In ‘Designing for Shape Change: A Case study on 3D Printing Composite Materials for Responsive Architectures,’ Elena Vazquez, Benay Gursoy, and Jose Duarte present details on customizing parts to optimize shape changing behavior. Forging straight ahead into the 4D, the Pennsylvania State University researchers delve more comprehensively into smart materials and how they are able to morph depending on user requirements and changes in the environment—whether due to temperature, moisture, or other elements.
Looking into past studies regarding the ability for building systems to become enhanced due to ‘shifting environmental conditions,’ the authors became inspired, envisioning new concepts for architectural 4D frameworks—along with embracing the concept of unpredictability within these frameworks that can be viewed as opportunities to learn. Their question, and mission, became not only how to harness such capabilities, but also how to control them as they formed a unique ‘hydroactive architectural skin system’ that would morph in reaction to moisture in the air. The materials are a 3D printed, wood-based, bio-composite. With customized settings, the team was able to study the behavior of the material, along with comparing notes to previous 4D experiments using wood.
“In the case of wood-based composites, 3D printing enables the design of specific patterns for layers that lead to differential swelling and then to shape-change,” state the researchers.

Six 3D printed bilayer composite samples of PLA with varying tool path geometry and their response to being immersed in hot water.
In setting parameters for 3D printing, the team used the Silkworm plug-in for Grasshopper to customize the G Code—thus establishing control not only over the nozzle, but also the printing pattern. This means being able to manipulate the fiber orientation and shape-changing dynamics. Additional identified parameters are as follows:
- Number of print layers
- Layer height
- Order for active and constraint layers in the bilayer configuration
- Road distance controlling porosity
“The 3D printing settings that we control also through custom G Code include bed and nozzle temperatures and the 3D printing speeds,” state the researchers. “Another parameter that is in play while 3D printing is the filaments used, and whether the objects are printed using a single material or with multiple materials.”
In beginning the case study, the team 3D printed some samples with PLA to have a baseline for comparing. The next set of ‘explorations’ included the use of Laywood, a wooden material made up of 40wt% wood fiber. The authors state that samples printed with Laywood offer an elongation rate of 106% if substantial amounts of humidity are present. Activators are both temperature and humidity, with the amount of time samples were exposed directly corresponding to the level of effect.

The shape changes of the six bilayer wood-based bio composite samples with 10 minute intervals for a total duration of 40 minutes.
Aware of the effect that both porosity and print angles had on activated shapes, the researchers created 175 x 75mm prototypes in the form of combined triangles. They discovered that samples subjected to humidity deformed from 70 minutes onward.
“To assess how the samples keep changing shape over hours instead of minutes, we recorded shape-change of prototype B over a period of 7 hours,” said the researchers.
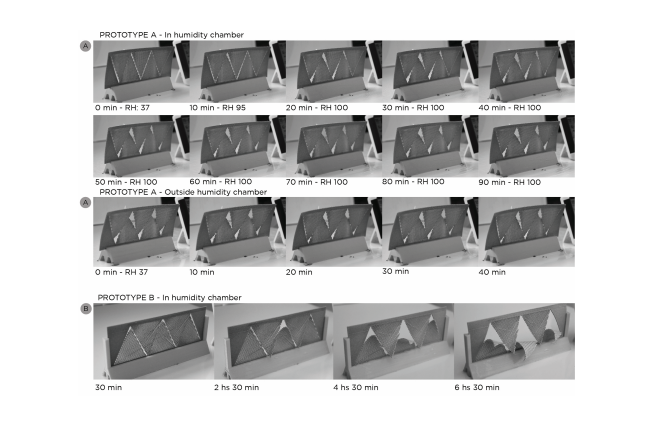
The shape-changes of the Prototype A with 10 minute intervals, B) The shape-changes of Prototype B with 2 hours intervals.
During their experimenting, the researchers discovered that they could change porosity levels—which allowed them to control the 4D models. They were also able to use the study parameters to control the level of transparency in the ‘architectural skins’ they created. As many other research studies before this have made note of, 3D printing will allow for the fabrication of complex geometries. In relation to this project, the authors note that many other types of material could be used in creating the architectural skin system. In noting also that single-material prototypes deformed completely when subjected to humidity, the authors suggest that in the future a multi-material approach could be more successful
“In the explorations conducted, design decisions orchestrate the interdependence between geometry -from tool path to overall form, 3D printing settings, and time, as the added dimension in the design process. Time, in this study represents shape transformation, and we argue that a systematic material exploration and computation brings us one step closer to controlling this dynamic behavior in designing for shape-change,” concluded the researchers.
“We postulate that once the shape-changing behavior is formalized through systematic material explorations, material intelligence can be embedded in parametric computer models. This constitutes a next stage in this research and can enable us to explore design variations in the computer prior to materialization. It will also allow us to create computer simulations to assess the performance of the architectural skin designs in controlling air flow, daylight and interior temperature.”
Scientists involved in 3D printing research are hard at work around the world improving and perfecting different ways to use the technology. Along with making continually new strides in software and hardware for 3D printing, the study of materials is a strong center of focus—and composites have become very popular with strengthening metals used in the process, from carbon nanotube composites to PEEK composites or trials with continuous fiber.
[Source / Images: ‘Designing for Shape Change: A Case study on 3D Printing Composite Materials for Responsive Architectures’]Subscribe to Our Email Newsletter
Stay up-to-date on all the latest news from the 3D printing industry and receive information and offers from third party vendors.
Print Services
Upload your 3D Models and get them printed quickly and efficiently.
You May Also Like
Nikon SLM Solutions Sells SLM 500 to Primary Weapon Systems to Expand Suppressor Production
Primary Weapons Systems (PWS) is a Boise, Idaho-based manufacturer of suppressors, firearms, and related components. A subsidiary of Vigilant Gear and a sister company to aftermarket Glock slide manufacturer Lone...
3DPOD 261: Tooling and Cooling for AM with Jason Murphy, NXC MFG
Jason Murphy´s NXC MFG (Next Chapter Manufacturing) is not a generalist service; instead, the company specializes in making tooling. Using LPBF and binder jet, the company produces some of the...
HP and Firestorm Labs Form Partnership to Use Multi Jet Fusion 3D Printers in Deployable Factories
HP Inc., maker of a range of additive manufacturing (AM) solutions including the Multi Jet Fusion (MJF) ecosystem, has announced a partnership with Firestorm Labs, a developer of containerized, deployable...
3D Printing News Briefs, July 2, 2025: Copper Alloys, Defense Manufacturing, & More
We’re starting off with metals in today’s 3D Printing News Briefs, as Farsoon has unveiled a large-scale AM solution for copper alloys, and Meltio used its wire-laser metal solution to...