Researchers from Chile and Spain used a variety of samples to study settings for 3D printing samples in ‘Parametric Study of 3D Additive Printing Parameters Using Conductive Filaments on Microwave Topologies.’ While accessibility and affordability has accelerated exponentially for 3D printing users over the past few years, skill in setting parameters—along with limits in lower-level hardware—is an ongoing topic; here though, the research team adds another level of complexity to the equation in 3D printing with conductive filaments.
While there are many previous studies regarding 3D printing with a variety of different techniques, and parameters, conductivity is rarely further explored—with most data centered around dielectric filaments; however, as affordability in materials continues to expand, use of conductive filament merits more study regarding characterization, performance, and settings.
“Depending on the specific software used and the printer, each prototype can be constructed in many different ways in terms of percentage of infill, wall size, and height of the layer and infill pattern,” state the researchers.
Remarking on the few compatible filaments on the market for basic 3D printing, the researchers decided to use 1.75-mm Electrifi conductive filament in this study, offering a resistivity of 0.006 Ω⋅ cm—chosen due to its very high level of conductivity in comparison to the few others available.
Characterization was performed with a microstrip transmission line, using a substrate targeted toward conductive filament printed on a modified Ocular 3D printer. For ultimate optimization, the team customized the hot-end with a CNC machine, aiming toward improved filament flux and preventing any possible damage or clogging.
“Before the characterization of the 3D-printed microstrip lines, a reference 50 Ω microstrip line is made with copper foils over the previously characterized PLA,” stated the researchers. “The dimensions of the printed PLA substrate are 70 mm ×70 mm ×1.7 mm.

Measured transmission losses of the reference transmission line over the PLA and compared with a standard microstrip line etched on FR-4.
“To compare the measurements and to remove the dielectric losses introduced by the substrate, the transmission losses of the copper microstrip line etched on the same PLA substrate was subtracted from the measurements results of the fully 3D microstrip line transmission coefficient.”
Printer settings were established once microstrip line dimensions were outlined, with infill percentages shown in the figure below:
Concentric infill, triangle infill, and zig-zag infill were chosen, and patterns were constructed with layer heights of 0.2 mm, 0.25 mm, and 0.3 mm—meant to offer stability during fabrication. Lower layer heights proved less stable in prior experiments. Overall, the team 3D printed a variety of 27 microstrips.
Two different antennas were built in the end: one microstrip patch and one pyramidal horn. The first was meant to be like a typical manufactured one, while the other was meant to test out both an aperture antenna topology with a waveguide feed as well as a method for assessing the efficacy of a lighter-weight product and its effect on performance. The team tested both antenna in an anechoic chamber.

Microstrip 3D-printed patch antenna. a) Isometric layout. b) Top view of the constructed microstrip patch antenna.
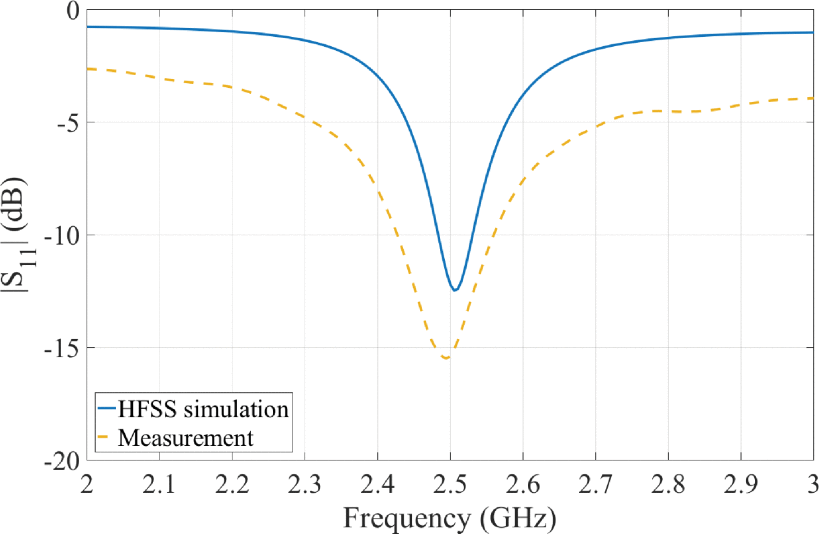
Simulated and measured reflection coefficient |S_{11}| as a function of frequency of the microstrip 3D-printed patch antenna.
“The low-weight pyramidal horn antenna showed good agreement in comparison with the simulated antenna, showing lower losses than the microstrip antenna. This can be explained by the fact that the values of currents for waveguide topology tend to be lower than in a resonant topology such as the microstrip patch antenna,” concluded the researchers. “As the low-weight horn antenna has a similar behavior to that of its fully metallic equivalent, it can be very useful for applications where weight is an important issue, such as antennas with critical mechanical movements or antennas on unmanned aerial vehicles (UAV).”
3D printing parameters is a constant source of challenge—and study—for users involved in a wide array of projects from processing parameters and testing cellular structures to optimizing parameters for use with other materials, and investigating typical issues like surface roughness.
What do you think of this news? Let us know your thoughts! Join the discussion of this and other 3D printing topics at 3DPrintBoard.com.
[Source / Images: ‘Parametric Study of 3D Additive Printing Parameters Using Conductive Filaments on Microwave Topologies’]Subscribe to Our Email Newsletter
Stay up-to-date on all the latest news from the 3D printing industry and receive information and offers from third party vendors.
Print Services
Upload your 3D Models and get them printed quickly and efficiently.
You May Also Like
U.S. Navy Lab Uses 3D Printing to Reduce Tooling Lead Time By Over 90%
The F-35 Lightning II Joint Program Office (JPO), responsible for life-cycle management of the key fifth-generation joint strike fighter (JSF) system used by the U.S., its allies, and its partners,...
Etsy Design Rule Change Reduces Selection of 3D Printed Goods
Online marketplace Etsy has implemented a rule change requiring all 3D printed goods on the site to be original designs. The update to the site’s Creativity Standards states, ¨Items produced using...
Honeywell Qualifies 6K Additive’s Nickel 718 for 3D Printed Aerospace & Defense Parts
6K Additive is renowned for manufacturing sustainable additive manufacturing (AM) powder, and offers a wide portfolio of premium metal and alloy powders that include titanium, copper, stainless steel, and nickel,...
MetalWorm Sells WAAM Systems to Research Institutes in Brazil and Malaysia
Turkish WAAM firm MetalWorm has sold a system in Malaysia and another in Brazil. This is an excellent example of a few emerging trends in additive. Firstly, WAAM was experimented...