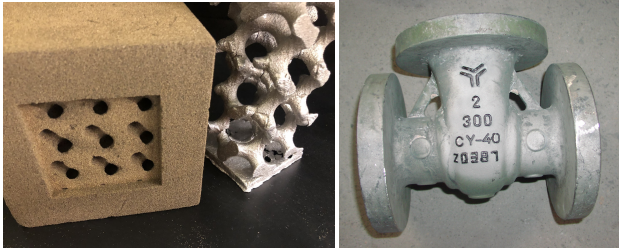
Complex casting with 3D printed mold (left) and traditional casting with traditional cores and molds (right)
Sand casting is a technology with a long history, but it’s being reinvented by additive manufacturing. 3D printed sand molds allow for highly geometrically complex castings, and in a paper entitled “Economies of Complexity of 3D Printed Sand Molds for Casting,” a group of researchers outlines the benefits of using additive manufacturing in sand casting:
- the integration of structural elements such as periodic lattices in order to optimize weight versus strength
- the structural inclusion of unique features such as embossed part numbers and/or other details of the production history
- complex geometries that generate new casting applications not possible previously
In the paper, the researchers describe a complexity evaluation tool that scores CAD models to determine the most economical casting approach based on slicing and 2D geometry evaluation. The three potential outcomes include traditional sand casting; AM-enabled sand casting and a hybrid of the two with 3D printed cores in traditional casting flasks.
“Four algorithms were developed that all began by slicing each of the benchmark STL files and performing analysis per layer producing an average complexity across all layers,” the researchers explain. “This process was repeated for three orientations of each part and the results were averaged including: an unrotated case, a rotated case 90 degrees in X axis and rotated 90 degrees in Y axis. The rotations were completed in order to detect a complexity bias relative to orientation. For each orientation, the complexity numbers from all layers were individually calculated and then the total was divided by the number of layers for a mean value that was independent of the number of slices selected. By using more layers, the accuracy was expected to improve by improving the statistical sampling; however each additional layer meant an increase in the duration of computation.”
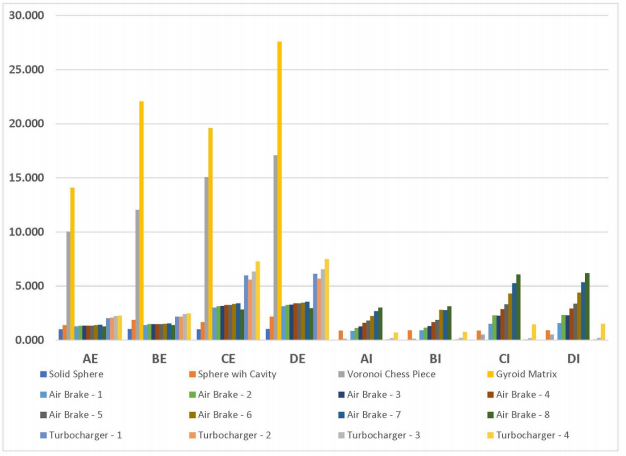
The complexity factor values for Algorithms AD are shown for each of the benchmark castings. E indicates exterior. I indicates interior.
Algorithm A was the simplest and summed the number of contours detected for each layer. Algorithm B was similar to A except that instead of incrementing the sum of contours, a ration was calculated and added to a running sum. Algorithm C summed the number of contours but also included a sum of concavity defects that were sufficiently concave. Algorithm D was an aggregate of the other algorithms: the contours, the ratio of perimeter over area and the number of concavity defects summed together.
16 structures were selected for casting, ranging in complexity from simple spheres to a gyroid matrix and a Voronoi tesselation chess piece. The different castings were run through the complexity software, and the resulting data was compared to complexity scores assigned by previous work in which the scores were generated manually and correlated well with the decision as to which casting process was most suitable.
Of the four algorithms, Algorithm D gave values that “provide a decision boundary that was in line with the intuition of the authors as well as obvious extreme cases (sphere as a case of simplicity or a gyroid matrix for a case that can only be cast with the help of 3D printing),” according to the researchers.
“This layerwise complexity factor was compared to a known complexity factor for conventional casting fabrication method and showed similar results but without requiring design knowledge of the traditional methods,” the researchers state. “The economics of complexity and quantity were shown for a traditional casting tooling method and then compared to three methods that involved additive manufacturing.”
The researchers presented four options:
- Traditional manufacturing (TM): Traditional subtractive processes to make molds / cores.
- 3D Sand Printing (3DSP): Complete sand printing of both molds and cores.
- 3D Sand Printed Core (3DSPC): 3D sand printing of cores and conventional pattern making for the mold cope and drag.
- FDM Patternmaking (FDMP): Conventional core making and 3D printing using fused deposition modeling of hard patterns for conventional mold making with the advantage of faster mold fabrication.
The most economical method depended on the complexity and quantity of the parts being made. For example, for an air brake, 3DSP was the most cost effective regardless of level of complexity. However, 3DSPC was the most cost effective for more complex objects or objects in quantities of 100 or higher. For castings of low complexity, FDMP was the best choice, while for quantities of 1,000 3DSPC was the most cost effective for the full range of complexities.
Authors of the paper include Ashley Martof, Ram Gullapalli, Jon Kelly, Allison Rea, Brandon Lamoncha, Jason M. Walker, Brett Conner and Eric MacDonald.
Discuss this and other 3D printing topics at 3DPrintBoard.com or share your thoughts below.
Subscribe to Our Email Newsletter
Stay up-to-date on all the latest news from the 3D printing industry and receive information and offers from third party vendors.
Print Services
Upload your 3D Models and get them printed quickly and efficiently.
You May Also Like
Heating Up: 3D Systems’ Scott Green Discusses 3D Printing’s Potential in the Data Center Industry
The relentless rise of NVIDIA, the steadily increasing pledges of major private and public investments in national infrastructure projects around the world, and the general cultural obsession with AI have...
Formlabs Teams Up with DMG MORI in Japan
In late June, Nick Graham, Chief Revenue Officer at Formlabs, announced on LinkedIn that the company had partnered with DMG MORI, one of the world’s leading machine tool companies, to...
EOS in India: AM’s Rising Star
EOS is doubling down on India. With a growing base of aerospace startups, new government policies, and a massive engineering workforce, India is quickly becoming one of the most important...
3D Printing News Briefs, June 25, 2025: R&D Materials, 3D Printed Veneers, & More
In today’s 3D Printing News Briefs, 3DXTECH has launched a program that gives customers early access to experimental materials, and the first Lithoz CeraFab Multi 2M30 in the Czech Republic...