Companies, organizations and individuals continue to attempt to lend support to the COVID-19 pandemic supply effort. We will be providing regular updates about these initiatives where necessary in an attempt to ensure that the 3D printing community is aware of what is being done, what can be done and what shouldn’t be done to provide coronavirus aid.
One of the more interesting innovations to come out of corporate supply and marketing efforts in response to the coronavirus crisis is the development of 3D-printed nasal swabs. In addition to Formlabs, HP and EnvisionTEC, Carbon is 3D printing nasopharyngeal swabs to replenish the supply for COVID-19 testing. It is now doing so at a rate of 1 million swabs weekly and distributing them with in vitro diagnostic and medical device maker Resolution Medical.
The swabs being made by these companies are unique in that, as far as we are aware, this is the first time 3D printing is being used to produce testing swabs for end use. Moreover, they are incorporating unique features that increase the surface area of the swab while reducing the material used, resulting in faster printing and potentially improved mucous collection. This is true of Carbon’s swab design, which also has a brush-like texture.
While one might envision cotton or wood swabs being used for the COVID-19 tests, these materials cannot be used because they might affect the ribonucleic acid (RNA) of the collected sample. To print its swabs, Carbon is relying on a biocompatible resin called KeySplint Soft Clear, used for orthodontic devices such as mouth guards. The swabs are classified by the U.S. Food and Drug Administration (FDA) as a Class I 510(k) Exempt in vitro diagnostic medical device.
Ensuring a steady supply of test swabs is only one part of the problem for expanding the capacity for COVID-19 testing. In Washington state, for instance, not only are they in need of more swabs, but also the viral transport media that the swab goes into. In some cases, there is not a sufficient supply of the reagents needed to run the tests.
Additionally, there are not enough machines to run the various types of tests that are being deployed, nor enough healthcare workers trained in the operation of those tests, resulting in backlogs. This occurred in California, where roughly 33 percent of the over 83,000 tests taken had been processed as of last Saturday.
As is well reported, hospitals are in short supply of the personal protection equipment (PPE) for engaging with patients. This same gear is necessary for lab technicians to process test samples. While we await federal mobilization of large manufacturers to produce the necessary equipment, which has its own extended timeline for retooling factories, numerous 3D printing companies have attempted to lend their support by producing PPE.
Carbon is working alongside its client adidas to manufacture face shields for healthcare workers, reportedly using the same material as is used for its 3D printed footwear. Carbon dental customer Candid has converted its manufacturing operations to make face shields as well, with Carbon claiming to make over 18,000 shields weekly.
We learned from Dr. Beth Ripley, Director of the VA 3D Printing Network in the VHA Innovation Ecosystem, that face shields are among the safest items that can be manufactured by hobbyist volunteers. She also pointed out, however, that under non-emergency circumstances, these devices would still need to be made according to Current Good Manufacturing Practices in the U.S. Therefore, it helps for experienced medical device makers and experts to produce these items.
The School of Pharmacy at Queen’s University Belfast typically focuses its 3D printing efforts to make drug delivery systems and medical devices—such as catheters with antibiotics for dialysis patients, microneedles and 3D printed tablets contained multiple drugs. In response to the pandemic, the lab is making face shields. Modifying designs by Spanish engineers, the group is producing parts for healthcare staff across the Belfast Trust medical system. What distinguishes the school’s design from some others being made is the fact that many expose the forehead or may have comfortability issues. So far, the school has made roughly 1,000 face shields and has shared its design online.
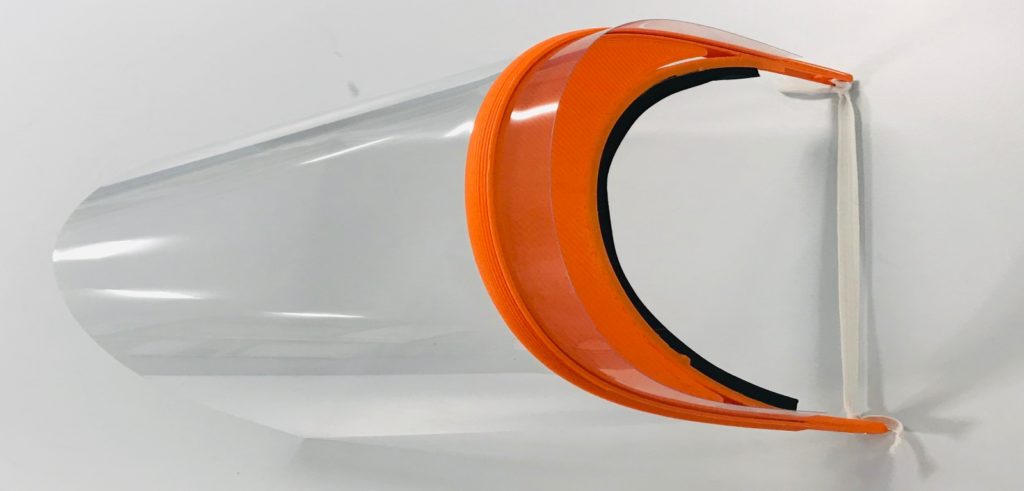
A face shield made with a 3D printed visor and laser cut plastic film. Image courtesy of the School of Pharmacy at Queen’s University Belfast.
3D Systems has also begun printing an emergency stopgap face mask (SFM) for use when standard PPE is not available or in less critical, non-medical environments that don’t require FDA-compliant PPE. The SFM was designed alongside engineers and clinicians at the Veterans Health Administration, is available in multiple sizes and is printed from a biocompatible nylon material using selective laser sintering (SLS). The device is made up of a 3D-printed mask and filter cover, two elastic strips, and a rectangular patch of filter material. It can be disinfected and even sterilized, if the situation demands it.
3D Systems has uploaded the designs, instructions for use, and a manufacturing guidance document for 3D printing the mask using 3D Systems’ SLS equipment and materials, Duraform PA or Duraform ProX PA. This means that manufacturers that have those machines and materials may be able to manufacture the parts in partnership with medical experts. The company will continue to update its COVID-19 response page with the devices it is developing and the stage at which they are ready for production and use.
As the pandemic continues to grip the world, we will continue to provide regular updates about what the 3D printing community is doing in response. As always, it is important to keep safety in mind, remain critical about the potential marketing and financial interests behind seemingly good humanitarian efforts from businesses, and to do no harm.
Subscribe to Our Email Newsletter
Stay up-to-date on all the latest news from the 3D printing industry and receive information and offers from third party vendors.
Print Services
Upload your 3D Models and get them printed quickly and efficiently.
You May Also Like
3D Printing News Briefs, July 2, 2025: Copper Alloys, Defense Manufacturing, & More
We’re starting off with metals in today’s 3D Printing News Briefs, as Farsoon has unveiled a large-scale AM solution for copper alloys, and Meltio used its wire-laser metal solution to...
3DPOD 260: John Hart on VulcanForms, MIT, Desktop Metal and More
John Hart is a Professor at MIT; he´s also the director of the Laboratory for Manufacturing and Productivity as well as the director of the Center for Advanced Production Technologies....
3D Printing News Briefs, June 28, 2025: Defense Accelerator, Surgical Models, & More
In this weekend’s 3D Printing News Briefs, 3YOURMIND was selected to join an EU Defense Accelerator, and PTC has announced model-based definition (MBD) capabilities within Onshape. Finally, a study out...
EOS in India: AM’s Rising Star
EOS is doubling down on India. With a growing base of aerospace startups, new government policies, and a massive engineering workforce, India is quickly becoming one of the most important...