We’ve seen handheld bioprinters used to draw new cells onto bone and print skin to help heal burn wounds, and now a pair of researchers from China’s Tsinghua University have developed a bioprinting robot that can treat gastric wounds from inside the body itself. Professor Tao Xu and PhD student Wenxiang Zhao worked together to create a prototype robot that is small enough to be endoscopically inserted into a patient’s stomach for treatment. They published a paper on their work, titled “Preliminary engineering for in situ in vivo bioprinting: a novel micro bioprinting platform for in situ in vivo bioprinting at a gastric wound site,” in the Biofabrication journal.
If they are not treated, open wounds on a person’s stomach wall can become very serious, and even require surgery.
“Gastric wall injury is one of the most common diseases in digestive tract and about 12% of the world’s population suffer from it to varying degrees, according to a research of Lancet [13]. Recent studies have showed that the main reason for common gastric wall injury is H. pylori inside digestive tract weakened protective effects of mucosae. And the mainstream treatment methods includes conservative medication and surgical treatments,” Professor Xu and Zhao wrote in their paper.
“At present, little research has been carried out on the application of bioprinting techniques to tissue repair in gastric tract, yet this is a field worth exploring. To carry out bioprinting in situ in vivo, the first step is to develop an available micro bioprinter, based on which we can continue subsequent research on creating tissues with bioactivities. This paper is the first step of the research on a new approach aiming to repair tissues through in situ in vivo bioprinting.”
Together, they created a micro bioprinting platform that’s small enough to be installed on an endoscope, and because it can actually fold down into a skinnier version of itself while being inserted and then open up once inside, the platform is able to reach the specific site in order to complete in situ 3D printing to treat the wound.
They explained in their paper that “the projection of the platform’s working space should be larger than the platform’s cross-sectional area,” so it’s able to have as much workspace as possible while still fitting in the smallest space it can. That’s why the researchers chose a Delta robot, which means that its head is made up of a moving platform and a fixed, rigid base, and surrounded by three arms, or kinematic chains, that move independently of each other.
“Each kinematic chain is composed of a driving arm and a passive arm, which are connected by spherical hinge. The latter one consists of a parallelogram closed loop to keep the moving platform moving horizontally,” they explained. “However, a spherical hinge is too difficult to process in such a micro platform so we used PC-MEMS techniques to create two perpendicular revolving joints composed of two rigid layers and one flexible layer with offset axes of rotation to replace the original spherical hinge in the kinematic chains.”
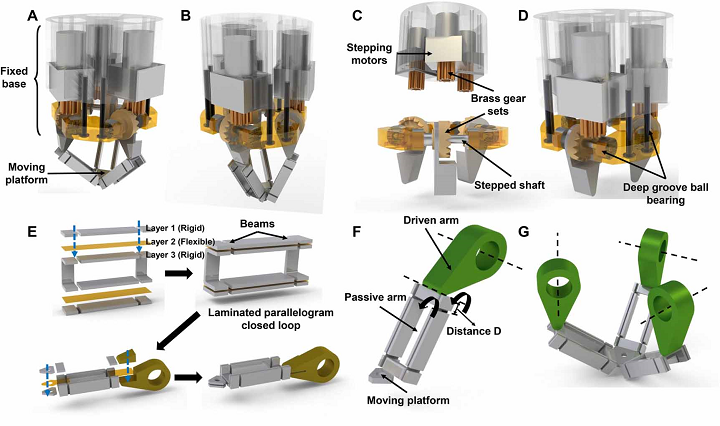
Fabrication of the bioprinting platform. (A) Delta robot in normal status. (B) Delta robot in fold status. (C), (D) Fabrication of fixed base of bioprinting platform. (E) Lamination of kinematic chain using the PC-MEMS techniques. (F) Kinematic chain. (G) Moving platform with kinematic chains.
Once the platform has folded itself down to get inside the body, its three arms then guide a tube that extrudes two different kinds of hydrogel bioink in two separate layers to build a scaffold which covers the gastric wound. One bioink contains human gastric epithelial cells, and the other one has human gastric smooth muscle cells.
In order to test how well the platform completes the bioprinting task, Professor Xu and Zhao determined that it needed to “perform the basic trajectories necessary in tissue scaffolds,” and developed a stomach model for their experiments. They used Materialise Mimics software to reconstruct the CT data of a human stomach, and stereolithography technology to print the model out of transparent resin, along with a curved pipe that would mimic an endoscope. The pair fixed their bioprinting platform on the pipe, and installed a 23 gauge needle in it, which was connected to a syringe through a polytetrafluoroethylene (PTFE) tube in order to reduce friction during the actual extrusion process.
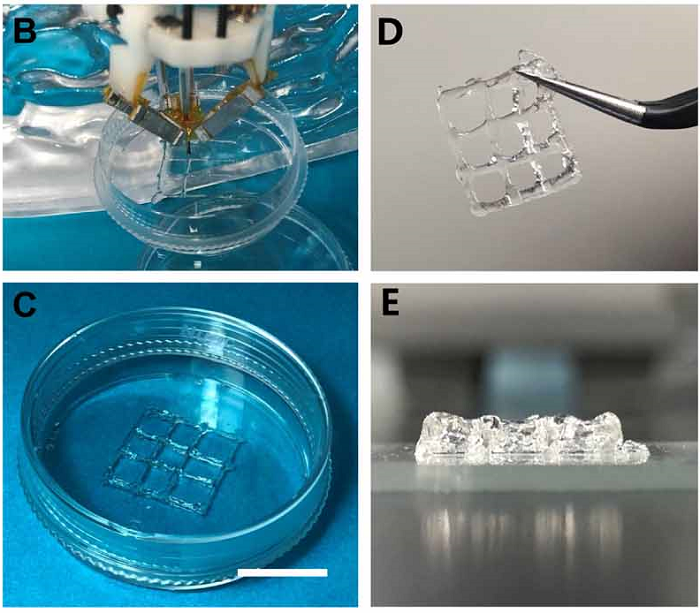
Bioprinting experiment equipment. (B) The process of in situ in vivo bioprinting. (C) The printed 2-layer tissue scaffolds consisting of GES-1 cells and HGSMCs before cross-linking. (Scale bar: 1 cm). (D, E) The printed 8-layer scaffold with favorable mechanical properties.
“We tested the system in two ways. First, with a biological model of a human stomach and an endoscope, to mimic the insertion and printing operation elements of the process. Second, we carried out a bioprinting test in a cell culture dish to test how effective the device was at bioprinting viable cells and repairing wounds,” Zhao explained.
“A 10-day cell culture showed that printed cells remained at a high viability and a steady proliferation, which indicated good biological function of the cells in printed tissue scaffolds.”
The two-layer structure was stable, with smooth fibers, and the eight-layer scaffold had clear contours and high shape fidelity, while being small enough to be picked up using tweezers. While their experiment was successful, Professor Zu said that they still need to refine the system, such as making the robot’s 3D printing platform even smaller and further improving the bioinks.
“The corresponding endoscope and other parts such as the detecting system will also be designed and integrated to make in situ in vivo bioprinting a reality,” they concluded.
(Source: New Atlas / Images: Tsinghua University)
Subscribe to Our Email Newsletter
Stay up-to-date on all the latest news from the 3D printing industry and receive information and offers from third party vendors.
Print Services
Upload your 3D Models and get them printed quickly and efficiently.
You May Also Like
Making 3D Printing Personal: How Faraz Faruqi Is Rethinking Digital Design at MIT CSAIL
What if your 3D printer could think more like an intelligent assistant, able to reason through a design idea, ask questions, and deliver something that works exactly the way the...
Reinventing Reindustrialization: Why NAVWAR Project Manager Spencer Koroly Invented a Made-in-America 3D Printer
It has become virtually impossible to regularly follow additive manufacturing (AM) industry news and not stumble across the term “defense industrial base” (DIB), a concept encompassing all the many diverse...
Heating Up: 3D Systems’ Scott Green Discusses 3D Printing’s Potential in the Data Center Industry
The relentless rise of NVIDIA, the steadily increasing pledges of major private and public investments in national infrastructure projects around the world, and the general cultural obsession with AI have...
Formlabs Teams Up with DMG MORI in Japan
In late June, Nick Graham, Chief Revenue Officer at Formlabs, announced on LinkedIn that the company had partnered with DMG MORI, one of the world’s leading machine tool companies, to...