3D printing has gradually been making its way into the manufacturing and fabrication of end-use, functional components and parts. Previously thought of as merely a technology for prototyping, and having been around for decades for this cause, only recently has the technology been considered for the creation of custom, functioning parts that actually serve a purpose.
Today, Rocket Lab, a privately held aerospace company which is financed by several high-tech investors including Lockheed Martin, has announced that its carbon-composite Electron Launch System has become the world’s first battery-powered rocket. The launch system, which is used to launch small satellites into orbit, features the electric Rutherford engine, which is the first oxygen/hydrocarbon engine to use 3D printing for all of its primary components, including everything from its engine chamber, to its pumps, main propellant valves, and injector.
3D printing has allowed Rocket Lab’s team of engineers to manufacture an engine that is very lightweight, as well as greatly reducing the required build time. More traditional manufacturing methods can not come close to the ability that 3D printing has provided in making such lightweight parts, and the build time has been decreased from months to just days, using this technology.
“Historically, the time and expense to launch small satellites have been prohibitive, costing many millions of dollars and requiring endless patience and flexibility waiting for months to ‘hitch a ride’ to space,” explained Peter Beck, CEO of Rocket Lab. “With Electron, companies can launch whenever they would like, at a substantially more affordable cost. This monumental advancement in space technology gives satellite-reliant businesses the freedom they have been waiting for, which will lead to vast improvements in how we use satellite technology in space.”
This is all made possible, thanks to the affordability that 3D printing has provided. The engine has the ability to be 3D printed in just three days time, making it much quicker for companies looking to launch small 100kg payloads into Earth’s orbit. More impressive is the fact that the batteries within the launcher are capable of producing almost one megawatt of electricity, which is enough to provide power to an entire city block. The propulsion cycle uses electric motors, combined with incredible lithium polymer batteries, to run its turbopumps at almost unbelievable speeds.
It is expected that Rocket Lab will begin using this new battery-powered rocket system to launch satellites for customers starting sometime in 2016.
“Although the privatization of the space industry has promised an easier path to commercial launches, space has remained an incredibly difficult and expensive place to reach,” explained Beck. “Electron makes it possible for us to continue to execute on our vision to enable easier access to space. As more small satellite companies are able to quickly reach orbit, we will see immense advancements in communication and imaging technologies, which has the potential to drastically change our world – from improved traffic reporting to crop planning to even mitigating the life-threatening damages of natural disasters.”
Electron measures just 20 meters in length and has a diameter of 1 meter, with a lift-off mass of 10,500 kg. A dedicated launch will cost customers $4.9 million, and only requires a lead time of a few weeks. What do you think about this incredible battery-powered Rutherford rocket engine? Discuss in the Rocket Labs forum thread on 3DPB.com. Check out the video below.
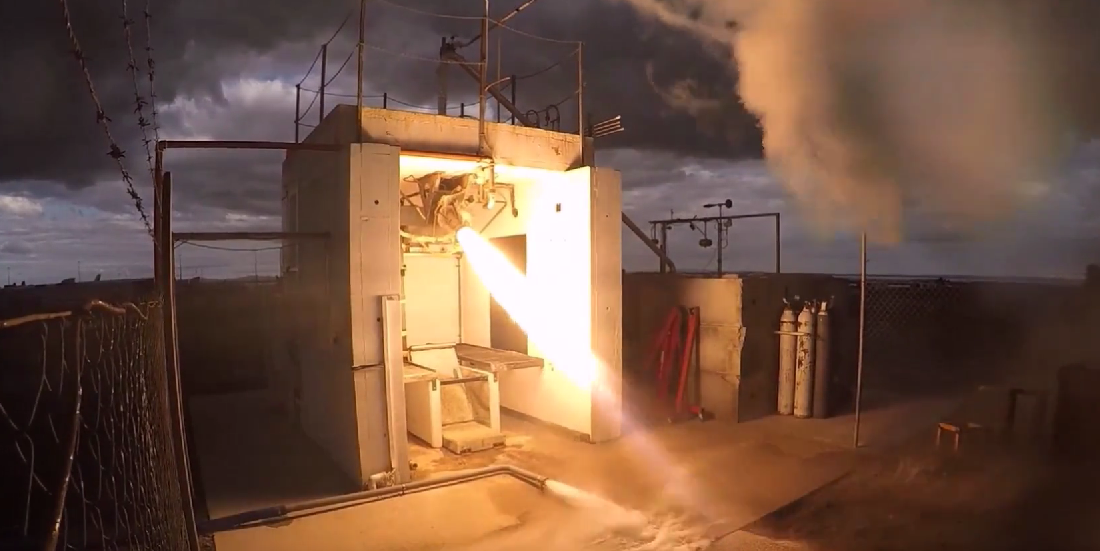

Subscribe to Our Email Newsletter
Stay up-to-date on all the latest news from the 3D printing industry and receive information and offers from third party vendors.
Print Services
Upload your 3D Models and get them printed quickly and efficiently.
You May Also Like
3D Printing News Briefs, July 2, 2025: Copper Alloys, Defense Manufacturing, & More
We’re starting off with metals in today’s 3D Printing News Briefs, as Farsoon has unveiled a large-scale AM solution for copper alloys, and Meltio used its wire-laser metal solution to...
Etsy Design Rule Change Reduces Selection of 3D Printed Goods
Online marketplace Etsy has implemented a rule change requiring all 3D printed goods on the site to be original designs. The update to the site’s Creativity Standards states, ¨Items produced using...
Siraya Tech Introduces New Elastomer 3D Printing Materials, Including Foaming TPU
California company Siraya Tech, founded in 2019 with a focus on material science, customer focus, and agility, develops high-quality 3D printing materials that meet the needs of creators, hobbyists, and...
3D Printing News Briefs, April 12, 2025: RAPID Roundup
The news from last week’s RAPID+TCT in Detroit just keeps on coming! That’s why today’s 3D Printing News Briefs is another RAPID Roundup of more exciting announcements from the trade...