Oerlikon AM Partnering with Hirtenberger to Eliminate Post Processing Steps in Additive Manufacturing
Oerlikon, headquartered in Switzerland, was busy making announcements at Formnext this year regarding new developments; however, collaborations continue to be all the rage within the 3D printing industry (which is very good for users who reap the rewards of complementary partnerships working to please them) and Oerlikon did not disappoint as they reported progress on their continued work between Oerlikon AM and Hirtenberger, an Austrian company that specializes in surface finishing.
The partnership began earlier in 2019 as they began testing a post-processing method for additive manufacturing called the Hirtisation Process, which we wrote about previously. This technique is based on the treatment of 3D printed surfaces, removing support structures, and best of all—automating post-processing for users. Hirtisation can be simplest described as a solvent-based reverse electroplating process. The process provides for some of the best finishes we’ve ever seen in metals. If implemented properly this could save users 50% or more of part cost by replacing a lot of manual steps in powder and support removal by one machine. According to a recent press release, the two companies have ‘intensified’ their collaboration, and have formed a team to investigate the best way to integrate the process into AM technology and the growing value chain.
This new process offers:
- Smoother surface textures
- Production of complex parts that may require interior supports
- Removal of supports with destroying the parts or prototypes
Oerlikon AM plans to use this technology in applications such as turbomachinery, oil, gas, automotive, and general industry. The two companies also expect to offer their services to companies mainly engaged in rapid prototyping. Overall, users around the world who are able to use such technology will be relieved to forgo the inconvenience of post-processing, and all the extra steps involved. Moving away from such methods will save time and money, and allow designers, engineers, and everyone involved to spend their time innovating rather than removing support structures.
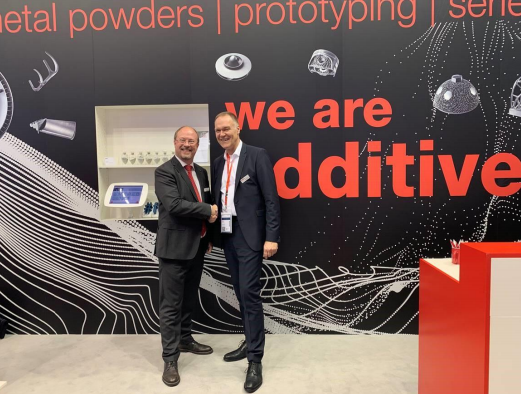
From left to right: Dr. Wolfgang Hansal, Managing Director, Hirtenberger Engineered Surfaces and Dr. Sven Hicken, Oerlikon, Head of Additive Manufacturing Business Unit.
“For Oerlikon AM, the Hirtisation Process addresses one of AM’s major challenges, which is to provide our customers with parts with more complex geometries – some of which are not possible nor economical with existing AM and post-processing technologies,” said Dr. Christian Haecker, Head of Oerlikon AM Industrialization. “The process fits perfectly in our desire to offer customers services and products along the entire value chain. We also see a benefit in increasing repeatability of defined AM surface quality.”
The technology should be introduced to North America by the two companies in 2020.
“We provide a crucial step in the process chain of 3D printing of metal parts,” said Dr. Wolfgang Hansal, Managing Director, Hirtenberger Engineered Surfaces. “We see ourselves as an industrial enabler of automated surface finishing. We maintain the full freedom of the printed parts design, while allowing cost efficient post-processing. Closing the interfaces along the production chain from post-processing back to construction, design and printing is key for the establishment of reliable additive manufacturing, from prototyping to large quantity serial production. For these reasons, Oerlikon AM is an important partner.”
Oerlikon continues to improve 3D printing and AM processes, from being involved in other collaborations to participating in an AM open cluster, to working to create new materials. Hirtisation uses some very aggressive solvents so the process may not be suited for all applications and users. We have heard of positive results from one service bureau however while one German automotive company reportedly had to turn theirs off. In metals right now Hirtisation represents an incredible promise to radically reduce costs and improve Ra. If they get it right Oerlikon and Hirtenburger could make a major impact with it. What do you think of this news? Let us know your thoughts! Join the discussion of this and other 3D printing topics at 3DPrintBoard.com.
[Source / Images: Oerlikon press release]Subscribe to Our Email Newsletter
Stay up-to-date on all the latest news from the 3D printing industry and receive information and offers from third party vendors.
Print Services
Upload your 3D Models and get them printed quickly and efficiently.
You May Also Like
Making Space: Stratasys Global Director of Aerospace & Defense Conrad Smith Discusses the Space Supply Chain Council
Of all the many verticals that have been significant additive manufacturing (AM) adopters, few have been more deeply influenced by the incorporation of AM into their workflows than the space...
EOS in India: AM’s Rising Star
EOS is doubling down on India. With a growing base of aerospace startups, new government policies, and a massive engineering workforce, India is quickly becoming one of the most important...
PostProcess CEO on Why the “Dirty Little Secret” of 3D Printing Can’t Be Ignored Anymore
If you’ve ever peeked behind the scenes of a 3D printing lab, you might have caught a glimpse of the post-processing room; maybe it’s messy, maybe hidden behind a mysterious...
Stratasys & Automation Intelligence Open North American Tooling Center in Flint
Stratasys has opened the North American Stratasys Tooling Center (NASTC) in Flint, Michigan, together with automation integrator and software firm Automation Intelligence. Stratasys wants the new center to help reduce...