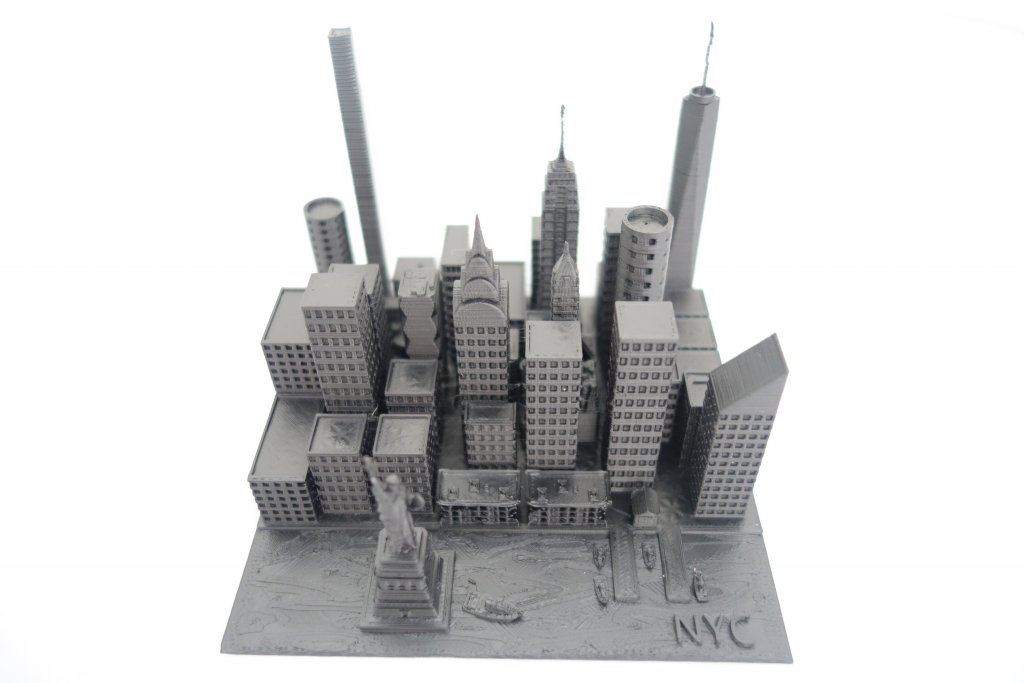
“This industry will bring a lot of improvements to people, but 3D printed objects are made with different plastics, and these material have a terrible impact on the environment. Indeed, only a small proportion of plastic waste are well recycled and reused during ten to fifteen cycle as they should be, the rest are incinerated or placed in landfills. Moreover, a huge quantity of plastic never reaches the recycling bin and ends in nature which represents a critical pollution problem.
“NefilaTek is a new company that makes Eco-friendly 3D printing filament from recycled plastic. The idea is to decrease the environmental impact of the 3D printing industry by making high-quality filament from plastic waste from Montreal. Reconditioning used plastic into useful objects is the main challenge of our time to reduce plastic pollution and overproduction.”
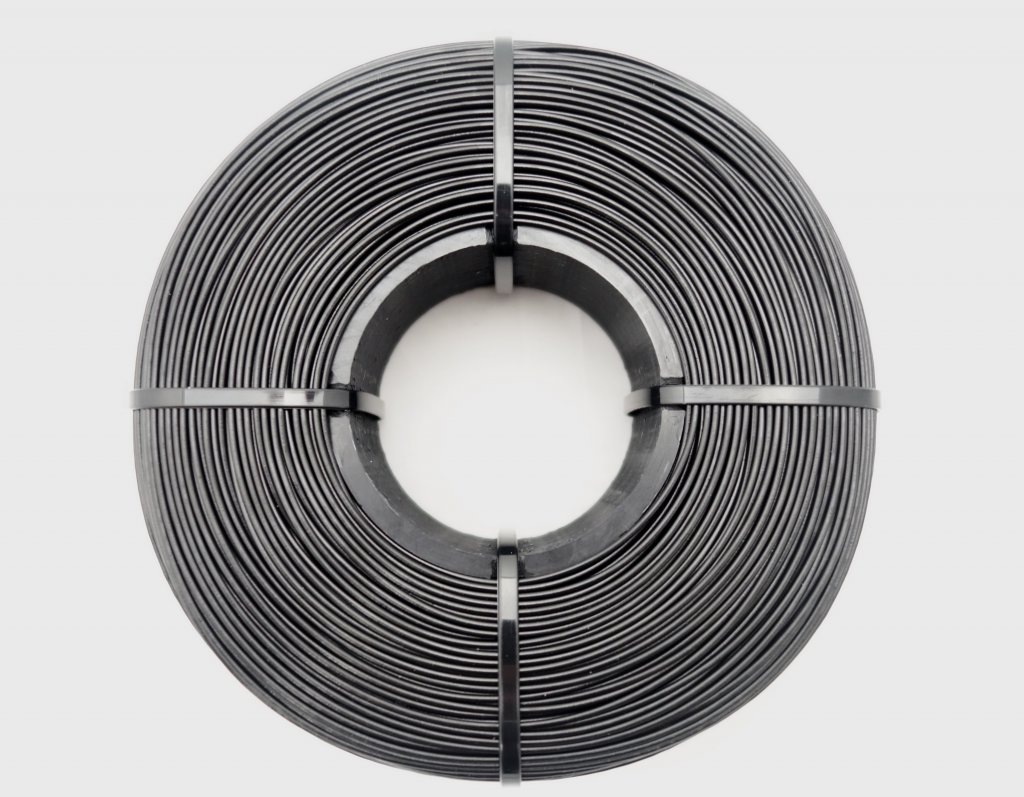
No spool filament is also a great benefit.
The company did tell us that, “All our filaments are made from 100% recycled raw materials, we don’t have any virgin plastic in our filament.”
R&D engineer Angel Chauffray did say something that makes us happy which is that “they’ve reached an industrial tolerance for the filament diameter 1.75mm +/- 0.05, it performs at least as well as other filaments with this tolerance.”
Subscribe to Our Email Newsletter
Stay up-to-date on all the latest news from the 3D printing industry and receive information and offers from third party vendors.
You May Also Like
NSF Awards Kentucky $1M for Advanced Manufacturing
The National Science Foundation has awarded a $1 million grant to the University of Louisville for the Advancing Manufacturing and Building Construction Technologies (NSF AMT) project. This initiative is part...
3D Printing News Briefs, May 11, 2024: 3D Printed Stent, Tower, Sculptures, & More
We’re starting off with medical research in today’s 3D Printing News Briefs, as researchers in Korea used CT images and 3D printing to fabricate an educational simulator for a mastoidectomy....
3D Printing Unpeeled: Wind Turbines, Probiotics and Lenses
TPI Composites, ORNL and Ingersoll Rand are working to make wind turbine tooling segments that can be 18.3 meters long. These elements also include resistive wires that help keep the...
Tethon 3D Releases Cost-effective Bioprinter
Tethon 3D, known for its ceramic-loaded DLP materials, custom resins, and DLP 3D printers, has recently released a bioprinter. Vat polymerization printers like DLP systems have been widely used by...