In the recently published ‘3D printed shape-programmable magneto-active soft matter for biomimetic applications,’ researchers from China explore the development of a high-performance material that transforms quickly from one shape to another as required for specific applications.
Materials scientists continue to be inspired by nature in many of their studies and consequent innovations today, and as 3D printing morphs into 4D printing with shapes that deform and then return to their original shape, digital fabrication itself continues to expand. Most of these materials and consequent deformation are driven by external forces in the environment such as temperature or moisture and can be used as complex geometries for applications like medicine, robotics, and more.
In this study, the authors examine the use of magnetic field control and magneto-active soft materials (MASMs) as they offer the potential for both soft sensors and actuators. Previous research has been performed with 3D magnetic printing, resulting in the fabrication of both anisotropic composites coupled with magnets.

Shape-programming strategy and manufacturing process of MASMs. (a) The flow chart of shape-programming strategy and a programming case for imitation of inchworm. The deformations are simulated by COMSOL, and the direction of the UMF is indicated by the red arrows. (b) Schematic illustrations of 3D printing and encapsulation. 3D printing is employed for manufacturing the various magnetic structural elements, which are encapsulated by silicone rubber. (c) The photos of the MASM samples with oriented magnetic structural elements. The radius of the disk samples is 10 mm. (For interpretation of the references to color in this figure legend, the reader is referred to the Web version of this article.)
With a new ‘shape-programming strategy,’ the goal for this study was to create stable shapes that transform quickly and are also programmable. The research team put the benefits of 3D printing to work:
“With the advantages of 3D printing, this manufacturing approach enables the magnetic structural elements with any shape, distribution, and orientation to generate anisotropic magnetization profiles. This method allows us to program magnetic moment in the soft matrix, enabling the desired actuation capabilities of the MASMs. The deformation property of shape programmable MASMs have been studied synthetically, and the related physical mechanism has been proposed.
“With these excellent capabilities, various biomimetic structures (inchworm, manta ray, and soft gripper) can be easily fabricated with walking, swimming and snatching functions under the uniform magnetic field (UMF). This proposed approach can make up for the shortcomings of the existing programming methods and opens new avenues to fully capitalize the potential of MASMs.”
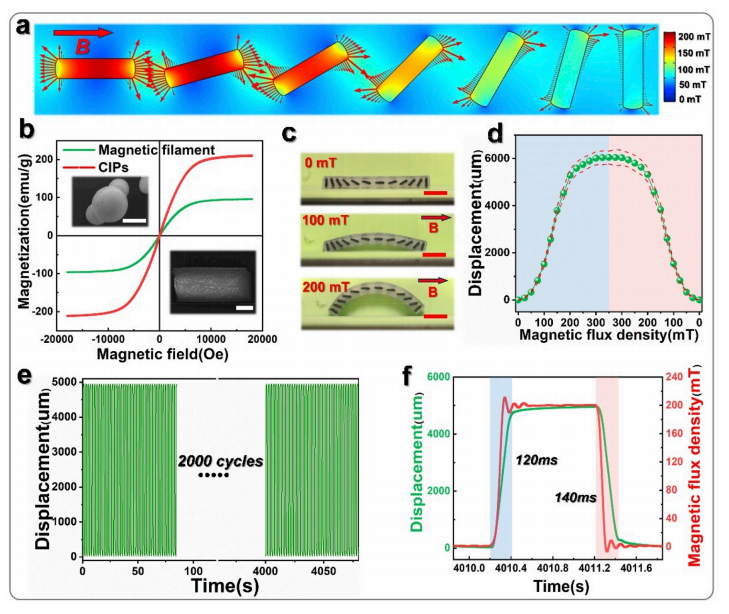
Shape-change mechanisms and deformation performance of MASM strip. (a) Finite element analysis of the oriented magnetic structural elements evaluated by COMSOL. The strength of the applied UMF is 300 mT, and the direction is indicated by the red arrow. The magnetic flux density is indicated by the color legend, and the direction and magnitude of Maxwell’s surface stress tensor are indicated by the direction and logarithmic size of the red arrows. (b) Magnetization curves (magnetic moment per unit mass) of magnetic filament and CIPs. The inserted photos are SEM images of CIPs and magnetic filament, and the scale bars are 2 μm and 0.5 mm respectively. (c) Photographs of the bending deformation of the MASM strip under 0, 100, and 200 mT, and the scale bars are 5 mm. In this case, the magnetic structural elements with a length of 1.5 mm, width of 0.3 mm, and thickness of 4 mm have distributions in SR. (d) Curve of the bending deformation of the MASM strip under increasing and decreasing magnetic flux density, which is controlled by the current in the electromagnet. The deformation is evaluated by the displacement of the central point of the MASM strip. The test schematic is illustrated in Fig. S1e. (e) Cycle test of deformation performance of the MASM strip under transient magnetic field. The time for each cycle is 1.5 s, and it includes the transient increase and decrease of the magnetic field. The transient magnetic field is generated on the basis of the motion of the permanent magnet controlled by a linear motor, as shown in Fig. S1f. (f) Single-cycle curves of bending deformation and transient magnetic field. The response and reset times are marked. (For interpretation of the references to color in this figure legend, the reader is referred to the Web version of this article.)
PLA was mixed at a 6:1 volume ratio with Carbonyl iron particles (CIPs), blended mechanically for 30 minutes, and then added to the extruder of an FDM 3D printer.
“Here, it should be noted that printing magnetic structural elements is just one of the methods for the design of magnetic moment. Adjusting the magnetic moment can also depend on the particle distribution and magnetic domain,” explained the researchers.
Upon 3D printing, however, the magnetic structures were comprised of isotropic ferromagnetic properties due to the uniform dispersion of PLA particles. The team 3D printed samples with a variety of different oriented magnetic structural elements, confirming that these differences did affect mechanical properties of the MASMs.
Ultimately, the researchers were able to create a range of biomimetic structures inspired by nature such as the inchworm, manta ray, and a soft gripping device. Fabricated samples were also inspired by animals such as snakes and mollusks, and the MASM forms were capable of mimicking their structures and movements; however, magnetization was dependent on distribution and orientation of adjacent magnetic structural elements—meaning that overall magnetics must be considered for required efficiency.
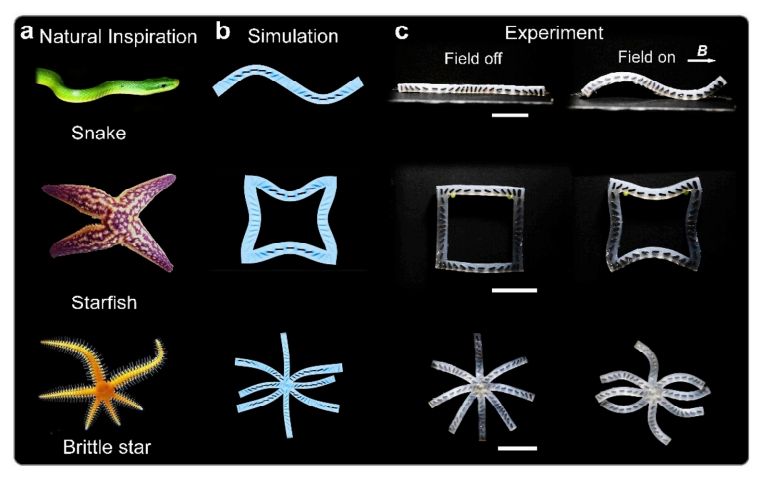
Various shape-programmable MASMs with two-dimensional shape change under applied magnetic fields for biomimetic imitation. (a) Photographs of snake, starfish, and brittle star. (b) Finite element simulation of programmed shapes via COMSOL. The magnetic flux density is indicated by the color. (c) Two-dimensional shape changes of MASMs under applied magnetic fields. The intensity of the horizontal UMF is 200 mT, and the direction is indicated by the arrow. For different programmed shapes, the magnetic structural elements with a length of 1.5 mm, a width of 0.3 mm, and a thickness of 4 mm have different distributions in SR. All scales are 10 mm. (For interpretation of the references to color in this figure legend, the reader is referred to the Web version of this
article.)

Design of soft robots and actuator on the basis of shape-programmable MASMs. (a) Walking motion of the inchworm-like soft robot on serration plate. The bending of the robot is driven by the UMF, and it is restored by the coupling of gravity and elastic forces. The white scale bar is 10 mm. (b) Swimming of the manta ray-like soft robot under water. The swing of the swimming robot is also driven by the UMF. The white scale bar is 10 mm. (c) Grab and release of the soft gripper. The gripping action is driven by the UMF, and the weight of the cylindrical object is 15.3 g. The white scale bar is 20 mm. In these cases, the intensity of the UMF is 300 mT, and the direction is as indicated by the arrow.
The sample structures, ‘successfully fabricated,’ exhibited potential for functionality in exercises such as locomotion, swimming, and grabbing. They also displayed the desired mechanical properties with stability and accuracy in shape-changing—ensuring performance required for the future design of actuators and soft robotic innovations.
Upon factoring in the low density, ‘excellent flexibility,’ and suitable properties for actuation, the team continued to move forward with their project, making soft robots and actuators:
- The inchworm design translated into a soft robot able to ‘walk’ on a serration plate created by the researchers.
- The manta ray design inspired another soft robot with ‘muscles and wingspan’ made of both MASMs and SR. It was even able to swim underwater.
- The soft gripper functioned beyond that of conventional similar devices, with grab-and-release manipulated by magnetic actuation.
“This work simply uses uniform magnetic field (UMF) as the actuation only, but more complex actuation behaviors can also be generated by using the gradient magnetic field. The proposed approach opens new avenues to fully capitalize the potential of MASMs, allowing researchers to develop a wide range of soft actuators that are critical in soft robotics, medical care, and bionics applications,” concluded the authors upon completing their study.
Scientists have always had a history of being inspired by nature, and this has played a fascinating role in the progression of 3D printing as biomimetics have been the force behind new prosthetics, innovative architectural structures, drone technology, and more.
What do you think of this news? Let us know your thoughts! Join the discussion of this and other 3D printing topics at 3DPrintBoard.com.
[Source / Images: ‘3D printed shape-programmable magneto-active soft matter for biomimetic applications’]Subscribe to Our Email Newsletter
Stay up-to-date on all the latest news from the 3D printing industry and receive information and offers from third party vendors.
Print Services
Upload your 3D Models and get them printed quickly and efficiently.
You May Also Like
Heating Up: 3D Systems’ Scott Green Discusses 3D Printing’s Potential in the Data Center Industry
The relentless rise of NVIDIA, the steadily increasing pledges of major private and public investments in national infrastructure projects around the world, and the general cultural obsession with AI have...
Formlabs Teams Up with DMG MORI in Japan
In late June, Nick Graham, Chief Revenue Officer at Formlabs, announced on LinkedIn that the company had partnered with DMG MORI, one of the world’s leading machine tool companies, to...
EOS in India: AM’s Rising Star
EOS is doubling down on India. With a growing base of aerospace startups, new government policies, and a massive engineering workforce, India is quickly becoming one of the most important...
3D Printing News Briefs, June 25, 2025: R&D Materials, 3D Printed Veneers, & More
In today’s 3D Printing News Briefs, 3DXTECH has launched a program that gives customers early access to experimental materials, and the first Lithoz CeraFab Multi 2M30 in the Czech Republic...