Yi Wei Daniel Tay of the School of Mechanical and Aerospace Engineering at Nanyang Technological University recently submitted a thesis, ‘Large scale 3D concrete printing : process and materials properties,’ exploring the potential for more progressive techniques and materials in the construction industry.
This research examines the need for good flow in concrete ink, along with challenges in finding the correct printing parameters for performance and quality products. Ultimately, pumpability, layer adhesiveness, and buildability are critical elements as well, with all these features being explored during the fabrication of a large-scale sample—along with the option of refining the need for formwork via 3D printing.
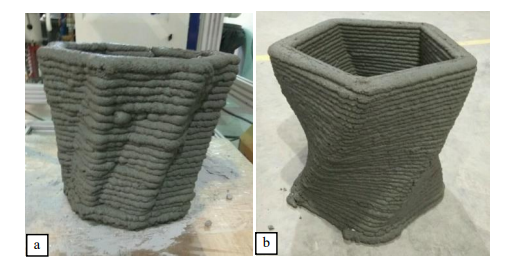
(a) Poor balance between travel speed and flow rate (b) proper balance
between travel speed and flow rate
Not only is pouring concrete in formworks for temporary support a labor intensive process, it is also more expensive; in fact, as Tay notes, formwork comprises 40 to 60 percent of the cost of a concrete frame, and ten percent of the overall building expenses.
Tay realizes the benefits of 3D printing in construction:
- Shorter building times
- Cheaper construction
- Less human labor
- Reduced material waste
- Greater latitude in design
- Better potential for integration of functionality
“All these reductions are eventually translated to cost-saving, which compel the exploration of using 3D printing in construction for structural with customized complex geometries,” stated Tay.
Worldwide, 3D printing with concrete is garnering interest—leading to a variety of different projects and studies, from reinforcement of concrete walls to developing and using fiber additives, to experimenting with progressive new techniques. Methods for 3D printing with concrete continue to grow, to include:
- Binder jetting
- Material deposition method
- Contour crafting
- Curved-bed printing
- Mesh mold
“3D concrete printing can be a complicated process, especially if the requirements are not clear. The printing parameters and material properties should be tailored to fulfil the project requirements such as cost and duration,” explained Tay. “With the printing path and speed established, the vertical loading stress can be determined. This vertical stress can be compared with the yield stress of the mixture to determine if it is suitable for printing.
The use of suitable materials is critical, as researchers continually seeking more sustainable options, to include:
- High volume fly ash concrete
- Geopolymers
- Recycled glass aggregates
For this study, graded concrete material was created by varying the printing parameters. As the effects were studied, Tay discovered that both flow and travel speed have enormous impact on filament and dimensions.
“The main advantage of having a functionally graded structure is the reduction in material and the decrease in printing speed as the support structure region uses less material and help to reduce printing time,” concludes the author. “This shows that through topology optimization, this functionally graded material can be manufactured to produce a structure that has improved performance compared to the un-optimized structure.”
“The future of construction is most likely to be an integrated process that allows the organization to take advantage of both conventional and additive manufacturing technologies. With rapid urbanization in many developing countries, there is an urgent need to come up with clever ideas that optimize the sustainable performance of the buildings that we live and work in. Regulators also play a significant role in sustainable construction by creating the right incentives for companies that choose to build in a sustainable way.
What do you think of this news? Let us know your thoughts! Join the discussion of this and other 3D printing topics at 3DPrintBoard.com.
[Source / Images: ‘Large scale 3D concrete printing : process and materials properties’]Subscribe to Our Email Newsletter
Stay up-to-date on all the latest news from the 3D printing industry and receive information and offers from third party vendors.
Print Services
Upload your 3D Models and get them printed quickly and efficiently.
You May Also Like
3D Printing News Briefs, July 2, 2025: Copper Alloys, Defense Manufacturing, & More
We’re starting off with metals in today’s 3D Printing News Briefs, as Farsoon has unveiled a large-scale AM solution for copper alloys, and Meltio used its wire-laser metal solution to...
3DPOD 260: John Hart on VulcanForms, MIT, Desktop Metal and More
John Hart is a Professor at MIT; he´s also the director of the Laboratory for Manufacturing and Productivity as well as the director of the Center for Advanced Production Technologies....
3D Printing News Briefs, June 28, 2025: Defense Accelerator, Surgical Models, & More
In this weekend’s 3D Printing News Briefs, 3YOURMIND was selected to join an EU Defense Accelerator, and PTC has announced model-based definition (MBD) capabilities within Onshape. Finally, a study out...
EOS in India: AM’s Rising Star
EOS is doubling down on India. With a growing base of aerospace startups, new government policies, and a massive engineering workforce, India is quickly becoming one of the most important...