Chinese researchers are looking further into the uses of titanium in bioprinting, outlining their findings in the recently published ‘Mechanical behavior of a titanium alloy scaffold mimicking trabecular structure.’ Five different unit cells were used in this study as the authors experimented with creating new trabecular structures via electron beam melting.
3D printing has already carved an indelible mark in the medical world, on a path that just keeps blazing forward due to the hard work of researchers. While tissue engineering is at the forefront of research today, along with the use of 3D printed models and devices, orthopedics specifically have been enormously and positively impacted by the technology allowing for much greater flexibility and customization.
Trabecular bone structures not only encourage ‘bioactivity’ of implants, but they also promote better growth of cells in the form of osteoblasts—along with directing bone tissue to connect with pores, creating implant-bone bio-fixation.
“With the development of 3D printing technology and new biological materials, the application of trabecular structure in artificial joint replacement is increasing, and the design, fabrication and mechanical properties of trabecular structures are the focus of current research,” state the authors.
“The morphological characteristics and mechanical behavior of 3D printed titanium alloy trabecular structure will affect the effects of artificial prosthesis replacement; therefore, the aspects need to be further researched.”
There has been previous research, but as the researchers point out, they were motivated to perform this study due to a lack of comprehensive study on ‘the mechanical behavior of titanium alloy trabecular structure at present stage of clinical usage.’
After 3D printing trabecular structures, they considered the following:
- Differences between design and manufacture
- Effects of different porosity and pore size on mechanical properties
- Mechanism of structural damage
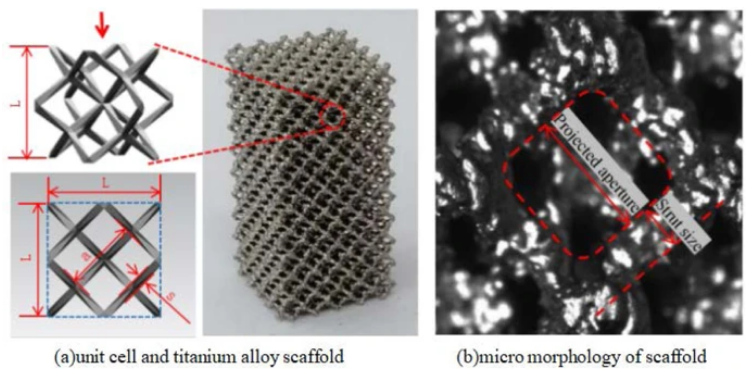
Titanium alloy scaffold built by unit cell (L, a and s are unit, projected aperture and strut size, respectively) and micro morphology of titanium alloy scaffolds mimicking bone trabeculae. a unit cell and titanium alloy scaffold, b micro morphology of scaffold
The research team obtained five cuboid scaffolds for the study, each with varying porosities, fabricated via EBM with Ti6Al4V titanium alloy powder. Other specimens were 3D printed too, in the form of dense cylindrical titanium.
“The correlation between porosity and mechanical properties were studied on scaffold specimens with different aperture and porosity at the same loading speed,” stated the authors. “The compression tests included researching the anisotropy of specimens under the same loading speed from two different loading directions as well as the effects of different loading speeds on mechanical properties.”
They also examined mechanical properties of samples from a variety of locations and printing processes, to include nine different sites and three orientations. Density was noted as: 4.3541037 g/cm3 calculated from 3D printed dense cylindrical specimens. The research team also noted that porosity was always ‘lower than that designed.’
Comparison between design value and actual value of scaffold specimen. (a) Strut size, (b) Projected aperture, (c) Porosity
Suitable porosity and connectivity allow for:
- Adhesion
- Proliferation
- Differentiation
- Guiding of bone tissue into the pore
“The parameters of 3D printed titanium alloy scaffold, such as aperture, porosity, pore shape and surface treatment, have an important effect on bone growth and osteoblast performance in vitro,” concluded the researchers. “We have systematically studied the structural design, fabrication and mechanical behavior of a 3D printed titanium alloy scaffold mimicking trabecula bone. This study may shed a light on the application of prostheses with proper structures and functions.”
What do you think of this news? Let us know your thoughts! Join the discussion of this and other 3D printing topics at 3DPrintBoard.com.
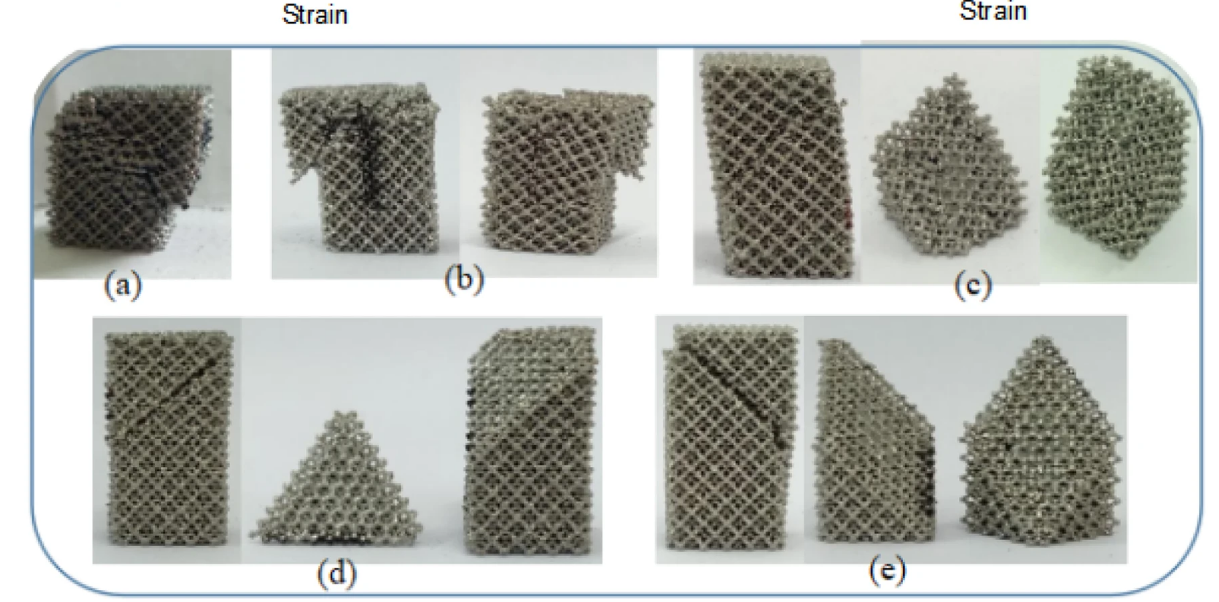
Compressive stress-strain curves of 9 specimens from 9 different locations and their local magnification maps, and fracture morphology of some specimens. the (a) to (e) are the fracture patterns of five specimens
Subscribe to Our Email Newsletter
Stay up-to-date on all the latest news from the 3D printing industry and receive information and offers from third party vendors.
Print Services
Upload your 3D Models and get them printed quickly and efficiently.
You May Also Like
3D Printing News Briefs, July 2, 2025: Copper Alloys, Defense Manufacturing, & More
We’re starting off with metals in today’s 3D Printing News Briefs, as Farsoon has unveiled a large-scale AM solution for copper alloys, and Meltio used its wire-laser metal solution to...
Etsy Design Rule Change Reduces Selection of 3D Printed Goods
Online marketplace Etsy has implemented a rule change requiring all 3D printed goods on the site to be original designs. The update to the site’s Creativity Standards states, ¨Items produced using...
Siraya Tech Introduces New Elastomer 3D Printing Materials, Including Foaming TPU
California company Siraya Tech, founded in 2019 with a focus on material science, customer focus, and agility, develops high-quality 3D printing materials that meet the needs of creators, hobbyists, and...
3D Printing News Briefs, April 12, 2025: RAPID Roundup
The news from last week’s RAPID+TCT in Detroit just keeps on coming! That’s why today’s 3D Printing News Briefs is another RAPID Roundup of more exciting announcements from the trade...