Yesterday we learned that Formlabs obtained an additional $15 million in funding from New Enterprise Associates making it estimated to be worth a billion dollars. We told you about that story and the immediate implications here, and now we have some analysis. This gives it coveted unicorn status amongst startups since so few privately held start-up companies are worth over a billion dollars. At first blush this unicorn status is meaningless. If I sold you a one billionth share of my shoe for two bucks then my shoe would be a unicorn too. The valuation and the resulting unicorn status are decided and conveyed by the same people hoping to profit from selling the business for more later on. Please also note that the people doing this selling and telling are VCs, who make their money allocating risk but almost all live near earthquake fault lines. These people are in the manufacturing inevitability business. So the Tl;dr is, nothing. It is not important that some of the people who invested in Formlabs would now like us to believe it is now worth a billion dollars as opposed to $10. What is important, however?
What are the implications for our industry?
$100 million is the new $3 million. VC’s are now willing to sink over a $100 million in a third 3D printing company after Desktop metal and Carbon. This tells us a number of things. VCs really do believe in 3D printing which is nice. It also tells us that VCs believe that there will be one or two winners in the Additive Manufacturing market. Meanwhile, we see a chaotic open-source FDM 3D printer ecosystem with over 500 entrants. This implies that investors are expecting a mass die-off there of companies. Everyone I speak to expects the great majority of 3D printer companies to die off soon. It’s a near universally held truth, and you know when predicting the future these are almost never correct. What if we see more granular approaches to market and more companies filling more niches? What if specialization and systems integration into custom manufacturing solutions provides an alternative?
Have’s and Have Nots. There are a few companies with oodles of cash, namely Carbon, Desktop metal and Formlabs. This once again illustrates the power the US has in capital allocation. Shapeways moved to the states and the other high funding companies all hail from there. In a globalized world, it is still a great advantage to be a US startup. Other companies such as Ultimaker have tens of millions of funding and seem to be running a marathon rather than running for the exits. Does this mean we are about to see a bifurcation in our industry with the European companies opting to stay private and the Americans going public? EOS is a huge firm that has grown incredibly quickly and yet it all in the hands of its founder Dr. Langer. What are the implications of this?
Will we also see a war of attrition on the desktop? In metal 3D printing people at Formnext, last year seemed to be building dreams and wars of attrition, not parts. Huge investments in stands made us believe that this sky castle was a better long-term bet than the next. Will we seem similar wars of attrition on the desktop? Will the happy few simply outspend those others who took little or no investment?
Kickstarter went from being a universe on and of itself to a byword for optimism induced consumer fraud. Formlabs success is a huge validation of the Kickstarter model and Kickstarters ability to build actual businesses. Far from dream coolers or once omnipresent Pebble watches some smart kids built an amazing business out of a Kickstarter. Will this mean that Kickstarter will once again become a mechanism for funding businesses or will it be novelties all the way down?
Jeff Immelt is probably as connected as one could get in manufacturing. His Rolodex could get Formlabs a strategic seat at the table right at a time when the boards of polymer companies, industrial firms, and large car companies are considering making end-use parts with 3D printing. Whereas Formlabs did enter into production with dental, casting and other applications, Immelt armed with Formlabs new sintering system could open some very exciting doors for Formlabs at the precise moment that they need it.
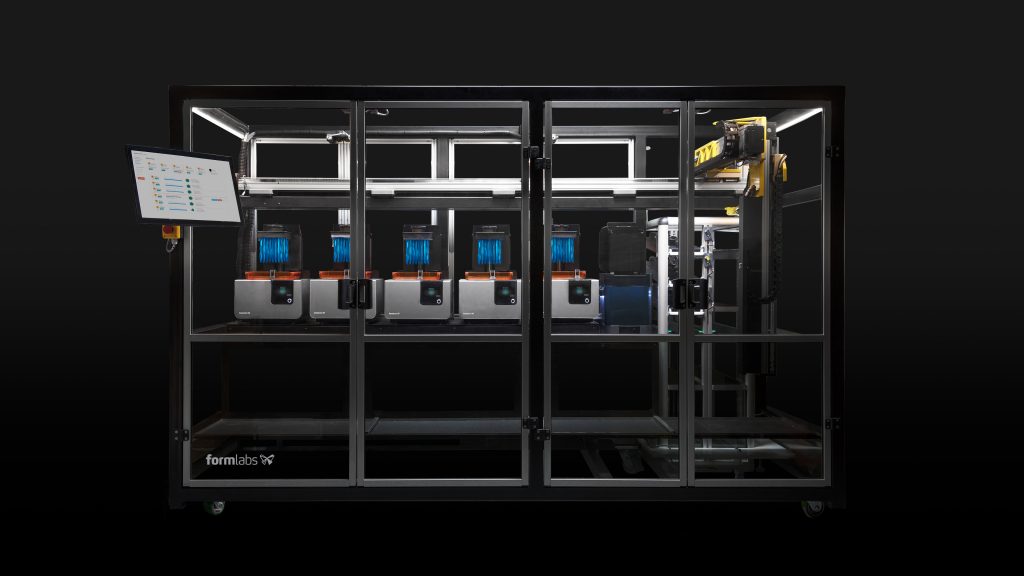
The Formlabs Form Cell Automated manufacturing setup.
Leaping into manufacturing. So far it seemed to me that industrial laser sintering was in the driving seat in “protected things” such as regulated items and medical while FDM would naturally win in manufacturing because of the price and diversity in materials. A more shop floor focus by Formlabs could see the company lead into competition for the manufacturing crown and this would mean a real challenge for FDM and EOS. Meanwhile, it could also decide to continue to dominate a mid-level manufacturing no man’s land where it would be the system in the room at the lab or at the design department. I think that the latter would be a much better bet in growth and margins long term. The wrong choice here could sink them.
Innovator’s Dilemma. If they go the manufacturing route it would mean a big challenge for EOS in the long run as well as a continued challenge for 3D Systems. How will they respond with pressure from below? The latter firm made a patent litigation settlement with Formlabs in 2014 which meant that Formlabs pays them 8% of sales in order to be able to use SLA. This was a win for 3D at the time but I think that the stability and lack of worry it brought Formlabs meanwhile was important. Also, it must have terrified the 3D systems guys each installment to learn what they were getting paid.
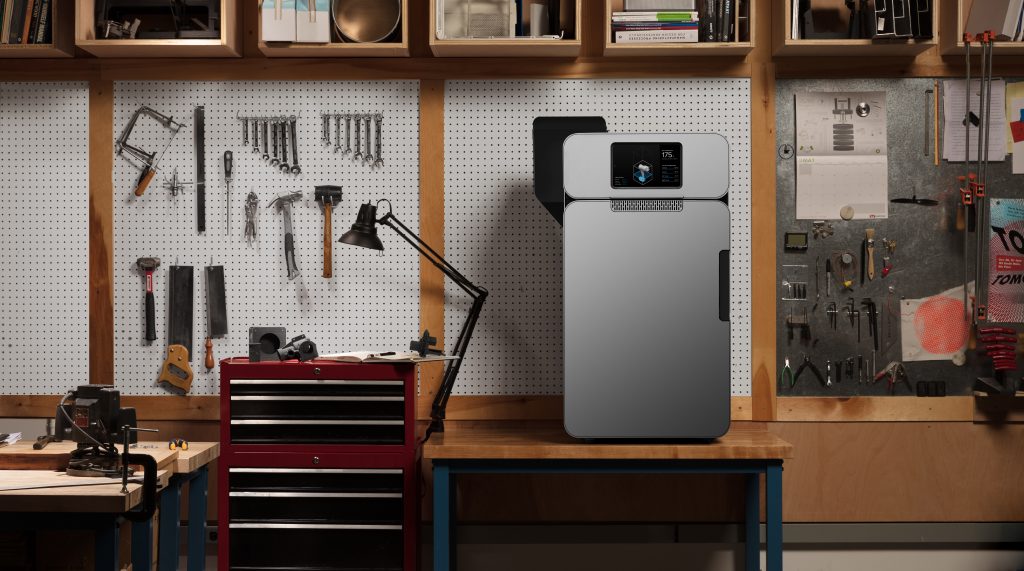
The Fuse Powder Bed Fusion System
$100m. Tucked away in the press release Formlabs mentioned that its run rate was at least $100 million a year, which by the by was 70% lower than my estimates. There are dozens of successful desktop startups that have a few million in revenues. Only a few have 30 million or more. To as an organization make it through several transitions, lose people, find people, find structures and replace them successfully is a challenge. It is a great achievement that a 7-year-old startup in hardware is doing at least sixth of 3D Systems’ revenue. Having the escape velocity to do that makes them well poised for further growth. Also, a billion dollar valuation with over 100m in revenue is less of a stretch than some more fanciful startup valuations recently.
Scale and scope. Additionally, the company has expanded globally with multiple offices and now will extend its technologies to powder bed fusion as well. This will be an additional hurdle to follow. What will be the model of the successful 3D printing OEMs of the future? Service businesses that sell machines and have several technologies as Stratasys is; a jack of all trades as 3D Systems is; highly specialized but complete offering firms such as Ultimaker; a command and control company like EOS; or will it be a scrappy Prusa i3 clone maker that will only do one thing? We still can not know, but I think that Formlabs unique path has given us many implications for our industry. How exactly did they get this far?
Why was Formlabs able to out-execute and get this far?
Closed works too. The riotous open FDM ecosystem is making leaps, bounds, sidesteps, tumbles generally forward. They are open, mostly pretend open source companies that through scrappy competition have made an open landscape that is increasingly being used for manufacturing. Recently I said that Stratasys should go open as well to become more competitive against this ecosystem. But, here is Formlabs and they’re closed. Their software, their printer, their materials. They decide, Apple-like, what is right for you.
Ease of Use. The closed Formlabs approach actually as a user gives you the best UX in 3D printing. The Formlabs printers are still the easiest to use from buttons to software in the industry. UX is not only for conferences and press releases, it matters. I’m not a fan of SLA but damn the thing just works.
Outexecute. Formlabs took what looked to be a rather simple challenge and outexecuted in all regards. Obsessive about quality and experience they went it alone in popularizing SLA and Pro. By holistically looking at the entire experience they performed better for one particular group of people: designers and engineers that needed smooth, highly detailed parts in semi-office settings. Too often companies want to be all things to all men and end up being nothing to no one.
Timing. That Formlabs was the first to tout Pro is largely understood and their focus on not the shop floor and not the desktop but the in-between was in retrospect brilliant. They anticipated what everyone else found out later, that the majority of desktop 3D printer buyers were companies. Also, they waited to bring out the Form Cell to do manufacturing, they didn’t try to sell manufacturing solutions straight off the bat. Being too early can suck too. The company had the only completely finished the prettiest product when it mattered, not to everyone but to enough people to grow.
Contrarian. Being contrarian is good on paper, rarely fun in real life. In 2009 I was at a meeting with around 10 or so industry experts discussing the challenges in 3D printing and every single one of us concluded that stereolithography was dead. We were unanimous in declaring that in the coming revolution of real-world end-use parts, SLA was toast. Ooops.
Lucky. At a time when there were dozens of FDM startups pouring into 3D printing most didn’t even give SLA a second glance. Exotic expensive photopolymers, lasers, it seemed so finicky. To the open source rough and tumble grease and solder folks the whole SLA thing just seemed a tad effete compared to what they were doing. And it is not open source? Lets completely ignore them. This ended up being a godsend to the company and to this day they’ve had spectacularly little competition in desktop SLA.
Right place. Being close to MIT matters, its easier for some of the best people to join you and for you to get advice from some amazing people as well. Location still matters a lot in today’s world.
Max is very smart. 3D Printing has a lot of bright people in it, among those bright people Max is an exceptionally bright one. He’s also relentless in pursuing a vision. For most people and most firms such an approach leads to failure but if someone like Max surrounds himself with the brightest of people then sometimes, just sometimes the future happens.
Essentially there was a firm that sought out excellence at the right time in a contrarian way. By developing a system with good usability they, VC fueled were able to find and keep customers while being left to their own devices. Can’t wait to see what they’ll do next.
Subscribe to Our Email Newsletter
Stay up-to-date on all the latest news from the 3D printing industry and receive information and offers from third party vendors.
Print Services
Upload your 3D Models and get them printed quickly and efficiently.
You May Also Like
Making Space: Stratasys Global Director of Aerospace & Defense Conrad Smith Discusses the Space Supply Chain Council
Of all the many verticals that have been significant additive manufacturing (AM) adopters, few have been more deeply influenced by the incorporation of AM into their workflows than the space...
EOS in India: AM’s Rising Star
EOS is doubling down on India. With a growing base of aerospace startups, new government policies, and a massive engineering workforce, India is quickly becoming one of the most important...
PostProcess CEO on Why the “Dirty Little Secret” of 3D Printing Can’t Be Ignored Anymore
If you’ve ever peeked behind the scenes of a 3D printing lab, you might have caught a glimpse of the post-processing room; maybe it’s messy, maybe hidden behind a mysterious...
Stratasys & Automation Intelligence Open North American Tooling Center in Flint
Stratasys has opened the North American Stratasys Tooling Center (NASTC) in Flint, Michigan, together with automation integrator and software firm Automation Intelligence. Stratasys wants the new center to help reduce...