The recently published ‘Topology optimization and 3D printing of multimaterial magnetic actuators and displays’ opens up the topic of refining actuation systems for greater functionality, as they will progressively be required to do more tasks by demanding users. In this study, the researchers offer a comprehensive toolkit for multiobjective topology optimization and multimaterial drop-on-demand 3D printing for actuators.

Overview of the specification-driven 3D printing process. The structure of individual actuators (or the arrangement of multiple actuators) is optimized using a multiobjective topology optimization process. Note that, in general, the final optimized structure can be of any arbitrary shape as shown. The optimization uses the bulk physical properties of the individual materials and the functional objectives as inputs. The generated optimized voxel-based representation of the structure is used by the printer to fabricate the optimized structure using a drop-on-demand inkjet printing process. This allows high-dimensional designs to be automatically generated and fabricated with minimal human intervention. In this work, a rigid acrylate polymer (RIG), an elastic acrylate polymer (ELA), and a magnetic nanoparticle (Fe3O4)/ polymer composite (MPC) are the main materials used. The contrast in the optical, mechanical, and magnetic properties is used to simultaneously optimize the visual appearance and the actuating forces while generating the voxel-level design.
Created from a composite of nanoparticles and polymers, the actuators also have soft components integrated into their structure—with the topology optimizer assigning materials, along with perfecting physical deflection and appearance. The mission of this research is to ‘advocate’ better sensing, actuation, and computation inside robotic materials with the overall goal to expand their functionality further. And as so many scientists often are inspired by nature, the authors mention here the example of cuttlefish, with an actuation system that manipulates both the physical and aesthetic and allows for required camouflage. Imitating such biology presents challenges though due to complexities in living structures.
“Many examples of contemporary actuation systems of high complexity consist of microscale actuators tiled into regular arrays,” stated the researchers.
“However, optimizing these actuation systems (with identical actuators) for power consumption, low footprint, and process reliability still requires a substantial amount of time.”

Actuator characteristics—Forces, displacements, and actuation bandwidth. (A) To characterize the actuator performance, we used the fundamental design with a small change. Here, only a fraction of the panel thickness, tp, is filled with MPC, denoted by l. The following results were obtained with a rectangular panel of size lp1 × lp2 = 8 mm × 9 mm, thickness tp = 1 mm, l = 0.15, and hinges with dimensions Wh = 0.5 mm, lh = 1 mm, and th = 0.25 mm. (B) Measured blocking forces of four identical devices shown as a function of the distance from the 2″ by 2″ by 0. 5″ magnet along with corresponding simulation results (see magnet, measurement setup, and simulation details in Materials and Methods). (C) Measured angular deflections of three identical devices as a function of distance from the magnet. (D) Optically tracked angular displacements as a function of time for actuation at frequencies from 0.01 to 10 Hz. (E) Angular displacement amplitudes as a function of frequency for three devices. (F) The apparent large-amplitude bandwidth depends on the setup of the magnetic field since the force experienced by the actuator itself varies with the displacement. This is highlighted in this plot with two cases—in one case, the force experienced by the actuator increases monotonically with angular displacement (⋆), and in the other case, there is a stable angular displacement when the panel aligns with the direction of maximum gradient (⋆⋆). See fig. S5 for corresponding time curves and details of the setup.
Manual designs can be arduous to produce, and the researchers point out in this study that this is where topology optimization techniques fit in, with ‘gradient-based methods’ offering good results for many different applications, to include design of not only photonic crystal structures but also passive and active compliant mechanisms and elastic metamaterials; however, such methods also present challenges, leaving the team to integrate a simulated annealing (SA) strategy.
SA has been useful previously in the design of trusses, but the research team also had to consider issues like droplet spreading and use of the proper materials, as well as the role they play. They chose to use 3D printing to create the actuators due to benefits such as accuracy and complexity in structures and the ability to use varying materials. Printing was performed on a custom drop-on-demand 3D printer:
“The specific actuator design we demonstrate is a planar, rigid structure consisting of, for instance, 186 by 186 by 160 cells that can each be filled with either a transparent rigid polymer or a dark magnetically responsive polymer,” state the researchers.
The optimizer is responsible for placing the materials in relation to properties, with both input images and target tilting angles key in the presentations for this study. Samples were printed with UV-curable inks with several different properties: optical, magnetic, mechanical with the following materials:
- Rigid acrylate polymer (RIG)
- Elastic acrylate polymer (ELA)
- Magnetic nanoparticle/ polymer composite (MPC)
“The appropriate inks are deposited by the printhead for each voxel from the generated stack of layered bitmaps containing the material assignments. Subsequently, after deposition of inks in each pass, a UV–light-emitting diode (LED) array is used to cross-link the inks using free-radical photopolymerization,” state the researchers.
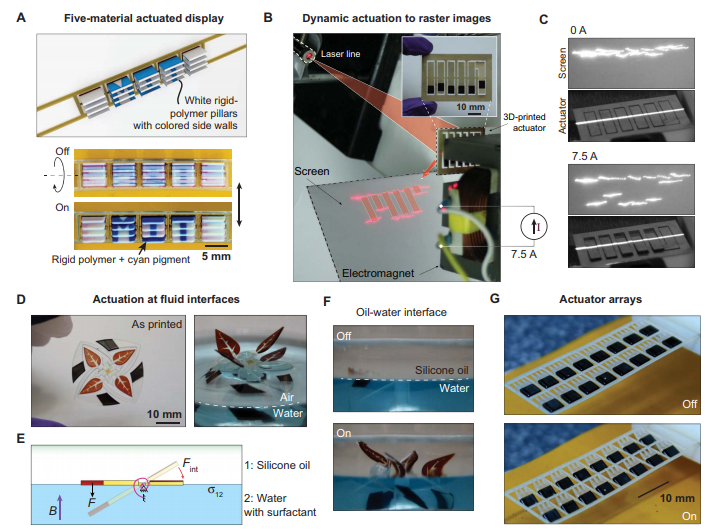
Applications of 3D-printed multimaterial soft magnetic actuators. (A) Five-material actuated display. Each panel consists of the design shown in Fig. 2G, on top of which four vertical walls of a white rigid polymer are printed. The side walls are patterned based on the image to be displayed. Here, the letters “M”, “I”, and “T” are chosen to be patterned on the side wall. An applied magnetic field generates a torque on the panel, allowing different sides of the walls to be visible from a fixed viewing angle. (B) A six-element array of mirrors is mounted next to an electromagnet powered by a current source (0 to 7.5 A). The torque experienced by each individual panel is controlled by the position of the MPC regions. Different images are rastered on a screen by shining a laser line across the mirror array. Here, the panels are designed to raster the MIT logo. See fig. S7 for a schematic of the setup. (C) The two sets of images show the still photographs of the screen and a snapshot of the mirror array with the electromagnet turned off and on (7.5 A). Dynamic actuation using a linear current ramp is shown in movie S1. (D) To demonstrate the use of the magnetic actuator arrays in liquid interfaces, we design water lilies that are positioned on water interfaces. The petal patterns are printed using three layers of the magnetic ink, and torsional hinges are made from the elastic polymer. Left: The top view of the as-printed part is shown where the solid dark regions are the actuating regions made with MPC. Right: When placed on the air-water (with 0.2% FC4430, s = 20.9 mN/m) interface, the leaves are held flat because of the interfacial tension of water. While it can be deformed by an applied field, as shown, some panels return to their flat position easily when the water is disturbed. (E) When tested in conditions with lower interfacial tension s12 = 3.7 ± 0.78 mN/m (interface of silicone oil and water with 0.2% FC4430), the array can be actuated back and forth reliably (movie S2). The schematic shows the restoring nature of the interfacial tension. (F) Experimental results of actuation at the silicone oil-water interface. (G) An array of 16 identical actuators with serrated edges is shown with and without an applied magnetic field (design in fig. S9). (Photo credit: S.S. and D.S.K., MIT.)
The research team did note ‘demands’ in the process for more functional ink—although they did discover during their experimenting that increasing actuation force but reducing power was simple, requiring them only to refine loading of the ink nanoparticles. They did also note instability upon loading nanoparticles past 12 wt %, along with clogging in the nozzles.
“Despite the remaining challenges in developing new inks and materials, a wide range of materials can be currently fabricated using this process: UV-curable rigid and stretchable acrylate polymers, liquid electrolytes, and conductive and semiconducting films,” concluded the researchers. “Using similar printing processes, other groups have demonstrated a wide range of different actuators including electrically actuated dielectric elastomer actuators.”
Voxel-level flexibility in material choices from both the fabrication and shape optimization perspective enables the first steps toward fully automated design and fabrication of complex, multimaterial devices.
3D printing offers a vast landscape for innovation for in the creation of materials—from metal to graded materials to biofilms, along with many different types of actuators. What do you think of this news? Let us know your thoughts! Join the discussion of this and other 3D printing topics at 3DPrintBoard.com.

Material property library. (A) The transmission through the MPC shown as a function of the wavelength for films of varying thickness, measured using a spectrophotometer. (B) The transmission through the clear rigid material shown as a function of wavelength for multiple film thicknesses. (C) Magnetization versus applied magnetic field for the MPC measured at room temperature. Magnetic nanoparticles make up ∼12% of the overall weight of the MPC. Typical mechanical stressstrain curves for the ELA, MPC, and the rigid polymer (RIG) are shown in (D) to (F), respectively. Elastic moduli of the polymers at linear strains, averaged from three samples each, vary significantly—ELA (528 kPa), MPC (507 MPa), and RIG (1290 MPa). (G) The schematic shows the fundamental hinge-based design with panel length lp and thickness tp. In this design, the panel is sectioned into two equal portions of RIG and MPC. The panel is attached to rigid boundaries on two sides with ELA torsional hinges of length lh, width wh, and thickness th. On the application of a magnetic field, the magnetic portion of the panel generates a torque. This is used as the fundamental block in the manually designed samples. (H) Image of a 2 × 2 array of panels each with two axes of rotation. The dark brown regions of the image show the MPC material, and the translucent portions show the rigid materials. The elastic torsional hinges are nearly identical to the rigid polymer in appearance. On the application of a magnetic field, each panel exhibits a unique combination of two-axis angular rotations. The top view of the flat as-printed sample is shown on the left. (Photo credit: S.S. and D.S.K., MIT.)
Subscribe to Our Email Newsletter
Stay up-to-date on all the latest news from the 3D printing industry and receive information and offers from third party vendors.
Print Services
Upload your 3D Models and get them printed quickly and efficiently.
You May Also Like
South Korean 3D Printing Industry Sounds Alarm Over Data Leakage
An article recently published in BusinessKorea has highlighted that small and medium-sized enterprises (SMEs) utilizing additive manufacturing (AM) in South Korea are increasingly worried about the threat of leaking intellectual...
MetalWorm Sells WAAM Systems to Research Institutes in Brazil and Malaysia
Turkish WAAM firm MetalWorm has sold a system in Malaysia and another in Brazil. This is an excellent example of a few emerging trends in additive. Firstly, WAAM was experimented...
From Rapid Qualification to On-ship 3D Printing, ABS Sets New Standards in Maritime AM
The American Bureau of Shipping (ABS) is taking significant strides in advancing additive manufacturing (AM) within the maritime sector. Amidst increasing interest and the need for modernization, ABS has been...
HAMR Industries Gets a FormAlloy X5R at Neighborhood 91
The Neighborhood 91 (N91) cluster of additive manufacturing firms in Pennsylvania has acquired a FormAlloy robot arm X5R Directed Energy Deposition (DED) system; specifically HAMR Industries. The X5R can work...