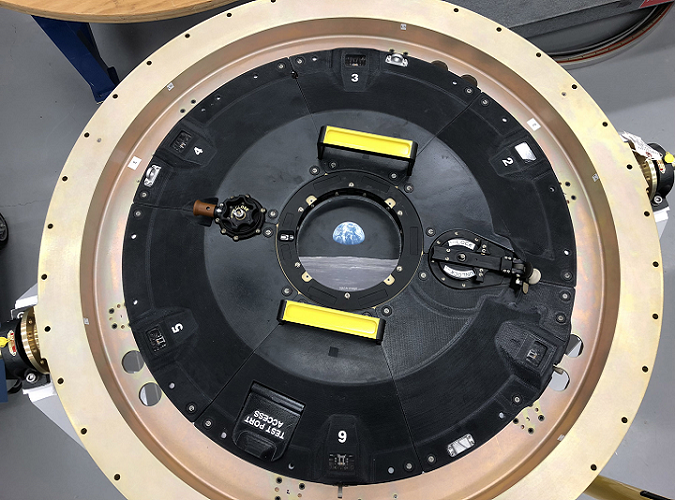
The Orion spacecraft leverages a variant of new Stratasys Antero 800NA to build an intricately-connected 3D printed docking hatch door.
By qualifying a growing range of materials for such high-performance use-cases, Stratasys can also attempt to maintain an edge over the new generation printer manufacturers looking to compete with their own industrial extrusion 3D printers. This includes firms like Roboze and 3DGence, who have developed cost-competitive thermoplastic deposition machines with the ability to 3D print high-temperature materials, including PEKK. As it stands, Stratasys is still much larger with more resources, perhaps allowing it to qualify these polymers at a faster rate than newcomers may be able to.
The full data report is now available to the public online, with more characterization to take place with future testing. Stratasys and Lockheed Martin will also showcase the material at this year’s Space Symposium in Colorado Springs, Colo.
Subscribe to Our Email Newsletter
Stay up-to-date on all the latest news from the 3D printing industry and receive information and offers from third party vendors.
Print Services
Upload your 3D Models and get them printed quickly and efficiently.
You May Also Like
Heating Up: 3D Systems’ Scott Green Discusses 3D Printing’s Potential in the Data Center Industry
The relentless rise of NVIDIA, the steadily increasing pledges of major private and public investments in national infrastructure projects around the world, and the general cultural obsession with AI have...
Formlabs Teams Up with DMG MORI in Japan
In late June, Nick Graham, Chief Revenue Officer at Formlabs, announced on LinkedIn that the company had partnered with DMG MORI, one of the world’s leading machine tool companies, to...
EOS in India: AM’s Rising Star
EOS is doubling down on India. With a growing base of aerospace startups, new government policies, and a massive engineering workforce, India is quickly becoming one of the most important...
3D Printing News Briefs, June 25, 2025: R&D Materials, 3D Printed Veneers, & More
In today’s 3D Printing News Briefs, 3DXTECH has launched a program that gives customers early access to experimental materials, and the first Lithoz CeraFab Multi 2M30 in the Czech Republic...