3D printing and additive manufacturing have become a matter of national importance in Germany, and to the automotive industry overall. Several organizations—along with the ongoing support of the Fraunhofer Institute for Laser Technology ILT and the Chair for Digital Additive Production DAP of RWTH Aachen University—are eager to see the Industrialization and Digitization of Additive Manufacturing for Automotive Series Processes (IDAM) lead the way for furthering the use of AM processes in the auto industry. Project partners for IDAM include a variety of small to medium enterprises (SMEs) and research institutions, all dedicated to the progress of metallic 3D printing for the manufacturing of vehicles.
BMW Group is behind much of this push, and their dedication to additive manufacturing for almost 30 years has not gone unnoticed. From an investment in a new AM facility in Munich to specialized projects like restoring Elvis’ long-lost BMW 507 from 1958, their work in 3D printing has been so prolific that by last year they had fabricated over one million parts, harnessing the untold power of this progressive technology. Currently, 3D printing and AM processes with metal are in force at BMW’s facility in Munich, along with GKN Powder Metallurgy’s factory in Bonn.
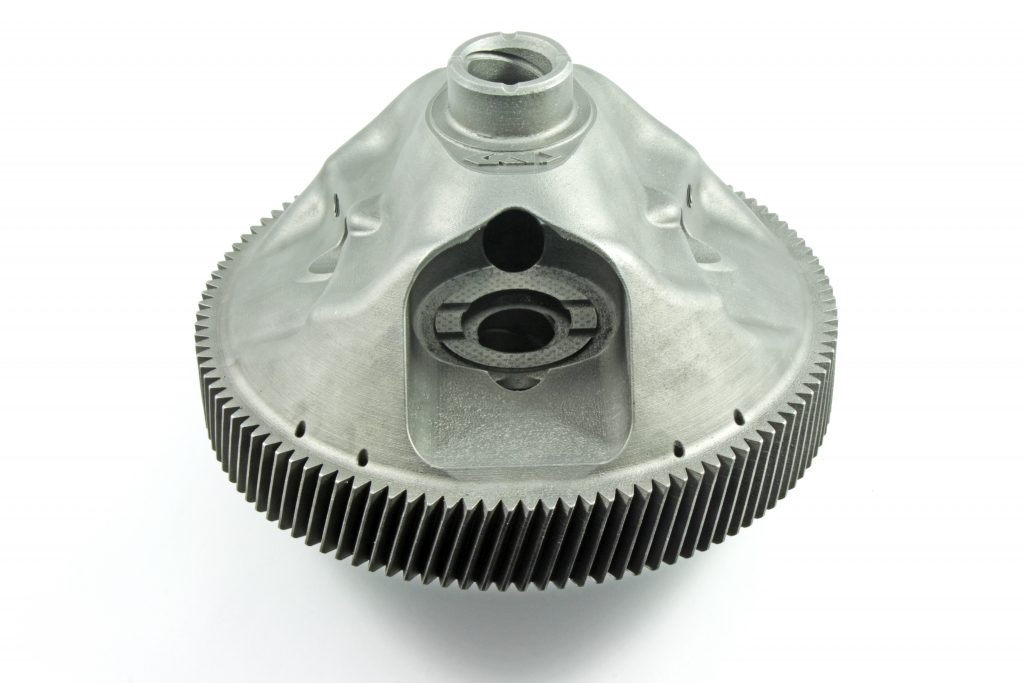
This structural optimized differential housing, jointly developed by GKN Powder Metallurgy and Porsche Engineering, is one of the growing new e-drive powertrain applications for Metal AM (Photo: GKN Powder Metallurgy)
There are 12 partners total working within the ongoing project via IDAM, and as Fraunhofer Institute for Laser Technology ILT points out in their latest press release, the use of metallic 3D printing should ‘sustainably strengthen Germany’s technological pioneering role and the country itself as a manufacturing location.’ Everyone involved is obviously envisioning making use of all of 3D printing’s most famed benefits, beginning with greater affordability. Along with that comes exponential reduction of turnaround time in manufacturing, and the ability to offer a wide range of customization options for clientele.
The IDAM team is present at both facilities, qualifying the technology for production of metal parts, with projections for manufacturing at least 50,000 3D printed parts annually. They also expect over 10,000 individual and spare parts to be created. This is a far cry from the initial use of 3D printing for low-batch production of customized parts. Even with plans for mass production, the partners expect high-performance parts to be created ‘under extreme cost pressure.’
Project partners include:
- Aconity GmbH, Herzogenrath
- Concept Reply GmbH, Munich
- Fraunhofer Institute for Laser Technology ILT, Aachen
- GKN Powder Metallurgy, Radevormwald
- Myrenne GmbH, Roetgen
- Intec GmbH – Ingenieurbüro für Automatisierungstechnik, Bad Neuenahr-Ahrweiler
- Kinexon Industries GmbH, Munich
- Chair for Digital Additive Production DAP, RWTH Aachen, Aachen
- Technical University of Munich, Chair of Metal Forming and Casting, Munich
- Schmitz Spezialmaschinenbau GmbH, Rheinbreitbach
- Volkmann GmbH, Soest
This activity truly marks the beginning of metal AM taking a prioritized role within Germany’s industrial dynamic, with two modular production lines being installed (one in Munich; one in Bonn). Customization is key here too, as modules can be changed to fit production needs.
“In addition, their process steps can be controlled and utilized flexibly,” states Fraunhofer Institute for Laser Technology ILT in their press release. “By taking an integrated view of the automotive production line into account, the project partners plan on reducing the manual share of activities along the process chain from currently around 35 percent to less than 5 percent. In addition, the unit costs of 3D printed metal components should be more than halved.”
The IDAM partners are currently using their experience and expertise in designing modules for the mass production line, to include automated processes for powder handling, monitoring, post-processing, and more.
“Since large industrial companies are involved, these linked modules can be used in the AM production lines under real conditions and on a large scale,” explains the Fraunhofer Institute for Laser Technology ILT release. “In addition, industrial standards can be set, and industry-relevant quality characteristics elaborated. Only through this interdisciplinary cooperation does the IDAM project make it possible to holistically examine metallic 3D printing for automotive series processes and to establish it sustainably in production.”
What do you think of this news? Let us know your thoughts! Join the discussion of this and other 3D printing topics at 3DPrintBoard.com.
[Source: Fraunhofer Institute for Laser Technology IL]Subscribe to Our Email Newsletter
Stay up-to-date on all the latest news from the 3D printing industry and receive information and offers from third party vendors.
Print Services
Upload your 3D Models and get them printed quickly and efficiently.
You May Also Like
The Dental Additive Manufacturing Market Could Nearly Double by 2033, According to AM Research
According to an AM Research report from 2024, the medical device industry, specifically in dentistry, prosthetics, and audiology, is expected to see significant growth as these segments continue to benefit from...
Heating Up: 3D Systems’ Scott Green Discusses 3D Printing’s Potential in the Data Center Industry
The relentless rise of NVIDIA, the steadily increasing pledges of major private and public investments in national infrastructure projects around the world, and the general cultural obsession with AI have...
AM Research Webinar Explores Continuum’s Sustainable Metal Additive Manufacturing Powders
Metal additive manufacturing (AM) powder supplier Continuum Powders is working to develop solutions that empower industries to reduce waste and optimize their resources. An independent life cycle assessment (LCA) of...
3D Printed Footwear Startup Koobz Lands $7.2M in Seed Round
California-based Koobz is focused on reshoring the U.S. footwear supply chain with advanced manufacturing processes, including 3D printing. The startup just announced that it has added $6 million to its...