During a recent Formlabs Webinar, growth marketing specialist, Faris Sheikh, performed an engaging live demonstration of the new Form 3 Stereolithography (SLA) printer. For the hundreds of viewers that tuned in on September 26th, the performance of the printing system unveiled some of the advantages inherent in its new features. Everything from a significant improvement in print quality over the previous model, the Form 2, to understanding how low-force SLA can deliver better surface quality and help to get a gentle release once the part is done printing. The Form 3: Live Product Demo webinar is a step-by-step presentation on how to set up and print on the Form 3, walking the audience through the making of a speaker prototype.
You probably read a lot about how the Form 3’s new low-force Stereolithography (LFS) technology is used to create parts that are consistently accurate, with amazing detail and surface finish, every single time. But Sheikh took his audience on a dive into the technology behind the Form 3, talking about what makes it special, helping potential users to understand the new print process and learn how to use it to avoid lead times.
Formlabs has been creating reliable, accessible printing systems for professionals for the last decade, ever since Max Lobovsky, CEO and Co-Founder of Formlabs decided it was time to tackle the $80,000 industrial SLA machine industry and turn it into something really affordable, easy to use and desktop-friendly. So Stereolithography has been the company’s forte since 2011, and the Form 3 is already the fourth iteration of the original Form machine. Over 50,000 of the company’s printers are used across the world in so many different brands, from Gilette to Disney, Boeing, New Balance, Amazon, Sony, and Google, just to name a few of the most known ones out there. And they really keep count of the parts being printed with their machines, which up to now its something like 40 million, but they expect that number to go up quickly with the new Form 3 and another version which is bigger, called the Form 3L.
“Our goal with the Form 3 was to reduce the peel force that is common in all SLA technologies and can have some negative consequences on printing processes. So to come up with LFS, this powerful form of SLA technology that decreases the forces of the peel process, we came up with two new features: a flexible tank and a light processing unit,” outlined Sheikh.
The face of the tank is made of a flexible film and reduces print forces to deliver high quality and printer reliability so that when the part comes out it is with a gentle release compared to traditional SLA. Sheikh explained that the company tested the peel forces and determined that there was a ten-time reduction on the Form 3, compared to its predecessor Form 2. That is a significant improvement between printer models. He also suggested that the flexible tank will impact on the surface finish, making it “incredible” as they say, and allow for a faster clean up and finishing after the parts are done the printing.
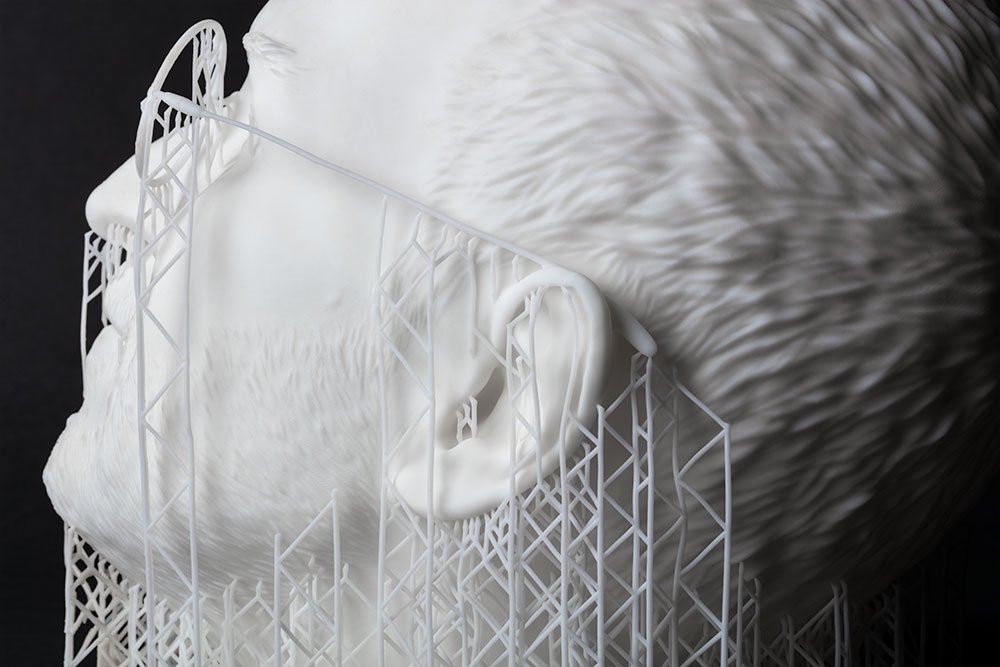
Steve Jobs sculpture designed by Sebastian Errazuriz, 3D printed in White Resin powered by the low-force tech of the Form 3
“Incredible surface finish is the result of good layer registration, that is, how accurately each layer is aligned with the previous layer. The more accurately they are aligned, the better surface finishes you will have as well as more translucent and clear parts. The greater sharpness in the edges is ideal for the jewelry industry which usually looks for delicate feature-capability and fine level of detail. While the bio and medical industry can benefit from models that will look so much more representative of what they are trying to do.”
The company suggests that 47% of Form 2 users said removing supports where their biggest pain points, while 62% said Formlabs could improve their machines to make the finishing process easier. So Formlabs developed the LFS which allows for easy support removal thanks to tiny touchpoints, or what Sheikh called “light-touch support” that can easily tear away so that being able to just pop off the part becomes a real improvement for users.

Light-touch support structures on the Form 3 leave behind four times less support material than supports printed on Form 2
“If you can finish faster and have a faster clean up it means that you have more time to work on the printing process and spend more time on the product. We want to make your life easier so you don’t have to worry about the printing process.”
The printing process with the Form 3 is simple, the user picks any of more than 20 material options from Formlabs, then prepares the design (Sheikh did it using the PreForm software, a free tool offered by the company), print the part and then wash and cure it (done on the FormWash and FormCure machines). The printing of the chosen speaker model by Sheikh takes six hours, but the preparation and post-processing can all be done in just over 30 minutes.
Sheikh shows how simple it is to use the PreForm software, which has automatic algorithms and helps the user orient the part and generates the supports with just one click. And since the part is going to be printed upside down, it needs supports layer by layer. Then, the print file is sent wirelessly to the printer and it starts printing. Since it takes six hours to print a prototype speaker of 753 layers, the printer will send a text message when it’s ready.
Considering the webinar is less than an hour long, Sheikh shows his audience how easy it is to release the part from the supports once it’s done, with another part that was already done printing.
“Taking off the supports is so simple with LFS, you can easily twist and all the supports come off in one second.”
Formlabs aims to create easy-to-use printers. Sheikh claims that Form 3 is an accessible machine, coming up to $3,500, with an industrial quality that can produce strong parts, making it an ideal successor to Form 2. Formlabs is looking to, not just create a very popular desktop SLA machine, but build a whole culture of innovation, impacting entire teams, enabling anyone to tackle their design, building machines that work remotely so that the printing process is easy and becoming a leading force in many industries.
[Images: Formlabs]Subscribe to Our Email Newsletter
Stay up-to-date on all the latest news from the 3D printing industry and receive information and offers from third party vendors.
Print Services
Upload your 3D Models and get them printed quickly and efficiently.
You May Also Like
3D Printing News Briefs, July 2, 2025: Copper Alloys, Defense Manufacturing, & More
We’re starting off with metals in today’s 3D Printing News Briefs, as Farsoon has unveiled a large-scale AM solution for copper alloys, and Meltio used its wire-laser metal solution to...
Etsy Design Rule Change Reduces Selection of 3D Printed Goods
Online marketplace Etsy has implemented a rule change requiring all 3D printed goods on the site to be original designs. The update to the site’s Creativity Standards states, ¨Items produced using...
Siraya Tech Introduces New Elastomer 3D Printing Materials, Including Foaming TPU
California company Siraya Tech, founded in 2019 with a focus on material science, customer focus, and agility, develops high-quality 3D printing materials that meet the needs of creators, hobbyists, and...
3D Printing News Briefs, April 12, 2025: RAPID Roundup
The news from last week’s RAPID+TCT in Detroit just keeps on coming! That’s why today’s 3D Printing News Briefs is another RAPID Roundup of more exciting announcements from the trade...