Volunteers and designers from non-profit organization LifeNabled and engineering software startup nTopology have been busy helping amputees in northern Guatemala. The team, led by LifeNabled co-founder Brent Wright, created a fully digital workflow to produce custom 3D printed prosthetic sockets with flexible inner liners that provide stability to amputees. Now, 35 patients in the jungle of Guatemala are walking on the world’s most advanced prosthetic and orthotic devices.
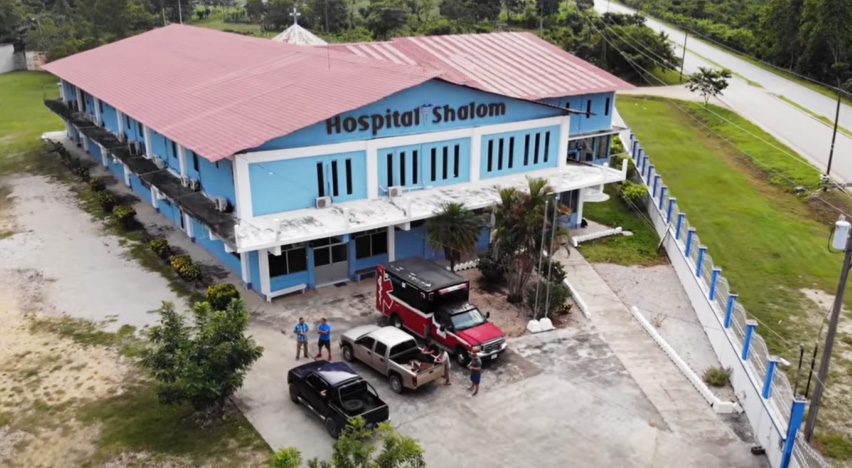
Hospital Shalom is the only facility that provides prosthetics care to patients of the Petén region in Guatemala.
There are roughly 57.7 million people worldwide living with limb amputation due to traumatic causes. Over 60% of them have suffered lower limb amputation, including below and above the knee. However, in developing nations, very few have access to quality prostheses. Even if they do, an amputee will often need a new device in as little as one year due to changes in the residual limb volume. For this reason, organizations around the world are continuously working to address this need as quickly as possible.
With his wife and co-founder Meredith Wright, Brent hosts bi-yearly clinics that have treated hundreds of patients in the poorest regions of Guatemala for over 15 years. For their most recent clinic, the team stopped using time-consuming, traditional fabrication methods to create their prosthetics and pivoted to a digital approach by partnering with the generative design 3D software company.
Using patient scan data as input, they automatically generated the prosthetic socket designs in nTopology, and 3D printed them in durable TPU using HP’s Multi Jet Fusion (MJF) technology. The new digital workflow saved the team more than three days of laborious work, bypassing the expertise-intensive and arduous traditional manufacturing steps and focusing on making the digital process as scalable and cost-effective as possible.
The hard work of Wright’s organization and nTopology is changing people’s lives for the better. Like many developing countries in Central America, Guatemala has severe healthcare limitations. Compared to the US and other high-income nations, physician density is relatively low, with 0.93 physicians per 1,000 people, failing to achieve adequate coverage rates for primary healthcare. That means more than six million people in Guatemala (roughly 35% of the population) lack access to essential health services, including amputees.
Aid organizations improve human resources by supporting and strengthening the health system. For Wright, that means investing in people on the ground, in their home countries, and teaching them how to evaluate patients and then fit the patient devices when they come in. But his NGO goes one step further and combines humanitarian labor with technology to “unlock true access to prostheses worldwide.”
Wright, a prosthetist and orthotist who works for EastPoint Prosthetics and Additive America, told 3DPrint.com that LifeNabled partnered with nTopology for this particular application due to its computing speed. “Literally within just a few minutes, I have mesh files ready to roll without really any user input aside from swapping out the meshes that I need. Most of the other programs required in and out and then a lot of computing power, which was not as fast as what nTopology offered. The bottom line is speed: nTopology excelled in the speed at which it produced the sockets.”
The process begins by taking 3D scans of the patients. In just two days, two LifeNabled volunteers were able to evaluate 35 amputees. Next, the engineering team designed each custom prosthetic and manufactured the sockets using HP’s MJF 3D printing technology. Within a month, LifeNabled delivered the prosthetics and fit them to the patients. Moreover, the team achieved this result at a fraction of the effort compared to previous clinics.

Digital fabrication of prostheses starts with a 3D scan of the patient (left), and then the custom socket and inner lining can be 3D printed (right).
Off-the-shelf linings are expensive and have a limited lifetime of only three to six months in the tropical climates of Guatemala. For the local people who live on $2 or $3 a day, paying more than $160 for a traditional gel-like inner liner is impossible. Thereby, the team opted for a washable and low-cost cloth sock to ensure good hygiene and a prosthesis socket with a flexible 3D printed foam liner for comfort. nTopology closely controlled lattice parameters, like beam thickness and porosity, and achieved the desired cushioning effect.
Without nTopology, applying the 3D printed foam to 35 custom socket designs would have been challenging, the company explained, as traditional fabrication of prostheses is a strenuous process. In addition, legacy software would often crash or take hours to generate a single result, but with nTopology’s reusable workflows, going from 3D scan to manufacturing-ready STL files was simple, repeatable, and semi-automated, and saved LifeNabled more than a day of computational processing.
Wright’s vision is to fully digitize the design and manufacturing steps, which are the most expertise-demanding phases of the prostheses fabrication process. Over the next five years, Wright and his team will continue investing in technology and automation and finding budget-friendly solutions for scanning and creating a global network of prosthetic device providers for developing nations.
“I know Hewlett-Packard essentially has a whole worldwide network. There are HP Multi Jet Fusion machines in places that you would never expect. In that, I believe there is always room to add a prosthesis of sorts into the build for a very low cost or no-cost solution,” Wright said. “My hope and dream would be to harness those relationships with those who have powder-based fusion machines, specifically HP Multi Jet Fusions, and as there is capacity, adding sockets and prosthetic devices to those machines and then getting them to patients in need.”
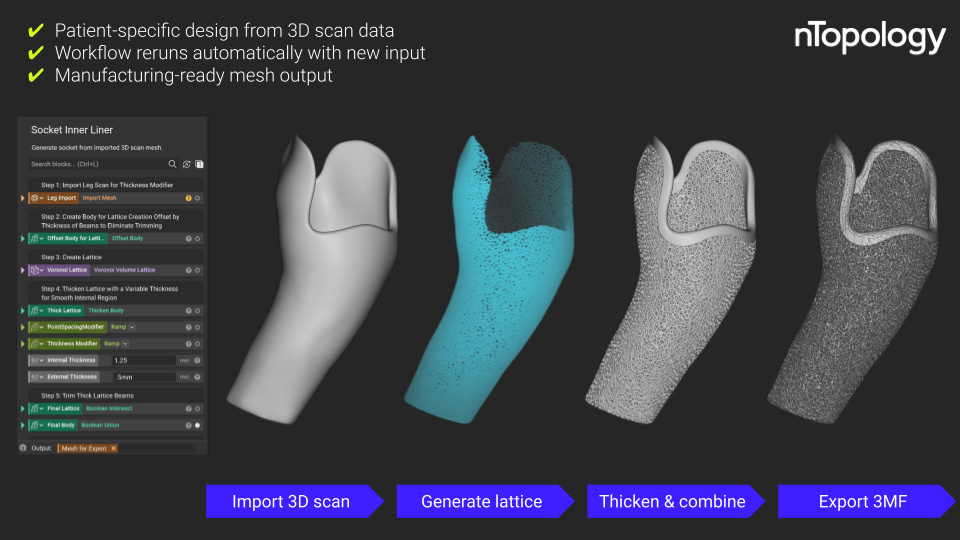
Overview of the design process in nTopology: from importing a 3D scan mesh to exporting a manufacturing-ready mesh file.
Multiple industrial-grade 3D printing systems located worldwide—even in developing countries—could be leveraged to manufacture the needed prosthetic devices. For a better idea of how this would work, Wright explained that if someone in, for example, Turkey, is looking for a prosthesis printed with an MJF system, but there is nobody available to do it, they could contact LifeEnabled. The organization would then run it through nTopology, and engineers would create a design file. Afterward, LifeEnabled would contact a Turkey company with MJF platforms for 3D printing and send it on its way to be distributed.
“It’s a dream, but I think it’s totally possible,” he commented.
With the average cost of a full prosthetic leg ranging from $5,000 to $70,000, without donated parts, Wright’s idea seems right on point. Moreover, through digital manufacturing and generative design tools, LifeNabled’s process can be replicated in other parts of the world to significantly improve the quality of life of amputees who don’t have the means to afford prosthetic care.
(Images courtesy of LifeNabled)
Subscribe to Our Email Newsletter
Stay up-to-date on all the latest news from the 3D printing industry and receive information and offers from third party vendors.
Print Services
Upload your 3D Models and get them printed quickly and efficiently.
You May Also Like
Metal Powder Supplier Elementum 3D Added to $46B Air Force Contract
Elementum 3D, a Colorado-based developer and supplier of metal powders used in additive manufacturing (AM), announced that the company has been added to the vendors list in the fourth on-ramp...
Ursa Major Lands $28.6M AFRL Deal for 3D Printed Draper Engine Flight Demo
The US Air Force Research Laboratory’s (AFRL’s) Rocket Propulsion Division at Edwards Air Force Base has awarded a $28.6 million contract to Ursa Major for follow-on work related to the...
3D Printing Financials: Rocket Lab’s Record-Breaking Year and Over 20 Launches Coming in 2025
Rocket Lab (Nasdaq: RKLB) closed 2024 with its best year yet. The company launched more rockets, signed more contracts, and expanded deeper into spacecraft and satellite production than ever before....
US Air Force Taps Beehive to Study 3D Printed Jet Engines
Propulsion 3D printing firm Beehive Industries secured a contract from the U.S. Air Force Life Cycle Management Center through SOSSEC. SOSSEC is a company that manages Other Transactions Authority (OTA)...