As 3D printing with metal continues to expand for industrial users around the world, so does the study of materials like powders, unique alloys, and a range of composites. In this study, outlining their findings in the recently published ‘Strength analysis of Ti6A14V titanium alloy produced by the use of additive manufacturing method under static load conditions,’ researchers focus on the uses of titanium alloy Ti6Al4V and comprehensive analysis of mechanical properties after printing via direct metal laser sintering (DMLS).
For many applications, the benefits of 3D printing and additive manufacturing processes overshadow more conventional methods for the creation of devices like dental implants, rocket engine components, car parts, and more. While greater affordability is key, so is the ability for many users to create parts that may never have been possible before—or even more notable, perhaps, is the option to scan older parts that have become obsolete and re-create them via 3D printing (especially helpful in applications like automotive and for the military).
Medical devices such as implants are often made from alloy due to the following advantages:
- High mechanical properties
- Low density
- Corrosion resistance
- Biocompatibility
Heat treatment is common with the use of metals, as it improves mechanical properties. Methods such as hot isostatic pressing (HIP) are often used; however, in this study, the researchers use DMLS additive manufacturing to create the samples to be tested for viable mechanical properties.
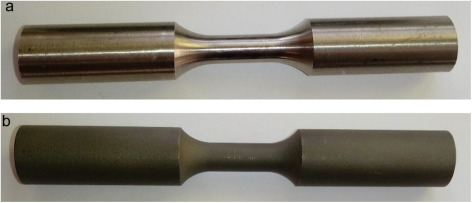
Physical form of research samples: (a) turned from a drawn bar, (b) manufactured by the additive method DMLS.
The team created samples in the form of annealed drawn bars (12mm in diameter) as well as a set created via DMLS on an EOS M280W machine, and annealed afterward.
“The printing process was characterized by the following parameters: laser power 200 W, minimum layer thickness 30 μm, scanning speed up to 7 m / s. The sample print direction was consistent with the Z axis,” explained the researchers.
Strength of the first samples was found to be lower in comparison, while hardness related different values:
“The difference in results is related to the method of sample preparation by the additive technology and the external load it has been subjected to,” stated the researchers.
“Slight changes in the hardness value in the x-plane of unloaded samples indicate similar mechanical properties of the material produced by the DMLS method.”

Samples for hardness tests: (a, b) samples from a drawn bar, (c, d) samples made using the DMLS method before tensile tests, (e, f) samples made using the DMLS method after tensile tests.
The team of researchers also noted that in this case, variances in hardness (between x-y and x-z) could be due to 3D printing of material grains, combined with deformations caused by the axial load.
Testing of sample DMLS macrostructures demonstrated obvious changes related to tensile load, indicating that it may also again be due to 3D printing—as well as set parameters and direction of material layers. The researchers compared macrostructures both before and after tensile loading, realizing that plastic deformations then occurred, and were plainly visible caused by the load line.
Because titanium is used in a host of 3D printing and AM processes today, this material is an ongoing source of study from use with composites, to medical devices like sternum or hip implants, printing with glass, and more.
What do you think of this news? Let us know your thoughts! Join the discussion of this and other 3D printing topics at 3DPrintBoard.com.

Macrostructure of the Ti6Al4V material resulting from the DMLS additive manufacturing method taken from: (a) samples along the Z axis, (b) sample gripping part, (c) distribution of force lines in the sample during tensile force; I – the area of significant changes in the material structure resulting from the tensile force action, II – transitional area, III – area with limited impact of tensile force.
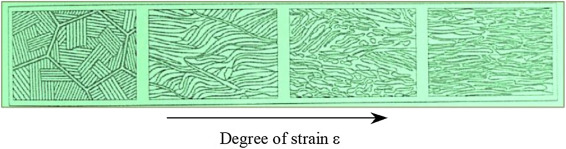
Schematic presentation of two-phase microstructure formation of two-phase α + β titanium alloy plastically deformable in the phase transition temperature range α + β → β as a function of deformation degree ε.
Subscribe to Our Email Newsletter
Stay up-to-date on all the latest news from the 3D printing industry and receive information and offers from third party vendors.
Print Services
Upload your 3D Models and get them printed quickly and efficiently.
You May Also Like
Reinventing Reindustrialization: Why NAVWAR Project Manager Spencer Koroly Invented a Made-in-America 3D Printer
It has become virtually impossible to regularly follow additive manufacturing (AM) industry news and not stumble across the term “defense industrial base” (DIB), a concept encompassing all the many diverse...
Inside The Barnes Global Advisors’ Vision for a Stronger AM Ecosystem
As additive manufacturing (AM) continues to revolutionize the industrial landscape, Pittsburgh-based consultancy The Barnes Global Advisors (TBGA) is helping shape what that future looks like. As the largest independent AM...
Ruggedized: How USMC Innovation Officer Matt Pine Navigates 3D Printing in the Military
Disclaimer: Matt Pine’s views are not the views of the Department of Defense nor the U.S. Marine Corps Throughout this decade thus far, the military’s adoption of additive manufacturing (AM)...
U.S. Congress Calls Out 3D Printing in Proposal for Commercial Reserve Manufacturing Network
Last week, the U.S. House of Representatives’ Appropriations Committee moved the FY 2026 defense bill forward to the House floor. Included in the legislation is a $131 million proposal for...