In ‘3D printing of continuous flax fiber reinforced biocomposites for structural applications,’ authors A Le Duigou, A. Barbé, E. Guillou, and M. Castro examine recent, increased interest in using natural materials like flax in 3D printing with filaments like PLA.
Focusing on FDM 3D printing, the researchers experimented with creating biocomposites with optimized mechanical properties through the inclusion of continuous flax fiber/PLA (cFF/PLA) composite filaments. They created a customized extrusion technique for use with the composite, which the authors state ‘evidenced a homogeneous distribution of yarn within the cross-section, while the twisted flax yarn led to fiber-rich areas at mesoscale.’
The research team was interested in creating a new composite with flax due to a ‘promising range’ of mechanical properties—often challenging to find with all the suitable qualities required. They explain that many biocomposites are popular today, but still possess less-than-suitable mechanical properties when using many different natural fibers.
“The cFF/PLA showed tensile modulus and strength values that exceeded the only available published result on continuous natural fiber printed composites by >4.5 times,” stated the researchers. “Tensile properties were in the same range as those for continuous glass fiber/PolyAmide (PA) printed composites, paving the way for the use of biocomposites in structural applications. Their weakest point was their transverse properties that remained poorer than similar flax/PLA thermocompressed composites.”
Other fiber composites such as glass, carbon, and aramid are also being studied to improve 3D printing performance, as materials are ‘impregnated to create improved structures. Using their on-site customized Prusa i3 3D printer, an Arduino card to control fan rotation, and Simplify3D software, the researchers created samples that could then be evaluated and compared with results of previous studies.
As a yarn, flax is an obvious choice for a composite to be featured in textile applications—allowing for better strength in weaving; however, the authors point out that fiber bundles were observed in ‘twisted architectures,’ affecting both the porosity content and overall microstructure.
“In addition, the flax yarn exhibited a deviation from the center of the filament that appears to be due to the co-extrusion die. Indeed, during the co-extrusion process, the polymer flows perpendicular to the flax yarn, which results in its positioning at the edge of the filament,” stated the authors.
“Trial tests have shown that a fiber volume content above 35% within filaments led to difficulties in obtaining high-quality printed samples. Thus, in the present work the developed cFF/PLA filaments contained a lower volume fraction of 30.4 ± 0.8% (wf ≈ 34.5%), which was close to commercial high-performance carbon/polyamide filaments [15,16]. Printing filaments did not affect fiber content and therefore cFF/PLA biocomposites had a similar fiber fraction than those of filaments.”
Longitudinal properties were improved in comparison to:
- Pure PLA (×7 for stiffness and ×4.5 for strength)
- Discontinuous natural fiber reinforced 3D printed biocomposites (×11 for stiffness and ×10 for strength)
- Available data on continuous jute/PLA printed biocomposites (×4.5 for stiffness and ×4.5 for strength)
The researchers think these properties could be explained by intrinsic, higher mechanical properties of flax, the higher aspect ratio of the fiber yarns, and better fiber content and homogeneity overall.
“The non-linear tensile behavior was found to be typical of natural fiber unidirectional composites with properties that were comparable to those of long flax fiber composites manufactured by thermocompression, VARTM, and AFP, as well as continuous glass/PA composites produced by a commercial 3D printer. Such high measured performance opens up 3D printed biocomposites to structural applications,” concluded the researchers.
“The weakest point of cFF/PLA printed composites was their transverse properties that remained lower than similar flax/PLA thermocompressed composites. The damage mechanism observed during tensile tests was similar to that observed in continuous synthetic fiber/polymer printed composites with filaments unwinding.”

(a) Microstructure of a continuous flax fibre/PLA (cFF/PLA) filaments, (b) SEM microphotograph of cross section of untested cFF/PLA samples, (c) cFF/PLA transversally printed (90°) and (d) cFF/PLA longitudinally printed (0°). Details of panel d showing (e) loops overlap and (f) regular loops.
Materials science in relation to 3D printing has come a long way just in the past few years. Although popularity is ever-increasing with desktop users, researchers and industrial manufacturers continue to use filaments like PLA, but are now accentuating them with a variety of other materials to create composites with graphene, continuous fibers, and even wood.
Find out more about the use of natural fibers like flax here. What do you think of this news? Let us know your thoughts! Join the discussion of this and other 3D printing topics at 3DPrintBoard.com.
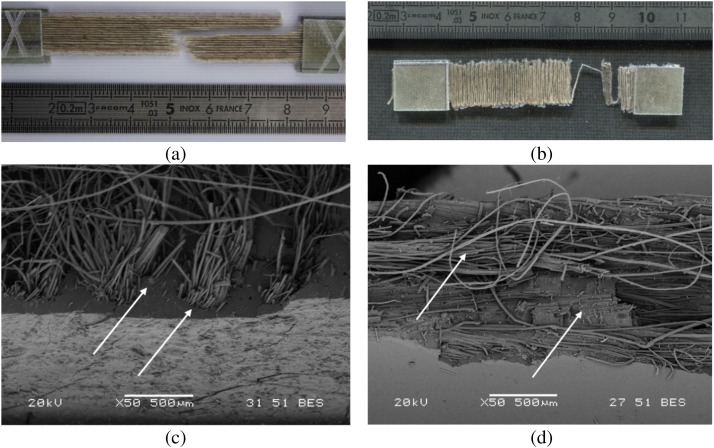
Macroscopic image of (a) longitudinal, (b) transverse fracture of cFF/PLA printed parts. SEM microphotograph of (c) longitudinal transverse fracture of cFF/PLA printed parts and (d) transverse fracture of cFF/PLA printed parts. White arrows evidence fibre bundle debonding and matrix failure.
Subscribe to Our Email Newsletter
Stay up-to-date on all the latest news from the 3D printing industry and receive information and offers from third party vendors.
Print Services
Upload your 3D Models and get them printed quickly and efficiently.
You May Also Like
Heating Up: 3D Systems’ Scott Green Discusses 3D Printing’s Potential in the Data Center Industry
The relentless rise of NVIDIA, the steadily increasing pledges of major private and public investments in national infrastructure projects around the world, and the general cultural obsession with AI have...
Formlabs Teams Up with DMG MORI in Japan
In late June, Nick Graham, Chief Revenue Officer at Formlabs, announced on LinkedIn that the company had partnered with DMG MORI, one of the world’s leading machine tool companies, to...
EOS in India: AM’s Rising Star
EOS is doubling down on India. With a growing base of aerospace startups, new government policies, and a massive engineering workforce, India is quickly becoming one of the most important...
3D Printing News Briefs, June 25, 2025: R&D Materials, 3D Printed Veneers, & More
In today’s 3D Printing News Briefs, 3DXTECH has launched a program that gives customers early access to experimental materials, and the first Lithoz CeraFab Multi 2M30 in the Czech Republic...