Companies, organizations and individuals continue to attempt to lend support to the COVID-19 pandemic supply effort. We will be providing regular updates about these initiatives where necessary in an attempt to ensure that the 3D printing community is aware of what is being done, what can be done and what shouldn’t be done to provide coronavirus aid.
The University of Michigan and Michigan Medicine have designed a 3D printable, personalized ventilator splitting device which makes it possible to tailor air pressure to multiple patients from a single ventilator unit. The VentMI device helps to address the most crucial issue with the vent splitters we have seen designed in response to the COVID-19 pandemic, the fact that each patient needs specific rates of pressure to perform effective treatment and not further damage their respiratory systems.
Inspired by scuba tank regulators, the VentMI tool controls compressed air pressure so that it each patient can receive specific treatment, without one patient receiving too much air or pressure and experience lung trauma. According to University of Michigan, the device will cost about 1/100th the price of a new ventilator, while doubling ventilator capacity.
The device has undergone animal testing on pigs and received approval from the FDA for emergency use. The patented device will be manufactured by Autocam Medical and sold and distributed by Michigan startup MakeMedical, with the University of Michigan receiving royalties through the licensing of the product. However, the VentMI will be sold at cost to healthcare providers so that these partners are not benefitting financially from the device during the crisis. Those interested in ordering VentMI devices can contact MakeMedical.
Origin, whose 3D-printed nasopharyngeal swabs are a part of a successful clinical trial for SARS-CoV-2 testing, has signed an agreement with Stratasys to promote Origin NP O1 Swabs to healthcare providers and testing centers in the U.S. According to the partners, the Origin One 3D printer can produce 1,500 swabs at a time with the possibility of multiple machines making 190,000 per day or 1.3 million per week.
Vat photopolymerization is the primary process being used to make these printed swabs (aside from HP’s Multi Jet Fusion). Though Stratasys does not offer any in its own portfolio, it is involved in other COVID-19-related medical supply efforts, including leading a coalition of businesses producing face shields for nearly 100 organizations. Using its existing network, Stratasys believes that it can extend the reach of Origin’s swabs. To learn more, interested parties can visit this link.
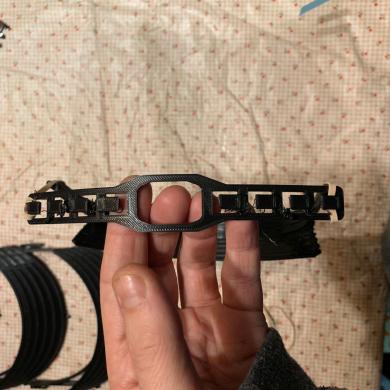
An example of an ear saver device reviewed by the National Institute of Health. Image courtesy of NIH.
Community Health Network, a healthcare network in Indiana, has an interesting story about the current status of personal protection equipment (PPE) demand. The group’s desktop technician, Mark Nix, started out making face shields using his desktop printers, but has shifted to ear savers, that is devices for preventing chaffing of the ears of healthcare workers who wear face masks all day. In addition to making 200 such tools daily, Nix is working with 30 other caregivers to expand his work.
In Philadelphia, a coalition of representatives from hospitals, universities, manufacturers, government and small businesses is providing PPE to local healthcare providers. The group, CoverAid PHL, has so far provided 4,500 masks to 13 organizations. What’s perhaps most interesting about the group’s work is that the masks are not made using 3D printing, demonstrating that low-tech may often be preferable to high-tech solutions. The group is sewing fabric masks using a standard design that is widely accepted.
As the pandemic continues to grip the world, we will continue to provide regular updates about what the 3D printing community is doing in response. As always, it is important to keep safety in mind, remain critical about the potential marketing and financial interests behind seemingly good humanitarian efforts from businesses, and to do no harm.
Subscribe to Our Email Newsletter
Stay up-to-date on all the latest news from the 3D printing industry and receive information and offers from third party vendors.
Print Services
Upload your 3D Models and get them printed quickly and efficiently.
You May Also Like
Reinventing Reindustrialization: Why NAVWAR Project Manager Spencer Koroly Invented a Made-in-America 3D Printer
It has become virtually impossible to regularly follow additive manufacturing (AM) industry news and not stumble across the term “defense industrial base” (DIB), a concept encompassing all the many diverse...
Inside The Barnes Global Advisors’ Vision for a Stronger AM Ecosystem
As additive manufacturing (AM) continues to revolutionize the industrial landscape, Pittsburgh-based consultancy The Barnes Global Advisors (TBGA) is helping shape what that future looks like. As the largest independent AM...
Ruggedized: How USMC Innovation Officer Matt Pine Navigates 3D Printing in the Military
Disclaimer: Matt Pine’s views are not the views of the Department of Defense nor the U.S. Marine Corps Throughout this decade thus far, the military’s adoption of additive manufacturing (AM)...
U.S. Congress Calls Out 3D Printing in Proposal for Commercial Reserve Manufacturing Network
Last week, the U.S. House of Representatives’ Appropriations Committee moved the FY 2026 defense bill forward to the House floor. Included in the legislation is a $131 million proposal for...